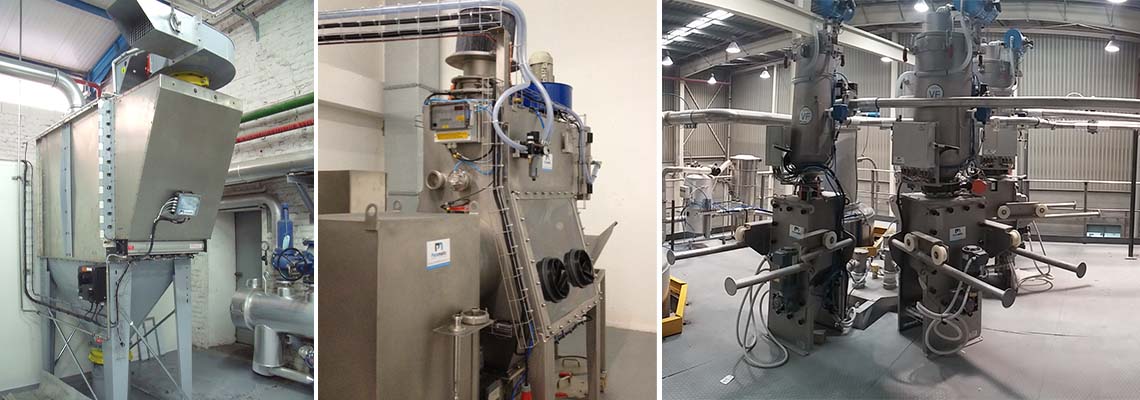
For every manufacturing facility that uses powders and bulk solids in their production process, dust collection and containment is a crucial requirement for maintaining a safe and healthy workplace. There are several mechanisms and types of equipment that can help accomplish this.
1. De-Dusting Rings
De-dusting rings, also known as Pouyes Rings, are used on material loading points that are considered manual operation. Workers may need to charge the materials directly into a storage hopper or mixing vessel. Pouyès rings are dust collectors intended for loading tanks, reactors or cylindrical containers.
Dust collection rings protect the operator's working environment by capturing particles directly at the emission source. Its simple design consists of an open inlet with bottom connection flange and a tapping to connect a hose back to a central dust collection system. By pulling a vacuum on the surrounding atmosphere, dust is captured as material is fed through the inlet.
They are commonly used in the following types of operations:
- Filling hoppers by small sacks of powder
- Reactor loading
- Drum filling
- Around the inlet of a mixer
- Dust removal from workstations
2. Physical Containment
One way to control fine particulates from freely floating around your facility is to design equipment to be dust tight. One of the best examples would be sack tip trays and bulk bag unloading equipment. Typically, these units are designed to allow the operator to open an access door to either untie the discharge spout on a bulk bag, or in the case of sack tip trays, directly load the bag onto the dump station tray. The operator would then manually open the container to release the material.
Glove boxes can be used to provide a physical barrier between the operator and the container. By having a glass window with glove attachments, the operator can cut or untie the bag and prevent any exposure or direct contact to the material inside. Also, surrounding production equipment with a poly-glass containment field can further isolate the surrounding area from exposure to toxic particulates.
3. Vacuum Conveying
Material conveying equipment is an essential requirement in any bulk material process. There are various ways to transfer material from your plant’s loading point to its final packaging destination. Mechanical conveying, pneumatic conveying, screw conveyors, etc. are all used in some form between production equipment and some tend to produce more dust than others.
However, vacuum conveying is one of the cleanest methods for conveying dry materials. Even if your pipe network forms leaks, the leak will be from the outside to the inside. With pressure conveying systems the leak would be from the inside to the outside, causing material spillage and dust in the atmosphere. The reason is simple, by pulling a vacuum from the feed source to the delivery point, there is almost no chance the material will leak outside the pipes. Also, by using a cyclone at the end of the material conveying system, a dust filter can be directly built into the top of the collection hopper. The heavy particulates spin around the cyclone and settle at the bottom and the dirty air is separated and scrubbed through the filter at the top. That way the clean air is delivered to the vacuum pump, keeping the area clean and the pump in prime operating condition.
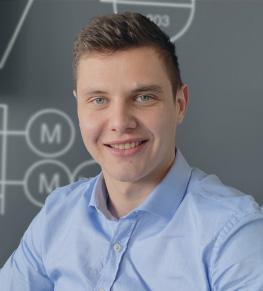
Do you need advice on dusting or dosing?
I am available to discuss the subject.
Loïc, powder expert
4. Central Dust Collection
Centralized dust collectors are used as the main source for the entirety of an industrial production process. The dust is separated from the air flow by means of filter elements with flat or folded pleats. A dust filtration equipment supplier must calculate all the necessary collection points and CFM (airflow in cubic feet per minute) required to pull the necessary amount of air into a central unit.
The heart of the system is the central baghouse which consists of a steel housing, horizontally or vertically inserted filter elements, a collection hopper for the dust to be discharged from and a pneumatic reverse pulse jet air cleaning system integrated in the filter access door. All elements, including the fan size and capacity of the central dust unit, will be designed based on the production facilities needs. Typically, it is oversized to allow for future process expansions and hook ups to the system.
5. DosingMatic process line
Palamatic Process has designed an automated ingredient dosing system called the DosingMatic®. This system is designed to prepare and balance all dry ingredients in weighed batches. The dosing shuttle automatically shuttles back and forth under loss-in-weight dosing hoppers and is filled via screw feeders. In this way the ingredients are prepared in a mobile weighing hopper and moved to a downstream connection point (pneumatic conveying system, screw conveyor, mixer, etc.). Weighing cells incorporate a buffer volume ranging from 50 to 300 liters depending on the requirements for each recipe. The system can be designed to incorporate anywhere from 10 to 40 loading hoppers. By automating the dosing of dry ingredients in a contained manner, dust exposure is significantly reduced.