Processed powders: gluten and starch
Handling of food starch
French company specialized in the conditioning of bulk products and raw materials.
Palamatic Process has developed a high speed big bag packing line with maximum hygiene. The purpose of the process is to condition the bulk material, which is fed from the truck to the buffer hopper, in big bags.
The raw material, with a grain size density of 500 kg/m³, is collected in a receiving cyclofilter which consists of a 304 L stainless steel buffer hopper with a storage capacity of 3,000 liters, a 20 m² dust collection filter and an indoor explosion vent.
Preparing big bags
A pallet unstacker feeds the big bags filling station automatically and without operator intervention. It can hold between 15 and 20 empty pallets and has a throughput of 250 pallets per hour. The pallets are simply loaded with a forklift truck by a forklift operator.
The pallet unstacker is designed for installation on motorized roller conveyors to automatically dispense pallets to the big bags filling station located in a clean room.
Once the pallet is in position, the operator installs the big bag on the automatic rotary hooks positioned on the upper part of the structure and which are entirely controlled by the PLC.
A big bag filling platform with a tilting railing provides easy access to the upper part of the big bag filling machine for hanging the handles and closing the big bag filling chute. This platform ensures ergonomic access to the big bag for the operator.
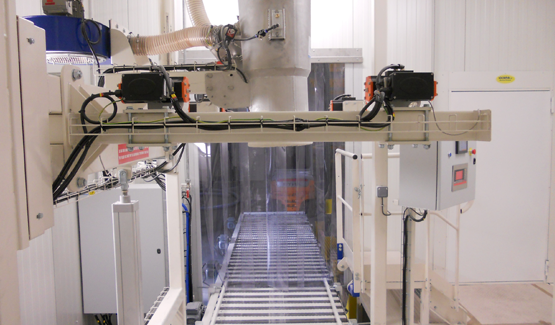

Metering and filling of the big bags
The bulk material is introduced into the receiving cyclofilter by means of a blower. The bulk material is then cycloned for air/product separation. The high efficiency filter, integrated into the conveying cyclone, ensures the final separation of the air. A compressed air cleaning system is used to clean the filter at each pneumatic conveying session. Vibrating fluidizers are positioned on the buffer hopper to prevent the materail from bridging and optimize its flow.
The material passes through a 30 m³ per hour rotary airlock valve with ATEX 22 motorization for controlled dosing and an ATEX 20/22 GSC 900 vibrating screen. The vibrating screener protects the machines that compose the packing process by eliminating potential agglomerates and potential foreign bodies. The vibrating screen is thus the guarantee of total hygiene.
A flexible connector isolates the big bag filling station from the vibrations of the vibratory screen. Its design allows it to be installed and uninstalled without tools and in a few seconds. The set consists of two stainless steel connectors and a flexible polyester (food grade) hose connection.
To stop metal particles, a double-stage magnetic grid separator is mounted under the sealed connection system. It is cleaned by opening the drawer.The bulk material then flows into the FlowMatic® 02 big bag filling station, which consists of a double-walled filling tube, a connecting inflatable seal, a tension cylinder, a height-adjustable structure to suit different big bag sizes and load cells to ensure commercial weighing.
The pneumatic tensioning cylinder is operated by the control cabinet. It controls the hanging height and deposits the big bag on the pallet as it is filled thanks to the compression of the cylinder air. This principle ensures optimal filling and excellent stability of the big bag on its pallet.
A vibrating table with airbags is mounted on the roller conveyor. This vibrating table is retractable so as not to make the roller conveyor vibrate. The objective is to optimize the holding of the big bag on its pallet and to obtain a homogeneous filling of the big bag.
Removal of the big bag
Once the big bag is filled, the inflatable seal deflates, the loops are automatically removed and the big bag is removed with its pallet by means of the motorized roller conveyor. The storage conveyor for filled big bags has a capacity of 4 units.