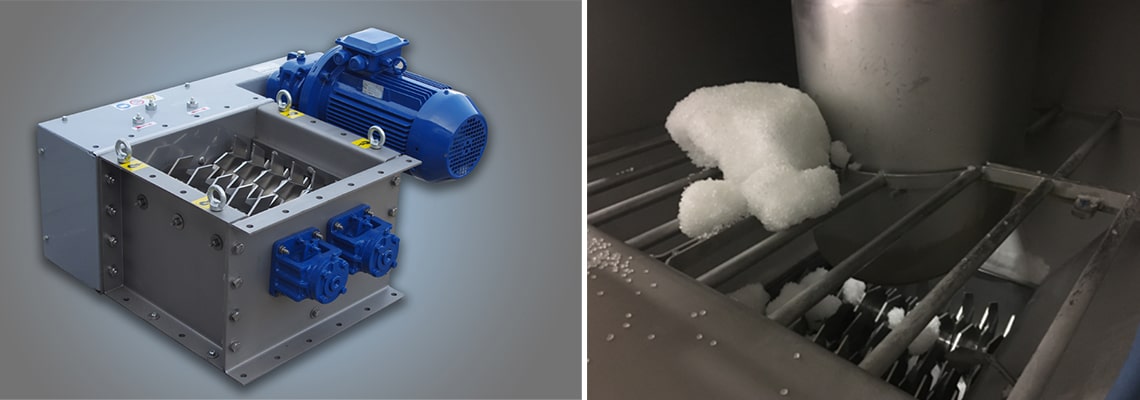
Kluitenbrekers (ook wel crushers of granulators genoemd) worden algemeen gebruikt in de poeder- en bulkgoederenindustrie om de stroomkarakteristieken van droge materialen te verbeteren. De breker bestaat meestal uit een vierkante of rechthoekige behuizing met een externe aandrijving en interne messen/messen die aan assen zijn bevestigd. De messen zijn omgeven door een vast rooster, waardoor grote stukken materiaal tegen de roterende mechanismen kunnen worden gebroken.
De breker werkt met een hoog rotatieniveau en een laag toerental om de grotere agglomeraten effectief te breken voor verwerking stroomafwaarts. De vaste zeef is een basisscheidingsmiddel voor de classificatie van poeders, waardoor vrijstromende deeltjes door de machine kunnen, terwijl klonters worden tegengehouden voor verdere verwerking. Laten we eens kijken naar veel voorkomende toepassingen voor kluitenbreker.
1. Deagglomeratie na langdurige opslag of vervoer van materialen
Vaak kunnen droge bulkmaterialen tijdens de opslag bezinken. Veel voorkomende voorbeelden waar dit gebeurt zijn big bags, vrachtwagens, silo's, IBC's en opslagcontainers. Wanneer materiaal wordt opgeslagen, treedt er op natuurlijke wijze ontmenging en verdichting van de deeltjes op, waarbij het fijnere materiaal naar de bodem zakt en de grovere deeltjes aan de oppervlakte blijven. Dit proces zorgt ervoor dat luchtzakken tussen de deeltjes dichtklappen en na verloop van tijd ontstaan er compressieklonten.
Bovendien kunnen containers of andere opslagmiddelen worden blootgesteld aan hoge vochtgehalten of mogelijk schimmel. Blootstelling aan vocht kan ook leiden tot de vorming van vaste klonters die meer energie nodig hebben om te scheiden.
Daarom installeren veel fabrikanten brekers direct onder hun silo's en leegstations voor big bags om het materiaal te helpen conditioneren en klonters te breken. Bij suikerproductieprocessen wordt vaak een beroep gedaan op dit soort conditioneringsapparatuur om de moeilijkere materiaaldeeltjes te helpen opbreken en ze terug te brengen in hun korrelige toestand. Brekers worden ook vaak gebruikt onder een station voor het legen van zakken. Wanneer zakken van 50 kg op pallets worden gezet en naar een andere faciliteit worden vervoerd, is er voldoende tijd om sommige poeders te verdichten. De operator kan de inhoud van de zak gewoon in het stortstation dumpen, waarna de breker het materiaal klaarmaakt voor het verdere proces.
2. Voorbereiding van het vervoer en levering van uw materiaal
Als het materiaal de neiging heeft te klonteren tijdens de opslag, is het logisch dat het vervoer van punt A naar punt B moeilijk en onproductief zal zijn. Indien uw installatie een pneumatisch transportsysteem heeft, of het nu in dichte of in verdunde fase, onder druk of vacuüm is, dan zal uw transportleiding aan efficiëntie inboeten of het risico lopen dat de leiding volledig verstopt raakt indien u stroomopwaarts geen klontbrekersysteem installeert.
Om het product met behulp van druktransport of vacuümtransport te kunnen transporteren, moet uw materiaal een goede lucht-deeltjesverhouding hebben (afhankelijk van het type transport en de bulkdichtheid van het poeder). De aanwezigheid van agglomeraten onderbreekt het mengen van de lucht/poederverhouding en kan daardoor leiden tot een drastische vermindering van uw verwerkingscapaciteit. Zelfs mechanische transfersystemen (schroeftransporteurs, transportbanden, triltransporteurs, enz.) hebben een materiaal nodig met behoorlijke stromingseigenschappen en een betrekkelijk homogene deeltjesgrootteverdeling. Vaak worden roterende kleppen gebruikt om de poedertoevoer in pneumatische transportleidingen op een constante snelheid te brengen. Het inbrengen van grote harde blokken in een roterende luchtsluis kan leiden tot apparatuurstoring.
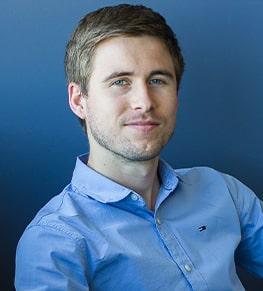
Heb je een project? Ik ben beschikbaar om
te adviseren en u te vergezellen in uw studie.
Guillaume, expert in het malen van poeder
Elk type van uitrusting voor het aanvoeren en vervoeren van bulkgoederen vereist een geconditioneerd droog poeder. Schroefdoseringen, trilgoten, roterende kleppen... vereisen allemaal een klontvrij poeder. Poederdoseerapparatuur is het meest geschikt voor het nauwkeurig wegen en doseren van poeders. Deze apparatuur wordt vaak gebruikt in commerciële verpakkingen voor eindgebruikers. Daarom is een nauwkeurige dosering naar gewicht of volume essentieel. Het doseren van materiaalagglomeraten leidt tot inefficiëntie in de werking van de voederapparatuur. Indien het poeder geen constante doorstroomsnelheid heeft, kan over- of onderdosering optreden door de aanwezigheid van klonters die de nauwkeurigheid van het doseergewicht verstoren. Nogmaals, het vergruizen van uw materiaal zal bijna elke fase van uw productieproces ten goede komen.
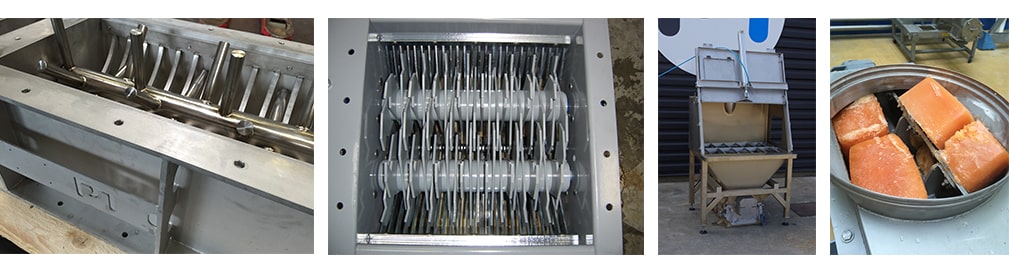
3. Noodzaak van voorvermaling voor een proces met hoge toegevoegde waarde
Zeefapparatuur is een belangrijke stap in de controle van de kwaliteit van uw productie. Neem het voorbeeld van zout, dat bij blootstelling aan vocht een baksteenachtige massa kan vormen. Het inbrengen ervan in een zeef kan het zeefgaas of zelfs de hele zeef zelf beschadigen. Hetzelfde geldt voor kristalsuiker en sommige poedervormige chemicaliën.
Zeefschudders hebben verschillende functies: zij verwijderen te grote deeltjes aan de bovenkant van de verdelingscurve, zij controleren de productielijn op vreemde voorwerpen (kwaliteitscontrole) en zij verwijderen stof van de fijnere deeltjes aan de onderkant van de curve. Wat ze (meestal) niet aankunnen, zijn de grotere agglomeraten die niet gemakkelijk kunnen worden gescheiden.
Hetzelfde principe geldt voor maal- en mengapparatuur. Als u poeder in een molen voert om de deeltjes te verkleinen en waarde toe te voegen, zal de molen aan efficiëntie inboeten als het poeder niet uniform van aard is. Bovendien zal de molen na verloop van tijd meer energie verbruiken omdat hij overwerkt wordt om grotere brokken te breken waarvoor hij oorspronkelijk misschien niet ontworpen was (wat leidt tot onnodige slijtage van de apparatuur of zelfs uitval).
Proberen samengeklonterde poeders te mengen werkt ook nooit goed. Specerijenmengsels en instantvoedselbereidingen zijn een ander voorbeeld. Als u poeders probeert te mengen die klontjes bevatten, krijgt u inconsistente smaakmengsels. Dit kan gevolgen hebben voor de verkoop van direct-aan-consumentproducten (pannenkoekenmixen, droge sauzen, kant-en-klare bakkersrecepten, enz.)
Conditionering, de-agglomeratie, voorvermaling, enz. van het poeder is daarom een essentieel onderdeel van elk hoogwaardig produktieproces. Een homogeen materiaal met gemakkelijke vloei-eigenschappen is van het grootste belang voor het bereiken van betere apparatuurprestaties, consistente resultaten en een hoge productiviteit.
Neem contact op met een van onze experts voor hulp bij poederbehandelingsoplossingen en om een offerte aan te vragen.