All bulk material manufacturing processes require equipment that can add value to your raw material inputs. If powder processing equipment such as pin mills, lump breakers, classifiers, mixers and extruders are the engines of your manufacturing process, then material conveying and feeding systems certainly are the infrastructure that ties everything together. However, there is often confusion between the terms screw conveyor, screw feeder, vibrating conveyor and vibrating feeder. For the purpose of this article, we are going to focus on the two main types of feeders: screw feeders and vibrating feeders. We will also define exactly what is powder feeding equipment and how to choose the best type of equipment based on your materials.
1. Defining Feed Equipment
First let’s define what feed equipment is not. Material feeding equipment, also called powder dosing equipment, is not a conveying system. Mechanical conveyors, such as screw conveyors (also called auger conveyors) and vibratory conveyors, typically consist of one inlet and an outlet purely for the purpose of moving material from point A to point B over longer distances. They usually run at a fixed rate and move material downline at a constant throughput measured in pounds or kilograms per hour.
In contrast, feeding equipment is used in situations where more control and precision of the material flow rate is required. Also, screw feeders and vibratory feeders are not for moving material over longer distances, rather they are used to dose material from a hopper or IBC tote into a packaging line, or possibly a powder mill. They are much smaller than mechanical conveyors consisting of an integrated hopper, agitator, small tube or flat bed and a variable frequency drive. The integrated hopper is necessary for feeding equipment because a constant head load must be maintained for proper operation. The speed can be controlled on feeding equipment via a VFD, to allow slower and faster feed rates.
If your process requires repacking the processed material into 25 – 50 lbs. paper bags, and you need to be certain you’re not over or under packing the container, feeding equipment is the way to go. Similarly, powder mills cannot run on a head load or be slug fed, they perform at their best while running under a steady and consistent feed rate.
2. Considering your Material Characteristics
Powders and granular materials can have several different properties that will greatly affect how they behave in a material manufacturing process. Consider the following common traits often found in dry bulk materials:
- Hygroscopic: Sugar, salt and certain types of chemical powders can readily and easily absorb moisture and humidity from their surrounding atmosphere. This can cause the material to clump and harden during extended periods of storage and rest.
- Aeratable: Glass beads, flour and resins often have a low angle of repose and behave much like a fluid when aerated. This material can easily flood (uncontrollable flow) downstream processes if not kept in check.
- Fibrous: Wood flour or biomass fibers and the like contain long particles that interlock and form masses that can block up flow channels.
- Adhesive: Materials such as pigment powders can stick and cling to every surface imaginable, which can make this type very challenging to handle.
- Friable: Pasta, flaked or some granular products can be easily broken (known as attrition) if handled too roughly. Therefore, equipment that is capable of gently handling and transferring the material is necessary to preserve the integrity of the product.
- Free-flowing: Plastic pellets flow easily by gravity with little to no help from flow aids or specially designed equipment.
- Abrasive: Glass powders, Portland cement, etc. can have properties that wear down equipment components quickly if your process is not designed with this characteristic in mind. This can lead to frequent and costly maintenance.
Understanding how your material will behave and what to prevent is an important step in choosing the right kind of feeding equipment.
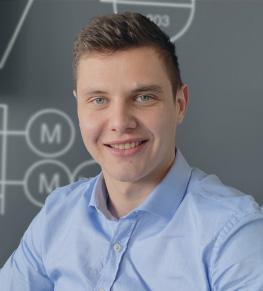
You are not sure which type of dosing device to
choose? I am available to discuss and advise you.
Loïc, powder expert
3. Performance and Design Differences
So now that we understand how feeders are used and various material characteristic categories, let’s put both of those components together and define what feed equipment will work best. Screw Feeders use a built-in hopper with stirring agitator that flood feeds a tubular channel. Within the tube is a small screw that pushes the product through an outlet into the downstream process. There are several designs for the small auger within screw feeders such as: pigtail screws, ribbon screws, and screws with a drive shaft.
- Pigtail screws have no central shaft and are often used for materials that have the following characteristics: light density and/or are sticky or cohesive. Examples include: flour, cocoa powder, and oxides.
- Ribbon screws have a central shaft but the flights are open and connected at one point to the shaft. Ribbon screws are used on materials that are light and granular such as PVC and polymer pellets.
- Screws with central shafts are used for denser or fluid materials like metal powders, for example.
Screw feeders offer a good deal of precision, in some instances dosing at an accuracy of -/+ 1-2 grams. They are a common type of feeder as they fit most applications, except in instances of materials that are friable or heat sensitive.
Vibrating feeders have a similar build (hopper and tubular structure unit) but instead of a screw, shaker motors are attached to the unit and the structure is supported by spring coils, to allow the unit to vibrate. A very minimal angle will allow the unit to shuffle the material down the feed bed into the downstream process. The feed rate can be controlled by increasing or decreasing the vibration amplitude and frequency. The shuffling action helps preserve the integrity of the materials, or avoid unnecessary wear and tear in the case of abrasive materials. Therefore, whenever dealing with materials that are either friable, temperature sensitive or abrasive, vibrating feeders are the way to go.
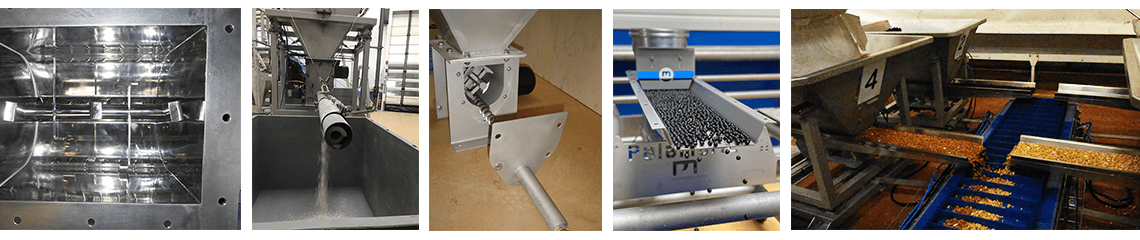
4. Pros & cons of screw feeders and vibratory feeders
Screw feeder
Main advantages of a screw feeder:
- The screw types can vary and easily be swapped out to meet a wide variety of material types.
- The screw provides a positive extraction (pulling) from the hopper.
- Can be designed for easy to clean applications, without having to remove the whole unit from the line.
Main disadvantages of a screw feeder:
- Adhesive materials and fines can build up inside the material, restricting flow
- Moving parts can cause additional wear on the equipment, resulting in more maintenance needs.
- Consumers more power than vibrating feeders.
Vibratory feeder
Main advantages of a vibrating feeder:
- Handles low and high feed rates
- Produces a uniform material flow that provides gentle handling
- Virtually no moving parts, minimizing maintenance needs
- Low power consumption
Main disadvantages of a vibrating feeder:
- Vibrating action can generate some dust with certain fine powders
- Vibration can possibly segregate materials that have been mixed
- Will not provide a positive extraction (a means of pulling material from the hopper)
- Adhesive or fine materials can build up on the feed tray, restricting flow.
Palamatic Process has 30 years of bulk material handling and powder processing expertise. If you are looking for help with powder feeding and material dosing equipment, please contact our team of sales engineers for guidance in finding the best solution for your process.