Description
PalSack®01 Bag Filling Station - Containment, accuracy, cleanability
Our PalSack® 01 bag filling system provides accurate dosing of dry material via an integrated screw feeder. The PalSack® 01 bag packaging machine can be used to fill all types of bags, such as: burlap, paper, plastic, open mouth, lined, single layer, double layer, microperforated, etc., and ranging in weight from 10 to 100 lbs. The obtainable production rates can reach up to 100 bags / hour.
The bagging machine offers many integrated features, such as: bag stitching, removing the internal liner, automatic weld sealing for water tight closure, motorized roller conveyor, vacuum bag lifter, etc.
Equipment Advantages:
- A double jacketed filling head with an inflatable seal or clamping jaws for a secure connection and dust containment.
- Loss-in-weight (LIW) or gain-in-weight (GIW) functionality
- A dosing system adapted to your production and process requirements (precision, cleanability, flow rate, etc.)
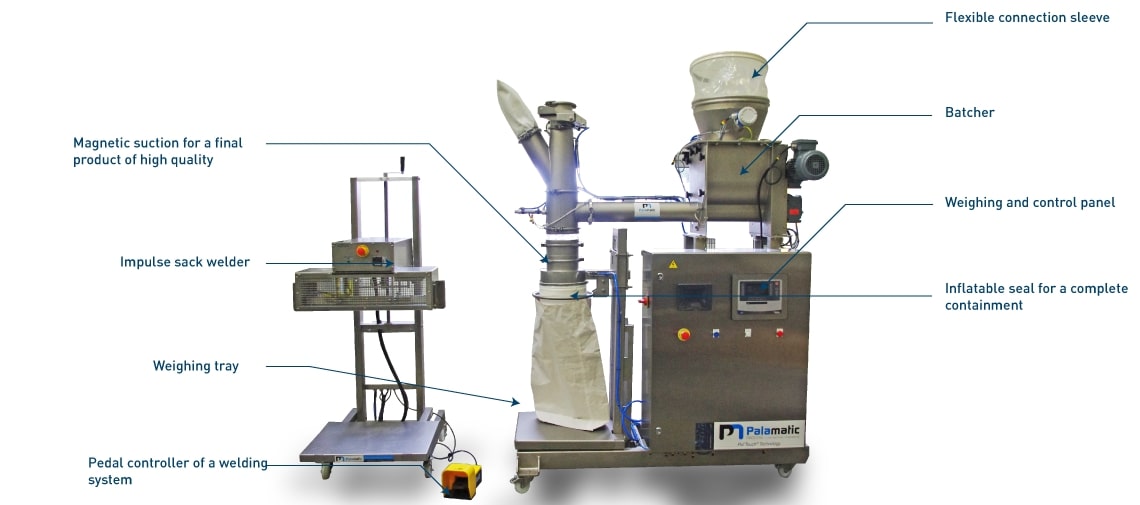
Possible configurations of the PalSack®01 model:
Ref. | Available equipment | Functions | Advantages | |
---|---|---|---|---|
Choice 1 | J | Inflatable seal | Dust tight bag connections | Maximum confinement |
M | Clamping jaws | Quick bag connections | Speed, ergonomic installation and multi-format bags | |
Choice 2 | P | Support tray | Tension of the bag during filling | Hygiene, height adjustment for adaptability to multi-format bags |
C | Motorized roller conveyor | Holding and evacuation of the bag during filling | Ergonomics, increased speed | |
Choice 3 | Net | Net weighing | Provides accurate amounts of the packaged product | Accelerated rate (dosing in hidden time) / may require a double check weighing system |
Gross | Gross Weighing | Weighing of the entire container and contents | Commercial weighing, traceability |
Our PalSack®01 packaging machine is configurable by modulating the basic possible equipment: Choice 1 + Choice 2 + Choice 3.
Possible reference example: PalSack®01-J-P-Net
Choice 1: Two types of bag connection styles:
- "J" Inflatable seal: This provides a completely dust tight connection. The double-envelope design balances the material to escaping air volumes. A hygienic design is possible for easy dismantling of all parts to be cleaned.
- M" clamping jaws: The docking of the bag by half-moon clamps is designed with an oval shaped fill head with two jaws actuated by a pneumatic cylinder. This connection method is recommended when filling bags that are suspended over the station.
Our engineering office can customize solutions for your automatic bagging machines according to your plant’s production and design requirements. Our team can work with you to offer tailor-made solutions, after visiting your site and upon receiving your precise specifications.
Palamatic Process also offers a range of semi-automatic or automatic bag filling systems for open mouth bags. The purpose of the bagging machine is to package powdered or granular products in open-mouth bags. The filling station is suitable for a large number of bags and is characterized by its ease of use.
-
Rate3
-
Automation3
-
Containment5

PalSack®01-J-C-Gross
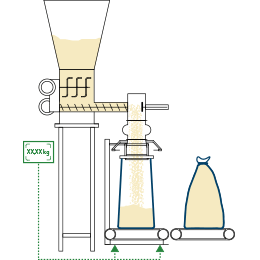
PalSack®01-M-C-Gross
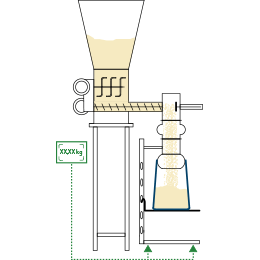
PalSack®01-J-P-Gross
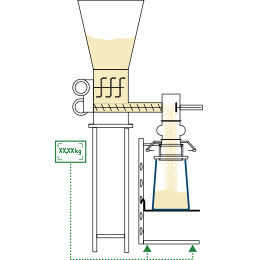
PalSack®01-M-P-Gross
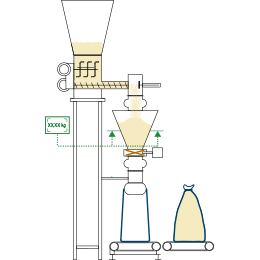
PalSack®01-J-C-Net
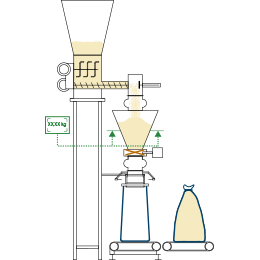
PalSack®01-M-C-Net

PalSack®01-J-P-Net
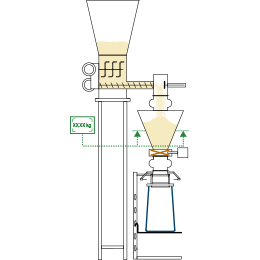
PalSack®01-M-P-Net
Equipment advantages
- Minimized retention
- Compact design and cleanability of the system
- Rotary valve for product dosing
- Clamping ring
- Confinement
Media
View our equipment in videos
Bag filling machine
Bagging station for packing spice mixtures
View our equipment in photos
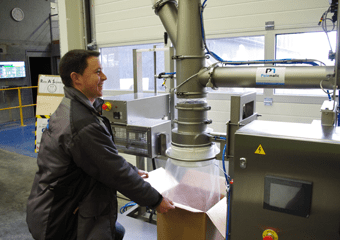
Sack filling system
Sack filling industrial equipment for the food industry. Filling bags with milk and dairy powders.
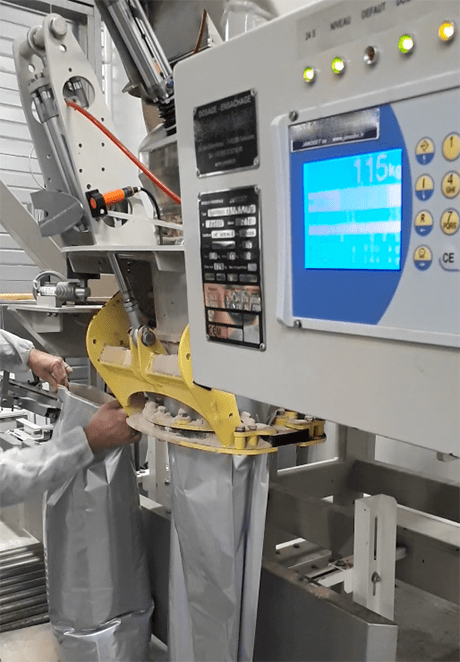
Bag filling skid
Mobile bag filling station that can be moved by the forklift truck. The filling skid is equipped with an easyclean screw feeder.
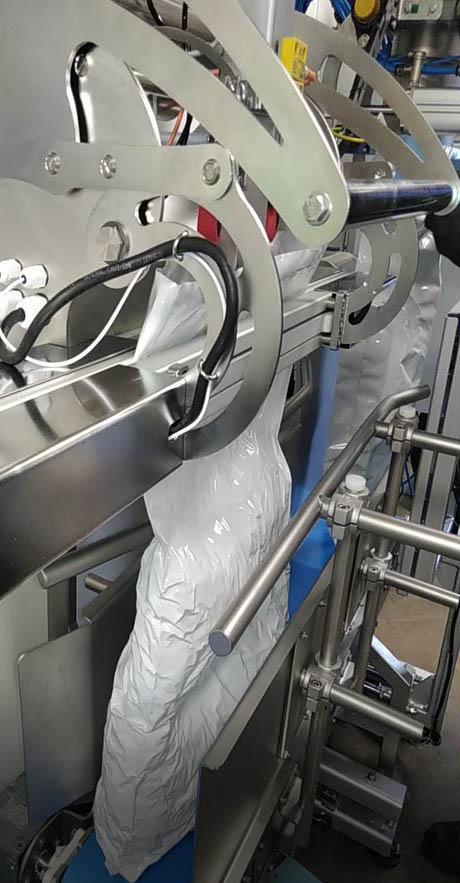
Bag sealing system
The bag packaging line is equipped with a sealing system to ensure the containment of the packaged powder.
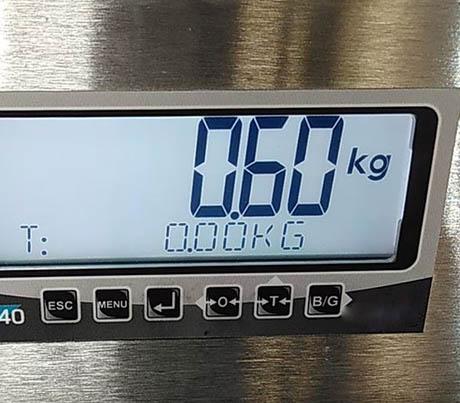
Sack filling line with weighing
Industrial weighing system on bulk pigment packaging line.
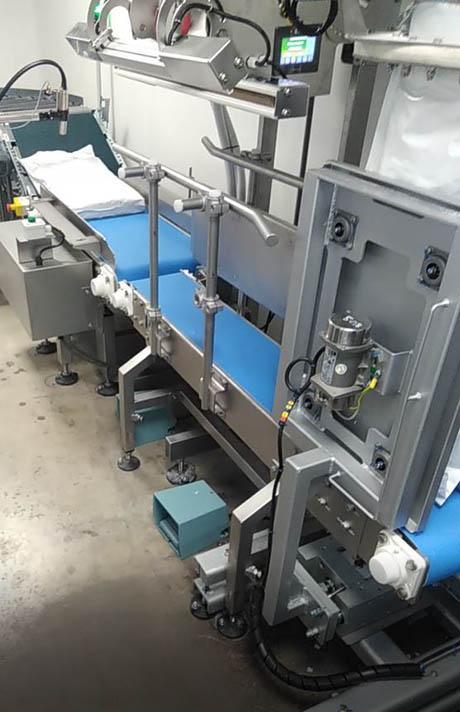
Automatic sack filling line with belt conveyor
Belt conveyor and bag packing line with integarted sealing machine for air tight closure of the bag.
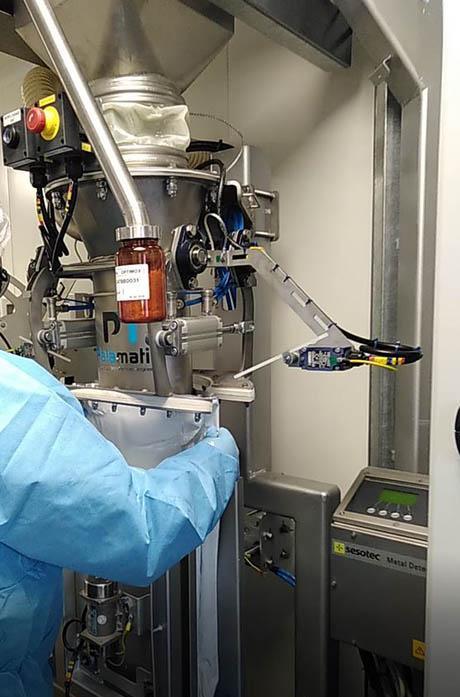
Big bag filling station bag positioning
After filling, the bag is sealed and evacuated on a belt conveyor.
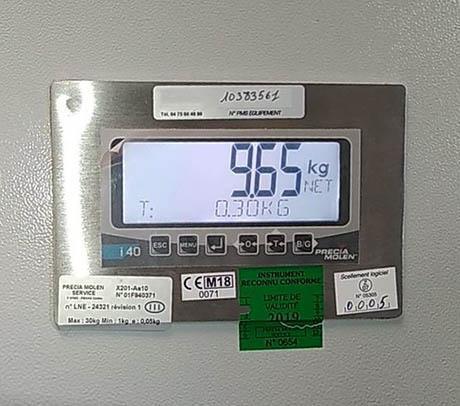
Bag filler station - commercial weighing
The bag filler is fitted with load cells that allow the gain in weight function of the flexible container.
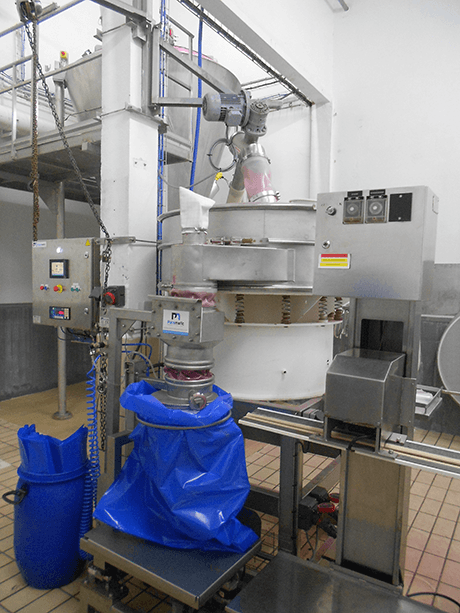
Industrial sack filling
Skid for packaging of ingredients at the outlet of the atomization tower.
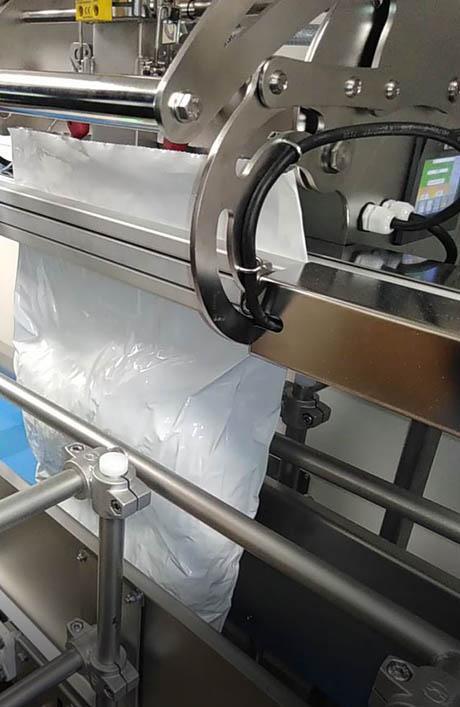
Integrated bag sealing equipment
Pulse bag sealing machine to weld the closure of the bag after the material filling phase.
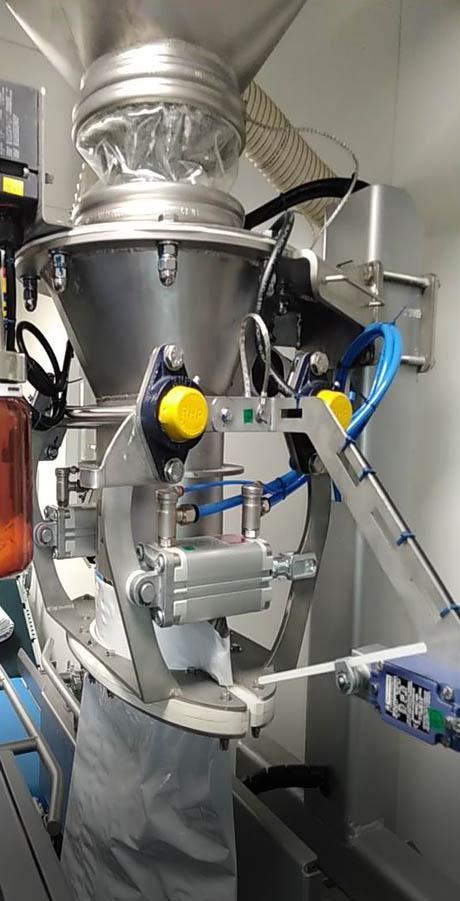
Bag filling system - Filling head
The bag filling machine is fed with bulk material via a butterfly valve installed on the buffer hopper.
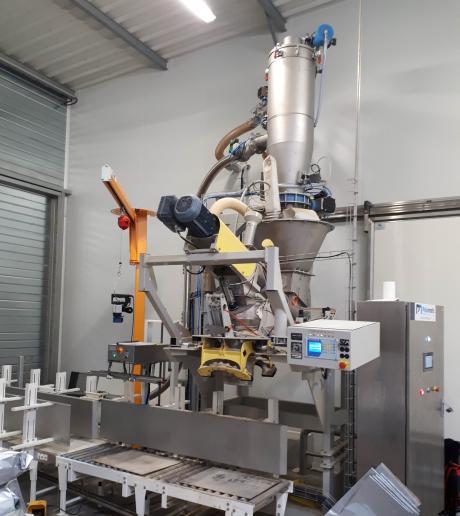
Sack filling PalSack® - Powder processing
The filling head is provided with clamps to hold the bag during the filling phase.
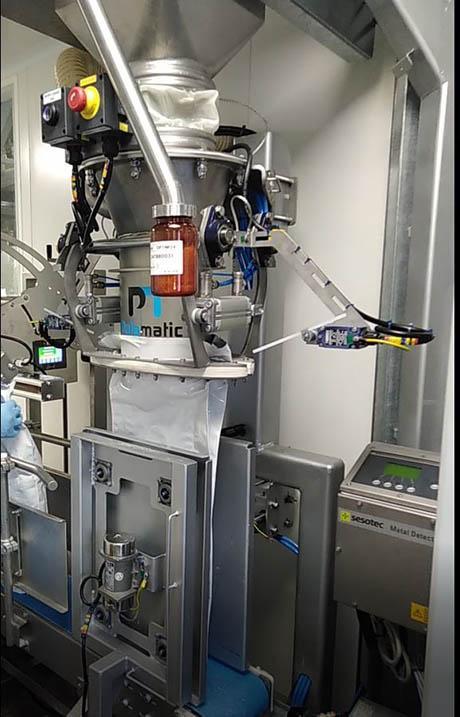
Sack filling station with bag positioning
After the material filling cycle is complete, the bag is sealed and evacuated on a belt conveyor.
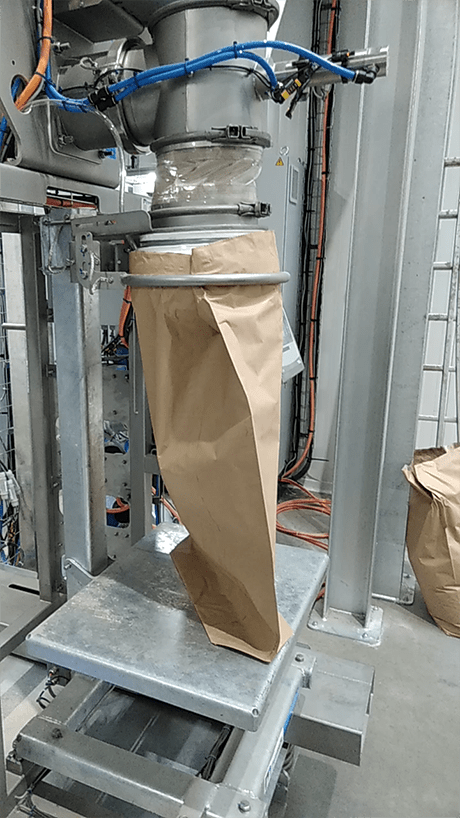
PalSack®01 - Sack filling system
This bag filler uses a D13 model screw feeder with integrated agitator, to promote material flow. Positioned under the industrial mixer, it feeds the bag packing station with an accuracy of -/+ 20 grams.
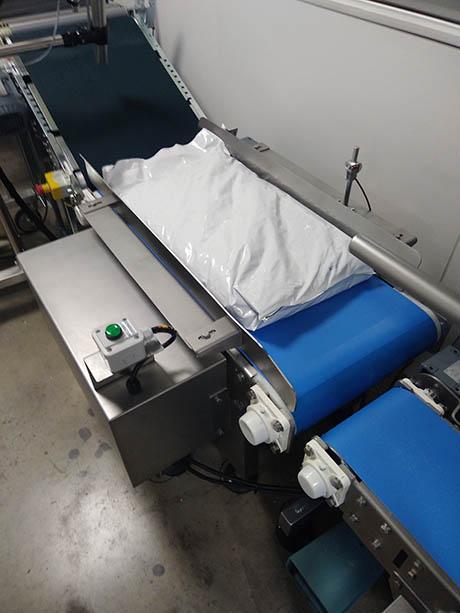
Bag filling line with weight control
Process for conveying and conditioning flakes in the petrochemical sector.
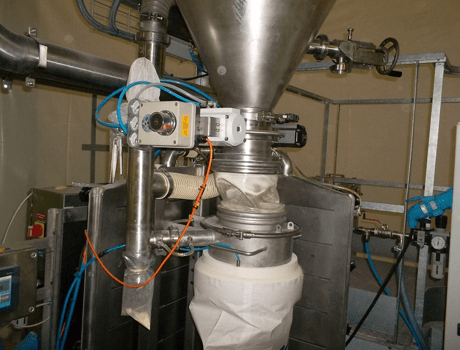
Automatic bagging system
The upstream dosing device fills the bag. The volumes are balanced via the double jacketed filling tube.
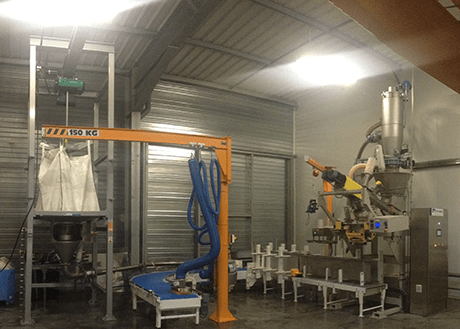
Sack filling system
The bag filler station is supplied by a bulk bag emptying station. Once the bags are filled, they are transferred via a belt conveyor and palletized by use of a vacuum bag lifting station.
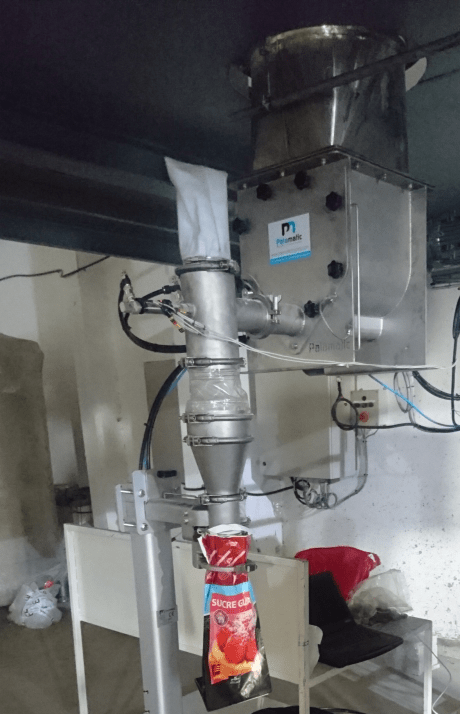
Bag filling - PalSack® 01
The powder mixture (corn, colouring, flavourings, pyrophosphate and carbonate) is recovered by a screw feeder for bagging. Several filling heads are available to match the different types of bags (5-10-25 kg).
A magnetic bar is positioned in the bag filling mouth.
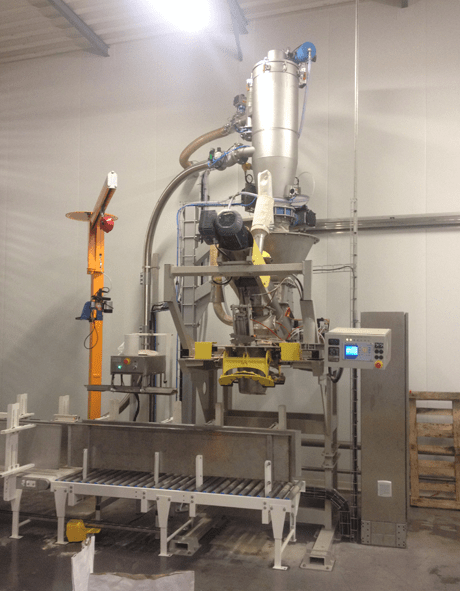
Industrial bag filling system - PalSack® 01
The bag packing station allows commercial weighing of the bags, which are then removed on a roller conveyor.
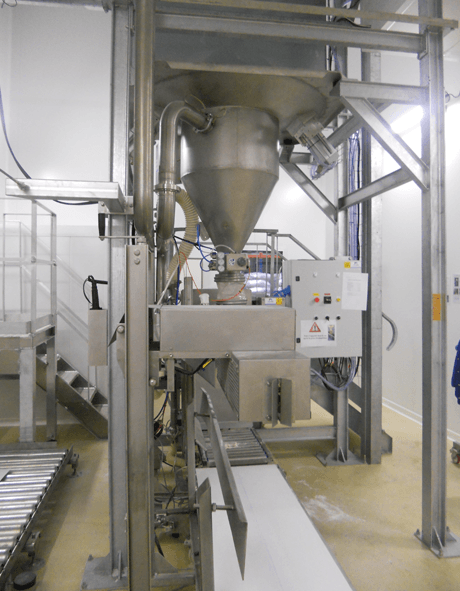
Sack filler for sugar industry
Bag filling line with belt conveyor for the packaging of granulated sugar.
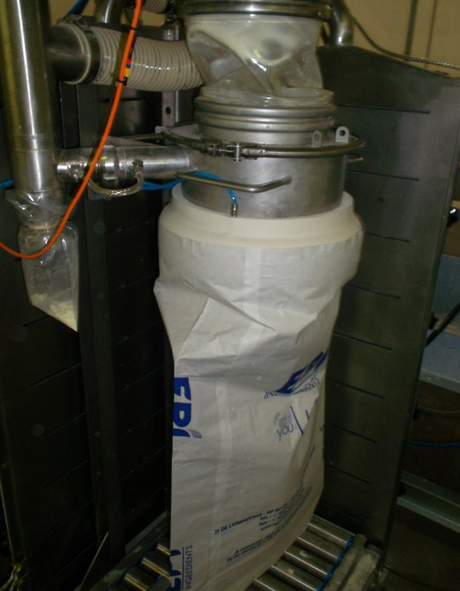
Sack filling station for food industry
Bag filler system for the packaging of animal flour on an industrial production line.
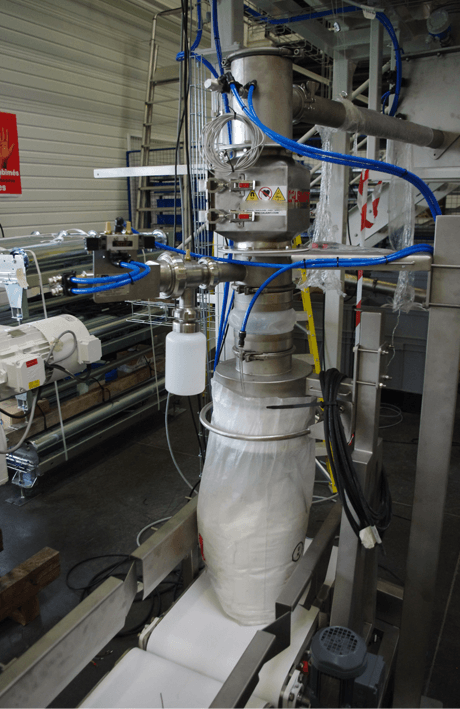
Bag filler for pharmaceutical products
Assembly of a sack filling system for packaging of citric acid powder.
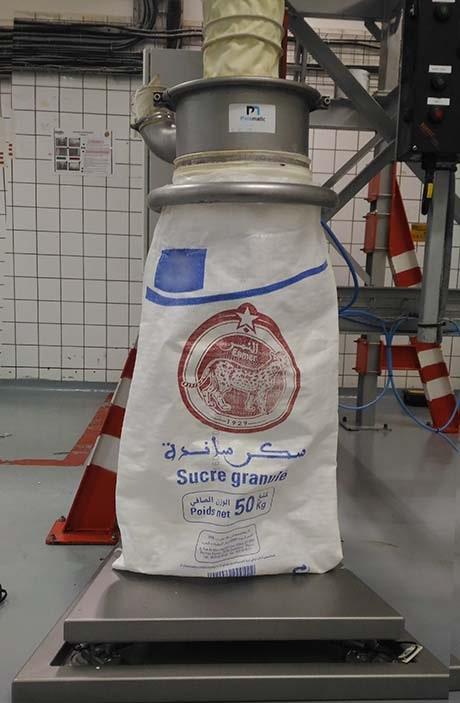
Sack filling system by Palamatic process
Turnkey industrial solution for the milling and bag packaging of icing sugar.
Features
Technical specification
Rate | 10 to 100 sacks/h. |
---|---|
Capacity | 5 to 60 kg/sack |
Manufacturing materials | Painted steel, 316L stainless steel |
Installed power | 1.5 kW |
Compressed air consumption | 0.1 Nm³ |
Dust removal rate | 100 m³/h. |
Weighing accuracy: +/- 40g
Inflatable seal: FDA
Operating procedure:
1- Bag installation
2- Docking of the bag (inflatable seal)
3- High speed filling of the bag
4- Weighing management
5- End of filling, deflation of the seal and evacuation of the bag
Our design office is at your disposal to propose solutions adapted to your process and your production requirements.
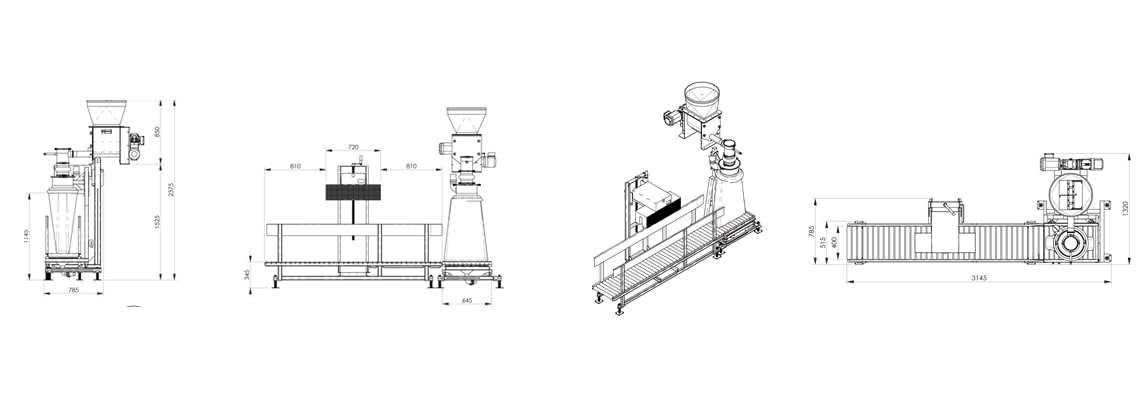
Layout of the PalSack®01-J-C-N
Options
Case studies
CASE STUDIES WITH THIS EQUIPMENT
Processing line for biscuit production factory
Processed powder: Crystal sugar - Line for biscuit factory - Food manufacturer that specializes in biscuits, chocolate and cocoa. The customer's process requirements involved the milling of granulated...Food and Animal Feed
Clean room for packing
Processed powder: milk powder - Clean room for packing - A leading dairy and manufacturer of high value-added milk powder for the leaders in the infant market.Food and Animal Feed
Packing of white, organic and brown sugar
Processed powders: refined white sugar and brown sugar - Packing of white, organic and brown sugar - Leader in Africa and the Mediterranean Basin in the sugar industry and vegetable oil industry.Food and Animal Feed
Seaweed preparation
Processed product: seaweed - Seaweed preparation - Manufacturer of organic raw material for cosmetics.Fine chemical
Cake mix
Processed powders: modified starch, sodium bicarbonate, fat powder, whipping base, gelatin, milled sugar - Cake mix - Company based in Saudi Arabia that manufactures and distributes dry food materials...Food and Animal Feed
Natural food flavours
Processed powders: apetence factors, natural food flavours - Natural food flavour - The company, which is specialized in the manufacture of flavours for domestic animal feed, was looking to install a...Food and Animal Feed
Aromatic herbs conditioning
Processed powder: dried grass seeds - Seeds conditioning - Installation of a double discharge station: big bag emptying and container emptying for mixer feeding as well as a double filling station...Food and Animal Feed
Foundation production line
Processed powders: silica and iron oxide - Foundation manufacturing line - The aim of the installation is the mixing and homogenization of the different ingredients.Fine chemical
Continuous transfer of crackers
Processed products: appetizers, snacks, chips and crackers - Continuous transfer of crackers - At the extrusion outlet, after the potato flour feed, the puffed crackers are directly collected to feed...Food and Animal Feed
Grinding and packaging of finished products
Processed products: dried insects - Grinding and packaging of finished products - Workshop for processing and packaging products for the animal nutrition sector.Food and Animal Feed
Turnkey solution for the screening, dosing and filling sacks with toxic materials
Treated powder: Lithium nickel manganese cobalt oxide - Turnkey solution for sieving, dosing and filling 22 kg bags of toxic powder. Improvement of ergonomics and operator safety.Energy