Processed powders: white refined sugar, surfine caster sugar, crystal sugar
Packing in big bag of white sugar and crystal sugar
Our customer, a leading sugar manufacturer for the Maghreb, wants to increase its big bag packing capacity in order to deliver a larger number of manufacturers using its refined sugar. This big bag filling facility is designed to achieve a minimum throughput of 40 big bags per hour with minimum operator action. To achieve this, the Palamatic Process solution integrates a complete set of big bag handling and the necessary transitics for pallet handling.The entire machine design is conceived and manufactured according to the EHEDG Equipment Hygienic Design Guide.
The processed materials being crystal sugar, refined sugar and surfine granulated sugar of density 0.8 with good flowability, the FlowMatic® 06 big bag packaging station incorporates an intermediate weighing hopper with a capacity of 2 tons allowing dosing in masked time. When the empty big bag is placed by the operator on the filling head, the PLC controls the sugar metering in the weighing hopper. The weighing management is ensured by a Palamatic Process dosing unit specifically developed for big bag filling applications. This dosing unit integrates a very high dosing speed by using a 4-20mA butterfly valve coupled in parallel to a dosing screw managed by a frequency variator. This unique technology ensures that the sugar is dosed in less than 3 seconds with an accuracy of less than 300g.
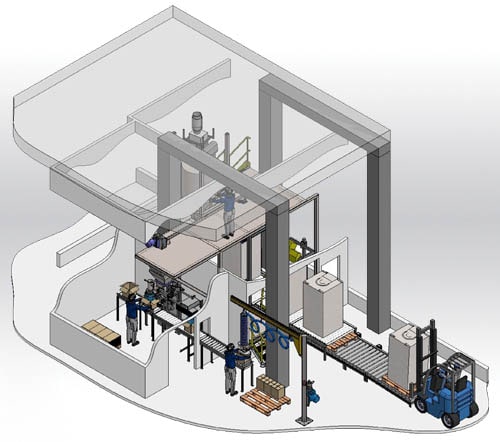
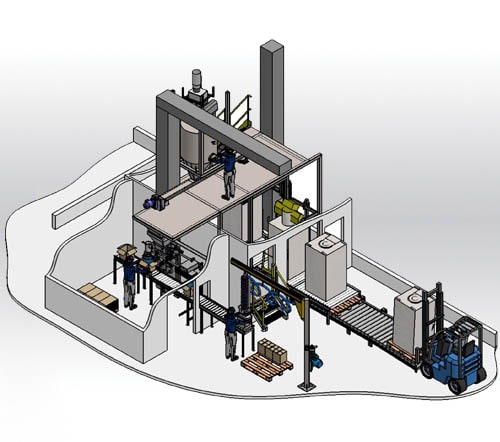
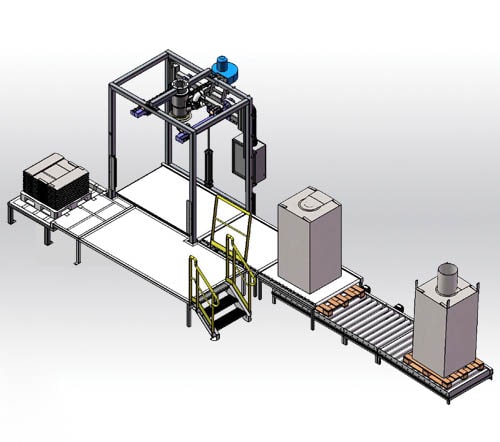
The use of the dosing hopper in masked time allows all manual operations to be carried out without loss of packing flow rate. The operations carried out during the metering in the hopper of the packing machine are: positioning the big bag, connecting the big bag sleeve to the inflatable joint, attaching the loops of the big bag to the automatic hooks, pre-inflation, inflation of the big bag via the fan provided for this purpose and closing the previous big bag by welding the sleeve.
When the sugar dose is metered into the weigher, the drain valve opens to almost instantly fill the empty big bag. A pneumatic tensioning system and pre-inflating of the big bag ensure optimal filling of the inner bag. A dust collection and venting line ensures the containment and balancing of volumes during sugar transfer.
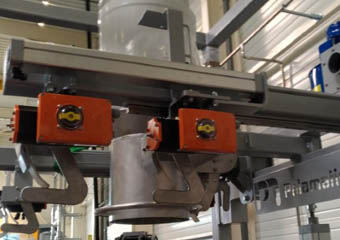
Hooks in position to allow
the big bag to be hung
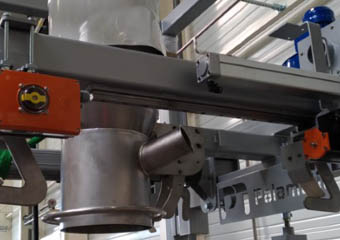
Hooks in position to allow
the big bag to be filled
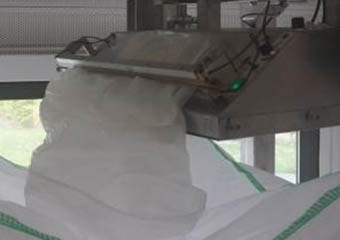
Welding of the big bag cuff
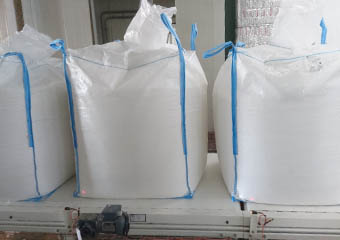
Big bags on roller conveyor
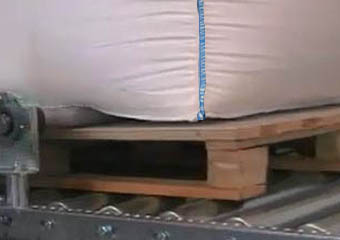
Placing the big bag on the pallet
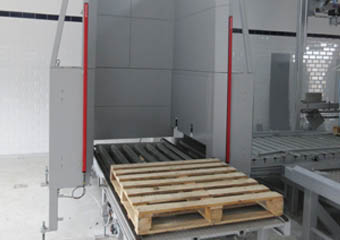
Pallets unstacker
The handling of the filled big bags is ensured by a set of belt conveyors, thus avoiding the use of pallets in the packing area. The big bag is positioned on its pallet outside the packaging area via a double deck conveyor: pallet/big bag. An empty pallet unstacker feeds the big bag "docking" conveyor.
From an ergonomic point of view, the operator works on a single-floor platform with a drop-off area for empty big bag pallets. Similarly, the connection head of the big bag has mobile hooks that move towards the operator to facilitate the installation of the big bag loops. At the end of the packing operation, the big bag is unhooked automatically via the pneumatic tilting hooks.
The weighing chain integrated on the dosing hopper consists of three load cells connected to a commercially certified weighing transmitter. This weighing hopper is certified annually.
In addition, the big bag conveyor incorporates a weighing chain (scale) ensuring additional control of the weight of the big bag for complete traceability of the packing batches.
Features integrated into the big bags packaging line:
- FlowMatic® 06 big bag filling station with conveyor
- Ergonomic hooks for big bag handles
- Pre-inflation fan for big bags
- Inflatable containment seal
- Vibrating table
- Checkweighing system / Conveyor scale
- Weighing buffer hopper of 2 tons
- "Specific" metering system on big bag packing
- Unstacker for empty pallets
- Installation of an access walkway to the filling station
- Automatic sampler
- Big bag cuff welding machine
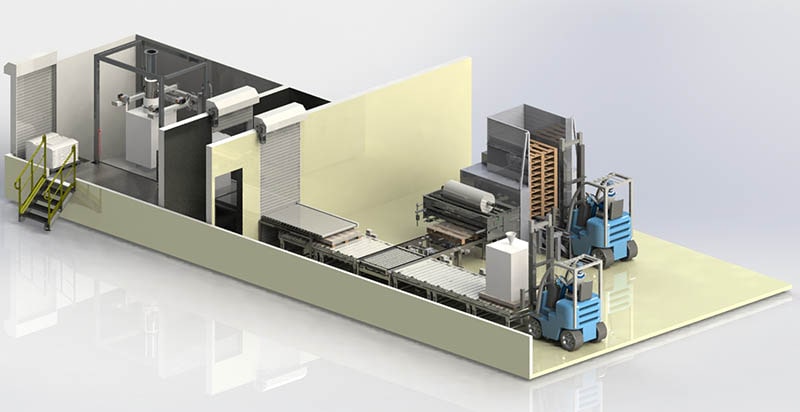
Other possible hygienic big bag packaging installation: packaging line with laying down of mats
and placing of the big bag on its pallet