Description
Venting filter for installation on storage hoppers, dosing systems…
The hopper venting filter is designed to contain and control dust particles and complies with air pollution regulations. The venting filter is ideal for venting dust-loaded air volumes.
The venting filter is extremely compact for venting the loading hoppers. The dust, separated from the air flow by means of a filter element, falls into the hopper thanks to the compressed air cleaning system integrated in the cover. The cleaning is carried out by an adjustable electronic sequencer.
The integration of venting filters prevents pressure build-up in the equipment and thus maintains a perfect dust tightness in order to guarantee a clean process.
-
Efficiency5
Equipment advantages
- Reintroduction of fines into the process; no product loss
- High cleaning efficiency
- High filtration efficiency
- Compact design
- Easy installation and retrofitting
- Low emission level due to B.I.A.-certified filter media
- Maintenance-free air jet cleaning unit integrated in the cover
Media
View our equipment in photos
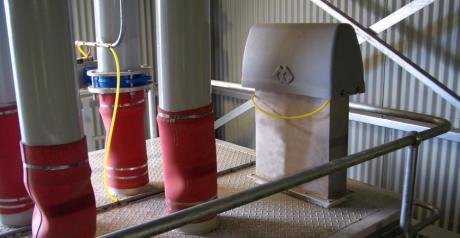
Dust collector on hopper
The Palamatic Process degassing filter ensures low dust emission for the hoppers.
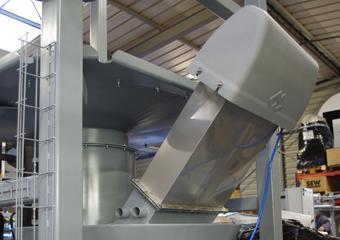
Hopper venting filter on big bag discharge station
The Palamatic Process degassing filter ensures low dust emission of the hoppers.
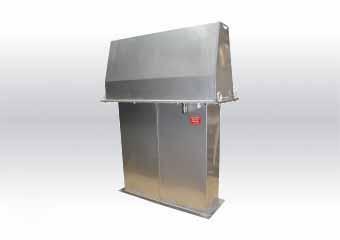
Hopper venting filter
Industrial dust removal on packing and powder handling processing lines.
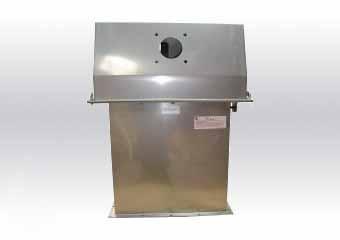
Industrial filtration hopper venting system
Small dimensions polygonal filter for installation on buffer storage hoppers or weighing hoppers.
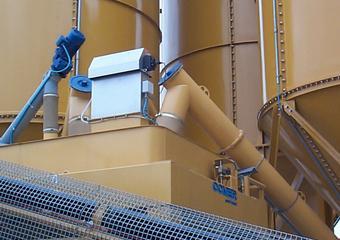
Venting filter Palamatic Process
The polygonal filter can be used in various industries.
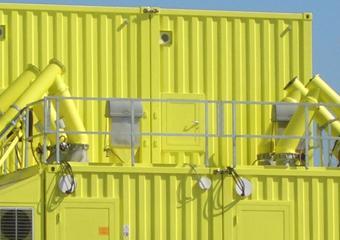
Industrial venting filtration
The degassing filter is extremely compact and is suitable for mechanically loaded hoppers.
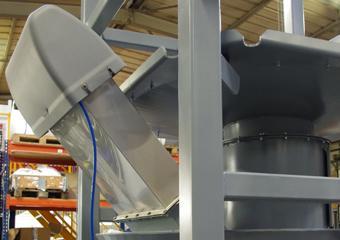
Big bag unloading venting filtration
The compressed air cleaning system integrated in the cover removes dust particles from the filter elements.

Venting filter for mechanically filled hoppers
The dust filter is installed on a centrifugal screen on an industrial spice production line.
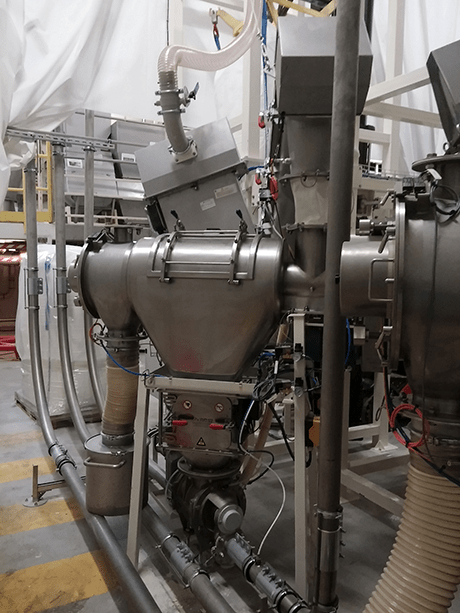
Venting filter for installation on intermediate storage hoppers
The dust filter is installed on a centrifugal screen on an industrial spice production line.
Features
Technical specification
- Filter surface: from 0.5 to 2m².
- Power supply: 24 V AC
- Filtering element: non-woven polyester certified "BIA" (class U, S, G and C)
- Cleaning: compressed air counter-current - 6 bar
- Electronic board: included, with possibility of adjusting pause and pulsation times
- Maintenance: to be carried out on the clean side
- Construction material: plastic cover (optional stainless steel 304 or 316L); body in stainless steel 304 (optional 316L)
- Realization: body made of a single welded part to avoid product retention
- Weight: 21 kg
- Installation: connection of the filter to the exhaust fan
Case studies
CASE STUDIES WITH THIS EQUIPMENT
Processing line for biscuit production factory
Processed powder: Crystal sugar - Line for biscuit factory - Food manufacturer that specializes in biscuits, chocolate and cocoa. The customer's process requirements involved the milling of granulated...Food and Animal Feed