Détection des particules métalliques dans l’industrie des poudres : normes et réglementations à connaître
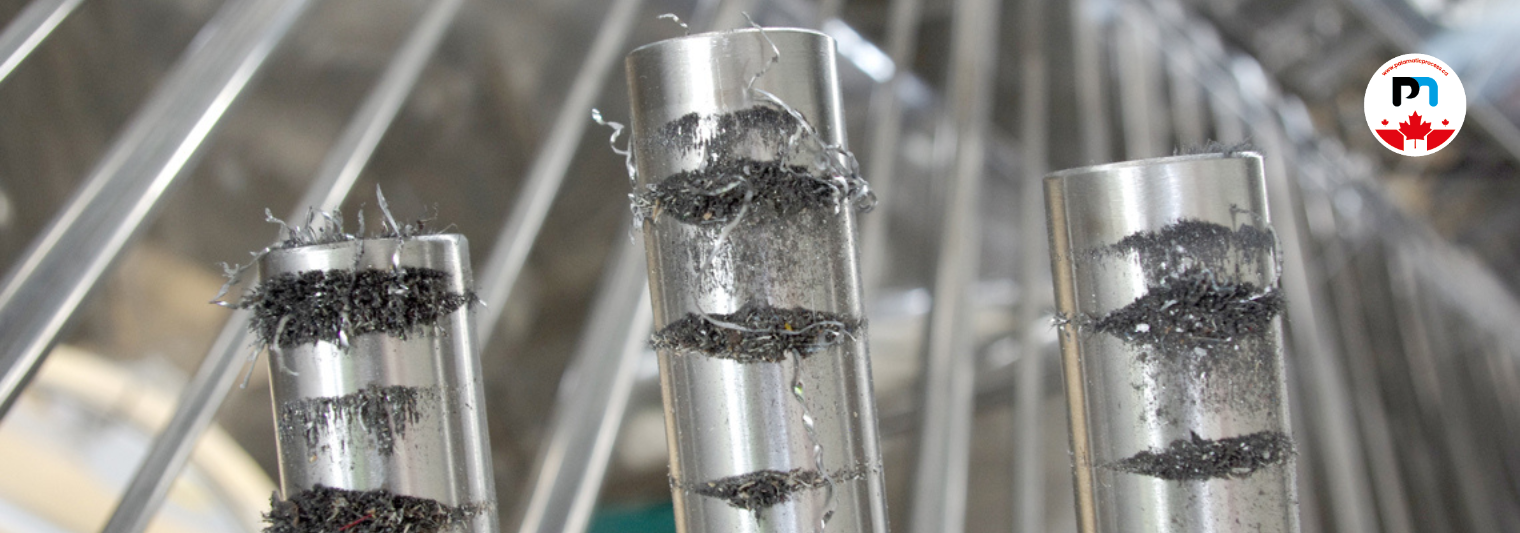
- 1. Pourquoi réglementer la détection des particules métalliques ?
- 2. Quelles sont les principales normes en vigueur ?
- 3. Comment se conformer aux réglementations sur la détection des métaux ?
- 4. Quelles sanctions en cas de non-conformité ?
- 5. FAQ : Questions fréquentes sur la détection des particules métalliques
- 6. Conclusion
La contamination métallique est un enjeu majeur dans l’industrie des poudres, notamment dans les secteurs agroalimentaire, pharmaceutique et chimique. Pour garantir la sécurité des produits et la conformité réglementaire, des normes strictes encadrent l’utilisation des détecteurs de métaux et des séparateurs magnétiques.
Cet article explore les principales réglementations en vigueur et leur impact sur les industriels manipulant des poudres.
Pourquoi réglementer la détection des particules métalliques ?
Les risques liés à la contamination métallique
La présence de particules métalliques dans les produits en poudre peut avoir des conséquences graves sur la santé des consommateurs et entraîner des pertes économiques significatives pour les entreprises concernées.
Conséquences pour la santé des consommateurs :
- Risque d'ingestion de corps étrangers : La présence de corps étrangers durs, pointus ou acérés dans les produits alimentaires représente un réel danger pour le consommateur en cas d'ingestion accidentelle.
- Hospitalisations liées à l'ingestion de corps étrangers : L'ingestion de corps étrangers représente environ 4 % des urgences endoscopiques chez l'adulte.
Conséquences industrielles et économiques :
- Fréquence des rappels de produits : La contamination physique, notamment par des particules métalliques, est une cause fréquente de rappels de produits dans l'industrie agroalimentaire.
- Exemples concrets de rappels récents : Des rappels de pains, produits de boulangerie ou produits surgelés ont été effectués en raison de la présence possible de corps étrangers métalliques.
- Implications économiques : Les rappels de produits entraînent des coûts élevés pour les entreprises (pertes directes, réputation, confiance).
Les secteurs concernés
La contamination métallique touche plusieurs secteurs industriels, chacun étant confronté à des défis spécifiques.
- 1. L'agroalimentaire : Les produits en poudre tels que la farine, le lait en poudre et les épices sont particulièrement vulnérables. Les rappels pour présence de corps étrangers métalliques sont fréquents.
- 2. L'industrie pharmaceutique : La présence de particules métalliques peut altérer l'efficacité des médicaments et poser des risques pour la santé des patients. Les bonnes pratiques de fabrication imposent une surveillance stricte.
- 3. L'industrie chimique et plasturgie : Les particules métalliques peuvent affecter la qualité des produits finis (défauts, non-conformités). La détection est essentielle pour la qualité et la sécurité.
2. Quelles sont les principales normes en vigueur ?
La réglementation encadrant la détection des particules métalliques varie selon les industries et les régions. Les normes définissent des exigences strictes pour garantir la sécurité des consommateurs et la conformité des produits.
Normes alimentaires internationales
Dans l’industrie agroalimentaire, la contamination métallique est une cause majeure de rappels de produits. Pour y remédier, plusieurs normes et certifications imposent des contrôles rigoureux.
- HACCP (Hazard Analysis Critical Control Point)
- Système de gestion des risques qui impose l’identification et la maîtrise des points critiques liés aux contaminants physiques. Les détecteurs de métaux doivent être positionnés à des points de contrôle critiques (CCP), notamment avant le conditionnement. Exigé par de nombreuses autorités sanitaires (FDA, DGCCRF, etc.).
- IFS (International Featured Standards) & BRC (British Retail Consortium)
- Normes reconnues pour garantir la sécurité des produits finis. Elles imposent l’intégration de détecteurs de métaux et d’aimants industriels. BRC exige, par exemple, que les équipements puissent identifier des particules métalliques inférieures à 1,5 mm dans certains types d’aliments.
- ISO 22000
- Norme internationale couvrant l’ensemble de la chaîne alimentaire. Inclut des exigences sur la maîtrise des dangers physiques (détection métaux), s'appuie sur HACCP mais intègre des obligations de traçabilité et de validation des équipements.
Réglementations pharmaceutiques
La présence de particules métalliques peut compromettre la pureté des médicaments et exposer les patients à des risques graves.
- GMP (Good Manufacturing Practices – Bonnes Pratiques de Fabrication)
- Imposent des contrôles systématiques de contamination métallique à toutes les étapes. Les détecteurs de métaux doivent être calibrés et validés régulièrement.
- USP <232> et <233> (United States Pharmacopeia)
- Normes spécifiques au contrôle des impuretés élémentaires, y compris métalliques. Fixent des seuils maximaux de métaux lourds acceptables.
Normes spécifiques aux industries chimiques et plastiques
Ces industries sont soumises à des réglementations visant à éviter la contamination et garantir la sécurité.
- ATEX 2014/34/UE (Atmosphères Explosives)
- S’applique aux zones à risque d’explosion (poudres combustibles). Les équipements de détection doivent être certifiés ATEX pour éviter tout risque d’étincelle.
- REACH (Registration, Evaluation, Authorization and Restriction of Chemicals)
- Règlement européen visant à limiter l’usage de substances dangereuses. Obligation de prouver que les processus sont exempts de contamination métallique pouvant altérer les propriétés chimiques.
Cas concrets d’application des normes de détection des particules métalliques
-
1. Industrie agroalimentaire : mise en conformité avec HACCP et BRC
Cas : Une usine de production de lait en poudre en Europe
Suite à la détection de microparticules d’acier inoxydable.Problème identifié : Usure des équipements de broyage.
Actions mises en place : Intégration d’un détecteur de métaux haute sensibilité en fin de ligne, ajout d’un aimant haute intensité avant conditionnement, plan de validation HACCP.
Résultats : Réduction de 98% des contaminations, certification BRC niveau AA.
-
2. Industrie pharmaceutique : conformité avec GMP et USP <232>
Cas : Fabrication de gélules pharmaceutiques
Suite à la détection de résidus d’acier.Problème identifié : Dégradation des machines de compression.
Actions mises en place : Installation de détecteurs haute fréquence en amont, validation périodique GMP/USP, traçabilité intégrale.
Résultats : Aucune contamination ultérieure, conformité USP assurée.
-
3. Industrie chimique et plasturgie : respect des normes ATEX et REACH
Cas : Fabrication de poudres plastiques (industrie automobile)
Pour éviter les défauts dus aux particules métalliques.Problème identifié : Risque de particules métalliques altérant la qualité, site classé ATEX.
Actions mises en place : Utilisation de séparateurs magnétiques aux étapes critiques, ajout d’un système de détection en ligne certifié ATEX, validation selon REACH.
Résultats : Taux de non-conformité < 0,01%, certification ATEX validée.
3. Comment se conformer aux réglementations sur la détection des métaux ?
Se conformer aux réglementations nécessite une approche rigoureuse combinant technologie, procédures de contrôle et validation continue.
Intégration des détecteurs de particules métalliques dans les lignes de production
L’un des principaux moyens d’assurer la conformité est d’intégrer des équipements de détection performants à différentes étapes du processus.
1. Choisir le bon type de détecteur
Plusieurs technologies sont disponibles :
- Détecteurs électromagnétiques : Repèrent contaminants ferreux et non ferreux via champs magnétiques. Idéal pour poudres sèches.
- Détecteurs à rayons X : Identifient métaux mais aussi verre, plastiques denses.
- Séparateurs magnétiques : Capturent physiquement les particules ferreuses en amont.
Exemple : En agroalimentaire, utilisation fréquente de détecteurs à tunnel sur convoyeurs avant conditionnement.
2. Définir les points de contrôle critiques (CCP)
Les CCP sont des étapes où la détection/élimination doit être maximisée :
- À la réception des matières premières.
- Avant et après le tamisage (détecter usure équipement).
- Juste avant le conditionnement (dernier contrôle).
Bonnes pratiques : Utiliser la méthode HACCP pour identifier et surveiller ces points.
Bonnes pratiques pour garantir la conformité
1. Calibration et validation des détecteurs
Les détecteurs de métaux doivent être régulièrement testés et calibrés.
Tests de validation recommandés :
- Test de bille métallique : Passage d'échantillons calibrés.
- Vérification des seuils de sensibilité : Ajustement selon normes.
- Contrôles documentés : Archivage pour traçabilité et audits.
2. Enregistrement et traçabilité des contrôles
La documentation est essentielle.
Éléments à inclure :
- Horodatage des contrôles.
- Résultats des tests et calibrations.
- Actions correctives si détection.
Exemple : En pharma (GMP), conservation des enregistrements pendant au moins 5 ans.
3. Formation du personnel à la gestion des contaminants métalliques
Un personnel bien formé évite les erreurs et assure une surveillance efficace.
Programme de formation recommandé :
- Sensibilisation aux dangers.
- Procédures de contrôle et d’entretien.
- Conduite à tenir si détection.
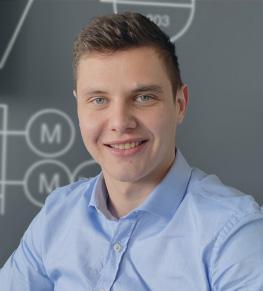
Vous avez un projet ?
Je suis disponible pour vous conseiller et vous accompagner dans votre étude.
Loïc, expert en sécurité des procédés poudres et détection de contaminants
4. Quelles sanctions en cas de non-conformité ?
Le non-respect des réglementations relatives à la détection des particules métalliques peut avoir de lourdes conséquences pour les entreprises, tant sur le plan financier que juridique.
Conséquences juridiques et financières
Lorsqu’une contamination métallique est détectée dans un produit mis sur le marché, les autorités sanitaires peuvent exiger un rappel de lot, une suspension de production ou même des sanctions pénales.
1. Rappels de produits et perte financière
- Un rappel de produit peut coûter plusieurs millions d’euros à une entreprise en raison de la destruction des stocks et du remboursement des distributeurs.
- En cas de contamination alimentaire, les supermarchés et les consommateurs peuvent réclamer des indemnisations, augmentant encore l’impact financier.
- Exemple (2022) : Rappel de >200 000 unités de farine contaminée (perte estimée : 4M€).
2. Sanctions administratives et pénales
- Autorités sanitaires (DGCCRF, FDA, EFSA) peuvent imposer des amendes (non-respect HACCP, BRC, ISO 22000).
- Fermeture temporaire ou définitive de l’usine peut être ordonnée si les mesures correctives ne sont pas mises en place rapidement.
- En cas de mise en danger des consommateurs, les dirigeants peuvent faire face à des poursuites judiciaires pour négligence ou mise en danger de la vie d’autrui.
- Exemple (2021) : Entreprise pharma condamnée à 1,2M€ d'amende (médicaments impropres).
Impact sur la réputation et la confiance des consommateurs
Une contamination métallique peut gravement affecter l’image de marque d’une entreprise et entraîner une perte de parts de marché.
1. Perte de confiance des consommateurs
- Les rappels de produits sont souvent médiatisés, ce qui peut nuire à la crédibilité d’une entreprise.
- Une étude a révélé que 70 % des consommateurs évitent une marque après un rappel de produit lié à un danger sanitaire.
2. Risque de rupture de contrats avec les distributeurs
- Les grandes chaînes de distribution imposent des normes strictes et peuvent rompre un contrat si un fournisseur ne respecte pas les exigences de sécurité alimentaire.
- Exemple : Marque de nutrition infantile perdant son contrat principal (chute CA de 30%).
Solution : Une gestion proactive des risques et un contrôle qualité rigoureux sont essentiels pour éviter ces situations.
5. FAQ : Questions fréquentes sur la détection des particules métalliques
- Comment fonctionne un détecteur de métaux dans une ligne de production ?
Il utilise un champ électromagnétique pour repérer la présence de particules métalliques. Si le champ est perturbé, un signal alerte l’opérateur ou active un système d’éjection. - Quels sont les métaux les plus couramment détectés dans l’industrie des poudres ?
Principalement : Acier inoxydable (usure équipements), Fer (outils, structures), Aluminium (emballages), Métaux lourds (contamination accidentelle matières premières). - Quelle est la réglementation en vigueur pour la détection des métaux en agroalimentaire ?
Les principales normes sont HACCP, BRC & IFS, ISO 22000. - Quelle est la différence entre un détecteur de métaux et un séparateur magnétique ?
Un détecteur repère et signale/rejette. Un séparateur magnétique capture physiquement les particules ferreuses. - À quelle fréquence faut-il vérifier et calibrer un détecteur de métaux ?
Recommandation : tests de validation quotidiens, calibration complète mensuelle (selon normes). - Comment éviter les faux positifs dans la détection des métaux ?
Assurer un environnement exempt d’interférences électromagnétiques, ajuster la sensibilité selon le produit (attention aux sels/humidité), former les opérateurs. - Quels secteurs autres que l’agroalimentaire sont concernés par ces réglementations ?
Industrie pharmaceutique (GMP, USP), Chimie et plasturgie (REACH, ATEX), secteur minier et métallurgique.
6. Conclusion : garantir la sécurité et la conformité grâce à la détection des métaux
La contamination par des particules métalliques représente un risque majeur pour l’industrie des poudres. Qu’il s’agisse de produits alimentaires, pharmaceutiques ou chimiques, le respect des normes et réglementations est essentiel pour garantir la sécurité des consommateurs et éviter des sanctions lourdes.
L’intégration de détecteurs de métaux adaptés, combinée à des points de contrôle critiques bien définis, permet de réduire drastiquement les risques de contamination.
De plus, une maintenance régulière, une formation des opérateurs et une documentation rigoureuse sont des éléments clés pour assurer la conformité aux exigences réglementaires.
✅ Besoin d’optimiser la détection des métaux dans votre ligne de production ? Contactez nos experts pour un audit personnalisé et des solutions adaptées à vos besoins industriels.