Description
Magnetic detection with magnetic bars and metal detector
The hygienic regulations require very high-quality rules regarding industrial production lines involving raw ingredients and bulk materials handling.The magnetic detector system is ideal to attract instantly ferrous particles, weakly magnetized or of very fine size. It securely holds them on its bars, keeping unwanted materials out of the final product.
The magnet positioned at the installation inlet and outlet has became a standard for numerous industries to protect the equipment and the production lines.
2 solutions of magnetic detection
- Magnetic bars
- Metal detector
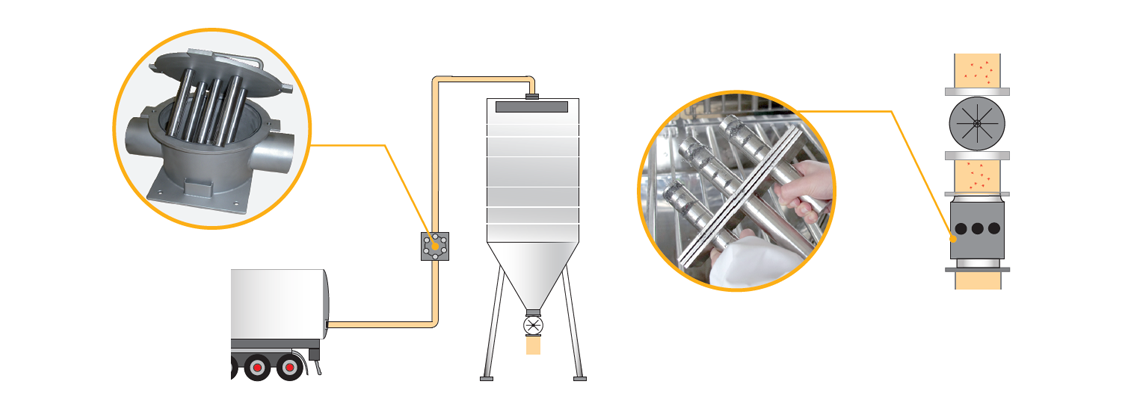
Magnetic bars
The magnetic bars helps to wipe out the problem of ferrous contamination improving product quality in numerous industries working with flour, powders, plastic granulates, sawdust etc... These bars are positioned amidst the product flow and firmly holds the ferrous particles on its bars.
3 designs:
- Static (1 ou 2 grids)
The single grid magnetic detector is designed to stop ferrous particles present in the material flow. It works by keeping the undesired material out of the final product. The quick-cleaning magnets are configured for an easy maintenance.
The section can be square or circular.
The stainless steel magnetic separator, made with two magnetic grids placed underneath each other, provides the same advantages as the single magnetic grid but it is more effective due to its special layout; it ensures the quality material of the final product and limits a number of cleaning interventions.
- Rotative grid
The rotative magnetic bars enable the detection of all types of metals to provide a clean material as well as protect your bulk handling production line. The rods are arranged in a circle which rotates gently agitating the material and maintaining its flow.
- Inline on pneumatic conveying lines
They guarantee (in dry phase) the purity of bulk materials with optimum decontamination of particles from 20 µm and eliminates ferrous objects.
The magnetic bars are installed on the pneumatic conveying pipes.
Metal detector
This gravity metal detector is manufactured to suit any gravity application. This system is ideal to manage the free-flowing material regardless its location on the industrial production line. When powders or bulk materials pass through the metal detector, the small ferrous contaminants are immedialty separated from the flowing bulk material.
The equipment can be equipped with an automatic waste flange system. It is the optimal solution to control cocoa, coffee, sugar, aromas, fruit and dry vegetables, flour, rice, chemical powders and plastic granulates.
-
Hygiene5
-
Ease of implementation5
Equipment advantages
- Qualify raw materials as soon as they are delivered to you
- Avoid foreign bodies in manufacturing processes
- Prevent machine damage
- Ensure a high quality end product
- Detection and capture at the point of entry
- Detection at the end of the production line
Media
View our equipment in photos

Magnetic bars for magnetic separation
Magnetic detection on a detergent powder storage unit.
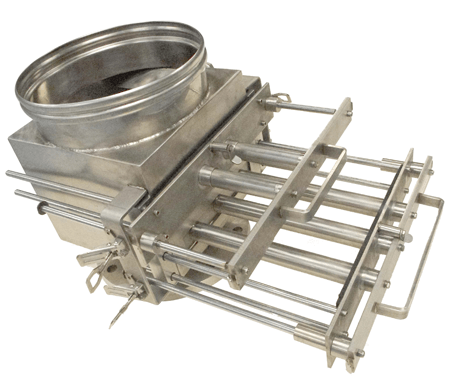
Magnetic detector with circular section
Metal detector on food additive dosing line with cleaning in place of all equipment.
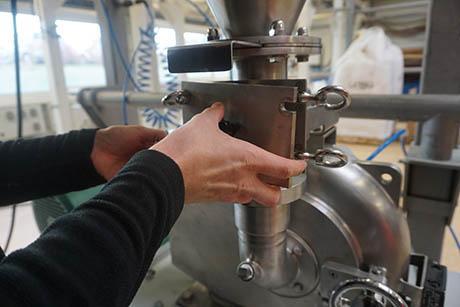
Magnetic detector on crushing mill
Magnetic detection on a big bag discharge line of of bleaching agents for tank feeding.
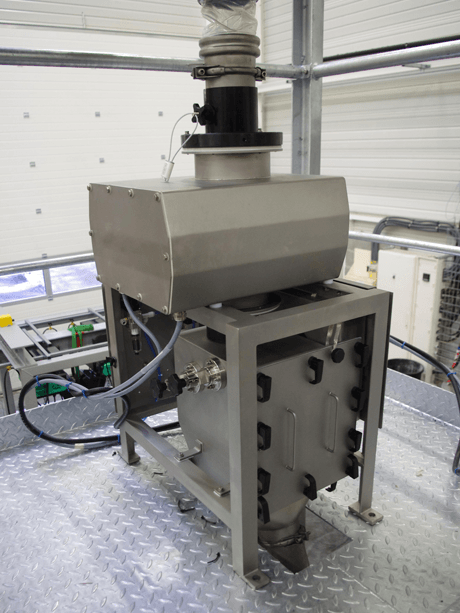
Magnetic detector on box packing line
Removal of metal contamination from powders and granules on industrial production lines.
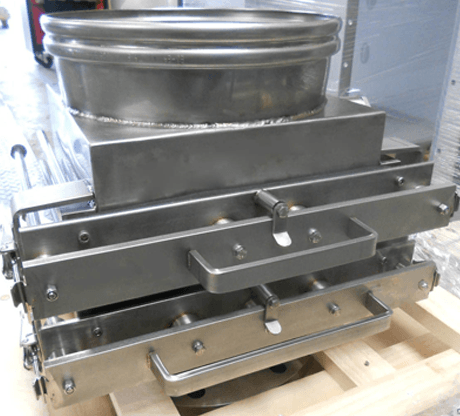
Static magnetic detector for industrial production lines treating raw ingredients and bulk materials
Magnetic bars on a pneumatic gelatin conveying line for coating capsules to feed a weighing hopper.
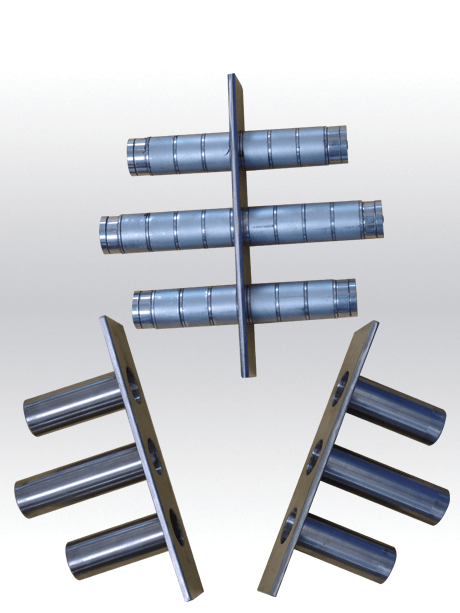
Cleaning of the magnetic bars
Magnetic bars on a big bag packing line with a capacity of 40 big bags per hour.
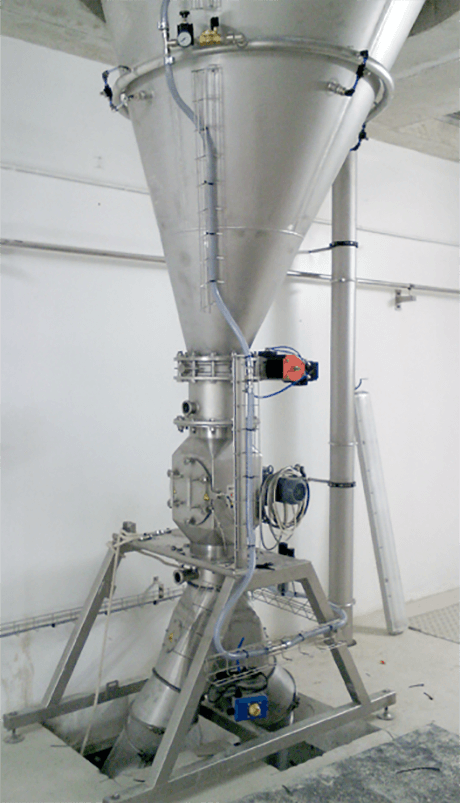
Magnetic bars on milk powder production line
Considering a difficult product flowing, the rotary magnetic bar technology enables keeping a high throughput as well as guarantees a high quality of the material.
The rotary solution guarantees the throughput of difficult bulk materials.
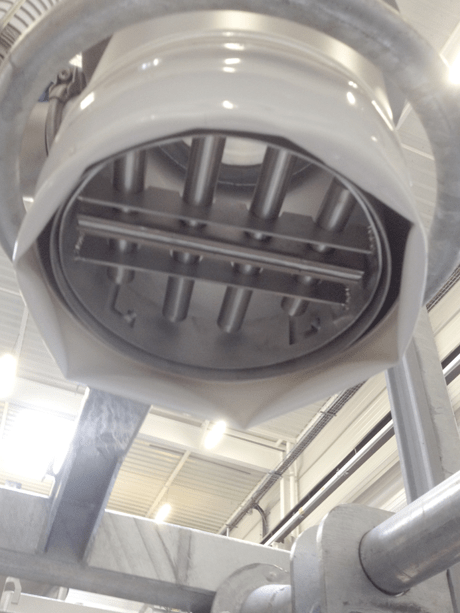
Big bag filling station for food product with magnetic detector
Process for food materials "spraying": magnetic detection with bars as close as possible to the big bag loading station. The bulk material packed is free of contaminants.
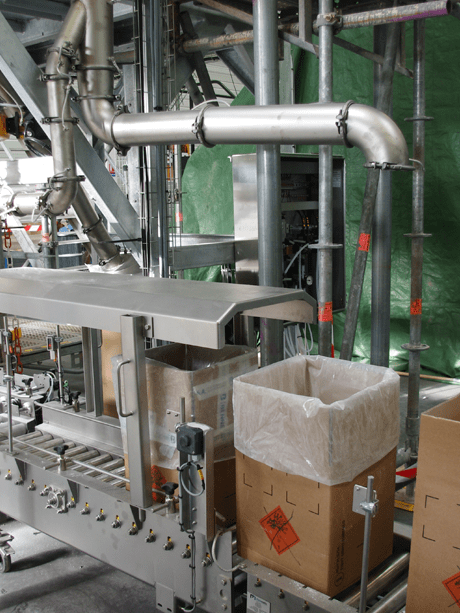
Magnetic detector with ejector on box conditioning line
The Palamatic Process metal detector removes all metal contamination from your powders and granules.
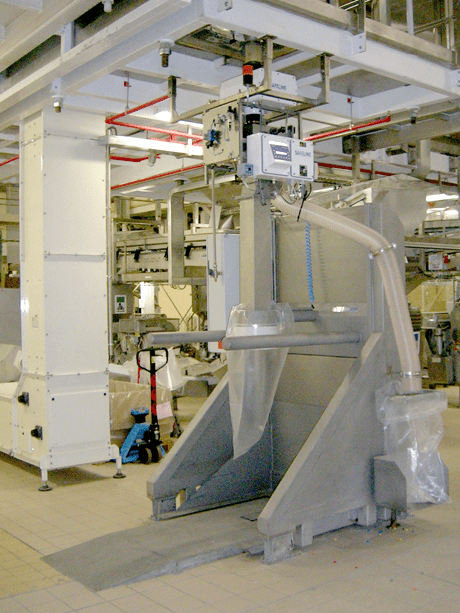
Magnetic detector on bulk bag of chocolate beads filling station
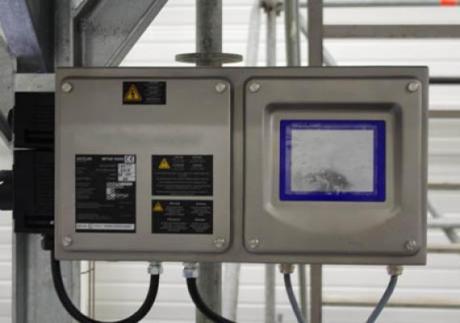
Cardboard box conditioning line: magnetic detector with ejector
If a foreign body is detected when the product passes through, a quick-acting cylinder then "bypasses" the inlet chute on the side to a waste collector.
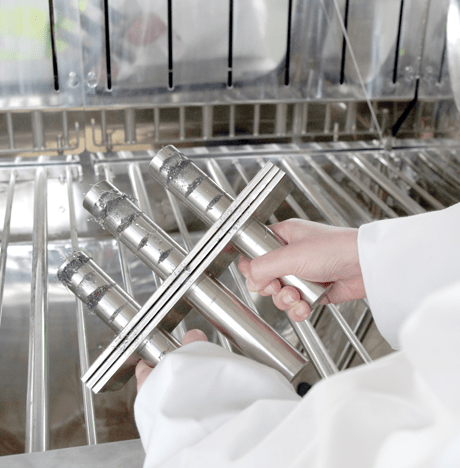
Magnetic detection on milk powder production line
Magnetic detector on a big bag packing line in a hygienic zone (white zone) for baby food products.
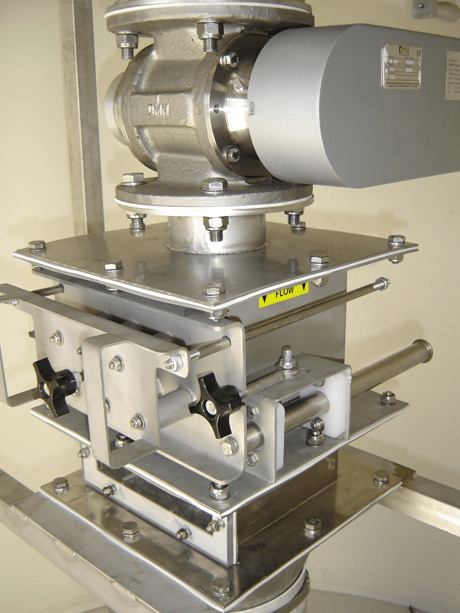
Magnetic detector on pneumatic conveying line
The magnetic bars, installed on the pneumatic conveying line, control the materials coming from various loading points. This configuration optimizes the investment cost and compact design.
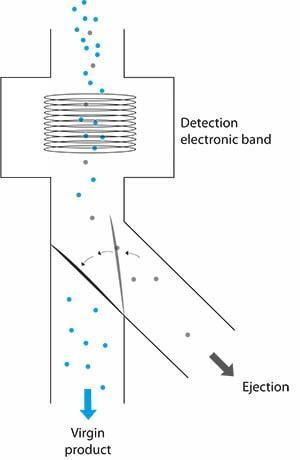
Double magnetic detection bars under silo
Directly set under the storage silo, the magnetic double grids feeds the pneumatic conveying pipeline. To facilitate the daily control of the production line, a magnetic drawer is installed under the rotaty valve with easy access to the magnets. The mechanical design of the drawer ensures high resistance to pressure.
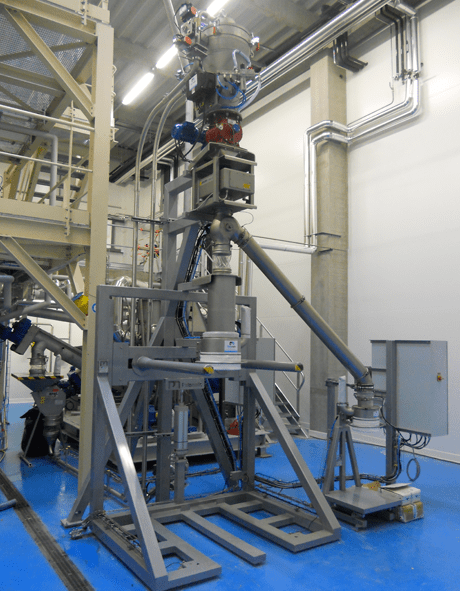
Magnetic detector on big bag filling FlowMatic® 03
Integrated equipment:
- FlowMatic® 03 - Big bag filling station
- Clamping ring
- Palsack® - Sack filling station
- Drop through rotary valve
- Magnetic detector
- Industrial automation
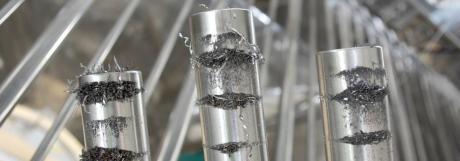
Magnetic detector screen
Magnetic detector on bulk or powder conveyor.
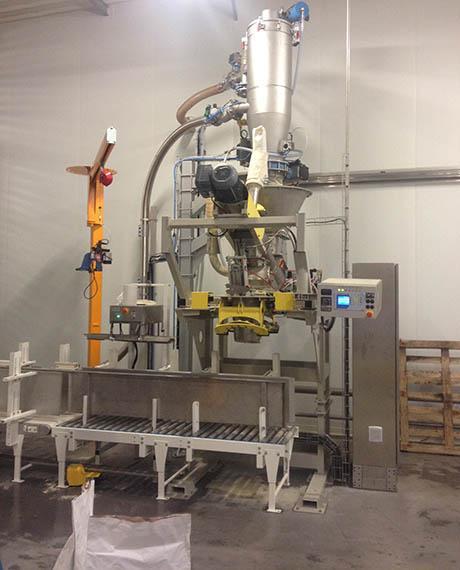
Magnetic detector on sack filling unit
Magnetic detector on a conditioning line of animal flour in big bags.
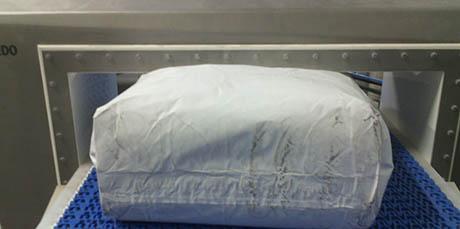
Belt conveyor with magnetic detector
Magnetic detection of bags of powder on a belt conveyor.
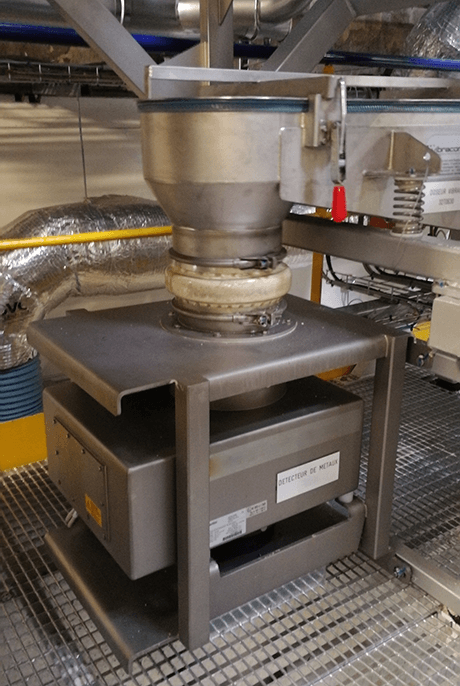
Magnetic detector on pneumatic conveying line
Metal detector on a line for discharging and crumbling resinous products.
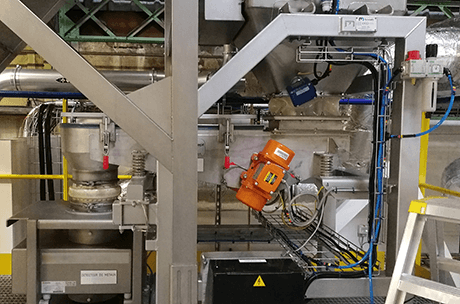
Processing line with magnetic detection
Magnetic detection on a food additive dosing line with cleaning in place of all equipment.
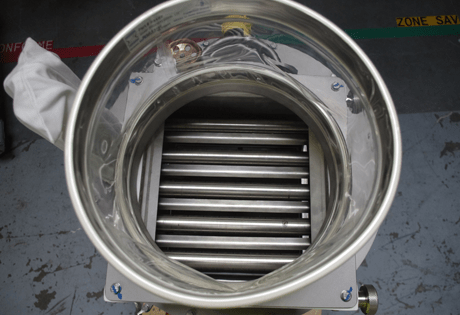
Magnetic bars on filling head
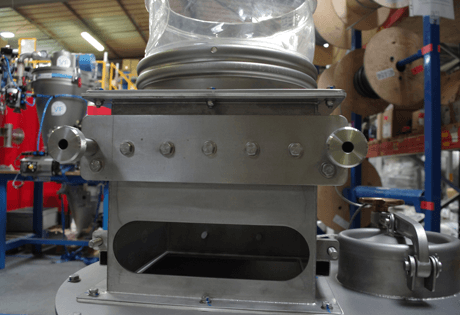
Bulk processing line magnetic detection
Magnetic bars under flexible connection sleeve on cake mixing production line.
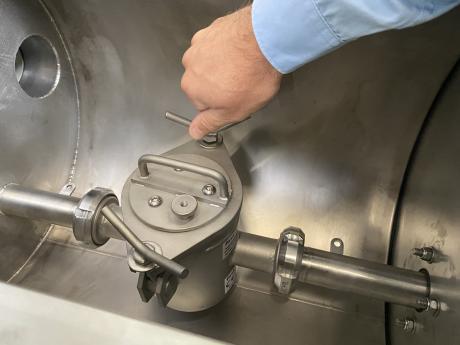
Pneumatic conveying line with magnetic detection
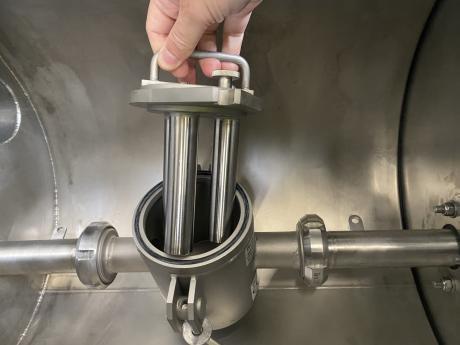
Easy dismantling of the magnetic detection system
Features
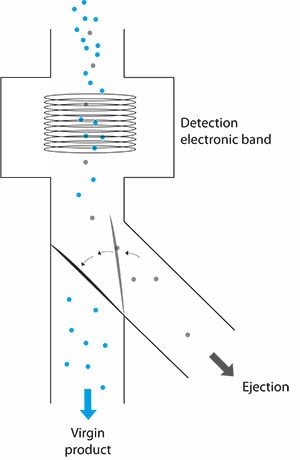
Specific features of magnetic detectors
- Excellent detection of ferrous particles, resistance to maximum interference and high reliability.
- Permanent and automatic self-calibration with self-balancing and temperature compensation.
- Fully automatic operation is guaranteed after setting the level of sensitivity and the duration of ejection to the desired values.
Case studies
CASE STUDIES WITH THIS EQUIPMENT
Infant milk powder preparation
Product concerned: infant milk powder - Infant milk powder preparation - Industrial specialized in baby food production - The process consist of conditionning infant milk powder in diverse containing...Food and Animal Feed
Chocolate beads handling
Processed products: chocolate beads - Storage in big bag - This customer is a world-renowned manufacturer and produces very fragile chocolate beads that are intended for packing (B to C).Food and Animal Feed
Loading of ingredients for the production of beverage
Processed materials: citric acid, potassium sorbate, sodium benzoate... - Loading of ingredients for the production of beverage - This installation concerns a new production line in a new building of...Food and Animal Feed
Loading silos with sugar
Processed materials: crystal sugar - Loading silos with sugar - A container tipper is used to feed the high pressure pneumatic conveying network to feed 2 silos of 50 tons.Food and Animal Feed
Refined sugar conveying
Processed material: refined sugar - Refined sugar conveying - On-site installation of repackaging equipment for the transfer of sugar stored in shipping containers with an inner liner to a bulk bag...Food and Animal Feed
Dried tomato powder process
Processed product: dried tomato powder - Industrial process for tomato products - The application requested by the customer is the filling of big bags and cartons at the outlet of the atomization...Food and Animal Feed
Capsule production line
Processed Powder: pharmaceutical capsules - Capsule production line - At the exit of the capsule manufacturing lines (after forming, filling and drying), the client needed to count the number of...Fine chemical
Grinding and packaging of finished products
Processed products: dried insects - Grinding and packaging of finished products - Workshop for processing and packaging products for the animal nutrition sector.Food and Animal Feed
Spray tower for packaging feed
Processed powders: skim milk powder / whole milk powder. Client in Africa.Food and Animal Feed
Production of dried fruits and seeds
Processed powder: dried fruits and seeds - Mixing and packaging - Our customer wanted to implement a new production line in its plant to support its growth.Food and Animal Feed
Cardboard box confined packaging station
Cardboard box confined packaging station - Powder dosing line at dryer outlet for cardboard box packaging feed.Energy