Container emptying: How can I ensure that my IBCs are disposed of cleanly and simply ?
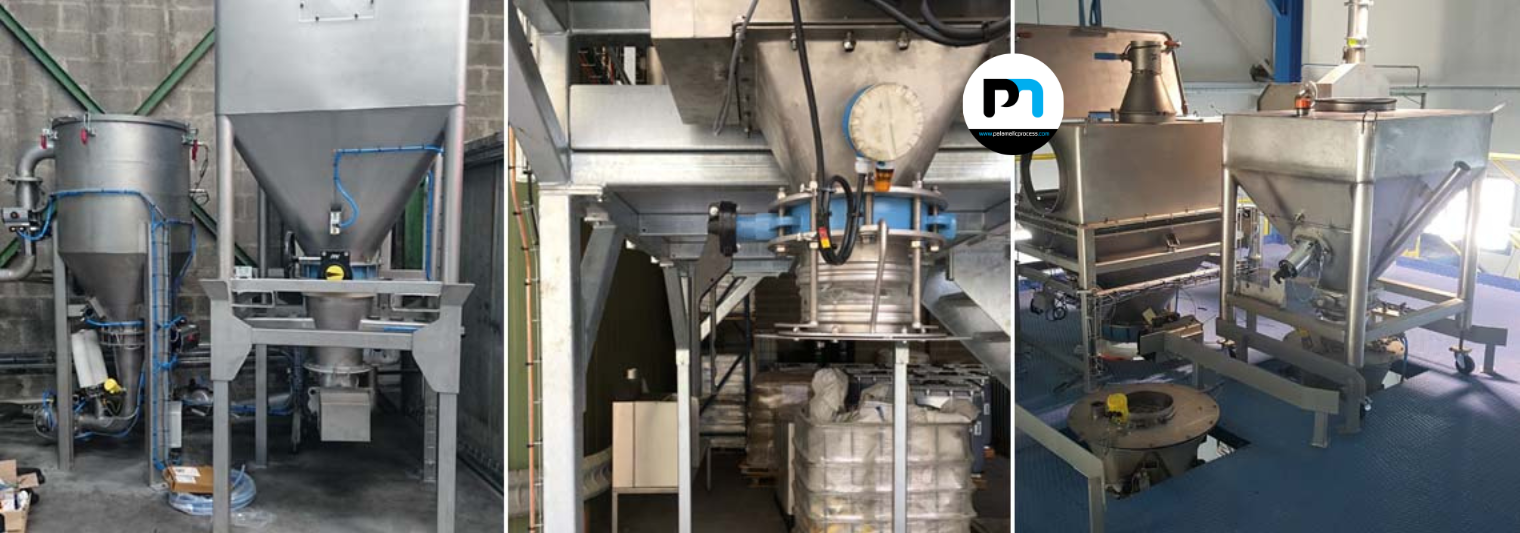
- 1. Why choose an IBC container for easy control of the dosage of powdered ingredients ?
- 2. The characteristics of powders influencing the emptying of an IBC container
- 3. Best practices for optimising the emptying of an IBC container
- 4. FAQ: Answers to frequently asked questions about the emptying of IBC containers
- 5. Conclusion
Emptying IBC containers is a technical stage in many industrial sectors such as the food industry, chemicals and pharmaceuticals. Unlike big bags or drums, IBC containers offer a more precise, clean and ergonomic solution for the extraction of powders and granules.
However, to guarantee a smooth flow without product loss, certain good practices must be implemented.
Why is simply emptying an IBC container a preferred solution to fully automatic solutions?
What are the factors influencing the emptying of the product?
How can blockages be avoided and extraction without residue ensured?
This article explores the different emptying methods, the challenges encountered and the solutions that enable fast, simple, safe and contained emptying.
1. Why choose an IBC container for easy control of the dosage of powdered ingredients ?
Precise and controlled dosing
One of the main advantages of the IBC container is its discharge unit, which can also act as a dosing system.
By integrating double butterfly valves or precise guillotine valves, it becomes possible to take exactly the necessary quantity of product and to stop the flow without risk of waste or contamination.
This makes it very easy to change products with a single container emptying station.
Better management of dust emissions
Unlike big bags, which can be emptied imprecisely and generate particle emissions, the IBC container is designed to considerably limit the dispersion of powders into the atmosphere.
Thanks to its rigid structure and the available sealed connection systems, it ensures cleaner extraction.
The use of hermetic valves reduces operator exposure and guarantees a safer working environment that complies with health standards.
An investment that quickly pays for itself
Although the initial cost of an IBC container is higher than a big bag, it pays for itself quickly thanks to simplified emptying installation and maintenance.
The required emptying station is much more compact, as it requires neither a hoist nor a high structure.
In addition, solutions such as IBCFlow01 allow for fast and efficient emptying with less infrastructure and manpower.
The result: savings in the long term, better productivity and greater reliability of the industrial process.
Increased flexibility for product changeover
The IBC container also facilitates the change of raw material, unlike big bags which require complex handling or even investment in several emptying stations.
Thanks to its easy-to-install container system, it allows for a quick changeover from one product to another without the risk of cross-contamination.
This flexibility is a major asset for industries handling several powder references in the same process.
2. The characteristics of powders influencing the emptying of an IBC container
A station suitable for fluid and easy-to-drain products
When a powder or granule has a good fluidity naturally, without generating excessive dust or presenting specific hazards, a simple draining station is generally sufficient.
These stations allow the valve to be opened and the product to drain by gravity, without the need for additional equipment.
They are ideal for applications where the flow rate must be constant and where there is no risk of the product clogging up or sticking to the walls.
Flow aids for difficult powders
If the material tends to clump together, clog up or form arches, it is essential to incorporate flow aids.
A vibrating emptying station can be used and is often the most suitable solution to facilitate the movement of the product and avoid blockages.
Airtight solutions for fine and very dusty powders
Some fine powders are extremely volatile and can generate significant dust emissions during emptying.
For these applications, it is essential to opt for semi-automatic dispensing stations with a sealing system.
These stations are generally equipped with tulip seals or hermetic connection systems to limit the dispersion of particles and guarantee a cleaner and safer working environment.
Confined and automated stations for hazardous products and high flow rates
When the product being handled is hazardous, toxic or flammable, or when very large volumes are being processed, it is advisable to invest in automated and contained drain stations.
This equipment incorporates precise control systems, advanced safety devices and sealed connections to ensure risk-free handling for operators.
This type of station is particularly suitable for the pharmaceutical, chemical and food processing industries that handle sensitive substances.
Depending on the characteristics of the product and the requirements of the process, it is therefore essential to choose a suitable emptying station that guarantees efficiency, cleanliness and safety.
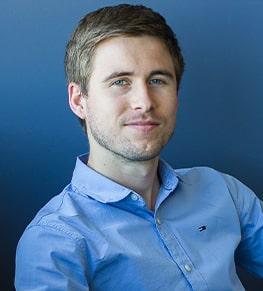
Do you have a project in mind ?
I am available to advise you and assist you in your research.
Guillaume, expert in IBC handling and hygienic powder discharge
3. Best practices for optimising the emptying of an IBC container
Acting on the container itself
The efficiency of the emptying process starts with the design of the IBC container.
An adapted inner coating can significantly improve the flow of powders.
Solutions such as polymiroir, teflon coating or ViwateQ® treatment reduce the adhesion of particles to the walls and facilitate the flow of material.
The angle of flow also plays a key role: for a free-flowing powder, an angle of 45° is sufficient, but for more sticky products or those prone to compaction, an angle of up to 60° is recommended to prevent the formation of arches and ensure optimal extraction.
Integrate flow aids into the container
For powders that are difficult to drain, it is possible to add support systems integrated directly into the container.
Among the effective solutions are pneumatic impactors, which create brief impulses to break up the arches, and vibrofluidisers, which inject air to fluidise the material and improve its movement towards the outlet.
Having a discharge station with flow assistance
Installing a suitable IBCFlow02 type discharge station can greatly improve the efficiency of the process.
A vibrating station is the most effective solution, as it vibrates the entire container, thus facilitating the descent of the product.
Alternatively, impactors installed on the station make it possible to act on the container without requiring any additional connection, thus simplifying installation and operation.
Acting on the powder itself
Moisture absorption is one of the main factors in powder clogging.
One of the major advantages of the IBC container is its perfect seal, which preserves the integrity of the powders and prevents them from clumping together due to ambient humidity.
The IBC container system also allows the powder to be completely inerted with a nitrogen sweep.
4. FAQ: Answers to frequently asked questions about the emptying of IBC containers
4.1 Why does my powder not flow properly from my container?
Several factors can cause powder to flow with difficulty. Excessive humidity encourages the particles to agglomerate, making it more difficult to empty the container. Too fine a particle size can also cause problems, as the particles accumulate and form arches inside the container. Finally, excessive compaction during transport or storage can block the natural flow of the product.
To overcome these difficulties, the integration of a vibrating system or fluidisation is recommended.
These devices promote the disintegration of the product and ensure a smooth and homogeneous flow.
4.2 How can dust emissions be avoided during emptying?
Dust dispersion during emptying can lead to product losses and pose safety risks for operators.
To minimise these emissions, it is advisable to use a tulip seal or an inflatable hermetic connection system between the IBC container and the emptying station.
These solutions limit the suspension of particles while guaranteeing a clean and safe transfer.
In addition, the integration of an active dust removal device can further improve the quality of the working environment.
4.3 What is the best equipment for clean and fast emptying?
The choice of equipment depends on the nature of the product to be emptied.
Gravity-fed systems are suitable for free-flowing powders and light granules that flow naturally.
On the other hand, for more compact products or those prone to clogging, the addition of mechanical assistance is recommended.
Solutions such as vibrating systems, fluidising plates or extraction screws ensure controlled flow and reduce product loss.
A good choice of equipment thus improves the speed and cleanliness of the process.
4.4 Can an IBC container be reused after emptying?
Yes, IBC containers are designed to be reused many times.
In the pharmaceutical and dairy industries, thorough cleaning must be carried out after each emptying.
An improperly maintained IBC can lead to cross-contamination between different products and alter the quality of the materials handled.
To guarantee optimal reuse, it is recommended to adopt a cleaning protocol adapted to the type of product stored.
Automated washing stations are available to ensure efficient and fast cleaning, thus reducing the risk of residues and contamination.
4.5 How can an IBC container be integrated into an automated process?
The integration of an IBC container into an automated process is based on several elements.
Level sensors allow real-time monitoring of the volume of product available and anticipate reloading needs.
Motorised valves and automatic dosing systems ensure precise control of the material flow.
Finally, a sealed connection with the other equipment in the production line guarantees a secure transfer without product loss.
These solutions make it possible to optimise the efficiency of the process while reducing manual interventions.
Conclusion
The simple emptying of IBC containers is an ideal solution for guaranteeing the efficient, clean and controlled discharge of powders and granules.
Thanks to an optimised design and adapted equipment, it is possible to avoid product losses, reduce dust emissions and improve productivity.
Whether for discharge by gravity, mechanical assistance or a contained solution, the best practices described in this article optimise the use of IBC containers and ensure smooth management of raw materials.
📩 Need a solution tailored to your process?
Contact us today to find out more about our equipment and our contained discharge solutions!