Description
High-speed big bag unloading station - Automatic deconditioning without operator intervention
With a throughput of 20 to 40 big bags per hour, this fully automatic station carries out the cutting, handling and evacuation phases of big bags independently.
Implementation examples :
![]() |
![]() |
Cadence: 20 to 40 big bags/h.
Capacity: 2 tons/big bag
Objectives: Automatic cutting, containment & safety
The PALAMATIC PROCESS high-speed big bag unloading station allows the automatic deconditioning of big bags without operator intervention. The cutting, handling and evacuation phases of the big bags are autonomous without the operator's intervention. The latter only ensures the attachment of the big bag on the handling cross.

Operating mode:
1. Attaching and placing the big bag (operator action)
2. Moving the big bag inside the station (automatic hoist control)
3. Cutting and emptying the big bag (automatic solution)
4. Massage of the big bag (according to option) and crumbling of the product
5. Automatic big bag release
6. Compaction of the empty big bag
7. Automatic management of the accumulation of big bags to be emptied and automatic pallet palletization
The PALAMATIC PROCESS design office also offers customized solutions.
The high-speed big bag unloading station is also available in full containment with an integrated big bag compactor.
-
Rate5
-
Automation4
Equipment advantages
- Automatic cutting
- Integrated big bag compactor
- Improvement of bulk materials flow
- Automatic loading
Media
View our equipment in videos
Bulk bag discharging - High rate - Easyflow EF100 200
With a throughput of 20 to 40 bulk bags per hour, this fully automated material unloading station carries out the cutting, handling and evacuation phases of bulk bags independently.
View our equipment in photos
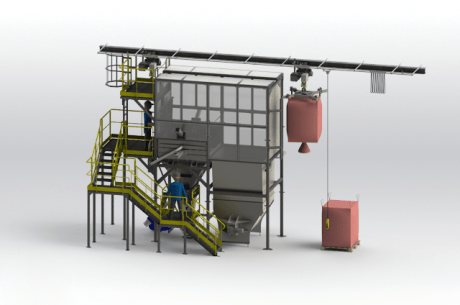
Bulk bag discharging - High rate - Contaiment cage with compactor
This bulk bag unloading system is used to automatically empty bulk bags without operator intervention.
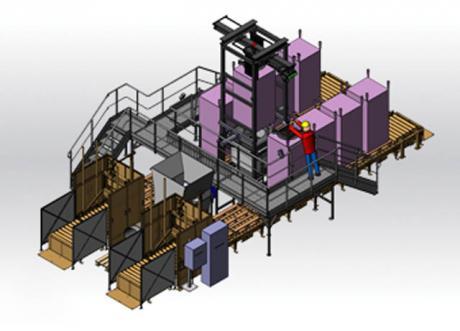
Example of an automated bulk bag discharging system
Two conveying lines with two pallet stackers for increased capacity.
Examples of options: dedusting ring and granulator.
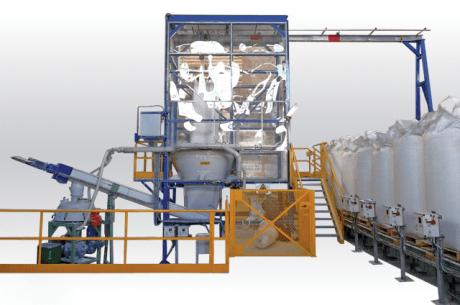
Total containment big bag discharge
Automatic cutting of the big bag. The cutting system is installed according to the big bag being handled.
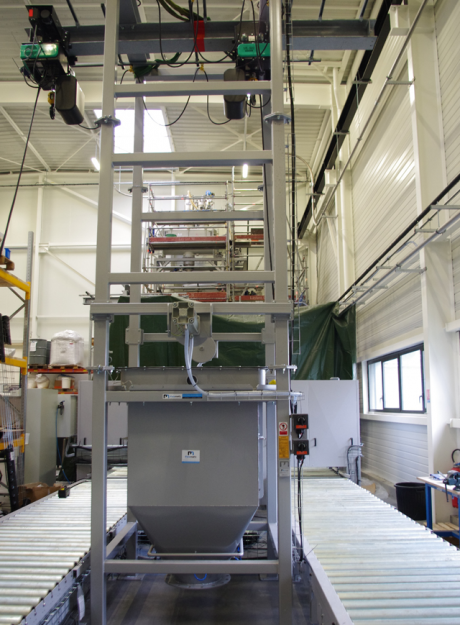
Big bag discharging - Double electri hoist loading
The electric hoist operates in automatic control.
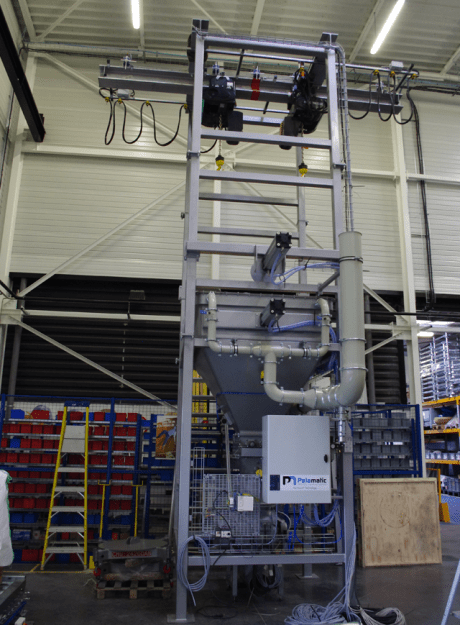
Big bag discharging - Double electric hoist loading
Bulk bag handling for industrial production lines involving raw ingredients and bulk materials handling.
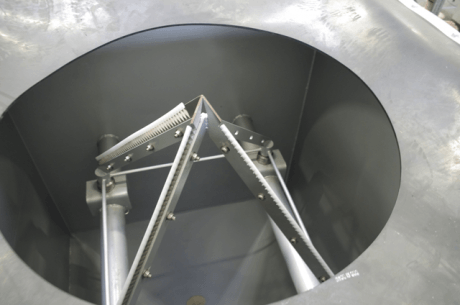
U-shaped bag puncture tip
The spike is used to burt the bottom of the bulk bag.
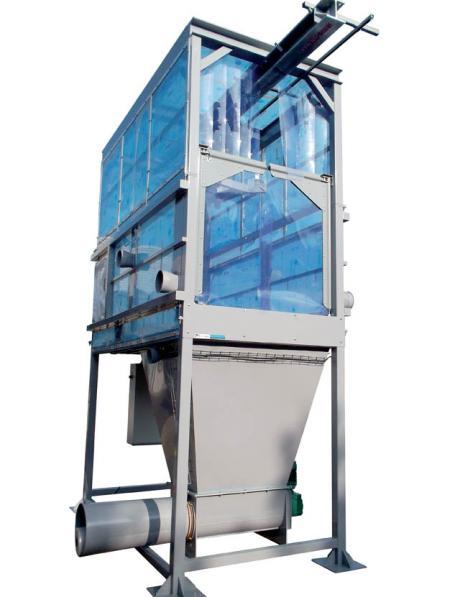
Big bag compactor
A big bag compactor is built-in to maintain a healthy working atmosphere.
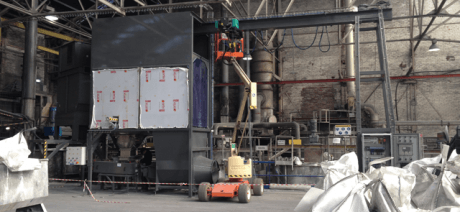
Bulk bag discharging high rate
Discharge of big bag of anticorrosive pigments: automatic cutting, containment and safety.
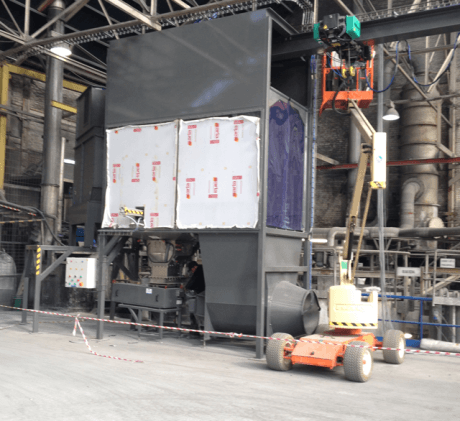
Jumbo bag discharging high rate
Rate of 20 to 40 big bags per hour.
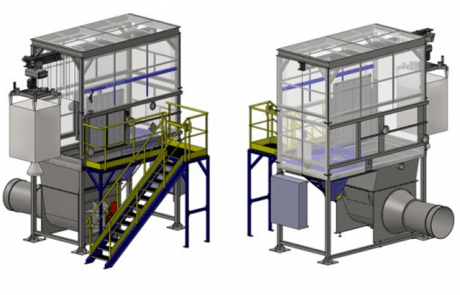
3D view - Bulk bag discharging high rate
We provide technical drawings.
Features
Technical specification
Rate | 20 to 40 big bag/h |
---|---|
Manufacturing materials | painted steel, 304L stainless steel, 316L stainless steel |
Finishing touches | RAL 9006, micro-blasted, electropolishing |
Installed power | 5 kw (depending on option) |
Operating pressure | 6 bar |
Required dust removal rate | 3,000 m³/h |
Maximum dimensions of the big bags (length* width * height) | 1,200* 1,200 * 2,400/ other custom-made |
Entrance | 4-20 mA |
TOR input | 6 |
TOR outpout | 4 |
Options
Case studies
CASE STUDIES WITH THIS EQUIPMENT
Bulk pigment handling
Processed powders: zinc ash, zinc oxide, waelz oxide - Bulk pigment handling - The materials to be emptied are powders whose particularity is to have very heterogeneous characteristics.Chemical
Double confined EasyFlow® EF200 big bag emptying station
Products processed: solid coal rods - Double confined EasyFlow® EF200 big bag emptying station - The installation concerns two big bag unloading stations for high-speed, semi-automatic deconditioning...Minerals and building
Filling of truck with cement
Processed product: cement - Filling of truck with cement - Two EasyFlow® EF100 big bag unloading stations for high-speed semi-automatic unpacking.Minerals and building
Unloading and conveying of cement
Processed powder: cement - Unloading and conveying of cement - Unloading of cement from 1 ton big bags with pneumatic transfer of material to silo storageMinerals and building
Confined deconditioning, dosing and transfer of powders
Processed powders: Minerals and additives (such as titanium dioxide) for the manufacture of paints - Emptying of big bags into mobile IBCs with dosing and transfer of the product to a mixer downstream...Chemical
Cement deconditioning
Processed product: cement - Cement deconditioning - Autonomous bulk bag unloading system for the cement industryMinerals and building