Description
Featuring advanced technology, plow mixers provide excellent results in both speed and consistency of powder mixtures for batch processes. Due to their high-performance speed, they are among the fastest mixers with an average mixing time of 1 to 4 minutes. Another advantage this industrial mixer offers is no dead zones where unmixed ingredients could reside.
The performance of the batch process plow blender allows the mixing of bulk materials with very low dilution ratios (1/100,000). Deflocculating devices (additional choppers) with knives provide a very efficient dispersion and homogenization operation.
Our batch blade mixer offers flexibility and can easily be integrated into a fully automated system, or as part of manual filling and emptying industrial system.
The integrated discharging hatch combined with a "Clean in Place" (CIP) system enables a rapid change of recipes and batch runs without risk of cross-contamination or product waste.
Batch plow and blade mixer are available in 3 versions:
- Discharge from bottom hatch MRS
- Discharge from 15° hatch MRS15
- Discharge from 15° hatch MRS60
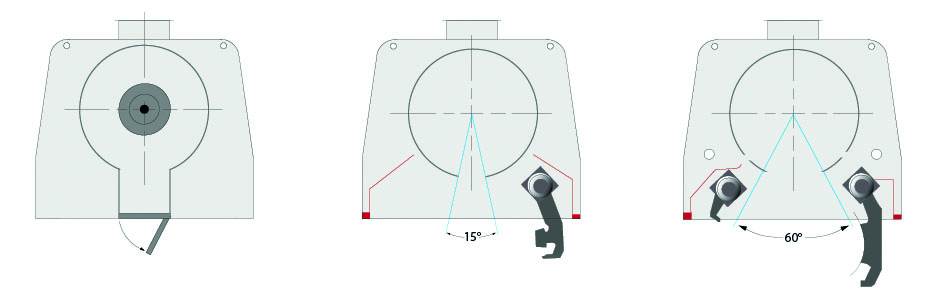
OPERATING MODE
Our Plow Mixer unit consists of one electrical motor, one reduction gear, coupling, and shaft with an agitation that has plow liked shaped attachments that collide with ingredients causing a multi directional response that mixes products quickly. The shaft is sealed with a bushing & PTFE gland housing at both ends.
Materials are loaded from top side, and the discharge is located at the bottom side in the center or end, depending on production needs, either batch type or continuous. The discharge height can be adjusted as required, so that material gets discharged into the container below it without dust emissions.
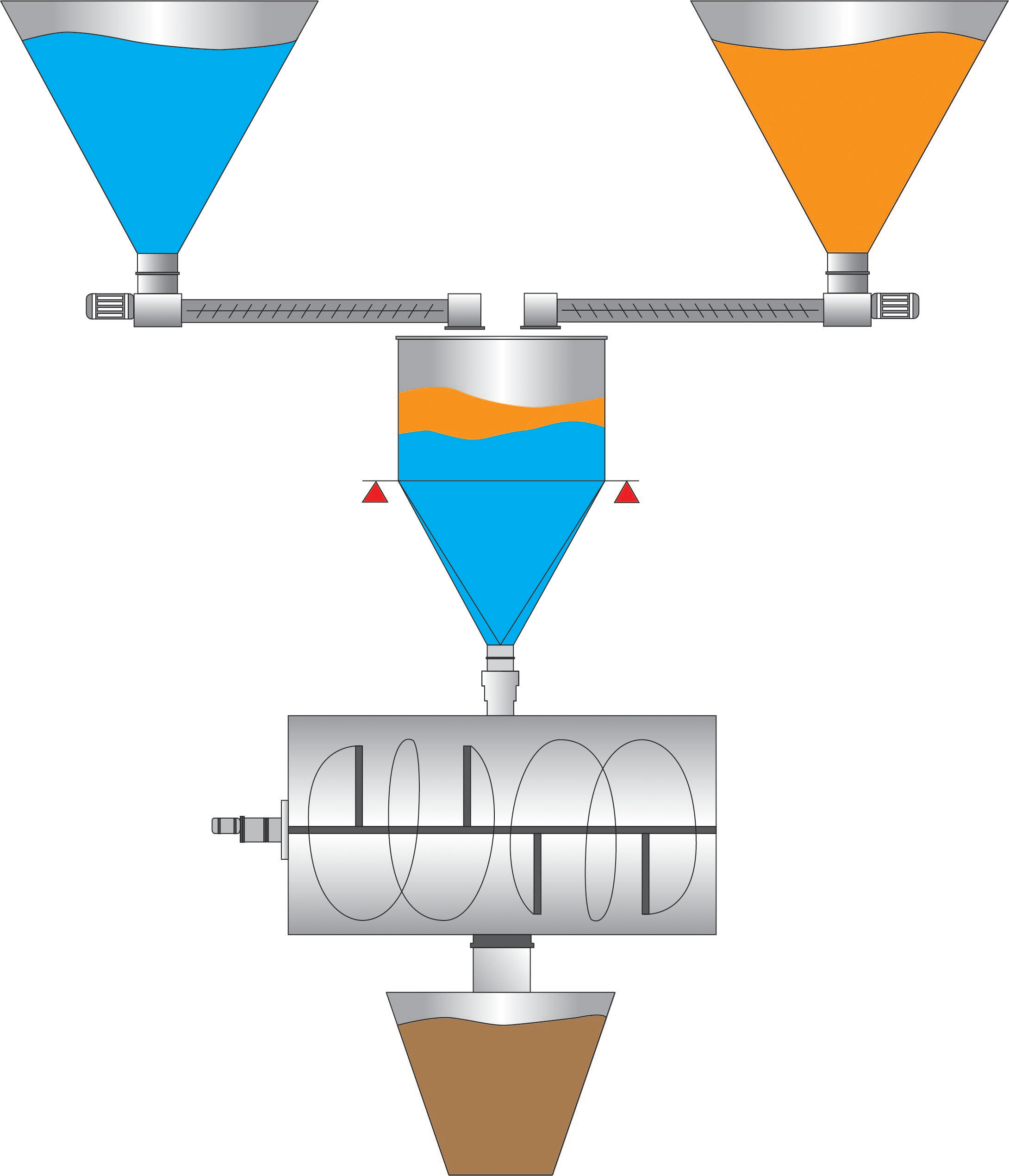
TECHNICAL FEATURES
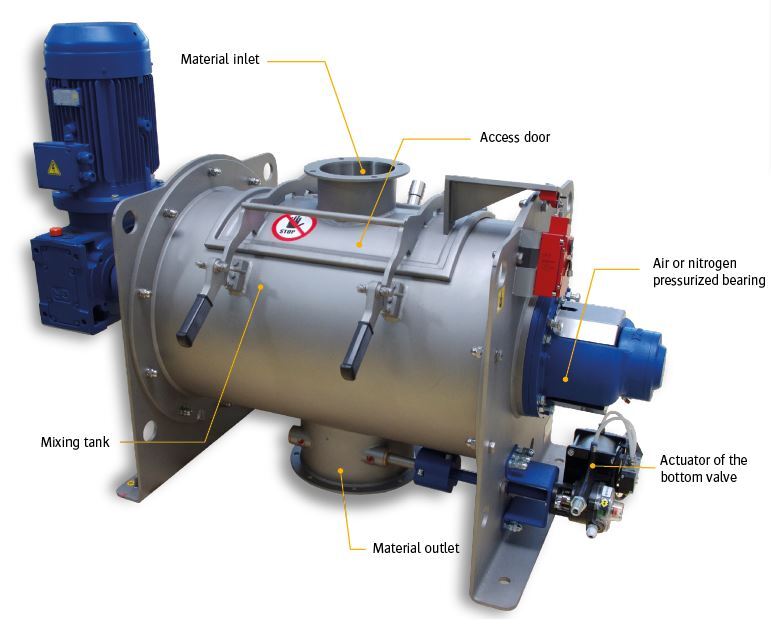
Equipment advantages
- Excellent batch reproducibility
- Made of steel, 304L and 316L stainless steel
- Dispersion: 20 gr./t.
- Maximum homogenization of the mixture
Media
View our equipment in videos
Plow and blade mixer
Plow blender and blade mixer
View our equipment in photos
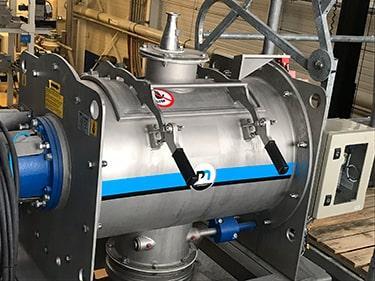
Plow and blade mixer Palamatic Process
The Palamatic Process discontinuous plow and blade mixer is ideal for obtaining high quality mixtures.
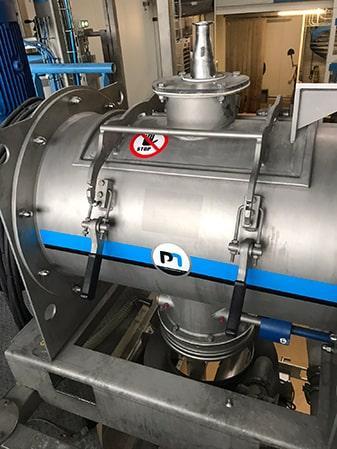
Discontinuous plow and blade mixer Palamatic Process
The industrial mixer is adaptable to all sectors of industrial activity.
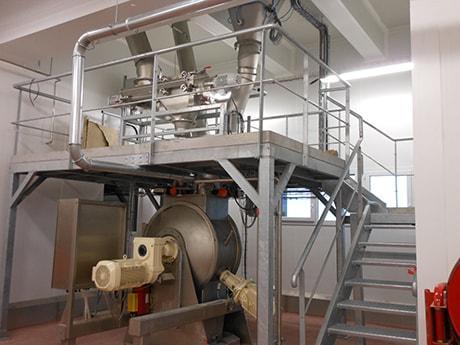
Spice mixer
Spice mixing line with cleanability of equipment and recipe flexibility.

Recipe flexibility
Management of the manufacturing of production recipes.
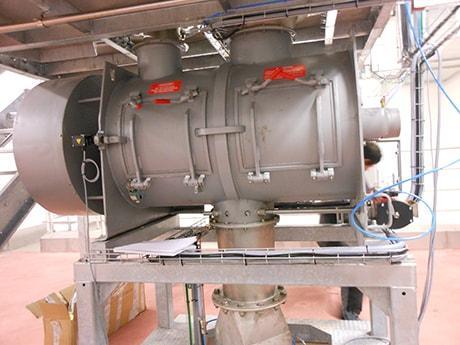
Incorporation of liquid into a mixer
The liquids incorporated are oil or liquid flavours.
Features
Technical specification
Motorization from 4 to 200 kW
Mixing capacity: from 2 to 15 batches per hour
Capacity from 75 to 15 000 liters:
Type | 75 | 150 | 300 | 550 | 800 | 1 100 | 2 000 | 3 000 | 4 800 | 6 000 | 8 800 | 10 500 | 15 000 |
---|---|---|---|---|---|---|---|---|---|---|---|---|---|
Usable | 56 | 105 | 210 | 385 | 560 | 770 | 1 400 | 2 100 | 3 360 | 4 200 | 6 160 | 7 350 | 10 500 |
capacity in dm³ |
Case studies
CASE STUDIES WITH THIS EQUIPMENT
Masterbatch and additives
Processed powders: cobalt, calcium carbonate CaCo3, titanium dioxide TIO2 - Masterbatch and additives - Discharge of raw materials while maintaining a healthy atmosphere without pollution and without...Chemical
Preparation of dried fruit recipes
Processed products: dried fruit - Preparation of dried fruit recipes - This installation involves the feeding of dried fruit to a mixer. The various dried fruits are stored in bags, boxes and big bags...Food and Animal Feed
Bagging of fruits and pulses
Processed products: dried fruits and vegetables - Bagging of dried fruits and vegetables - The installation concerns a mixing and packaging line for dried fruits and vegetables.Food and Animal Feed
Mixing and packing line for dried fruits
The dried fruit recipe preparation line allows you to: - load a paddle mixer with ingredients packaged in boxes - mix the different raw materials according to the recipe - transfer the dried fruit...Food and Animal Feed
Process for mixing dry ingredients
Processed Materials: Granulated Sugar, Rebaudioside M, Cocoa Powder and various minor ingredients - Process for mixing dry ingredients - The new facility expansion project required the capabilities of...Food and Animal Feed
Optimization of the processing of agglomerated dried fruit
Products processed: dried fruit and vegetables Disaggregation of a large volume of dried fruitFood and Animal Feed