1. Principle of operation
As its name suggests, the centrifugal sifter (also called a rotary sieve) works on the principle of centrifugal forces to screen powders and granular materials.
Typically, there is one inlet and two outlets, one for undersize or in spec powders and the other for oversized particles or foreign contaminants. The inlet and outlets are off center, compared to vibratory sieves that typically have the main inlet and outlet in line with each other. When material is fed into the inlet of the powder sifter, a small auger pushes the bulk powders into the cylindrically shaped sieving chamber.
Rapidly rotating paddles attached to the central drive shaft cause the powders to tumble around inside the screen basket. The screen is supported by a cage that can be removed for maintenance and replacement of the screen. As the paddles rotate, the powder particles are thrown against the screen. Any particles that are smaller than the mesh aperture escape through the screen, funneled through the discharge hopper and out to the downstream process. Anything that is oversized is carried along the length of the screen until it exits out the overs or reject outlet. There are different types of designs of centrifugal screeners. Some are cantilevered where two bearings are located on the motor side of the industrial screener. Others have a bearing at either end to support the drive shaft. In both arrangements, the overs end of the machine has an adjustable gap that allows the rejects to fall through more easily, or retained on the screen for longer to increase the powder screening efficiency. Drive assemblies can also vary from gear box style, belt or direct drive. Air purge seals are often utilized on the bearings to prevent the powder from entering the bearing housing. Rotary sifters are limited to one screen at a time; therefore, they can only perform one function at a time, e.g., safety screening, scalping oversized particles or de-dusting fines.
2. Types of screening applications
Safety Screening – One of the most common screening applications for centrifugal sieves is safety screening. Take a tour through any production plant processing dry materials and you will almost always find some type of screening equipment. Whether we are looking at a process for the food, chemical or minerals industry, the need to provide some type of safety barriers between the input of a process and the rest of the downstream production equipment is essential. Raw inputs can often carry unseen hazardous objects such as rocks and other types of tramp material. If these contaminants get into your process, and for example come across a high-speed impact mill, the result can be catastrophic. Safety screeners often use a very coarse mesh where 100% of the good powder can easily pass through the screen, but anything larger that should not be in the process can be caught and ejected safely.
Scalping – Scalping refers to taking up to 5% of the top end of the particle size distribution curve out of the process. This is probably the second most common screening application within bulk material production processes. Manufacturers, for a variety of reasons, may want to keep a tight control over the top end of a particle distribution curve.
For example, a producer of powder for beverage mixes wants to be sure that their product is completely water soluble. They may find that their powder mill cannot get 100% of their product within an acceptable distribution range and need to use a screener to skim 1-5% of the top end of the curve. Once the powder passes through the sieve, the oversized particles will be recycled back to the mill for a second pass.
Classifying – Powder classification often deals with multiple cuts of powder separation via the use of several screens. Flat deck screeners are typically used for this type of application.
A good example here is agricultural fertilizers like lime powders. A flat deck screener can use multiple decks with several screen sizes to create different grades of the same product. Note that because centrifugal sifters can only use one screen at a time, they typically are not found in applications involving multi-grade classification. However, it is possible to use centrifugal sifters in tandem to create different grades of material.
De-dusting – With very careful consideration and design, it is possible for a centrifugal sifter to serve the sole purpose of taking powders that are too fine out of the production stream. In this instance, all the good material gets immediately conveyed down the length of the screen and out the overs / rejects end into the rest of the downstream process. The sifter would use a screen that is undersize to knock out the fine dust from the material distribution curve.
One common example is agricultural feed where pellets are the desired outcome. Too many fines can slow down the intake of an animal feeding (think beef cows trying to chew on a powder). But again, it is more common to see flat deck screeners in de-dusting applications then it is with centrifugal sifters.
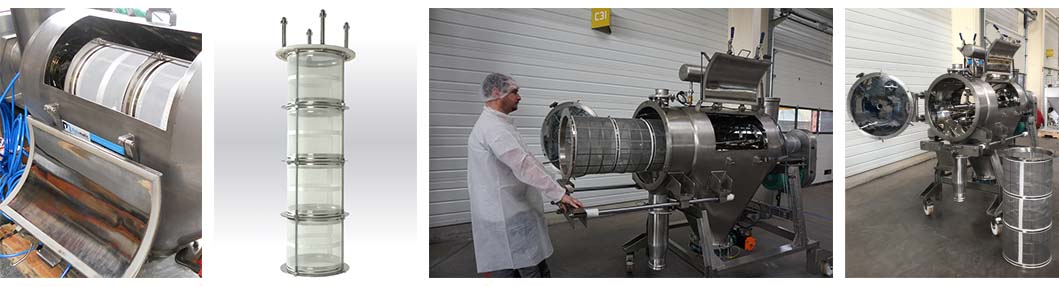
3. Deagglomeration capabilities
The main screening mechanism are rotary paddles that spin to create a centrifugal force that throws powder against the surrounding screen basket. Typically, the paddles spin at a rate of 600 – 800 RPM, depending on the make and size of the rotary sifter. This spinning action can actually create a low impact force on the particles to be screened. Therefore, it is very possible to use a rotary sieve to help break up soft agglomerates that typically could be easily teased apart between your fingers.
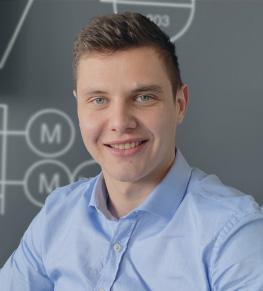
You have a screening project?
I am available to discuss.
Loïc, powder expert
A good example would be granulated sugar that has been held in dry storage for an extended period. Often times in this scenario, sugar can form compression lumps that are usually very friable and easily broken up. In this instance, a centrifugal sifter can serve two purposes in one (screening and lump breaking). Flat deck screeners (or vibratory screeners) are not able to do this task since the powder just mainly rolls or bounces across a flat mesh surface. Please take note however, if your powder agglomerates require the impact of a hammer to break apart, then a centrifugal sifter cannot provide enough force to break up these kinds of harder clumps of powder (typically related to moisture exposure).
4. Gravity vs. inline pressure screening
Centrifugal sifters can be designed for both gravity feed and pressure feed applications.
In gravity feed applications, the centrifugal is much more diverse in the applications it can serve (i.e., safety, scalping, classifying and de-dusting). However, in pressure conveying lines their use is limited to only safety screening. Because of the use of pressure, the screen must be coarse enough to allow powder particles to easily pass through the mesh aperture. If one attempts to use a rotary sifter for say, a scalping application in a pneumatic conveying line, the pressure would cause the near size particles to blind the screen mesh sending good powder out the rejects end.
It is important to inform your equipment supplier that the powder sifter will be used in a pneumatic conveying or gravity feed line. The design of the dry material screener will be different in both applications and must be designed and fabricated appropriately. It is also important to note that centrifugal sieves for use in pneumatic conveying lines can only be used in dilute phase applications and never in dense phase. That is because an inline sifter has its limitations on how much pressure it can withstand. Dilute phase uses high pressure and low velocity to convey material along its line. A sifter is limited to 12 psi of pressure, anymore and the seals will fail and create a dusty mess within your operating area.
5. Other modifications and types of screens
Most equipment suppliers can make a myriad of modifications and adjustments to rotary type screening equipment. Any industry can make use of this type of industrial screening equipment; however, the design elements can change based on the industry in need. A centrifugal screener going into an application for screening titanium dioxide (TiO2) will be a completely different design from one going into a pharmaceutical process for active pharmaceutical ingredients (APIs).
These modifications may include different types of steel for fabrication (mild vs. 316 stainless), different grit finishes (standard bead blast vs. mirror polish) and different weld radiuses for better cleanability. The rotary paddles can include adjustable wiper blades to set the gap tolerance between the screen mesh and the paddles for increasing the efficiency of the centrifugal effect.
Furthermore, different screen types can also be used. The most common one is nylon, which if it can be used, should be. Nylon mesh is flexible and can actually create an anti-blinding effect thanks to the same centrifugal forces responsible for screening the powders. Other types of screens are woven wire, wedge wire and perforated plates. They all offer pros and cons, wedge wire offers the most open area % while perforated plate is the most durable (in coarser specs) but the least open area %. Metal screens such as woven and wedge are not flexible, so they are not anti-blinding, but if made from 430 ferritic stainless steel can be caught my safety magnets below the screener in case of screen failure. This is not possible with nylon screens.
As can be seen, centrifugal sifters are quite simple and straightforward machines. However, they do offer a range of features and modifications that will best suit almost any powder sieving application. Our team at Palamatic Process has 30 years of bulk material handling and powder processing experience. Contact one of our sales reps today to discuss your industrial screening application!