Er bestaat vaak verwarring tussen de termen schroeftransporteur, doseerschroef, triltransporteur en vibrerende toevoerinrichting. In dit artikel definiëren we wat poederdoseerapparatuur precies is en hoe u het beste type apparatuur voor uw materialen kunt kiezen tussen een schroefdosator en een vibrerende dosator.
1. Belangrijkste functies van een doseerapparaat
De toevoeruitrusting is geen transportsysteem. Mechanische transportbanden, zoals schroeftransporteurs (ook wel vijzeltransporteurs genoemd) en triltransporteurs, bestaan gewoonlijk uit een inlaat en een uitlaat met als enig doel materiaal over lange afstanden van punt A naar punt B te verplaatsen. Zij werken gewoonlijk met een vaste snelheid en verplaatsen het materiaal stroomafwaarts met een constante snelheid, gemeten in ton of kilogram per uur.
Doseerapparatuur wordt gebruikt in situaties waar een grotere controle en nauwkeurigheid van de materiaalstroom vereist is. Schroefvoeders en vibratievoeders worden niet gebruikt om materiaal over lange afstanden te verplaatsen, maar eerder om materiaal uit een trechter of IBC te doseren naar een verpakkingslijn of industriële breker. Zij zijn veel kleiner dan mechanische transportbanden en bestaan uit een geïntegreerde trechter, een roerwerk, een kleine buis of platte basis en een aandrijving met variabele frequentie.
De geïntegreerde trechter is noodzakelijk voor doseerapparatuur, aangezien een constante hoofdbelasting moet worden gehandhaafd voor een goede werking. De snelheid kan via een VFD op de toevoeruitrusting worden geregeld, zodat een langzamere of snellere toevoer mogelijk is.
Als uw proces vereist dat verwerkt materiaal wordt herverpakt in papieren zakken van 25-50 kg en u er zeker van moet zijn dat de container niet te vol of te weinig wordt geladen, dan is een toevoerapparaat het antwoord. Evenzo presteren poedermolens het best wanneer zij werken met een constante, constante aanvoersnelheid.
2. Denk aan de kenmerken van uw materiaal
Poeders en granulaten kunnen verschillende eigenschappen hebben die hun gedrag in een fabricageproces sterk beïnvloeden. Het is daarom belangrijk deze kenmerken te bestuderen alvorens uw industriële uitrusting te kiezen. In het algemeen zijn de volgende eigenschappen gebruikelijk voor de analyse van bulkmaterialen:
- Hygroscopiciteit: Suiker, zout en bepaalde soorten chemische poeders kunnen gemakkelijk en gemakkelijk vocht uit de omringende atmosfeer opnemen, waardoor het materiaal gedurende lange perioden van opslag en rust kan gaan klonteren en verharden.
- Beluchting: Glasparels, meel en harsen hebben vaak een lage neerslaghoek en gedragen zich bij beluchting als een vloeistof. Dit materiaal kan gemakkelijk downstream-processen overspoelen (oncontroleerbare stroom) indien het niet onder controle wordt gehouden.
- Klontering: Houtmeel of biomassavezels en dergelijke bevatten lange deeltjes die samenklonteren en massa's vormen die stromingskanalen kunnen blokkeren.
- Hechting: Materialen zoals pigmentpoeders kunnen klevend zijn, d.w.z. zich vasthechten aan elk denkbaar oppervlak, waardoor dit soort producten zeer moeilijk te hanteren kan zijn.
- Brosheid: pasta's, vlokken of sommige korrelige producten kunnen gemakkelijk worden gebroken (zogenaamde wrijving) als ze te ruw worden behandeld. Daarom is apparatuur nodig waarmee het materiaal voorzichtig kan worden gehanteerd en overgebracht, zodat de integriteit van het product behouden blijft.
- Gemak van doorstroming: Kunststof pellets stromen gemakkelijk door de zwaartekracht, met weinig of geen stromingshulpmiddelen of speciaal ontworpen apparatuur.
- Schurend vermogen: glaspoeders, portlandcement, enz. kunnen eigenschappen hebben waardoor onderdelen van apparatuur snel slijten als bij het ontwerp van uw proces geen rekening is gehouden met deze eigenschap. Dit kan leiden tot frequent en kostbaar onderhoud.
Anticiperen op hoe uw poeder zich zal gedragen is daarom een essentiële stap bij de keuze van uw doseerapparatuur.
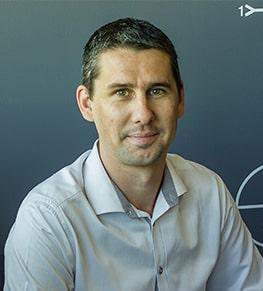
Twijfelt u over welk type doseerunit u moet kiezen?
Ik ben beschikbaar om met u te overleggen en u te adviseren.
Benjamin, deskundig poeder
3. Verschillen in prestaties en ontwerp
Schroefdoseerders maken gebruik van een geïntegreerde trechter met een roerwerk dat een buisvormig kanaal voedt. In de buis zit een kleine schroef die het product via een uitlaat naar het downstream-proces duwt. Er zijn verschillende ontwerpen voor de kleine schroef in schroefvoeders: pigtailschroeven, lintschroeven en schroeven met een aandrijfas.
- Staartschroeven hebben geen centrale schacht en worden vaak gebruikt voor materialen die de volgende kenmerken hebben: lichte dichtheid en/of kleverig of cohesief zijn. Voorbeelden: bloem, cacaopoeder en oxiden.
- Lintschroeven hebben een centrale as, maar de vleugels zijn open en op één punt met de as verbonden. Lintschroeven worden gebruikt voor lichte en korrelige materialen zoals PVC en polymeergranulaat.
- Centrale asschroeven worden gebruikt voor dichtere of vrijstromende materialen zoals metaalpoeders.
Schroefvoeders bieden een goede nauwkeurigheid. In sommige gevallen is de doseringsnauwkeurigheid -/+ 1-2 gram. Dit is het meest gebruikte type voeder, omdat het geschikt is voor de meeste toepassingen, behalve in het geval van brosse of hittegevoelige materialen.
Vibrerende toevoerapparaten hebben een soortgelijke structuur (trechter en buisvormige structuur), maar in plaats van een schroef zijn er trilmotoren aan de eenheid bevestigd en wordt de structuur ondersteund door veren, waardoor de eenheid kan trillen. Door een zeer kleine hoek kan de eenheid het materiaal langs het toevoerbed naar het stroomafwaartse proces verplaatsen. De voedingssnelheid kan worden geregeld door de amplitude en de frequentie van de trillingen te verhogen of te verlagen. Door te roeren blijft de integriteit van het materiaal behouden of wordt onnodige slijtage vermeden in het geval van abrasieve materialen. Daarom zijn trilgoten de ideale oplossing voor brokkelige, temperatuurgevoelige of abrasieve materialen.
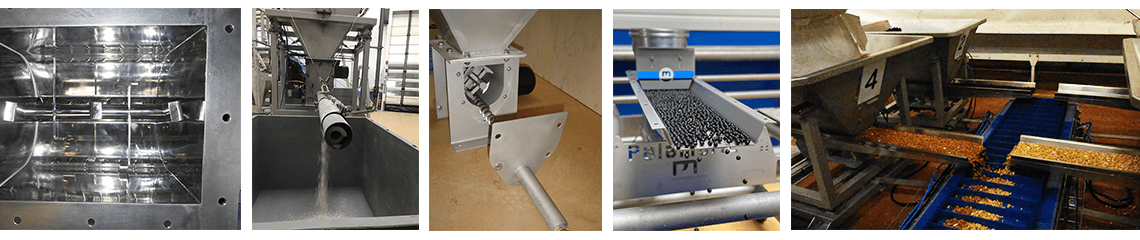
4. Voor- en nadelen van schroeftransporteurs en vibrerende transporteurs
Schroefdosering
Belangrijkste voordelen van een doseerschroef:
-
Schroeftypes kunnen worden gevarieerd en gemakkelijk worden verwisseld voor een grote variëteit aan poeders
- De schroef zorgt voor positieve extractie (tractie) uit de trechter
- Hij kan worden ontworpen voor gemakkelijk te reinigen toepassingen, zonder dat de hele eenheid uit de lijn moet worden gehaald
Belangrijkste nadelen van een doseerschroef:
- Kleefstoffen en fijne deeltjes kunnen zich ophopen in het materiaal, waardoor de verwerkingscapaciteit wordt beperkt
Bewegende onderdelen kunnen leiden tot extra slijtage van de apparatuur, waardoor meer onderhoud nodig is - Verbruikt meer energie dan een vibrerende feeder
Vibrerend doseersysteem
Belangrijkste voordelen van een vibrerend voeder:
- De feeder kan zowel lage als hoge voedingssnelheden aan
- Produceert een gelijkmatige materiaalstroom voor een vlotte verwerking
- Vrijwel geen bewegende delen, waardoor minder onderhoud nodig is
- Laag energieverbruik
Belangrijkste nadelen van een trilgoot:
- Door de trillende werking kan stof vrijkomen met sommige fijne poeders
- Trillingen kunnen materialen scheiden die gemengd zijn
- Biedt geen positieve extractie (een middel om materiaal uit de trechter te trekken)
- Kleverig materiaal of fijne deeltjes kunnen zich ophopen op de toevoerlade, waardoor de verwerkingscapaciteit wordt beperkt