Description
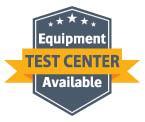
CONTAINED MANUAL BAG DUMP - SACKTIP SE OEB - SUITABLE FOR TOXIC OR DANGEROUS PRODUCTS
Optional integrated dedusting
Made of steel or stainless steel
Sacktip® SE is a dump station suitable for handling toxic or dangerous bulk materials. The sealed door with glove box allows the total containment of the powder and the protection of the operators during the bags opening operations.
Contained manual sack discharging range
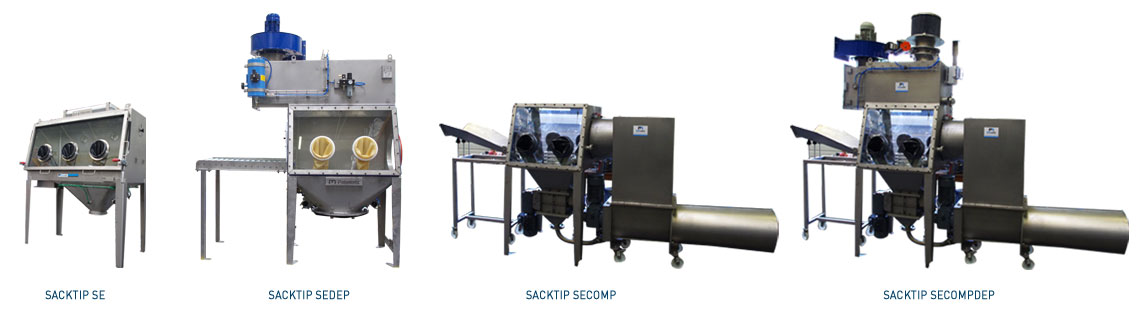
Drain for dangerous or toxic products:
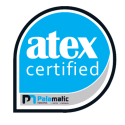
The SACKTIP SE OEB bag dump stations ensure the manual deconditioning of bulk materials that are delivered in bags at the production sites.
These bag dump stations, manufactured in steel or stainless steel and with an ergonomic design, allow the bulk materials to be stored and transferred to the production line without air contamination by dust emissions during the bag opening and discharge process. All cabins are equipped with dust extraction nozzles or integrated filters. Gloves, positioned on the glass door, allow to safely handle bags that contain dangerous or toxic materials.
The range of manual bag dump stations is ergonomically designed to provide a perfect solution for your manual unloading needs. Palamatic Process bag emptying stations are designed to significantly reduce the risk of air pollution by dust emissions during the manual bag opening and discharge process.
All bag dump stations are equipped with dust extraction nozzles or integrated filters
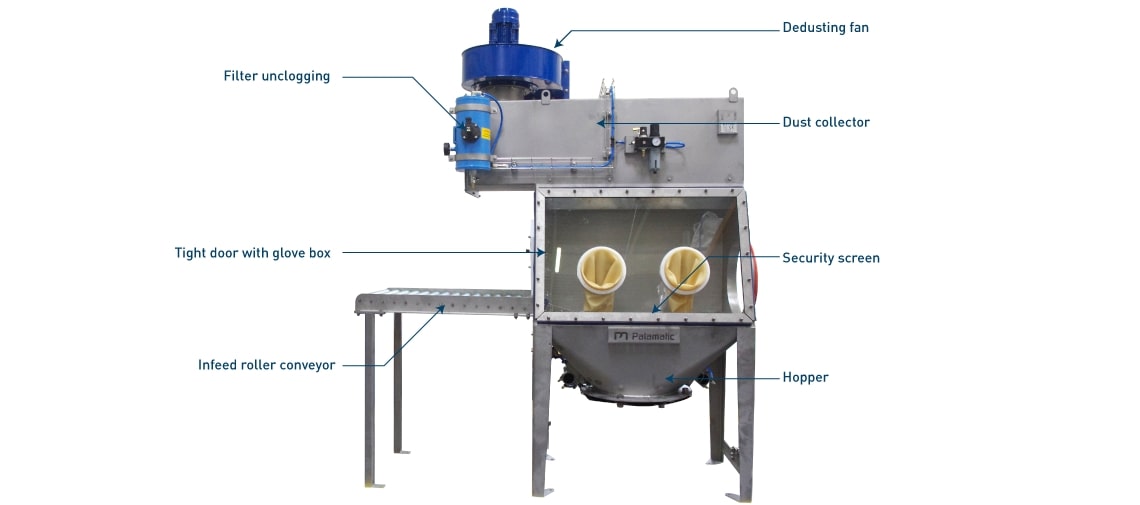
Operation procedure:
The operator places his bag on a laterally arranged roller conveyor and introduces it into the machine body on the screen provided for this purpose. Sliding bars facilitate the introduction of the bag into the heart of the machine. He can then open the bag and empty it. Once it is completed, the operator evacuates the empty bag to the compactor on the side opposite the roller train.
This machine is designed for the manual opening of all types of bags, limiting dust emissions by adding a dust removal unit and an empty bag compactor. Its ergonomic design ensures that the operator has an efficient and reliable workstation.
A dust extraction nozzle is provided on the top of the machine.
For parts in direct contact with the product and other parts that are not in direct contact with the product (door), the manufacturing materials to be defined are as follows: painted steel, stainless steel 304, stainless steel 316L, plexiglass, safety glass.
-
Rate2
-
Automation1
Equipment advantages
- Glove box for handling the product in a dust-tight container
- Holder for bag opening tool which is secured by its attachment cable
- Mirror polished finishing touches to improve product flow and ensure total hygiene
- Side bag evacuation chute to avoid cluttering the work area and store empty bags in a "confined dirty" area
- Perfect ergonomics
- Healthy working atmosphere
Media
View our equipment in photos
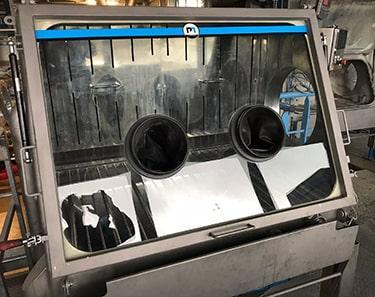
Sacktip® SE Palamatic Process
Discharging of bags with integrated glove box for handling the product in a vacuum: glass and gloves.
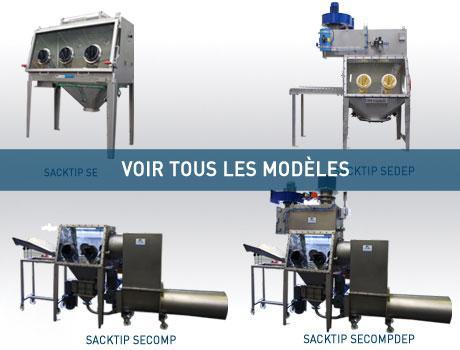
Gamme Sacktip SE
- Vidange de produits toxiques ou dangereux
- Parfaite ergonomie
- Atmosphère de travail saine
- Confinement poussé
- Protection des opérateurs
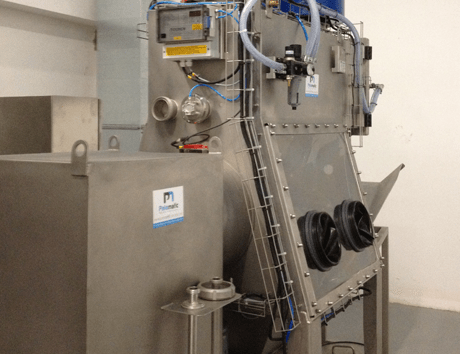
Sack manual discharging - Glove box
Glove box for handling bulk material in a closed container: glass and gloves.
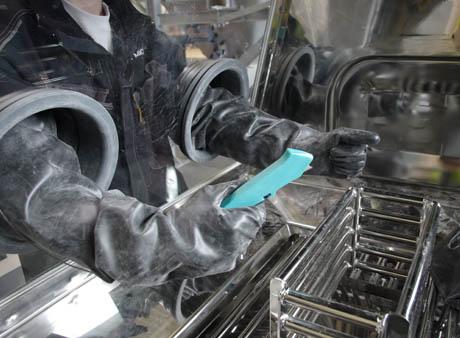
Containment - sack discharging
Dust-tight door with glove box.
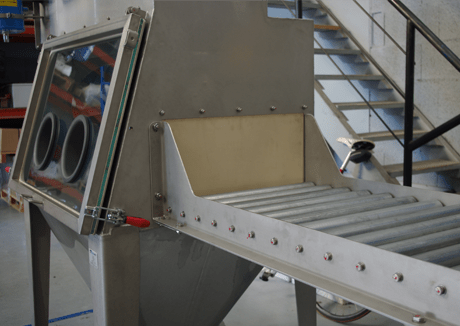
Contained manual sack discharging
Roller infeed conveyor - bulk material handling equipment.
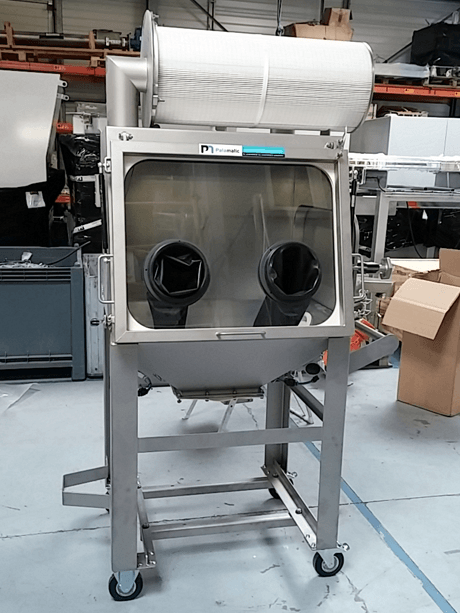
Contained manual bag dump station
Mirror polished finish to improve bulk solids and raw materials flow and hygiene.
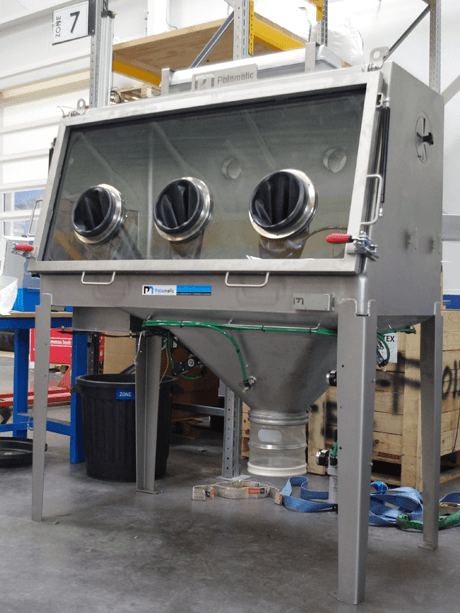
Powder processing bag dump station
The bags can be introduced by a dust tight airlock valve system (other alternatives: belt conveyor, roller conveyor...)

Bag dump station
Ergonomics and containment for toxic bulk materials.
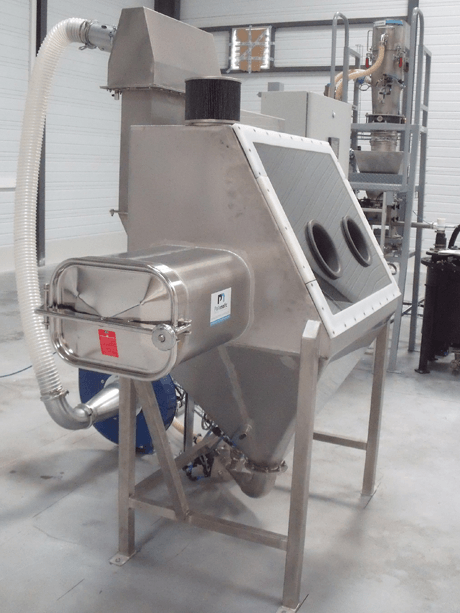
Sack discharging system
Airtight SAS for bag insertion.
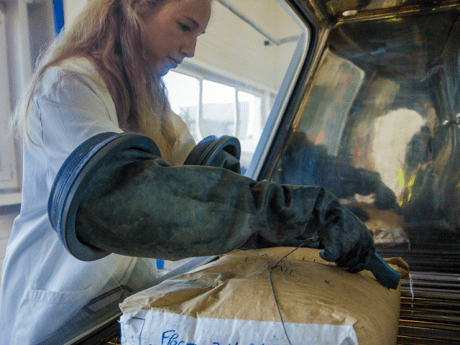
Contained sack discharging
Secure opening tool with a holding cable.
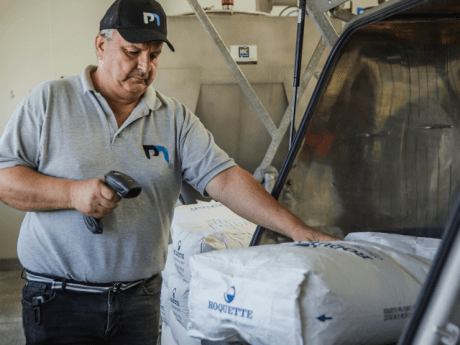
Tracking of bags
For batch management and process safety.
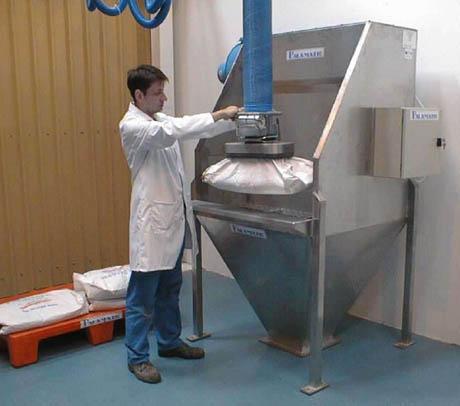
sack manipulator
For effortless lifting and handling of the bag.
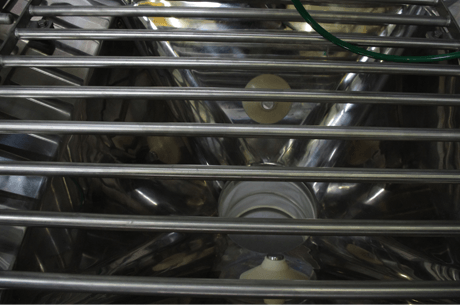
Contained manual bag discharging
The mirror polished finish is particularly suitable for the pharmaceutical sector.
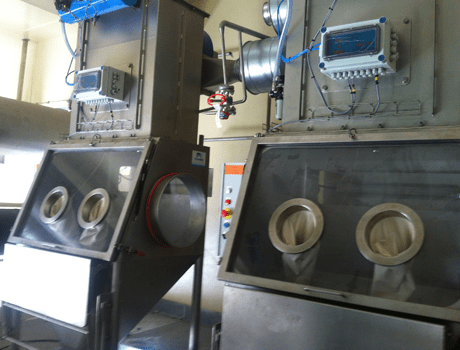
Double bag emptying station - Glove box
The gloves are mounted on the door and are mounted on PVC glove rings.
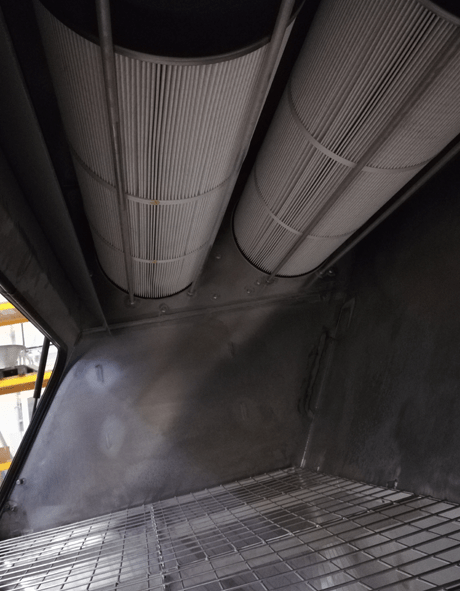
Bag dump station with dust collection
Dust extraction fan to maintain a healthy atmosphere.
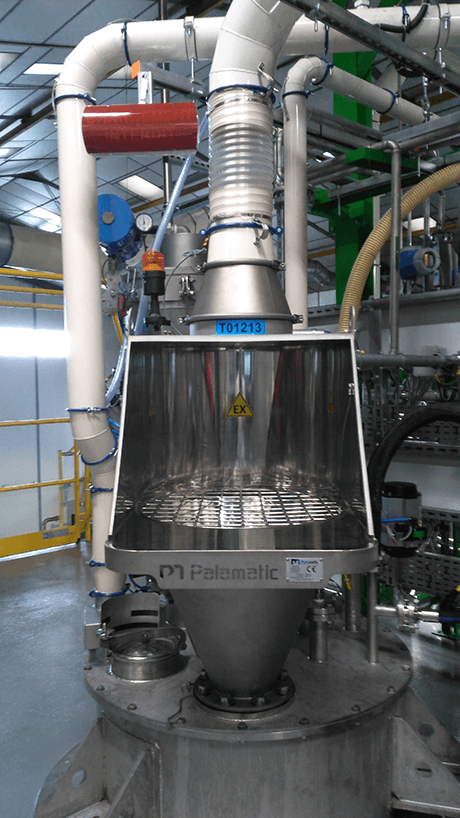
Custom manual bag emptying
All equipment can be configured according to your requirements. The Palamatic Process design office is able to offer you very specific solutions.
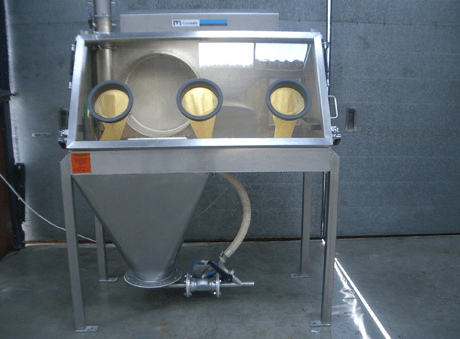
Contained sack discharging
Dust tight manual bag dump station with a tight door with glove box.
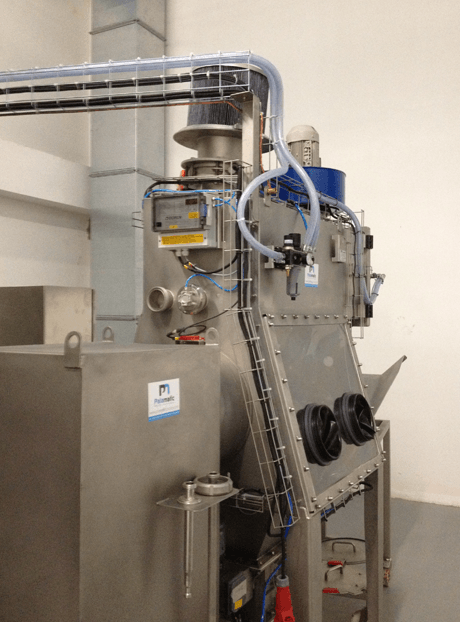
Contained sack discharging - Food powder
Possibility of unpacking drums as an option.
Features
Technical specification
The door remains hinged by a gas cyliner and the compression of the door seal is carried out by clamps securing the closing. Thus, the closure is sealed.
A removable mesh screen at 50 x 50 mm with 2 mm diameter wire is placed above the powder chute. Sliding bars placed on the screen allow the operator to move his bag with a minimum of effort.
Flow rate | 2 to 6 sacks/min. |
---|---|
Access door | Painted steel, 304L stainless steel, 316L stainless steel, plexiglass, anti-static lesan, tempered laminated glass |
Manufacturing materials | Painted steel, 304L stainless steel, 316L stainless steel |
Convoyor | Custom RAL, bead-blasting, electropolishing |
Gloves: latex, natural rubber, polyurethane, Hypalon, Butyl
Tightness: EPDM, NBR, natural rubber, silicone
Standard models of the range:
Model | Length of the bags to be handled (in mm) | Flow rate for dust extraction nozzle (m³/h) |
Hopper water volume (Liters) |
Outlet diameter (DN) |
Height from ground to outlet flange (mm) |
---|---|---|---|---|---|
SE 800 | 650 | 400 | 180 | 250 | 285 |
SE 1000 | 850 | 500 | 265 | 250 | 285 |
SE 1200 | 1,050 | 600 | 265 | 250 | 285 |
SE 1400 | 1,250 | 700 | 300 | 250 | 285 |
Options
Case studies
CASE STUDIES WITH THIS EQUIPMENT
Loading tank
Processed powder: very dusty and toxic bulk material - Loading tank - The objective of the installation is to contain the powder to avoid any dispersion during the different stages of conveying.Chemical
Bag and drum handling
Processed powder: Potassium Bi-Fluoride - Drum and bag handling in the nuclear sector: 25kg kraft paper bags with an inner liner and 90kg drums with an inner liner.Energy
Natural food additives
Processed powders: sodium bicarbonate, strain (bacteria) - Natural food additives - This industrial production line consists of the installation of bag dump station Sacktip® SE 800.Food and Animal Feed
Contained feeding of pharmaceutical ingredients
Processed material: titanium dioxide - Contained feeding of pharmaceutical ingredients - Big bag discharge by vacuum pipe for the contained feeding of pharmaceutical ingredients.Fine chemical
Unloading and conveying of cement
Processed powder: cement - Unloading and conveying of cement - Unloading of cement from 1 ton big bags with pneumatic transfer of material to silo storageMinerals and building
Secure and Optimize the Handling of Sensitive Powders in Industry
Powders handled: lithium, NMC compounds (Nickel, Manganese, Cobalt), and anode/cathode materials (graphite, LiFePO4), which require secure handling due to their toxicity, hygroscopic nature, and...Chemical
Safe preparation of pyrotechnic powders: automated dosing and mixing line
Treated powders: ammonium perchlorate Safe preparation of pyrotechnic powders: automated dosing and mixing lineDefense
A compact, hygienic and mutlti-stream solution to secure feeding of process tanks
Processed powders: lactose, permeate, various milk powders Automation of powder transfer and dosing in the dairy industryFood and Animal Feed