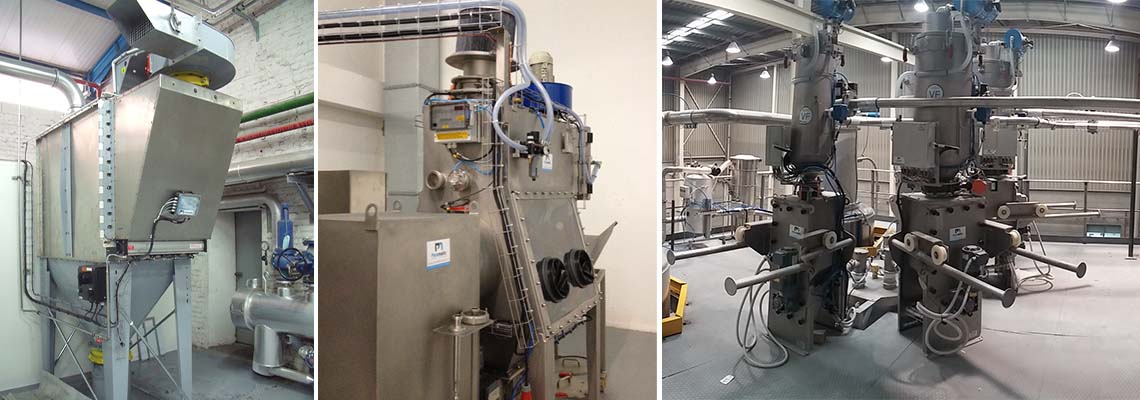
Dans toute unité de production, le dépoussiérage et le confinement sont des facteurs clés pour assurer un lieu de travail sûr et sain aux opérateurs. Il existe plusieurs dispositifs et types d'équipements qui permettent d'y parvenir que nous détaillons ci-dessous.
1. Anneaux de Pouyès / dépoussiérage
Les anneaux de dépoussiérage, également appelés d'anneaux de Pouyès, sont utilisés sur les points de chargement de matériaux qui relèvent d’une opération manuelle. Les opérateurs peuvent avoir besoin de charger les produits directement dans une trémie de stockage ou une cuve de mélange. Les anneaux de Pouyès sont des dépoussiéreurs destinés au chargement de cuves, de réacteurs ou de conteneurs cylindriques.
Les anneaux de dépoussiérage protègent l'environnement de travail de l'opérateur en capturant les particules directement à la source d'émission. Leur conception simple consiste en une entrée ouverte avec une bride de raccordement inférieure et un piquage pour raccorder un tuyau à un système central de dépoussiérage. En créant une dépression dans l'atmosphère environnante, la poussière est capturée au fur et à mesure que le matériau passe par l'entrée.
Ils sont couramment utilisés dans les types d'opérations suivants :
- Remplissage de trémies par de petits sacs de poudre.
- Chargement de réacteurs
- Remplissage de fûts
- Autour de l'entrée d'un mélangeur
- Dépoussiérage des postes de travail
2. Confinement physique
L'une des façons d'empêcher les particules fines de flotter librement dans votre atelier de production est de concevoir des équipements étanches à la poussière. L'un des meilleurs exemples est celui des stations de déversement des sacs et des big bags. En général, ces unités sont conçues pour permettre à l'opérateur d'ouvrir une porte d'accès afin de détacher le bec de décharge d'un big bag ou, dans le cas des plateaux à sacs, de charger directement le sac sur le plateau de la station de déchargement. L'opérateur doit ensuite ouvrir manuellement le conteneur pour libérer le matériau.
Les boîtes à gants peuvent être utilisées pour fournir une barrière physique entre l'opérateur et le conteneur. En disposant d'une fenêtre en verre avec des fixations pour gants, l'opérateur peut couper ou détacher le sac et éviter toute exposition ou contact direct avec le matériau à l'intérieur. De même, le fait d'entourer l'équipement de production d'un champ de confinement en poly-verre peut isoler davantage la zone environnante de l'exposition aux particules toxiques.
3. Transfert par le vide
Il existe plusieurs façons de transférer les poudres depuis le point de chargement de votre usine jusqu'à leur destination finale de conditionnement. Le transport mécanique, le transport pneumatique, les convoyeurs à vis, etc. sont tous utilisés sous une forme ou une autre entre les équipements de production et certains ont tendance à produire plus de poussière que d'autres.
Cependant, le transport par aspiration est l'une des méthodes les plus propres pour transporter des matériaux secs. Même si votre réseau de tuyaux présente des fuites, la fuite se fera de l'extérieur vers l'intérieur. Avec les systèmes de transport sous pression, la fuite se ferait de l'intérieur vers l'extérieur, provoquant des déversements de matériaux et de la poussière dans l'atmosphère. La raison en est simple : en tirant un vide de la source d'alimentation au point de livraison, il n'y a pratiquement aucune chance que le matériau fuie à l'extérieur des tuyaux. De plus, en utilisant un cyclone à la fin du système de transport du matériau, un filtre à poussière peut être directement intégré au sommet de la trémie de collecte. Les particules lourdes tournent autour du cyclone et se déposent au fond, tandis que l'air sale est séparé et épuré par le filtre situé en haut. De cette façon, l'air propre est acheminé vers la pompe à vide, ce qui permet de garder la zone propre et la pompe en excellent état de fonctionnement.
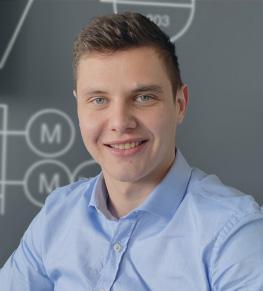
Besoin de conseils en dépoussiérage ou en dosage ?
Je suis disponible pour échanger sur le sujet.
Loïc, expert poudre
4. Dépoussiéreur central
Avec un dépoussiéreur centralisé, la poussière est séparée du flux d'air au moyen d'éléments filtrants à plis plats ou pliés. Un fournisseur d'équipement de filtration des poussières doit calculer tous les points de collecte nécessaires et le débit d'air en pieds cubes par minute (CFM) requis pour aspirer la quantité d'air nécessaire dans une unité centrale.
Le cœur du système est le dépoussiéreur à manches central qui se compose d'un boîtier en acier, d'éléments filtrants insérés horizontalement ou verticalement, d'une trémie de collecte pour l'évacuation de la poussière et d'un système pneumatique de nettoyage de l'air à jet pulsé inverse intégré dans la porte d'accès au filtre. Tous les éléments, y compris la taille et la capacité du ventilateur de l'unité centrale de dépoussiérage, sont conçus en fonction des besoins des installations de production. En général, elle est surdimensionnée pour permettre des extensions futures du processus et des raccordements au système.
5. Ligne process DosingMatic
Palamatic Process a conçu un système automatisé clé en main de dosage des ingrédients : DosingMatic®. Ce système est conçu pour préparer et équilibrer tous les ingrédients secs en lots pesés. La cabine de dosage fait automatiquement la navette sous des trémies de dosage à perte de poids et est remplie par des doseurs à vis. Les ingrédients sont ainsi préparés dans une trémie de pesée mobile et déplacés vers un point de connexion en aval (système de transport pneumatique, convoyeur à vis, mélangeur, etc.) Les cellules de pesée intègrent un volume tampon allant de 50 à 300 litres selon les besoins de chaque recette. Le système peut être conçu pour intégrer de 10 à 40 trémies de chargement.
En automatisant le dosage des ingrédients secs de manière confinée, l'exposition à la poussière est considérablement réduite.