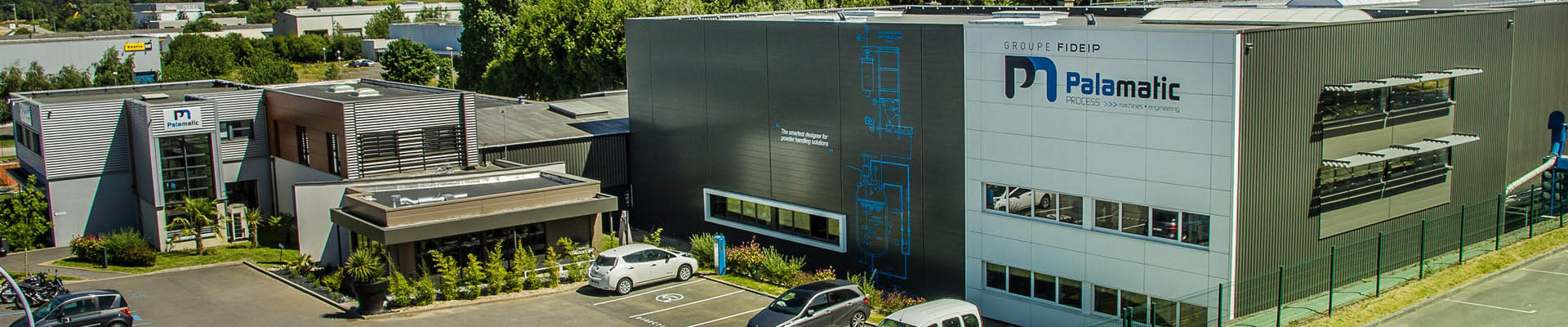
Case studies - Chemical
With our extensive knowledge of chemical industry processes, Palamatic Process can offer you quality assurance in your production line and/or integration of new equipment.
Fields of application: seeds and crop treatments, powder paints and coating, rubber, polymers and plastics, synthetic chemistry, detergent and laundry, petrochemistry, paper industry, etc.
Case studies with our customers
Optimization of Sensitive Powder Processing with a Custom Solution
Cement and plastering Pharmaceutical Nuclear Seeds industry Batteries and components Cosmetic and hygiene Paint and coating Thermics Veterinary Compound and plastic materials Defense Detergent and laundry powder Petrochemical Synthetic chemical Chemical Fine chemical Minerals and building Energy
Discharging station of big bags of cadmium in very high containment
Batteries and components Synthetic chemical Chemical Energy
Rubber parts production line
Rubber Chemical
Preparation process for the micro-ingredients
Rubber Chemical
Bag unloading station for reactor loading
Rubber Chemical
Process for feeding 2 lines of carbon black from flowbins
Rubber Chemical
Preparation and dosing workstation for metal powders
Rubber Chemical
Inerting skid at big bag filling station outlet
Seeds industry Chemical
Drum dumping and discharging in Atex zone
Synthetic chemical Chemical
Discharging of drained automative filters
Petrochemical Chemical
Big bags and sacks unpacking for reactor feed
Synthetic chemical Chemical
Big Bag Compactor for the Agro-Chemical Industry
Seeds industry Chemical
Double packaging big bags of Polyethylene Flakes
Petrochemical Chemical
Unloading drums of toxic powder
Paint and coating Chemical
Mobile big bag filling station for zirconium under dryer
Synthetic chemical Chemical
Unloading and conveying FIBCs of titanium dioxide for the ink and coatings industry
Paint and coating Chemical
Unloading and handling of graphite powder
Compound and plastic materials Chemical
Turnkey solution for big bag unloading and vacuum conveying of rheology additives for chemical manufacturing
Paint and coating Chemical
High-rate automatic big bag filling line for the export of natural soda ash
Detergent and laundry powder Chemical
Big bag unloading and mobile IBC docking for powder paint industry
Paint and coating Chemical
Packaging line for washing detergents and detergent products
Detergent and laundry powder Chemical
Big bag packing station
Synthetic chemical Chemical
Big bag filling under silo
Compound and plastic materials Chemical
Drum and bin tipper for skip feeding
Petrochemical Chemical
Container tipping of plastic granules
Compound and plastic materials Chemical
Discharge and pneumatic transfer of sodium nitrate
Synthetic chemical Chemical
Big bag discharge station
Paint and coating Chemical
Octabin Sealing System
Compound and plastic materials Chemical
Packaging of highly explosive powders in barrels
Synthetic chemical Chemical
Detergent powder milling
Detergent and laundry powder Chemical
Bulk solids supply to a manufacturing tank
Detergent and laundry powder Chemical
Unloading sacks for reactor feeding
Petrochemical Chemical
Pneumatic conveyor for mixer feeding
Paint and coating Chemical
Automatic loading of raw materials into reactors with integrated dosing
Synthetic chemical Chemical
Screening and packing skid for chromium powder
Synthetic chemical Chemical
FlowMatic® 04 automatic big bag packaging line
Seeds industry Chemical
Emptying of polypropylene bags for truck filling
Petrochemical Chemical
Discharging station for big bags of acid
Synthetic chemical Chemical
Discharge of big bags for truck tank filling
Petrochemical Chemical
Bag dumping for loading dough machines before coating
Compound and plastic materials Chemical
Atex 20 Loading of resins and polymers in chemical reactors under pressure
Paint and coating Synthetic chemical Chemical
Automatic bag emptying for feeding extrusion line
Petrochemical Chemical
Skid for unloading of bags of additives
Petrochemical Chemical
Big bag filling with corn seeds
Seeds industry Chemical
Automatic packaging line for big bags FlowMatic® 04: metering - conditioning - conveying
Seeds industry Chemical
One handle big bag filling with fertilizer
Seeds industry Chemical
Loading a chemical reactor from bags and big bags in ATEX zone 01
Synthetic chemical Chemical
Raw material feed and lump breaking of resinous materials
Paint and coating Petrochemical Chemical
Loading of wagons with pulverulent
Petrochemical Chemical
Discharge of paint powder containers into big bag
Paint and coating Chemical
Process for tanning additives: Feeding a chemical dispersion process from sacks and flexible or rigid containers.
Paint and coating Chemical
Discharge of big bags of zinc raw materials into etching tanks
Paint and coating Chemical
Discharge of big bags of bleaching agents for tank feeding
Detergent and laundry powder Chemical
Laundry powder storage line
Detergent and laundry powder Chemical
Additives feeding for extrusion line
Compound and plastic materials Chemical
Raw material deconditioning unit, masterbatch mixture preparation and incorporation on extruder line
Compound and plastic materials Chemical
Discharging, conveying and dosing in a dough processing machine
Compound and plastic materials Chemical
Discharge and pneumatic conveying of fluorinated derivatives
Petrochemical Chemical
Discharging of big bags of activated carbon to a reactor in a contained way and under ATEX 22 atmosphere
Synthetic chemical Chemical
Discharge of bags for feeding a mixing tank
Cosmetic and hygiene Paint and coating Fine chemical
Automatic big bag unloading system for PET flakes and pellets
Compound and plastic materials Insect breeding
Our team of experts can supply processes for more difficult to handle chemical bulk materials with strict safety rules. By gathering the necessary data on your production process, we make sure that all regulation requirements and risks are taken into consideration for the final design, including: accidents, environmental pollution, chemical burns, poison, fire and explosion hazards.
Our offer includes:
- Compliance with ATEX and Class/Div standards
- Sanitary design with CIP "Clean In Place"
- Compliance with the rules of cross-contamination
- Containment of toxic substances
- Dosage of raw materials
- Dedicated production lines
- Respect for the integrity of bulk materials (product degradation, humidity, etc.)
- Material certificates and documentation requirements
- Automation for traceability of all your production batches
By working closely with our customers, we can define and customize the technical solutions suited to your manufacturing specifications and safety constraints (ATEX, inerting, toxic).
The wide variety of powders and bulk materials used in the chemical industry, depending on the nature of the product (solid, liquid, flammable, oxidizing, toxic, etc.), requires an expert level of knowledge for appropriate treatment and handling. Our team of engineers and technicians are trained in the integration of various equipment and process technologies.
Palamatic Process offers turnkey systems regarding the loading of raw materials for processes involved in the transformation of petroleum derivatives (plastics, synthetic fibers, etc.). Our equipment is used in different stages for processing of these raw materials including: storage to pneumatic conveying and from dosing to automation.
Examples of materials processed: clarcel, titanium dioxide, carbon black, antimony, epoxy-polyester, graphite, nylon, sodium oleate, resins, sulphur, silicone, thermo-plastic, varnish, zinc...
Our powder experts give you advice on handling chemical powders: things to know when storing chemicals, recommended equipment for handling toxic materials...