Description
Drum discharging system - DrumFlow® 04
With a fully confined way of discharging your drum, the DrumFlow® 04 is the equipment you need to handle your hazardous and/or toxic products.
Thanks to the double inflatable seal technology to keep the dust enclosed, the DrumFlow® 04 will avoid contamination of your work environment.
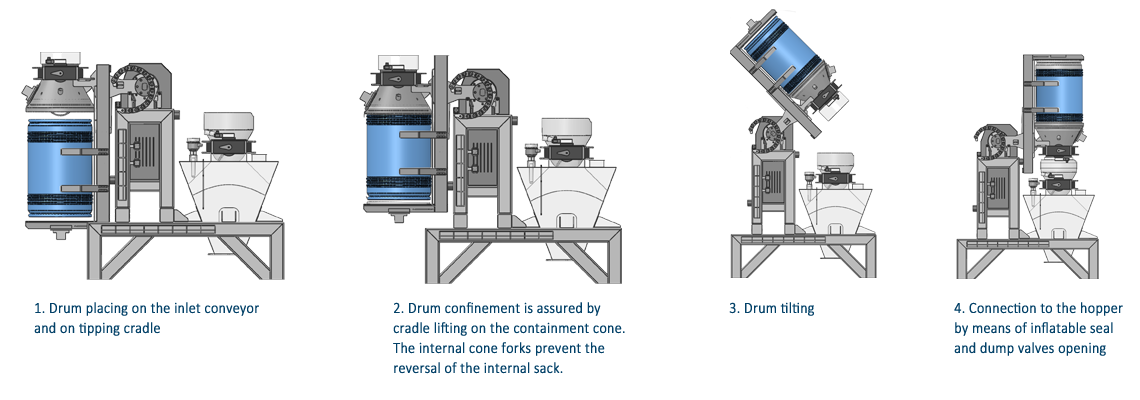
A mechanized roller conveyor transports the drums towards the unloading station. Positioning stops are provided. Once the drum is positioned, the operator can start the tilting cycle.
The capping cycle consists of mounting the drum to the stop on the capping cone. The drum is then pinched between the tray and the styling cone. Bars attached to the cone penetrate the drum to prevent the liner from turning over during tilting.
Then, the tilting cycle is to rotate the whole barrel + styling cone with drain piping. This tilting is provided by the second cylinder. The mobile assembly comes into contact with the rubber studs provided for this purpose.
The end of the drain piping is vertical at the end of tilting and it enters a socket joint, located on the powder inlet of the hopper. Once drained, the mobile assembly returns to its initial position by performing the 2 reverse tilting and stripping movements. A push cylinder allows the drum to be transferred to the motorized conveyor.
The entire drum tipper can be installed inside a safety enclosure, preventing any cycle start as long as the door of the enclosure remains open. This cabin, equipped with an access door, also optimizes the containment of the emptying station. It is also possible to install a glove box to allow the opening of the drums without entering the cabin.
-
Rate1
-
Containment5
Equipment advantages
- Total containment
- No drum handling
- Applications CMR toxic product
Media
View our equipment in videos
Drum tipping - DrumFlow®04
View our equipment in photos
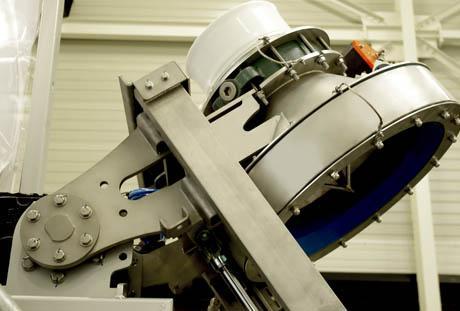
Dumping of bulk materials from drums
Drum tipper with capping head for containment.
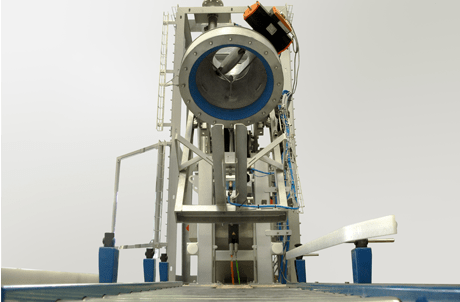
Drumflow 04 - Tipping over & sealed capping
Emptying by tilting and capping the drum.
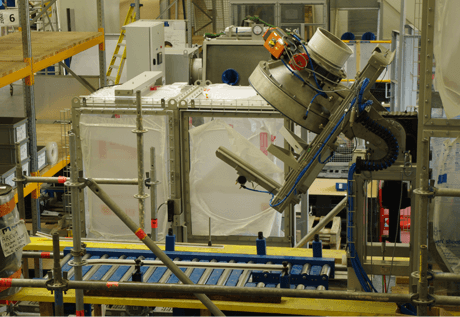
Powder drum discharging
The capping of the drum is done by raising the frame on the containment cone.
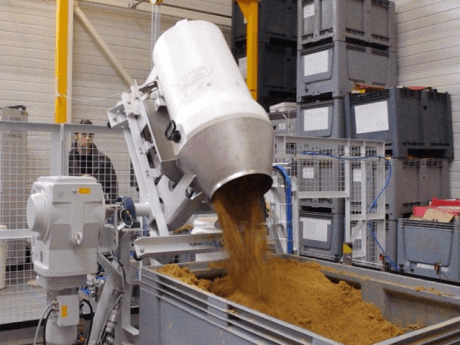
Automated drum tipping
Automated drum turner on a carbonate packaging line.
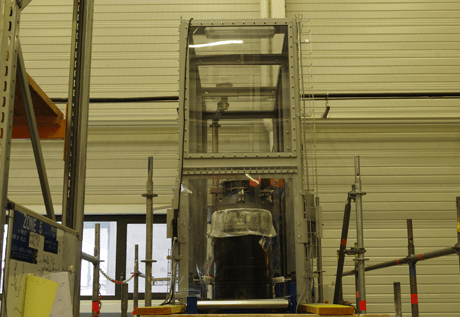
Drum discharging - Drumflow 04
The containment chamber of the drum tipper is the guarantee of a healthy working atmosphere.
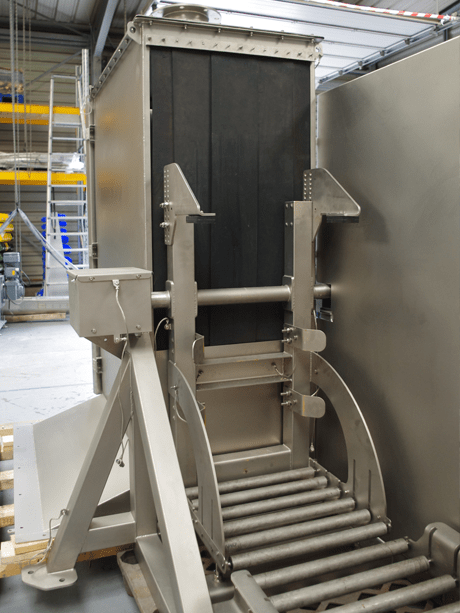
Drumflow 03 - Tipping over
Drum tipper with cabin for containment during the unloading operation
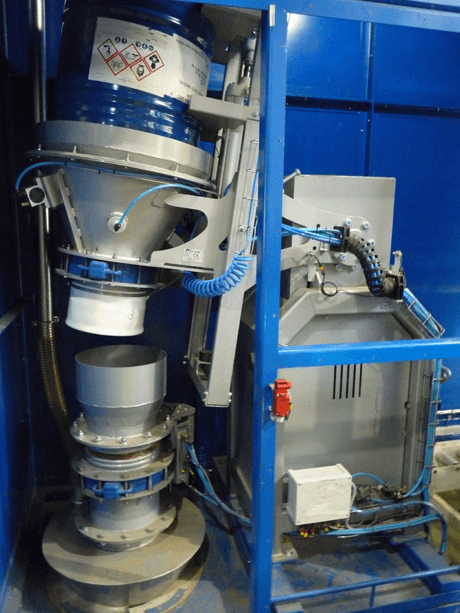
Drum discharging system
Capping and tilting for contained connection and discharging
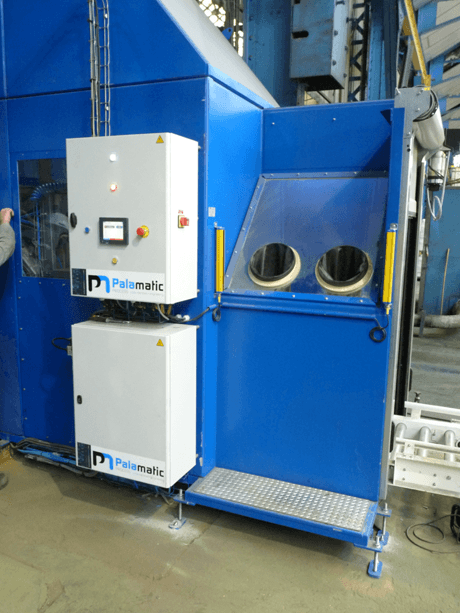
Contained drum emptying
Glove box for drum discharging station to protect the operator from possible toxic powders.
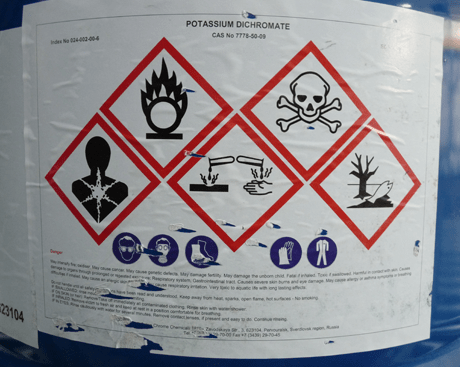
ATEX Drum discharging
The tight capping of the DrumFlow® 04 drum emptying system ensures a safe and healthy installation.
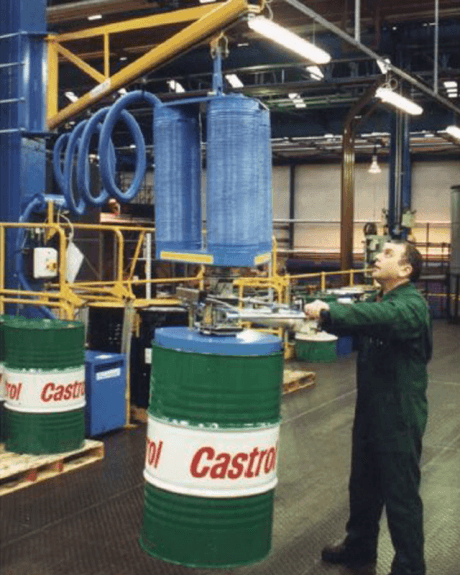
Drum manipulator
The drum manipulator is used to move drums and barrels safely without any effort on the part of the operator.
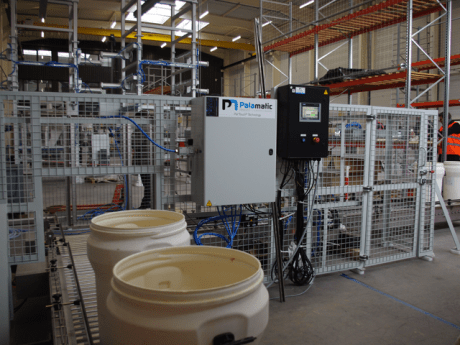
Drum conveyor
Automated deconditioning line for animal flour stored in drums.
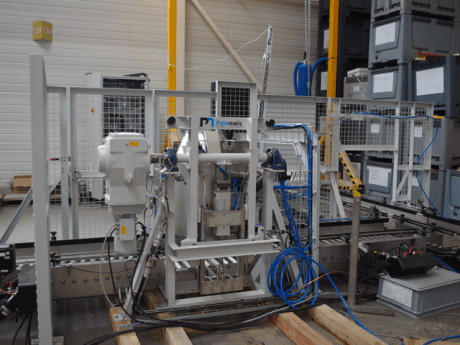
Industrial drum tipper
The maximum loading capacity of the drum tipper is 250 kg.
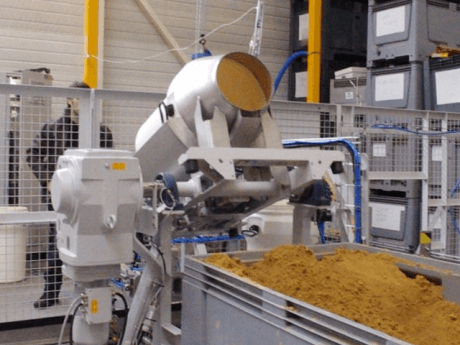
Drum discharging
Our handling systems make it easy to lift drums, turn drums over and empty drums.
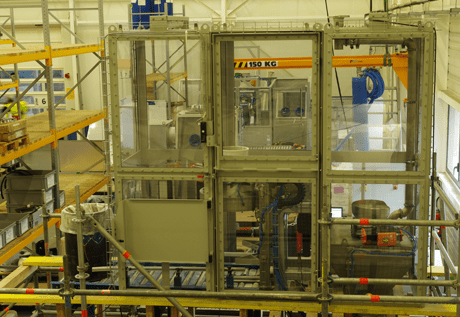
Automatic drum discharging
The containment of the drum emptying station ensures a healthy working atmosphere.
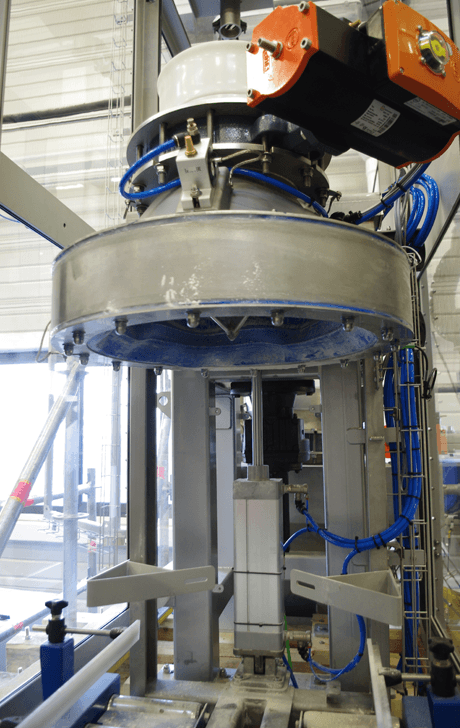
Tipping head barrel
The operator can completely or partially empty the contents of the drums into the hoppers, reactors or manholes of industrial mixers.
Features
Technical specification
Examples of results obtained:
Rate | 1 drum / 4-5 min |
---|---|
Capacity | 250 kg/ drum |
Manufacturing materials | Painted steel/stainless steel structure |
Inclination | Up to 180° |
Tilting of the drum | Electric motor 7,5 kW |
Drum capping | Pneumatic cylinder with overpressure leak test |
Connection to the drain | By low pressure inflatable seal |
Butterfly drain valve | DN150 |
Flow aid | Fluidizer on drain cone, vibrator on cone and drum bottom |
Typical operating mode :
Step 1: Installation of the drum on the infeed conveyor and on the tipping chair
Step 2: Drum capping by mounting the chair on the containment cone. The internal forks of the cone prevent the reversal of the bag.
Step 3: Tilting of the drum
Step 4: Connection to the hopper with an inflatable seal and open the drain valves.
Example of installation
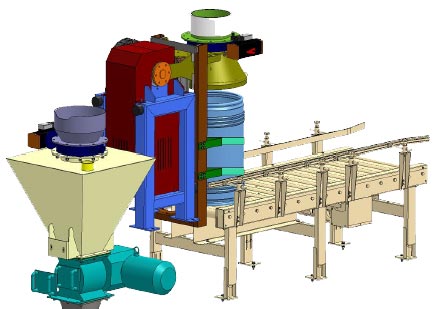
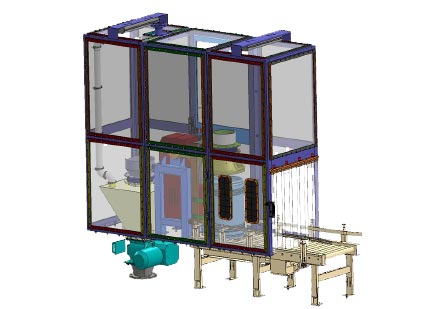
Case studies
CASE STUDIES WITH THIS EQUIPMENT
Bag and drum handling
Processed powder: Potassium Bi-Fluoride - Drum and bag handling in the nuclear sector: 25kg kraft paper bags with an inner liner and 90kg drums with an inner liner.Energy
Contained discharge of chemical powder
Processed powder: sodium methylate - Contained discharge of chemical powder - The process consists in safely unloading drums containing sodium methylate in a Class 1 / Division 2 hazardous environment...Chemical
Automatisation sécurisée de la vidange de fûts de perchlorate d’ammonium dans l’aérospatial avec le DrumBot 300
Treated powders: ammonium perchlorate Secure automation of the emptying of drums of ammonium perchlorate in the aerospace industry with the DrumBot 300Defense