Big bag unloading and mobile IBC docking for powder paint industry
Confined deconditioning, dosing and transfer of powders
Material(s): Various minerals and additives for paint manufacturing, including TiO2.
Objective: Unload big bags of various powders into mobile IBC stations for partial dosing into a pneumatic conveying line.
The client, based out of Pennsylvania, USA, is a manufacturer of paints and coatings for DIY home projects and professional painting services. The manufacturer needed to solve an issue regarding the current method of manually loading big bags directly into mixers, which was unsafe and creating a dusty mess in the workplace. The required solution was to safely unload and contain the materials form a big bag into transferrable IBC’s. The operator would need to fully discharge the big bag into the IBC and partially dose by weight the required amount of the material to be mixed, according to the recipe. The IBC would plug into a rotary airlock valve that fed a pneumatic conveying line for the transfer of the material to a downstream plow mixer. When the required amount of the specific ingredient was dosed into the conveying line, the IBC was sealed, disconnected and put into storage for later use.
Project scope of supply:
- Big bag unloading station
- 900 and 2,000 liter IBCs containers
- Rotary airlock valve and pneumatic conveying system
- Control panel & automation
Conceptual diagram:
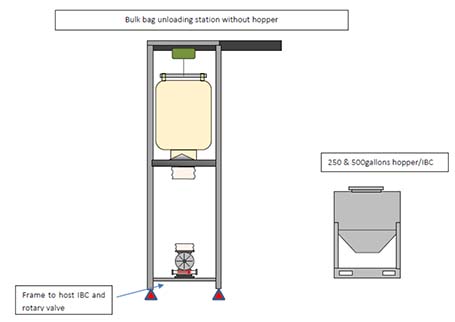
1. Big bag unloading station
The central piece to this project is the big bag unloading and IBC filling station.
Palamatic Process offered a modified version of our FIBC unloading unit - Loading with electric hoist EasyFlow® 125. In order to make the full discharge operation of the big bag efficient with no operator intervention, the station was equipped with a burst spike. By using the weight of the big bag, the serrated cutting blades can pierce the bottom of the big bag and create a u-shaped flap opening. The contents within automatically discharge into the IBC below. The big bag loading is provided by an electrical hoist on a trackway that can lift, transfer and lower the container onto the cutting tool. The hoist mechanism has a lifting capacity of 1,300 kg.
All parts that come into contact with the materials are made of 304 stainless steel. The entire installation is placed on load cells for the purpose of dosing the required amount of ingredients into the pneumatic conveying line, depending on the recipe.
2. 900 and 2,000 liter IBCs containers
For the purpose of dosing and storing various materials, mobile intermediate bulk containers were implemented. The IBCs are provided in 900 and 2,000 liters sizes to accommodate both lighter and heavier density materials. Other integrated features include:
- Reverse jet pulse dust filters: to prevent pressure back up in the IBC and maintain a dust free work environment. The dust filters are connected to a compression air tank to keep the filters clean, prevent clogging and reclaim material in the IBC.
- Vibratory Flow Aids: to help shake the bin and prevent material rat-holing or bridging.
- Manual butterfly valve: to provide an isolation gate to contain the material after dosing the required amount.
- Mobile Frame: the frame is designed with a forklift skid for transfer of the IBC in and out of the bulk material unloading dock.
- BFM flexible fitting and cap: To make a quick connection to the discharge outlet on the big bag unloading station as well as to cap it when removed and placed in storage.
- Low level sensor: to provide a visual indication when the IBC is empty and needs to be refilled or replaced.
3. Blow-through Rotary Airlock Valve and Pneumatic Conveying System
In order to safely and effectively dose the material into the powder blender located downstream, an 8” blow-through rotary airlock valve is connected to the bottom of the IBC outlet and manual butterfly valve. The rotary valve consists of a helical shaped, multi-lobed rotor, pressure capable housing, u-shaped trough at the bottom of the housing, and quick connect inlet and outlet flanges on the sides of the body. The powder dosing valve provides a steady and precise metered feed into the pressure conveying line for a consistent air to material volume mix.
The rotary dosing valve turns at a rate of 18 RPM with a theoretical flow rate of 315 pi³/hr and dosing accuracy of approx. 1 kg. The pressure blower consists of an acoustic hood for sound dampening, tri-lobe design, internal pressure safety valve, electronic pressure switch (to automatically adjust the pressure flow and avoid risk of material clogging the pipe), anti-vibration pads, etc.
4. Control Panel & Automation
The Pal’Touch visually programmed PLC provides complete direction over the electronic functions of the entire system. For this project, the client was provided with a Siemens S7-1200, 10” touch screen panel with Profinet communication. Palamatic Process can provide other options as alternatives if the client prefers. Palamatic Process designs, assembles and programs all controls panels in-house. Our team of automation engineers include user friendly raw material inputs, lot traceability, operator identification and dosing reliability. The PLC handles and controls the big bag loading and discharge, IBC functions described earlier, loss-in-weight dosing management, rotary valve actuation and booster pump monitoring and control. Further advantages include our Pal’Assist service for remote connection diagnostics. By integrating an ethernet remote maintenance box, our maintenance team can connect remotely and diagnose any issues within the control panel programming. Our technicians are also available for on-site commissioning and training support.
Palamatic Process has been supplying the powder and big solids industry with big bag handling equipment since 1992. In order to determine what solution is best for your project, contact one of our sales engineers. Together, our team of experts can provide the right kind of powder filling equipment that will fulfil your every production goal. Contact one of our experts today for assistance with needed material handling solutions and to request a quote.