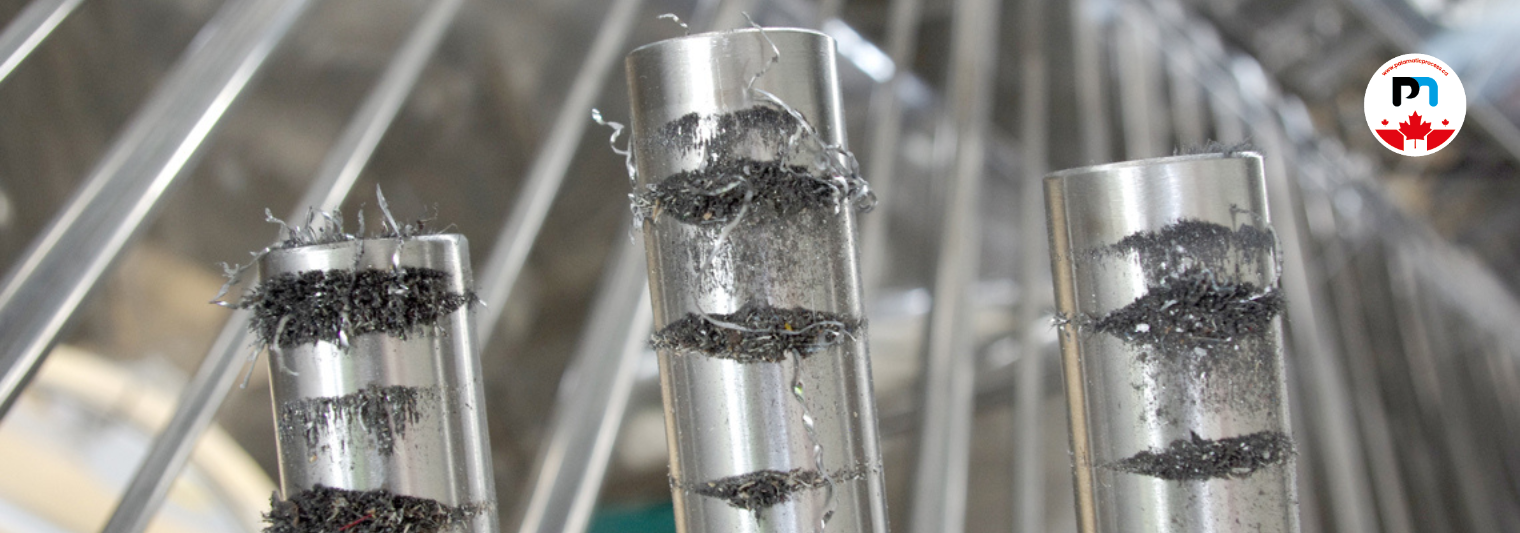
Metal contamination is a major issue in the powder industry, particularly in the food, pharmaceutical, and chemical sectors. To ensure product safety and regulatory compliance, strict standards govern the use of metal detectors and magnetic separators.
This article explores the main regulations in force and their impact on manufacturers handling powders.
1. Why regulate metal particle detection?
Risks associated with metal contamination
The presence of metal particles in powdered products can have serious consequences for consumer health and result in significant economic losses for the companies concerned.
Consequences for consumer health:
- Risk of ingesting foreign bodies: The presence of hard, sharp or pointed foreign bodies in food products poses a real danger to consumers if accidentally ingested.
- Hospitalizations related to the ingestion of foreign bodies: The ingestion of foreign bodies accounts for approximately 4% of endoscopic emergencies in adults.
Industrial and economic consequences:
- Frequency of product recalls: Physical contamination, particularly by metal particles, is a common cause of product recalls in the food industry.
- Specific examples of recent recalls: Bread, bakery products, and frozen foods have been recalled due to the possible presence of metal foreign bodies.
- Economic implications: Product recalls result in high costs for companies (direct losses, reputation, trust).
Sectors affected
Metal contamination affects several industrial sectors, each facing specific challenges.
- 1. Agri-food: Powdered products such as flour, milk powder, and spices are particularly vulnerable. Recalls due to the presence of metal foreign bodies are frequent.
- 2. Pharmaceutical industry: The presence of metal particles can alter the effectiveness of medicines and pose risks to patient health. Good manufacturing practices require strict monitoring.
- 3. Chemical and plastics industry: Metal particles can affect the quality of finished products (defects, non-compliance). Detection is essential for quality and safety.
2. What are the main standards in force ?
Regulations governing metal particle detection vary by industry and region. Standards define strict requirements to ensure consumer safety and product compliance.
International food standards
In the food industry, metal contamination is a major cause of product recalls. To address this, several standards and certifications impose rigorous controls.
- HACCP (Hazard Analysis Critical Control Point)
- A risk management system that requires the identification and control of critical points related to physical contaminants. Metal detectors must be positioned at critical control points (CCPs), particularly before packaging. Required by many health authorities (FDA, DGCCRF, etc.).
- IFS (International Featured Standards) & BRC (British Retail Consortium)
- Recognized standards for ensuring the safety of finished products. They require the integration of metal detectors and industrial magnets. BRC, for example, requires that equipment be able to identify metal particles smaller than 1.5 mm in certain types of food.
- ISO 22000
- International standard covering the entire food chain. Includes requirements for physical hazard control (metal detection), is based on HACCP but incorporates traceability and equipment validation requirements.
Pharmaceutical regulations
The presence of metal particles can compromise the purity of medicines and expose patients to serious risks.
- GMP (Good Manufacturing Practices)
- Require systematic checks for metal contamination at all stages. Metal detectors must be calibrated and validated regularly.
- USP <232> and <233> (United States Pharmacopeia)
- Specific standards for the control of elemental impurities, including metals. Sets maximum acceptable thresholds for heavy metals.
Specific standards for the chemical and plastics industries
These industries are subject to regulations designed to prevent contamination and ensure safety.
- ATEX 2014/34/EU (Explosive Atmospheres)
- Applies to areas at risk of explosion (combustible powders). Detection equipment must be ATEX certified to avoid any risk of sparks.
- REACH (Registration, Evaluation, Authorization and Restriction of Chemicals)
- European regulation aimed at limiting the use of hazardous substances. Obligation to prove that processes are free of metal contamination that could alter chemical properties.
Specific examples of the application of metal particle detection standards
- 1. Food industry: compliance with HACCP and BRC Case study: A milk powder production plant in Europe Following the detection of stainless steel microparticles.Problem identified: Wear and tear on grinding equipment.Actions taken: Integration of a high-sensitivity metal detector at the end of the line, addition of a high-intensity magnet before packaging, HACCP validation plan.Results: 98% reduction in contamination, BRC AA level certification.
- 2. Pharmaceutical industry: compliance with GMP and USP <232>Case: Manufacture of pharmaceutical capsulesFollowing the detection of steel residues.Problem identified: Degradation of compression machines.Actions implemented: Installation of high-frequency detectors upstream, periodic validation GMP/USP, full traceability.Results: No further contamination, USP compliance ensured.
- 3. Chemical and plastics industry: compliance with ATEX and REACH standards Case: Manufacture of plastic powders (automotive industry)To prevent defects caused by metal particles.Problem identified: Risk of metal particles affecting quality, site classified as ATEX.Actions implemented: Use of magnetic separators at critical stages, addition of an ATEX-certified online detection system, validation according to REACH.Results: Non-compliance rate < 0.01%, ATEX certification validated.
3. How to comply with metal detection regulations?
Compliance with regulations requires a rigorous approach combining technology, control procedures, and continuous validation.
Integration of metal particle detectors into production lines
One of the main ways to ensure compliance is to integrate high-performance detection equipment at different stages of the process.
1. Choose the right type of detector
Several technologies are available:
- Electromagnetic detectors: Detect ferrous and non-ferrous contaminants via magnetic fields. Ideal for dry powders.
- X-ray detectors: Identify metals as well as glass and dense plastics.
- Magnetic separators: Physically capture ferrous particles upstream.
Example: In the food industry, tunnel detectors are frequently used on conveyors before packaging.
2. Define critical control points (CCPs)
CCPs are stages where detection/elimination must be maximized:
- Upon receipt of raw materials.
- Before and after screening (to detect equipment wear).
- Just before packaging (final check).
Best practices: Use the HACCP method to identify and monitor these points.
Best practices to ensure compliance
1. Calibration and validation of detectors
Metal detectors must be regularly tested and calibrated.
Recommended validation tests:
- Metal ball test: Passing calibrated samples.
- Verification of sensitivity thresholds: Adjustment according to standards.
- Documented checks: Archiving for traceability and audits.
2. Recording and traceability of checks
Documentation is essential.
Elements to include:
- Time stamping of checks.
- Test results and calibrations.
- Corrective actions if detected.
Example: In pharma (GMP), records must be kept for at least 5 years.
3. Training staff in metal contaminant management
Well-trained staff prevent errors and ensure effective monitoring.
Recommended training program:
- Awareness of hazards.
- Control and maintenance procedures.
- What to do if contamination is detected.
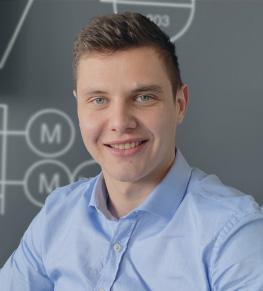
Do you have a project ?
I am available to advise and assist you in your research.
Loïc, expert in powder process safety and contaminant detection
4. What are the penalties for non-compliance ?
Failure to comply with regulations on metal particle detection can have serious consequences for companies, both financially and legally.
Legal and financial consequences
When metal contamination is detected in a product placed on the market, health authorities may require a batch recall, suspension of production, or even criminal penalties.
1. Product recalls and financial loss
- A product recall can cost a company several million dollars due to the destruction of stock and reimbursement of distributors.
- In the event of food contamination, supermarkets and consumers may claim compensation, further increasing the financial impact.
- Example (2022): Recall of >200,000 units of contaminated flour (estimated loss: $4 million).
2. Administrative and criminal penalties
- Health authorities (DGCCRF, FDA, EFSA) may impose fines (non-compliance with HACCP, BRC, ISO 22000).
- Temporary or permanent closure of the factory may be ordered if corrective measures are not implemented quickly.
- If consumers are put at risk, managers may face legal proceedings for negligence or endangering the lives of others.
- Example (2021): Pharmaceutical company fined €1.2 million (unfit medicines).
Impact on reputation and consumer confidence
Metal contamination can seriously damage a company's brand image and lead to a loss of market share.
1. Loss of consumer confidence
- Product recalls are often publicized, which can damage a company's credibility.
- A study found that 70% of consumers avoid a brand after a product recall related to a health hazard.
2. Risk of contract termination with distributors
- Large retail chains impose strict standards and may terminate a contract if a supplier fails to meet food safety requirements.
- Example: Infant nutrition brand loses its main contract (30% drop in revenue).
Solution: Proactive risk management and rigorous quality control are essential to avoid such situations.
5. FAQ: Frequently asked questions about metal particle detection
- How does a metal detector work in a production line?
- It uses an electromagnetic field to detect the presence of metal particles. If the field is disrupted, a signal alerts the operator or activates an ejection system.
- What are the most commonly detected metals in the powder industry?
- Mainly: Stainless steel (equipment wear), Iron (tools, structures), Aluminum (packaging), Heavy metals (accidental contamination of raw materials).
- What are the regulations in force for metal detection in the food industry?
- The main standards are HACCP, BRC & IFS, ISO 22000.
- What is the difference between a metal detector and a magnetic separator?
- A detector identifies and signals/rejects. A magnetic separator physically captures ferrous particles.
- How often should a metal detector be checked and calibrated?
- Recommendation: daily validation tests, complete monthly calibration (according to standards).
- How can false positives be avoided in metal detection?
- Ensure an environment free from electromagnetic interference, adjust the sensitivity according to the product (beware of salts/moisture), and train operators.
- Which sectors other than the food industry are affected by these regulations?
- Pharmaceutical industry (GMP, USP), Chemicals and plastics (REACH, ATEX), Mining and metallurgy.
6. Conclusion: Ensuring safety and compliance through metal detection
Contamination by metal particles represents a major risk for the powder industry. Whether for food, pharmaceutical, or chemical products, compliance with standards and regulations is essential to guarantee consumer safety and avoid heavy penalties.
The integration of suitable metal detectors, combined with well-defined critical control points, can drastically reduce the risk of contamination.
In addition, regular maintenance, operator training, and rigorous documentation are key elements in ensuring compliance with regulatory requirements.
✅ Need to optimize metal detection in your production line? Contact our experts for a customized audit and solutions tailored to your industrial needs.