Overstappen naar flexibele productie: IBC-containers voor efficiënte poederverwerking
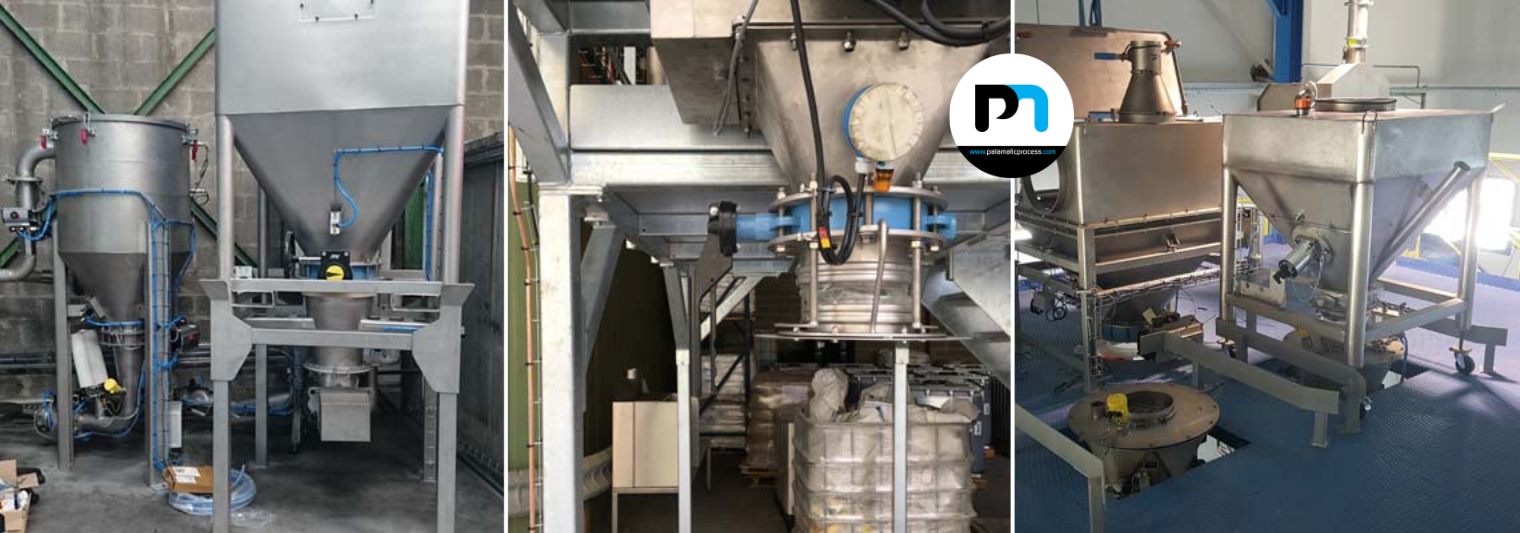
- 1. Waarom een overstap naar IBC-containers overwegen ?
- 2. Inleidende vragen voor een succesvolle overgang
- 3. Dimensionering van apparatuur en integratie van IBC-containers
- 4. Beperkingen en oplossingen voor het legen van IBC-containers
- 5. FAQ : Antwoorden op veelgestelde vragen over de overgang naar IBC-containers
- 6. Conclusie
De voedingsmiddelen-, farmaceutische en cosmetische industrie bewegen zich in de richting van schonere, geautomatiseerde productieoplossingen.
Het beheer van poeders in grote zakken brengt een aantal beperkingen met zich mee: repetitieve handelingen, stofemissies en kruisbesmetting. Volledige IBC-oplossingen bieden een betrouwbaar en flexibel alternatief.
Ze garanderen vereenvoudigde verwerking, verbeterde traceerbaarheid en eenvoudige integratie in geautomatiseerde processen.
Maar hoe maakt u de overstap? Met welke criteria moet u rekening houden?
Hoe dimensioneer je de apparatuur en optimaliseer je het legen van IBC-containers? Dit artikel beschrijft de essentiële stappen voor een efficiëntere en hygiënischere productie.
1. Waarom een overstap naar IBC-containers overwegen ?
1.1. Beperkingen van traditionele methoden
Hoewel traditionele poederverwerkingsmethoden nog steeds veel gebruikt worden, hebben ze grote nadelen die de productiviteit en kwaliteit van industriële activiteiten beïnvloeden.
Zware hantering en ergonomische risico's: Het hanteren van grote zakken vereist het gebruik van specifieke apparatuur zoals takels of vorkheftrucks. Deze handelingen vormen niet alleen een zware fysieke belasting voor de operators, maar brengen ook een aanzienlijk risico op arbeidsongevallen met zich mee. Repetitieve bewegingen en onhandige houdingen kunnen leiden tot aandoeningen aan het bewegingsapparaat, de belangrijkste oorzaak van beroepsziekten in de industrie.
Langere omsteltijden voor batches: Het wisselen van de ene productiebatch naar de andere met traditionele systemen brengt veel handelingen met zich mee: het verwijderen van lege zakken of big bags, het reinigen van apparatuur en het plaatsen van nieuwe containers. Deze handelingen kunnen tot 20% van de totale productietijd in beslag nemen, waardoor de productiviteit van de lijn aanzienlijk daalt.
Kruisbesmetting en hygiëneproblemen: Open systemen werken stofemissies en het risico op besmetting tussen verschillende producten in de hand. In gevoelige sectoren zoals de farmaceutische industrie en de voedingsindustrie kunnen deze problemen ernstige gevolgen hebben voor de kwaliteit van het eindproduct en de veiligheid van de consument.
Milieu-impact: Het gebruik van zakken en, in mindere mate, big bags genereert een aanzienlijke hoeveelheid afval. Papieren of plastic zakken zijn over het algemeen voor eenmalig gebruik, wat indruist tegen de doelstellingen van duurzame ontwikkeling die steeds meer bedrijven zich stellen.
Beperkte traceerbaarheid: Traditionele systemen bieden beperkte producttraceerbaarheid door de hele productieketen heen. Handmatige batchidentificatie en meervoudige productoverdracht vergroten het risico op fouten bij het traceren van grondstoffen en eindproducten.
1.2. Voordelen van IBC's
IBC's vormen een modern, efficiënt alternatief dat de beperkingen van traditionele methoden direct aanpakt en tegelijkertijd extra voordelen biedt.
Luchtdicht en hygiënisch: Het gesloten ontwerp van IBC's voorkomt het vrijkomen van stof en beschermt het product tegen verontreiniging van buitenaf. De roestvrijstalen modellen hebben gladde oppervlakken die gemakkelijk te reinigen en te desinfecteren zijn en voldoen aan de strengste hygiënenormen in de farmaceutische en voedingsmiddelenindustrie.
Gemakkelijke hantering en ergonomie: IBC-containers zijn ontworpen om gemakkelijk verplaatst te worden met palletwagens of geautomatiseerde systemen en verminderen de fysieke inspanning van operators aanzienlijk. Door hun gestandaardiseerde vorm en geoptimaliseerde afmetingen zijn ze gemakkelijk op te slaan en te hanteren, waardoor de werkomstandigheden en de veiligheid verbeteren.
Integratie in geautomatiseerde lijnen: IBC-containers zijn perfect geschikt voorautomatisering. Ze kunnen worden uitgerust met identificatiesystemen (RFID, barcodes) voor real-time tracering. Deze compatibiliteit metIndustrie 4.0-technologieën opent nieuwe mogelijkheden op het gebied van productiebeheer en optimalisatie van stromen.
Gecontroleerde, veilige lediging: Met specifieke ledigingssystemen, zoals deIBCFlow®02, kunnen poeders op een gecontroleerde manier worden geledigd, waardoor emissies worden beperkt en een volledige overdracht van het product wordt gegarandeerd. Geavanceerde technologieën zoals vlinderkleppen of dubbele klepsystemen zorgen voor een perfecte afdichting tijdens alle verwerkingsfasen.
Minder stilstand: Het gebruik van IBC's optimaliseert het wisselen van batches en vermindert de reinigingstijd. Een lege container kan onmiddellijk worden vervangen door een volle, waardoor de continuïteit van de productie wordt gewaarborgd. Deze operationele flexibiliteit vertaalt zich in een aanzienlijke verhoging van de bezettingsgraad van de apparatuur.
Duurzaamheid en rendement op investering: IBC's van roestvast staal zijn duurzaam en kunnen tientallen jaren worden gebruikt met minimaal onderhoud. Hoewel de initiële investering hoger is dan bij big bag-oplossingen, betaalt dezezich snel terug door besparingen op verbruiksartikelen en een verbeterde productiviteit.
Optimale traceerbaarheid: Elke container kan individueel worden geïdentificeerd, waardoor de batch tijdens het hele productieproces nauwkeurig kan worden gevolgd. Deze verbeterde traceerbaarheid maakt het eenvoudiger om productterugroepingen te beheren en te voldoen aan de steeds strengere wettelijke vereisten.
2. Inleidende vragen voor een succesvolle overgang
2.1. Aard van de verwerkte producten
Een succesvolle overgang naar het gebruik van IBC's hangt in grote mate af van een grondige analyse van de kenmerken van de verwerkte poeders. Deze eigenschappen bepalen niet alleen welk type container de voorkeur verdient, maar ook welke hulpapparatuur nodig is voor een optimaal beheer.
Deeltjesgrootte en -distributie: Deeltjesgrootte heeft een directe invloed op het stromingsgedrag van poeders. Producten met een fijne deeltjesgrootte (minder dan 100 micron) zijn over het algemeen meer cohesief en kunnen stromingshulpmiddelen nodig hebben. Poeders met een grovere deeltjesgrootte stromen daarentegen vrijer, maar kunnen tijdens de verwerking ontmengen. Een volledige deeltjesgrootteanalyse moet niet alleen de gemiddelde deeltjesgrootte omvatten, maar ook de verdeling (omvang en vorm van de deeltjesgroottekromme). Een smalle of bimodale verdeling kan de vloei-eigenschappen en verdichting van het product aanzienlijk beïnvloeden.
Bulk- en tapdichtheid: De dichtheid van poeders heeft een directe invloed op de capaciteit van IBC's. Een poeder met een lage dichtheid heeft meer capaciteit nodig. Een poeder met een lage dichtheid heeft een container met een groter volume nodig voor dezelfde massa product. Als we de verhouding tussen de afgetapte dichtheid en de schijnbare dichtheid (Hausner-index) kennen, kunnen we de samendrukbaarheid van het poeder beoordelen en anticiperen op mogelijke problemen met afstempelen tijdens transport.
Reologisch gedrag: Vloei-eigenschappen bepalen hoe gemakkelijk het poeder zal vloeien wanneer de container wordt geleegd. Poeders kunnen worden geclassificeerd volgens hun vloeibaarheid:
- Vrij stromende poeders: gemakkelijk te hanteren, vereisen weinig hulp
- Cohesieve poeders: kunnen agglomeraten vormen en hebben stromingshulpmiddelen nodig
- Zeer cohesieve poeders: vereisen specifieke oplossingen zoals fluïdisatie, vibratie of zelfs mechanische agitatie.
Specifieke tests zoals het meten van derotshoek, deCarr-index of het gebruik van afschuifcellen maken het mogelijk om deze eigenschappen nauwkeurig te beoordelen.
Gevoeligheid voor vocht en hygroscopiciteit: Hygroscopische poeders absorberen vocht uit de omgevingslucht, waardoor hun fysische en chemische eigenschappen kunnen veranderen. Voor deze producten zijn perfect afgesloten IBC's of containers met ontvochtigingssystemen essentieel. Gevoeligheid voor vocht kan ook bepalend zijn voor de keuze van constructiematerialen en afdichtingen.
Elektrostatische eigenschappen: Sommige poeders, vooral organische stoffen en polymeren, kunnen aanzienlijke elektrostatische ladingen genereren wanneer ze worden gehanteerd. Deze ladingen vormen niet alleen een explosierisico in bepaalde omgevingen, maar kunnen ook de productstroom beïnvloeden. Geaarde containers of containers gemaakt van dissipatieve materialen kunnen nodig zijn voor deze toepassingen.
Abrasiviteit en corrosiviteit: Abrasieve poeders kunnen de interne oppervlakken van containers geleidelijk beschadigen, vooral rond kleppen en afvoergaten. Voor deze producten worden slijtvaste materialen of specifieke coatings aanbevolen. Evenzo vereisen corrosieve producten geschikte materialen zoals316L roestvrij staal of beschermende coatings.
2.2. Productievolume en -snelheid
Een nauwkeurige beoordeling van productievolumes en werktempo's is essentieel om uw vloot IBC's en bijbehorende apparatuur op de juiste manier in te delen. Deze analyse moet niet alleen rekening houden met de huidige situatie, maar ook met toekomstige groeiprognoses.
Analyse van productiestromen: Door uw productiestromen gedetailleerd in kaart te brengen, kunt u de kritieke punten identificeren waar het gebruik van IBC-containers de meeste waarde oplevert. Deze analyse moet rekening houden met :
- Dagelijkse, wekelijkse en maandelijkse volumes verwerkte poeders
- Seizoensgebonden variaties en productiepieken
- Het aantal referenties en de frequentie van productwissels
- Verblijftijden van het product in het productieproces
De grootte van het containerpark: Het aantal benodigde containers hangt af van een aantal onderling afhankelijke factoren:
- Het totale volume van het product in omloop
- De volledige cyclustijd (vullen, transport, opslag, legen, schoonmaken)
- Wachttijden tussen de verschillende fasen van het proces
- Het aantal verschillende referenties dat wordt verwerkt
Een nauwkeurige berekening van deze parameters maakt het mogelijk om de initiële investering te optimaliseren en tegelijkertijd voldoende containerbeschikbaarheid te garanderen.
Modulariteit en schaalbaarheid: Modulaire oplossingen zijn bijzonder geschikt voor bedrijven met variabele of groeiende productievolumes. Door geleidelijk IBC-containers aan te schaffen, kunt u uw investering spreiden en aanpassen aan veranderende behoeften. Een modulaire aanpak kan ook worden toegepast op vul- en ledigingsapparatuur, met stations die kunnen worden geüpgraded en die een groeiend aantal containers tegelijk kunnen verwerken.
Beheer van fysieke en informatiestromen: Het optimaliseren van de fysieke stroom van containers moet gepaard gaan met een effectief geautomatiseerd beheer. Real-time volgsystemen maken het mogelijk om elke container te lokaliseren, de inhoud en de status (vol, leeg, wordt gereinigd) te kennen. Deze beheertools vergemakkelijken de productieplanning en minimaliseren het risico op onderbrekingen in de bevoorrading van lijnen. Ze dragen ook bij aan de volledige traceerbaarheid van batches, een fundamentele vereiste in gereguleerde industrieën.
Geoptimaliseerde omsteltijden: Het gebruik van IBC's verkort de omsteltijden tussen twee producties aanzienlijk. Om dit voordeel te maximaliseren, is het raadzaam om SMED-technieken (Single Minute Exchange of Die) toe te passen, waarbij de containers die nodig zijn voor de volgende productierun van tevoren worden voorbereid.
2.3 Regelgeving en normen
Industrieën die poeders verwerken zijn onderworpen aan strenge regelgeving die verschilt per bedrijfstak en geografisch gebied. Bij de overgang naar IBC's moet al in de ontwerpfase van het project rekening worden gehouden met deze eisen.
Sanitaire en voedingsnormen: In de voedingsmiddelenindustrie moeten materialen die in contact komen met voedingsmiddelen voldoen aan specifieke voorschriften, zoals de Europese Verordening (EG) nr. 1935/2004 of de FDA-normen in de Verenigde Staten. Containers die in deze industrie worden gebruikt, moeten zijn gemaakt van materialen die zijn goedgekeurd voor contact met voedingsmiddelen en die zijn ontworpen voor effectieve reiniging en desinfectie. Fabrikanten moeten 'conformiteitsverklaringen' afgeven waaruit blijkt dat hun containers aan deze eisen voldoen. De implementatie van een HACCP-systeem (Hazard Analysis Critical Control Point) kan ook specifieke aanpassingen aan containers en bijbehorende apparatuur vereisen.
Farmaceutische vereisten en GMP: De farmaceutische industrie is onderworpen aan Good Manufacturing Practices (GMP ). Deze richtlijnen stellen hoge eisen aan traceerbaarheid, reiniging en validatie van apparatuur. De IBC-containers die in deze sector worden gebruikt, moeten over het algemeen het volgende hebben
- Gepolijste oppervlakken (Ra-afwerking ≤ 0,8 μm voor oppervlakken die in contact komen met het product)
- Sanitaire armaturen die voldoen aan de normen (Tri-Clamp, BFM, enz.)
- Volledige documentatie, inclusief materiaalcertificaten, integriteitstests, kwalificatie van apparatuur, enz.
Validatie van de containerreiniging is bijzonder kritisch en kan de implementatie vereisen van specifieke procedures en analytische tests om de afwezigheid van residuen tussen twee producties aan te tonen.
ATEX veiligheid en milieu: Het omgaan met brandbare of explosieve poeders vereist naleving van de ATEX-richtlijn (ATmosphères EXplosibles). Deze Europese regelgeving en haar internationale equivalenten definiëren de maatregelen die moeten worden genomen om explosies in gebieden met een hoog risico te voorkomen. Voor de betreffende toepassingen moeten IBC's worden uitgerust met effectieve, gecertificeerde aardingssystemen. Bepaalde elektrische componenten (sensoren, weegsystemen) moeten zo zijn ontworpen dat ze veilig in deze omgevingen kunnen functioneren.
Traceerbaarheid en gegevensintegriteit: Gereguleerde industrieën eisen volledige traceerbaarheid van grondstoffen en eindproducten. IBC's kunnen worden uitgerust met permanente identificatiesystemen (gegraveerde platen, RFID-tags) om hun geschiedenis en inhoud te traceren. In de farmaceutische industrie isgegevensintegriteit ook cruciaal. Computersystemen voor het beheer van IBC-containers moeten voldoen aan de principes van Titel 21, Deel 11 van de Code of Federal Regulations (21 CFR Deel 11) ofBijlage 11 van de Europese GMP.
Normen voor transport en logistiek: IBC-containers die bestemd zijn voor extern transport moeten voldoen aan internationale normen zoals UN/ADR-certificering voor het vervoer van gevaarlijke stoffen. Hun afmetingen moeten compatibel zijn met logistieke standaarden (pallets, opslagrekken, vrachtwagens) om hun hantering in de hele toeleveringsketen te vergemakkelijken.
3. Dimensionering van apparatuur en integratie van IBC-containers
3.1 De juiste containers kiezen
Het kiezen van het meest geschikte type IBC-container is een cruciale fase in het succes van uw overgang. Bij deze keuze moet rekening worden gehouden met meerdere technische, operationele en economische parameters.
Constructiematerialen: De materiaalkeuze hangt voornamelijk af van de aard van de producten die worden verwerkt en de beperkingen van het gebruik:
Roestvrij staal (304L, 316L)
Voordelen: uitzonderlijke duurzaamheid, hoge chemische weerstand, gemakkelijk te reinigen, compatibel met steriele omgevingen
Toepassingen: farmaceutische industrie, fijnchemie, hoogwaardige voedingsindustrie
Overwegingen: 316L is beter bestand tegen corrosie dan 304L en verdient de voorkeur voor corrosieve producten of zouthoudende omgevingen.
Kunststof van levensmiddelenkwaliteit (PE-HD, PP)
Voordelen: lage kosten, lichtgewicht, bestand tegen zuren en basen
Toepassingen : Standaard voedselverwerking, niet-kritische chemicaliën
Overwegingen: Beperkte levensduur, gevoelig voor schokken en hoge temperaturen
Composietvaten
Voordelen: goed compromis tussen kosten en prestaties, lichtgewicht
Toepassingen : Niet-kritische producten, frequent transport
Overwegingen: Recyclebaarheid soms complex, gemiddelde duurzaamheid
Geometrie en afmetingen : IBC's zijn verkrijgbaar in verschillende formaten, meestal aangepast aan internationale logistieke standaarden:
Kubische/rechthoekige containers
Voordelen: optimalisatie van opslagruimte, stabiliteit
Overwegingen: Kan dode zones hebben in hoeken
Conische containers
Voordelen: gemakkelijker legen, minder residu
Overwegingen: minder optimaal gebruik van opslagruimte
De meest gebruikelijke standaardafmetingen zijn gebaseerd op palletafmetingen (1200 x 800 mm, 1200 x 1000 mm) met variabele hoogtes afhankelijk van de capaciteit.
Volumecapaciteiten: Bij de keuze van de capaciteit moet rekening worden gehouden met de productievolumes, de productdichtheid en de hanteringsbeperkingen:
500 liter: Geschikt voor kleine productieseries of producten met een hoge toegevoegde waarde.
1000 liter: standaardformaat dat een goed compromis biedt tussen capaciteit en wendbaarheid
1500-2000 liter: Voor productie van grote volumes, waarvoor geschikte transportuitrusting nodig is.
Specifieke kenmerken: Afhankelijk van de toepassing kunnen extra kenmerken nodig zijn:
Geïntegreerde tril-/vloeisystemen
Voordelen: Verbeterde stroming voor cohesieve producten
Toepassingen : Fijne poeders, producten gevoelig voor bezinking
Dubbele verwarmings-/koelmantel
Voordelen: handhaaft producttemperatuur, voorkomt condensatie
Toepassingen: temperatuurgevoelige producten, wassen Temperatuurgevoelige producten, wassen, vetten
Thermische isolatie
Voordelen: bescherming tegen externe temperatuurschommelingen
Toepassingen: warmtegevoelige producten, niet-temperatuuromgevingen Hittegevoelige producten, ongecontroleerde temperatuuromgevingen
Afsluitings- en sluitsystemen: de kwaliteit van het sluitsysteem is cruciaal om dichtheid te garanderen en het werk te vergemakkelijken:
Deksels met flensbouten
Voordelen: maximale dichtheid, drukbestendigheid
Overwegingen: langere openings-/sluitingstijden
Snelsluitsystemen
Voordelen: gebruiksvriendelijk, tijdbesparend
Overwegingen: regelmatig onderhoud van afdichtingen vereist
Bodemafsluiters
Er bestaan verschillende technologieën (vlinderklep, kogelafsluiter, meshefboom) met specifieke eigenschappen op het gebied van dichtheid, reinigbaarheid en slijtvastheid. De klepdiameter heeft een directe invloed op het debiet en moet worden aangepast aan de procesvereisten.
3.2. Vul- en leegstations
Efficiënte integratie van IBC's in uw productieproces vereist vul- en ledigingsstations die speciaal zijn ontworpen om de materiaalstromen te optimaliseren en tegelijkertijd veilige en hygiënische handelingen te garanderen.
Vulstations: IBC's moeten zo worden ontworpen dat de productintegriteit behouden blijft en dat ze snel en nauwkeurig werken:
Doseersystemen
Volumetrische doseersystemen: voor toepassingen die een gemiddelde nauwkeurigheid en hoge stroomsnelheden vereisen.
Gewichtsdoseersystemen: voor toepassingen die een hoge doseernauwkeurigheid vereisen
Gecombineerde systemen: combineren snelheid en precisie voor grote capaciteiten
Insluiting en beheer van stof
Opblaasbare afdichtingsmanchetten voor een goede afdichting
Plaatselijke afzuigsystemen om stofemissies op te vangen
Afgesloten cabines met filtratie voor zeer actieve of giftige producten
Verdichten en verdichten
Trilmotoren om het vullen te optimaliseren en het bezette volume te verkleinen
Verdichtingstafels voor producten die gevoelig zijn voor bezinking
Ontluchtingssystemen om ingesloten lucht af te voeren
Leegstations: Legen is vaak het kritieke punt bij poederverwerking. DeIBCFlow®02 is een geavanceerde oplossing voor deze fase:
Werkingsprincipes
Nauwsluitende verbinding met de containerklep
Geïntegreerde stromingshulpsystemen
Nauwkeurige regeling van afvoersnelheid
Geminimaliseerde stofemissies
Inperkingsniveaus
Open insluiting: voor ongevaarlijke producten met afzuigsysteem
Gesloten insluiting: voor gevoelige of actieve producten met vacuüm/drukoverdracht
Totale inperking: voor zeer actieve/toxische producten met gesloten circuit en meerdere barrières
Integratie in het proces
Directe afvoer naar mengers of reactoren
Voeden van verpakkingslijnen
Interface met pneumatische of mechanische transportsystemen
Wegen en regelen: Nauwkeurig wegen is vaak cruciaal:
Weegtechnologieën
Krachtopnemers (standaard)
Wegen boven het hoofd (verhoogde nauwkeurigheid)
Systemen met twee bereiken (capaciteit en nauwkeurigheid)
Geautomatiseerde besturing
Recept- en batchbeheer
Registratie van weeggegevens
Interface met MES, ERP
Reiniging en ontsmetting: Reiniging van stations is net zo belangrijk als reiniging van containers:
Reiniging ter plaatse (CIP/CIP)
Roterende spuitmonden (vullen)
Gesloten circuits (kleppen, aansluitingen)
Geautomatiseerde sequenties (wassen, spoelen, drogen)
Materialen en ontwerp
Gepolijste oppervlakken zonder dode hoeken
Geoptimaliseerde stromingshellingen
Gemakkelijke toegang voor onderhoud
3.3. Automatisering en transport
Het automatiseren van de doorstroming van IBC-containers is een belangrijke stap in het optimaliseren van uw totale productie. Het vermindert niet alleen handmatige interventie, maar verbetert ook de traceerbaarheid en betrouwbaarheid van de activiteiten.
Transportsystemen: De keuze hangt af van de configuratie, de beperkingen en het automatiseringsniveau:
Rollenbanen
Voordelen: eenvoudig, robuust, weinig onderhoud
Toepassingen: horizontale overdrachten, accumulatie
Varianten : Vrije (zwaartekracht) of gemotoriseerde rollen
Kettingtransporteurs
Voordelen: veelzijdigheid, hoogteverschillen overwinnen
Toepassingen: complexe circuits, richtingsveranderingen
Overwegingen: frequenter onderhoud
Automatisch geleide voertuigen (AGV/AMR)
Voordelen: maximale flexibiliteit, dynamische aanpassing
Toepassingen: veranderende omgevingen, verbinding tussen afgelegen gebieden
Overwegingen: hogere investering, IT-infrastructuur
Positioneersystemen : Precisie is essentieel voor geautomatiseerde operaties:
Mechanische stops en geleiders
Voordelen: betrouwbaarheid, eenvoud
Toepassingen : Grof positioneren, stoppen
Actieve centreersystemen
Voordelen: hoge nauwkeurigheid, tolerantiecompensatie
Toepassingen: automatische verbinding met stations
Sensoren en besturingen
Aanwezigheids- en identiteitsdetectie
Verificatie van correcte positionering
Bescherming tegen botsing en verplettering
Identificatie en traceerbaarheid: Een sleutelelement in het garanderen van traceerbaarheid en het vermijden van fouten:
Identificatietechnologieën
Barcodes (economisch)
RFID-tags (contactloos, opslag van informatie)
QR-codes (dichte informatie, omnidirectioneel)
Getraceerde informatie
Unieke containeridentificatie
Inhoud (product, partij, hoeveelheid)
Geschiedenis (vullen, opslag, reiniging)
Status en bestemming
Toezicht en controle: een gecentraliseerd systeem voor optimaal beheer:
Essentiële functies
Real-time weergave (status, positie)
Beheer van transferopdrachten en prioriteiten
Registratie van bewegingen en handelingen
Beheer van alarmen en afwijkingen
Integratie met bestaande systemen
Interface met MES
Communicatie met procesregelaars
Verbinding met kwaliteits-/traceerbaarheidssystemen
Operationele veiligheid: Automatisering moet alle veiligheidsaspecten omvatten:
Beschermingsmiddelen
Fysieke barrières en veilige gebieden
Aanwezigheidsdetectoren en laserscanners
Noodstops en veilige herstarts
Modi bij gestoord bedrijf en noodprocedures
Mogelijkheid tot handmatige interventie
Procedures voor incidentenherstel
Redundantie van kritieke systemen
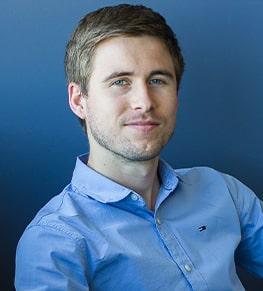
Heb je een project in gedachten ?
Ik ben er om je te adviseren en je te helpen met je project.
Guillaume, expert in modulaire oplossingen voor poederverwerking
4. Beperkingen en oplossingen voor het legen van IBC-containers
4.1. Producteigenschappen die het ledigen beïnvloeden
Het efficiënt legen van IBC's wordt direct beïnvloed door de fysieke eigenschappen van de poeders. Een grondig begrip van deze eigenschappen maakt het mogelijk te anticiperen op mogelijke problemen en passende oplossingen te implementeren.
Stroombaarheid en cohesie: Het vermogen van een poeder om vrij te stromen is cruciaal:
Classificatie volgens vloeibaarheid
Poeders met een vrije stroming (rotatiehoek < 30°): gemakkelijke en regelmatige lediging
Poeders met een gemiddelde stromingshoek (30-45°): kunnen een beetje hulp nodig hebben
Cohesieve poeders (hellingshoek > 45°): hebben hulpmiddelen nodig
4.2. Technische oplossingen voor efficiënt legen
Er bestaan verschillende systemen om het legen van IBC's te optimaliseren. Stromingshulpmiddelen, zoals trilplaten of luchtfluïdisers, voorkomen de vorming van holten en vergemakkelijken de productstroom. Voor vochtgevoelige poeders wordt het legen onder gecontroleerde atmosfeer aanbevolen.
4.3. Speciaal geval van gevoelige producten
Reactieve of sterk hygroscopische poeders vereisen speciale aandacht. Hermetisch afgesloten opslag voorkomt de absorptie van vocht. Het legen moet gebeuren in een afgesloten omgeving om contaminatie te vermijden. Reinigingssystemen (CIP) garanderen een onberispelijke hygiëne tussen elke productiebatch.
5. FAQ: Antwoorden op veelgestelde vragen over de overgang naar IBC-containers
5.1. Wat zijn de belangrijkste voordelen van IBC's ten opzichte van big bags?
- Minder kruisbesmetting
- Eenvoudiger te integreren in geautomatiseerde lijnen
- Minder handling enmenselijke tussenkomst
- Schoner en gecontroleerderlegen
5.2. Hoe kan ik een volledige lediging van IBC's garanderen?
Het gebruik van aangepaste ledigingsstations, zoals deIBCFlow®02, garandeert een volledige extractie van het product zonder verlies of resten.
5.3. Zijn IBC's geschikt voor alle soorten poeder?
Ja, zolang u het juiste model en de juiste accessoires kiest: kleppen, binnenbekleding, stromingshulpmiddelen.
5.4. Hoe lang gaat een IBC mee?
Een goed onderhouden IBC kan tientallen jaren meegaan, waardoor de bedrijfskosten lager zijn.
5.5. Kunnen IBC's in een bestaande productielijn worden geïntegreerd?
Ja, ze kunnen geleidelijk worden geïntegreerd om big bags te vervangen en de procesefficiëntie te verbeteren.
Conclusie
Overschakelen op IBC-containers betekent kiezen voor een schonere, flexibelere en meer geautomatiseerde productie. Deze overgangoptimaliseert de traceerbaarheid, vermindert verontreiniging enverbetert het poederbeheer.
📞 Bent u betrokken bij de verwerking of opwaardering van zeldzame aardmetalen?
Neem contact op met onze experts om samen een krachtige en veilige productielijn op maat te ontwerpen.