Transition vers une production flexible : adopter les conteneurs IBC pour une gestion efficace des poudres
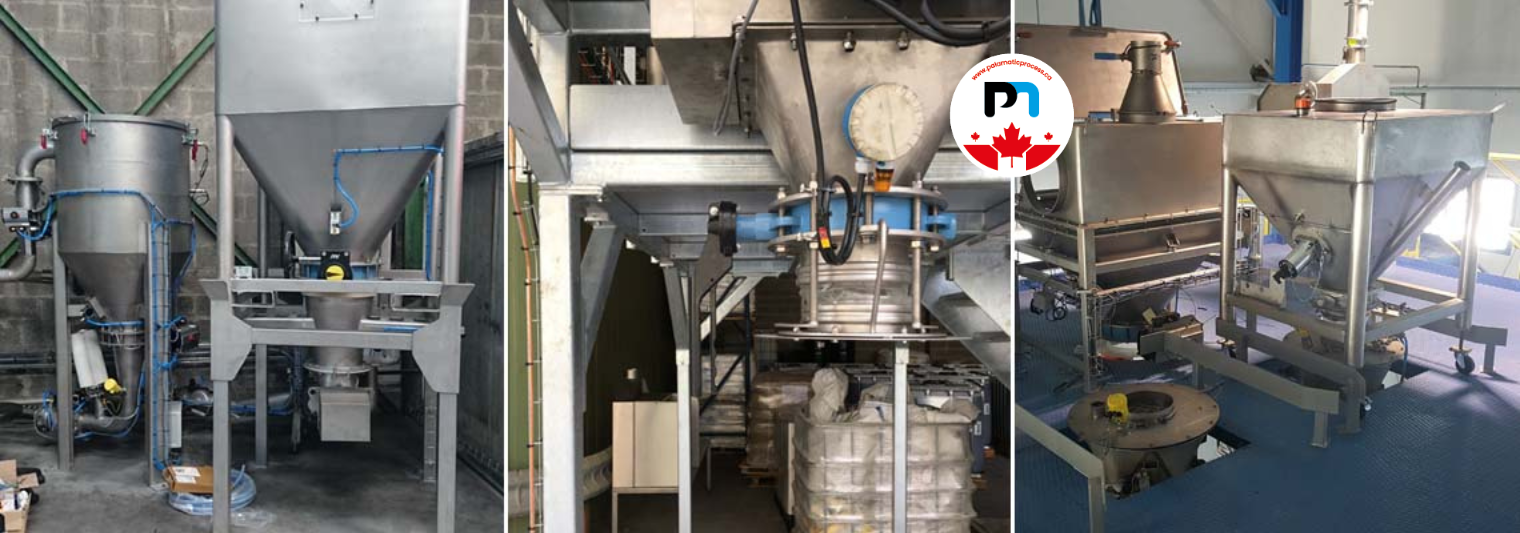
- 1. Pourquoi envisager une transition vers les conteneurs IBC ?
- 2. Questions préliminaires pour une transition réussie
- 3. Dimensionnement des équipements et intégration des conteneurs IBC
- 4. Contraintes et solutions liées à la vidange des conteneurs IBC
- 5. FAQ : Réponses aux questions courantes sur la transition vers les conteneurs IBC
- 6. Conclusion
Les industries agroalimentaires, pharmaceutiques et cosmétiques évoluent vers des solutions de production plus propres et automatisées.
La gestion des poudres en big bags et en sacs pose des contraintes : manipulations répétitives, émissions de poussières, contamination croisée. Les solutions full conteneurs IBC offrent une alternative fiable et flexible.
Ils garantissent une manutention simplifiée, une meilleure traçabilité et une intégration facile dans des processus automatisés.
Mais comment réussir cette transition ? Quels sont les critères à considérer ?
Comment dimensionner les équipements et optimiser la vidange des conteneurs IBC ? Cet article détaille les étapes essentielles pour adopter une production plus efficace et hygiénique.
1. Pourquoi envisager une transition vers les conteneurs IBC ?
1.1. Limites des méthodes traditionnelles
Les méthodes traditionnelles de manipulation des poudres, bien qu'encore largement répandues, présentent des inconvénients majeurs qui pèsent sur la productivité et la qualité des opérations industrielles.
Manutention lourde et risques ergonomiques : La manipulation des big bags nécessite l'utilisation d'équipements spécifiques comme des palans ou des chariots élévateurs. Ces opérations représentent non seulement une charge physique importante pour les opérateurs, mais également un risque d'accidents du travail non négligeable. Les mouvements répétitifs et les postures contraignantes peuvent engendrer des troubles musculosquelettiques (TMS), première cause de maladies professionnelles dans l'industrie.
Temps de changement de lot prolongés : Le passage d'un lot de production à un autre avec des systèmes traditionnels implique de nombreuses manipulations : retrait des sacs ou big bags vides, nettoyage des équipements, mise en place des nouveaux contenants. Ces opérations peuvent représenter jusqu'à 20% du temps de production total, réduisant significativement la productivité des lignes.
Contamination croisée et problèmes d'hygiène : Les systèmes ouverts favorisent les émissions de poussières et les risques de contamination entre différents produits. Dans les industries sensibles comme la pharmacie ou l'agroalimentaire, ces problématiques peuvent avoir des conséquences graves sur la qualité du produit final et la sécurité des consommateurs.
Impact environnemental : L'utilisation de sacs et, dans une moindre mesure, de big bags génère une quantité importante de déchets. Les sacs en papier ou en plastique sont généralement à usage unique, ce qui va à l'encontre des objectifs de développement durable que se fixent de plus en plus d'entreprises.
Traçabilité limitée : Les systèmes traditionnels offrent une traçabilité réduite des produits tout au long de la chaîne de production. L'identification manuelle des lots et les multiples transferts de produits augmentent les risques d'erreurs dans le suivi des matières premières et des produits finis.
1.2. Avantages des conteneurs IBC
Les conteneurs IBC représentent une alternative moderne et efficace qui répond directement aux limitations des méthodes traditionnelles tout en apportant des bénéfices supplémentaires.
Hermétique et hygiénique : La conception fermée des conteneurs IBC empêche toute émission de poussière et protège le produit des contaminations externes. Les modèles en acier inoxydable offrent des surfaces lisses, faciles à nettoyer et à désinfecter, répondant ainsi aux normes d'hygiène les plus strictes de l'industrie pharmaceutique et alimentaire.
Facilité de manipulation et ergonomie : Conçus pour être déplacés facilement à l'aide de transpalettes ou de systèmes automatisés, les conteneurs IBC réduisent considérablement les efforts physiques des opérateurs. Leur forme standardisée et leurs dimensions optimisées facilitent le stockage et la manutention, améliorant ainsi les conditions de travail et la sécurité.
Intégration dans des lignes automatisées : Les conteneurs IBC sont parfaitement adaptés à l'automatisation. Ils peuvent être équipés de systèmes d'identification (RFID, codes-barres) permettant leur suivi en temps réel. Cette compatibilité avec les technologies de l'Industrie 4.0 offre de nouvelles perspectives en termes de gestion de production et d'optimisation des flux.
Vidange contrôlée et sécurisée : Les systèmes de vidange spécifiques comme l'IBCFlow®02 permettent un déchargement maîtrisé des poudres, limitant les émissions et garantissant un transfert complet du produit. Des technologies avancées comme les vannes papillon ou les systèmes à double clapet assurent une étanchéité parfaite pendant toutes les phases de manipulation.
Réduction des temps morts : L'utilisation de conteneurs IBC permet d'optimiser les changements de lot et de réduire les temps de nettoyage. Un conteneur vide peut être immédiatement remplacé par un conteneur plein, assurant ainsi une continuité de production. Cette flexibilité opérationnelle se traduit par une augmentation significative du taux d'utilisation des équipements.
Durabilité et retour sur investissement : Construits pour durer, les conteneurs IBC en acier inoxydable peuvent être utilisés pendant plusieurs décennies avec un entretien minimal. Bien que l'investissement initial soit plus important que pour des solutions en big bags, l'amortissement se fait rapidement grâce aux économies réalisées sur les consommables et à l'amélioration de la productivité.
Traçabilité optimisée : Chaque conteneur peut être identifié individuellement, permettant un suivi précis des lots tout au long du processus de fabrication. Cette traçabilité renforcée facilite la gestion des rappels de produits et la conformité aux exigences réglementaires de plus en plus strictes.
2. Questions préliminaires pour une transition réussie
2.1. Nature des produits manipulés
La réussite d'une transition vers l'utilisation de conteneurs IBC repose en grande partie sur une analyse approfondie des caractéristiques des poudres manipulées. Ces propriétés détermineront non seulement le type de conteneur à privilégier, mais également les équipements auxiliaires nécessaires pour une gestion optimale.
Granulométrie et distribution particulaire : La taille des particules influence directement le comportement d'écoulement des poudres. Les produits à granulométrie fine (inférieure à 100 microns) présentent généralement une cohésion plus importante et peuvent nécessiter des assistances à l'écoulement. À l'inverse, les poudres à granulométrie plus grossière s'écoulent plus librement mais peuvent être sujettes à la ségrégation lors des manipulations. L'analyse granulométrique complète devrait inclure non seulement la taille moyenne des particules, mais également la distribution (étendue et forme de la courbe granulométrique). Une distribution étroite ou bimodale peut influencer significativement les propriétés d'écoulement et la compaction du produit.
Densité apparente et tassée : La densité des poudres impacte directement la capacité des conteneurs IBC. Une poudre de faible densité nécessitera un conteneur de volume supérieur pour une même masse de produit. La connaissance du rapport entre la densité tassée et la densité apparente (indice d'Hausner) permet d'évaluer la compressibilité de la poudre et d'anticiper les problèmes potentiels de tassement durant le transport.
Comportement rhéologique : Les propriétés d'écoulement déterminent la facilité avec laquelle la poudre s'écoulera lors de la vidange du conteneur. Les poudres peuvent être classées selon leur capacité d'écoulement :
- Poudres à écoulement libre : faciles à manipuler, nécessitent peu d'assistance
- Poudres cohésives : peuvent former des agglomérats et nécessiter des systèmes d'aide à l'écoulement
- Poudres très cohésives : exigent des solutions spécifiques comme la fluidisation, la vibration ou même l'agitation mécanique
Des tests spécifiques comme la mesure de l'angle de repos, l'indice de Carr ou l'utilisation de cellules de cisaillement permettent d'évaluer précisément ces caractéristiques.
Sensibilité à l'humidité et hygroscopicité : Les poudres hygroscopiques absorbent l'humidité de l'air ambiant, ce qui peut altérer leurs propriétés physiques et chimiques. Pour ces produits, des conteneurs IBC parfaitement étanches ou équipés de systèmes de déshumidification sont indispensables. La sensibilité à l'humidité peut également déterminer le choix des matériaux de construction et des joints d'étanchéité.
Propriétés électrostatiques : Certaines poudres, particulièrement les organiques et les polymères, peuvent générer des charges électrostatiques importantes lors des manipulations. Ces charges présentent non seulement un risque d'explosion dans certains environnements, mais peuvent également affecter l'écoulement du produit. Des conteneurs avec mise à la terre ou construits en matériaux dissipatifs peuvent être nécessaires pour ces applications.
Abrasivité et corrosivité : Les poudres abrasives peuvent endommager progressivement les surfaces internes des conteneurs, particulièrement au niveau des vannes et des orifices de vidange. Pour ces produits, des matériaux résistants à l'abrasion ou des revêtements spécifiques sont recommandés. De même, les produits corrosifs nécessitent des matériaux adaptés comme l'acier inoxydable 316L ou des revêtements protecteurs.
2.2. Volume et cadence de production
Une évaluation précise des volumes de production et des cadences de travail est essentielle pour dimensionner correctement votre parc de conteneurs IBC et les équipements associés. Cette analyse doit prendre en compte non seulement la situation actuelle mais également les projections futures de croissance.
Analyse des flux de production : La cartographie détaillée de vos flux de production permet d'identifier les points critiques où l'utilisation de conteneurs IBC apportera le plus de valeur. Cette analyse doit considérer :
- Les volumes quotidiens, hebdomadaires et mensuels de poudres manipulées
- Les variations saisonnières et les pics de production
- Le nombre de références et la fréquence des changements de produits
- Les temps de séjour des produits dans le process de fabrication
Dimensionnement du parc de conteneurs : Le nombre de conteneurs nécessaires dépend de plusieurs facteurs interdépendants :
- Le volume total de produit en circulation
- Le temps de cycle complet (remplissage, transport, stockage, vidange, nettoyage)
- Les temps d'attente entre les différentes étapes du processus
- Le nombre de références différentes manipulées
Un calcul précis de ces paramètres permet d'optimiser l'investissement initial tout en garantissant une disponibilité suffisante des conteneurs.
Modularité et évolutivité : Pour les entreprises dont les volumes de production sont variables ou en croissance, des solutions modulaires sont particulièrement adaptées. L'acquisition progressive de conteneurs IBC permet d'étaler l'investissement tout en s'adaptant à l'évolution des besoins. Une approche modulaire peut également concerner les équipements de remplissage et de vidange, avec des stations évolutives pouvant traiter un nombre croissant de conteneurs parallèlement.
Gestion des flux physiques et informationnels : L'optimisation des flux physiques de conteneurs doit s'accompagner d'une gestion informatisée performante. Des systèmes de suivi en temps réel permettent de localiser chaque conteneur, de connaître son contenu et son statut (plein, vide, en cours de nettoyage). Ces outils de gestion facilitent la planification de la production et minimisent les risques de rupture d'approvisionnement des lignes. Ils contribuent également à la traçabilité complète des lots, exigence fondamentale dans les industries réglementées.
Optimisation des temps de changement : L'utilisation de conteneurs IBC réduit considérablement les temps de changement entre deux productions. Pour maximiser ce bénéfice, il est recommandé d'adopter des techniques inspirées du SMED (Single Minute Exchange of Die) en préparant à l'avance les conteneurs nécessaires pour la production suivante.
2.3. Contraintes réglementaires et normatives
Les industries manipulant des poudres sont soumises à des cadres réglementaires stricts qui varient selon les secteurs d'activité et les zones géographiques. La transition vers des conteneurs IBC doit intégrer ces exigences dès la phase de conception du projet.
Normes sanitaires et alimentaires : Dans l'industrie agroalimentaire, les matériaux en contact avec les denrées alimentaires doivent respecter des règlements spécifiques comme le règlement européen (CE) n°1935/2004 ou les normes FDA aux États-Unis. Les conteneurs destinés à cette industrie doivent être construits avec des matériaux approuvés pour le contact alimentaire et conçus pour permettre un nettoyage et une désinfection efficaces. Les fabricants doivent fournir des "déclarations de conformité" attestant que leurs conteneurs respectent ces exigences. La mise en place d'un système HACCP (Hazard Analysis Critical Control Point) peut également nécessiter des adaptations spécifiques des conteneurs et des équipements associés.
Exigences pharmaceutiques et BPF/GMP : L'industrie pharmaceutique est régie par les Bonnes Pratiques de Fabrication (BPF) ou Good Manufacturing Practices (GMP). Ces référentiels imposent des standards élevés en matière de traçabilité, de nettoyage et de validation des équipements. Les conteneurs IBC utilisés dans ce secteur doivent généralement présenter:
- Des surfaces polies (finition Ra ≤ 0,8 μm pour les surfaces en contact avec le produit)
- Des raccords sanitaires conformes aux standards (Tri-Clamp, BFM...)
- Une documentation complète incluant certificats matière, tests d'intégrité, qualification des équipements
La validation du nettoyage des conteneurs est particulièrement critique et peut nécessiter la mise en place de procédures spécifiques et de tests analytiques pour démontrer l'absence de résidus entre deux productions.
Sécurité et environnement ATEX : La manipulation de poudres combustibles ou explosives impose le respect de la directive ATEX (ATmosphères EXplosibles). Cette réglementation européenne, et ses équivalents internationaux, définit les mesures à prendre pour prévenir les explosions dans les zones à risque. Pour les applications concernées, les conteneurs IBC doivent être équipés de systèmes de mise à la terre efficaces et certifiés. Certains composants électriques (capteurs, systèmes de pesage) doivent être conçus pour fonctionner en toute sécurité dans ces environnements.
Traçabilité et intégrité des données : Les industries réglementées exigent une traçabilité complète des matières premières et des produits finis. Les conteneurs IBC peuvent être équipés de systèmes d'identification permanents (plaques gravées, tags RFID) permettant de suivre leur historique et leur contenu. Dans l'industrie pharmaceutique, l'intégrité des données est également cruciale. Les systèmes informatisés associés à la gestion des conteneurs IBC doivent respecter les principes de la partie 11 du titre 21 du Code of Federal Regulations (21 CFR Part 11) ou de l'Annexe 11 des BPF européennes.
Normes de transport et logistique : Les conteneurs IBC destinés au transport externe doivent respecter des normes internationales comme la certification UN/ADR pour le transport de matières dangereuses. Leurs dimensions doivent être compatibles avec les standards logistiques (palettes, racks de stockage, camions) pour faciliter leur manipulation tout au long de la chaîne d'approvisionnement.
3. Dimensionnement des équipements et intégration des conteneurs IBC
3.1. Choix des conteneurs adaptés
La sélection du type de conteneur IBC le plus approprié constitue une étape déterminante dans la réussite de votre transition. Ce choix doit prendre en compte de multiples paramètres techniques, opérationnels et économiques.
Matériaux de construction : Le choix du matériau dépend principalement de la nature des produits manipulés et des contraintes d'utilisation :
Acier inoxydable (304L, 316L)
Avantages : Durabilité exceptionnelle, résistance chimique élevée, facilité de nettoyage, compatibilité avec les environnements stériles
Applications : Industrie pharmaceutique, chimie fine, agroalimentaire haut de gamme
Considérations : Le 316L offre une meilleure résistance à la corrosion que le 304L et est préférable pour les produits corrosifs ou les environnements salins
Plastique alimentaire (PE-HD, PP)
Avantages : Coût réduit, légèreté, résistance aux acides et bases
Applications : Agroalimentaire standard, chimie non critique
Considérations : Durée de vie plus limitée, sensibilité aux chocs et aux températures élevées
Conteneurs composites
Avantages : Bon compromis entre coût et performance, légèreté
Applications : Produits non critiques, transports fréquents
Considérations : Recyclabilité parfois complexe, durabilité intermédiaire
Géométrie et dimensions : Les conteneurs IBC sont disponibles dans une variété de formats, généralement adaptés aux standards logistiques internationaux :
Conteneurs cubiques/rectangulaires
Avantages : Optimisation de l'espace de stockage, stabilité
Considérations : Peuvent présenter des zones mortes dans les angles
Conteneurs coniques
Avantages : Vidange facilitée, réduction des résidus
Considérations : Occupation d'espace moins optimale en stockage
Les dimensions standard les plus courantes sont basées sur des footprints de palettes (1200x800 mm, 1200x1000 mm) avec des hauteurs variables selon les capacités.
Capacités volumiques : Le choix de la capacité doit tenir compte des volumes de production, de la densité des produits et des contraintes de manutention :
500 litres : Adapté aux productions de petites séries ou aux produits à haute valeur ajoutée
1000 litres : Format standard offrant un bon compromis entre capacité et maniabilité
1500-2000 litres : Pour les productions à volume important, nécessitant des équipements de manutention adaptés
Caractéristiques spécifiques : En fonction des applications, des fonctionnalités supplémentaires peuvent être nécessaires :
Systèmes de vibration/fluidisation intégrés
Avantages : Amélioration de l'écoulement pour les produits cohésifs
Applications : Poudres fines, produits sensibles au tassement
Double enveloppe chauffante/refroidissante
Avantages : Maintien de la température du produit, prévention de la condensation
Applications : Produits sensibles à la température, cires, graisses
Isolation thermique
Avantages : Protection contre les variations de température extérieure
Applications : Produits thermosensibles, environnements à température non contrôlée
Systèmes de fermeture et d'étanchéité : La qualité du système de fermeture est cruciale pour garantir l'étanchéité et faciliter les opérations :
Couvercles à brides boulonnées
Avantages : Étanchéité maximale, résistance à la pression
Considérations : Temps d'ouverture/fermeture plus long
Systèmes à serrage rapide
Avantages : Facilité d'utilisation, gain de temps
Considérations : Nécessite un entretien régulier des joints
Vannes de fond
Plusieurs technologies existent (papillon, boule, guillotine) avec des caractéristiques spécifiques en termes d'étanchéité, de nettoyabilité et de résistance à l'abrasion. Le diamètre de vanne influence directement le débit de vidange et doit être adapté aux besoins du process.
3.2. Stations de remplissage et de vidange
L'intégration efficace des conteneurs IBC dans votre processus de production nécessite des stations de remplissage et de vidange spécifiquement conçues pour optimiser les flux de matière tout en garantissant la sécurité et l'hygiène des opérations.
Stations de remplissage : Le remplissage des conteneurs IBC doit être conçu pour préserver l'intégrité du produit tout en assurant une opération rapide et précise :
Systèmes de dosage
Doseurs volumétriques : pour les applications nécessitant une précision moyenne et un débit élevé
Doseurs pondéraux : pour les applications exigeant une grande précision de dosage
Systèmes combinés : alliant rapidité et précision pour les grandes capacités
Confinement et gestion des poussières
Manchettes d'étanchéité gonflables pour créer une liaison étanche
Systèmes d'aspiration localisée pour capturer les émissions de poussières
Cabines fermées avec filtration pour les produits hautement actifs ou toxiques
Compactage et densification
Vibrateurs pour optimiser le remplissage et réduire le volume occupé
Tables de compactage pour les produits sensibles au tassement
Systèmes de désaération pour évacuer l'air emprisonné
Stations de vidange : La vidange représente souvent le point critique dans la manipulation des poudres. L'IBCFlow®02 constitue une solution avancée pour cette étape :
Principes de fonctionnement
Connection étanche à la vanne du conteneur
Systèmes d'assistance à l'écoulement intégrés
Contrôle précis du débit de vidange
Minimisation des émissions de poussières
Niveaux de confinement
Confinement ouvert : pour les produits non dangereux avec système d'aspiration
Confinement fermé : pour les produits sensibles ou actifs avec transfert sous vide/pression
Confinement total : pour produits hautement actifs/toxiques avec circuit fermé et barrières multiples
Intégration dans le process
Vidange directe dans mélangeurs ou réacteurs
Alimentation de lignes de conditionnement
Interface avec systèmes de transport pneumatique ou mécanique
Pesage et contrôle : La précision du pesage est souvent cruciale :
Technologies de pesage
Cellules de charge sous pieds (standard)
Pesage suspendu (précision accrue)
Systèmes à double gamme (capacité et précision)
Contrôle informatisé
Gestion des recettes et des lots
Enregistrement des données de pesage
Interface avec MES, ERP
Nettoyage et décontamination : Le nettoyage des stations est aussi important que celui des conteneurs :
Nettoyage en Place (NEP/CIP)
Buses rotatives (remplissage)
Circuits fermés (vannes, connexions)
Séquences automatisées (lavage, rinçage, séchage)
Matériaux et conception
Surfaces polies sans angle mort
Pentes d'écoulement optimisées
Accès facilité pour la maintenance
3.3. Automatisation et convoyage
L'automatisation du flux de conteneurs IBC constitue une étape clé vers l'optimisation globale de votre production. Elle permet non seulement de réduire les interventions manuelles mais également d'améliorer la traçabilité et la fiabilité des opérations.
Systèmes de convoyage : Le choix dépend de la configuration, des contraintes et du niveau d'automatisation :
Convoyeurs à rouleaux
Avantages : Simplicité, robustesse, maintenance réduite
Applications : Transferts horizontaux, accumulation
Variantes : Rouleaux libres (gravitaires) ou motorisés
Convoyeurs à chaînes
Avantages : Polyvalence, franchissement de dénivelés
Applications : Circuits complexes, changements de direction
Considérations : Entretien plus fréquent
Navettes automatisées (AGV/AMR)
Avantages : Flexibilité maximale, adaptation dynamique
Applications : Environnements changeants, connexion entre zones distantes
Considérations : Investissement plus important, infrastructure IT
Systèmes de positionnement : La précision est essentielle pour les opérations automatisées :
Butées mécaniques et guides
Avantages : Fiabilité, simplicité
Applications : Positionnement grossier, arrêt
Systèmes de centrage actifs
Avantages : Précision élevée, compensation des tolérances
Applications : Connexion automatique aux stations
Capteurs et contrôles
Détection de présence et d'identité
Vérification du positionnement correct
Sécurités anti-collision et anti-écrasement
Identification et traçabilité : Élément clé pour garantir la traçabilité et éviter les erreurs :
Technologies d'identification
Codes-barres (économique)
Tags RFID (sans contact, stockage d'info)
QR codes (info dense, omnidirectionnel)
Informations tracées
Identifiant unique du conteneur
Contenu (produit, lot, quantité)
Historique (remplissage, stockage, nettoyage)
Statut et destination
Supervision et pilotage : Un système centralisé permet une gestion optimale :
Fonctionnalités essentielles
Visualisation temps réel (état, position)
Gestion des ordres de transfert et priorités
Enregistrement des mouvements et opérations
Gestion des alarmes et anomalies
Intégration avec systèmes existants
Interface avec MES
Communication avec automates de process
Connexion aux systèmes qualité/traçabilité
Sécurité des opérations : L'automatisation doit intégrer tous les aspects de sécurité :
Dispositifs de protection
Barrières physiques et zones sécurisées
Détecteurs de présence et scrutateurs laser
Arrêts d'urgence et redémarrage sécurisé
Modes dégradés et procédures d'urgence
Possibilité d'intervention manuelle
Procédures de récupération après incident
Redondance des systèmes critiques
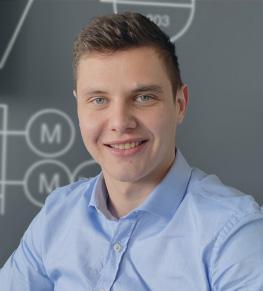
Vous avez un projet ?
Je suis disponible pour vous conseiller et vous accompagner dans votre étude.
Loïc, expert en solutions modulaires de transfert de poudres
4. Contraintes et solutions liées à la vidange des conteneurs IBC
4.1. Caractéristiques des produits influençant la vidange
La vidange efficace des conteneurs IBC est directement influencée par les propriétés physiques des poudres. Une compréhension approfondie de ces caractéristiques permet d'anticiper les difficultés potentielles et de mettre en place les solutions adaptées.
Coulabilité et cohésion : La capacité d'une poudre à s'écouler librement est déterminante :
Classification selon la coulabilité
Poudres à écoulement libre (angle de repos < 30°) : vidange facile et régulière
Poudres à écoulement moyen (angle de repos 30-45°) : peuvent nécessiter une assistance légère
Poudres cohésives (angle de repos > 45°) : nécessitent des dispositifs d'aide
4.2. Solutions techniques pour une vidange efficace
Différents systèmes existent pour optimiser la vidange des conteneurs IBC. Les aides à l’écoulement, comme les plaques vibrantes ou les fluidisateurs d’air, empêchent la formation de voûtes et facilitent le flux du produit. Pour les poudres sensibles à l’humidité, une vidange sous atmosphère contrôlée est recommandée.
4.3. Cas particulier des produits sensibles
Les poudres réactives ou fortement hygroscopiques nécessitent une attention particulière. Un stockage hermétique empêche l’absorption d’humidité. La vidange doit se faire dans un environnement confiné pour éviter toute contamination. Des systèmes de nettoyage en place (CIP) garantissent une hygiène irréprochable entre chaque lot de production.
5. FAQ : Réponses aux questions courantes sur la transition vers les conteneurs IBC
5.1. Quels sont les principaux avantages des conteneurs IBC par rapport aux big bags ?
- Réduction des contaminations croisées
- Intégration facilitée dans des lignes automatisées
- Moins de manutention et d’interventions humaines
- Vidange plus propre et mieux maîtrisée
5.2. Comment assurer une vidange complète des conteneurs IBC ?
L’utilisation de stations de vidange adaptées, comme l’IBCFlow®02, garantit une extraction totale du produit sans perte ni résidu.
5.3. Les conteneurs IBC sont-ils adaptés à tous les types de poudres ?
Oui, à condition de choisir le bon modèle et les bons accessoires : vannes, revêtements internes, aides à l’écoulement.
5.4. Quelle est la durée de vie d’un conteneur IBC ?
Un conteneur IBC bien entretenu peut durer plusieurs dizaines années, réduisant ainsi les coûts d’exploitation.
5.5. Est-il possible d’intégrer les conteneurs IBC dans une ligne de production existante ?
Oui, ils peuvent être intégrés progressivement pour remplacer les big bags et améliorer l’efficacité du process.
Conclusion
Adopter les conteneurs IBC, c’est opter pour une production plus propre, plus flexible et plus automatisée. Cette transition permet d’optimiser la traçabilité, de réduire la contamination et d’améliorer la gestion des poudres.
📞 Vous travaillez dans le traitement ou la valorisation de terres rares ?
Contactez nos experts pour concevoir ensemble une ligne de production sur-mesure, performante et sécurisée.