Incorporation of sugar and salt in liquid egg tanks
The PowderEgg®01 process for incorporating salt and/or sugar into liquid egg tanks is specially designed for the egg product food industry. The whole equipment is designed with the hygiene rules necessary for the egg industry.
- Hygiene and cleanability
- Reduced retention area
- Stainless steel design
- Precise dosing
- Controlled incorporation
- High loading rate
Incorporation of additives for standardization of egg yolk, egg white and whole egg
The integration of additives may be necessary to ensure that high quality finished products are consistently replicated and produced. The dosing and transfer line allows the incorporation of additives such as salt, sugar, maltodextrin, xanthan, etc. The operation process in yolks, whites or whole eggs provides standardization of your product.
The PowderEgg®01 line allows for the direct addition into the storage tank through the top of the tank or a liquid incorporator. The feeding of additives can be ensured by several powder handling equipment technologies, depending on your egg line: weighing, refractometer, densimeter, etc.
The number of additive feed stations can be adjusted according to your production needs and recipes. Therefore, Palamatic Process can offer your customers ever more technological and easy-to-use products with a foaming, gelling, emulsifying, thermostable capacity, etc.
Thanks to the modularity of the PowderEgg®01 line and its ability to change additives, your production process can quickly and easily adapt to changing demands for various applications involving powdered eggs (egg products) in industries such as: pastry, bakery, sauces (mayonnaise), butchery, fishing and more!
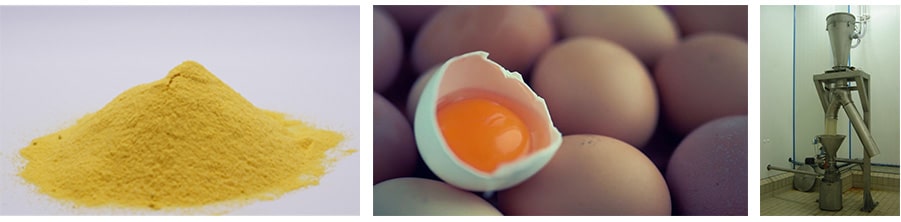
Also discover the PowderEgg®02 line
Hygiene
The demanding constraints and sanitation requirements of the egg products industry are fully integrated into the design of this dedicated Palamatic line. For example, the equipment’s product retention areas are reduced to a minimum, designed entirely in stainless steel and optimized for easy cleaning.
Clean-In-Place (CIP) solutions are possible as an option (spray water, foam gun, etc.) and must be defined according to the area where the equipment is located (dry area versus wet area).
To provide a high-quality product, rare earth magnets are also integrated on the additive incorporation line.
Transfer technology
The material transfer technology used to supply the storage tanks with additives is pneumatic conveying based on vacuum technology. This hygienic transfer technology ensures a precise and confined transfer of all your products. The flow rate can be adjusted according to your production needs and additive to be introduced.
From a few kilos to several tons/hour, the Duopal combined sack and bulk bag unloading station offers the flexibility your process needs to change products and packaging formats.
Palamatic Process' experience in egg food factories provides optimal result for your production. Palamatic Process lines can meet your needs for the incorporation of additives and the packaging of egg powder at the outlet of the drying tower, regardless of the fluidity of the powder or the processing of egg shell waste.
Discover other customer installations that used the PowderEgg®01 line for the incorporation of sugar and salt in liquid egg vats.
All the equipment integrated in the egg yolk and white powdering process line are available below.