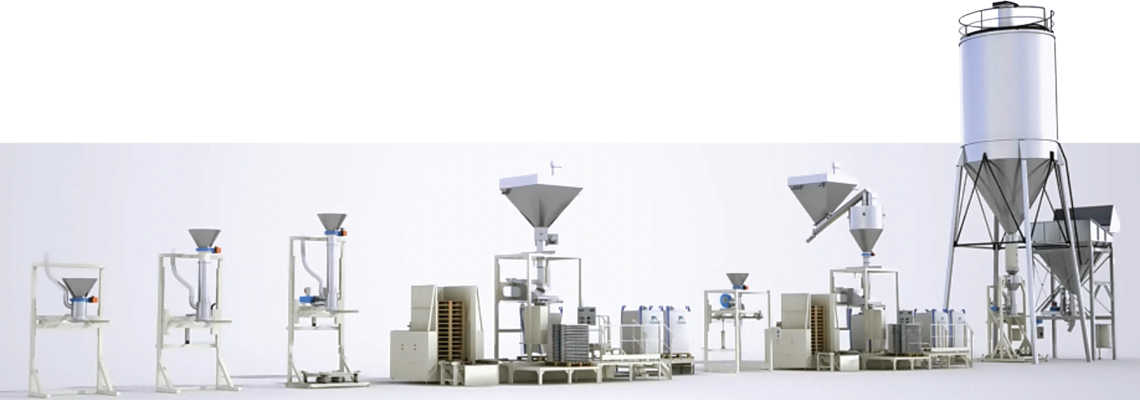
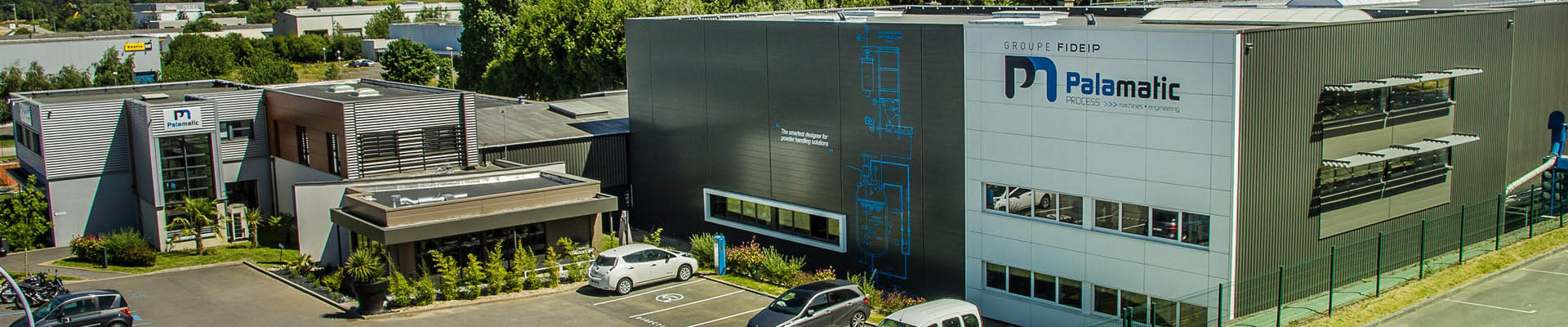
Palamatic Process has developed a range of big bag filling stations. The FlowMatic® range enables efficient handling of your powders.
Discover our turnkey solutions for bulk bag conditioning.
Bulk bag filling machines are designed to provide unmatched precision and reliability.
By choosing Palamatic Process big bag filling and handling solutions, you benefit from advanced technologies and customized solutions to optimize your production and ensure the quality of your products.
Flowmatic® 01 big bag filling station has a capacity of 10-20 bulk bags/hr. This filling equipment offers a cost-effective solution to filling your big bags and FIBC’s while ensuring total containment of your powders.
Flowmatic® 02 big bag filling system allows ergonomic handling of your big bags via pneumatic cylinder tensioning.
FlowMatic® 03 big bag filling equipment is equipped with load cells which allows for gross weighing and precise dosing operation. A pre-forming fan and vibrating base allow for optimal material packaging of your big bags and FIBC’s.
FlowMatic® 04 big bag filling station offers high efficiency (20-40 bulk bags/hr) and automation of your FIBC filling process. This series also offers the operator ease of use with features for handling the big bags and pallet unstacking.
FlowMatic® 05 big bag filling station offers 2 types of lifting solutions. The LT series incorporates a lifting table and the HC series uses a hydraulic cylinder. Both are designed to meet the hygienic requirements of the food and pharmaceutical industries. By incorporating load cells on the bag suspension system, the big bags can be kept off the floor while being packed. Inflatable seals and reverse air jet filters keep everything dust tight and contained for sanitary and safe working conditions.
FlowMatic® 06 big bag filler is designed to provide nearly full automation and high filling rates (30-60 big bags/hr) for any industrial process. This series is designed to handle continuous operation with minimal operator intervention via dosing, weighing and conveying.
Flowmatic® 07 big bag filling station is a mobile unit and is ideal for operations that require flexibility in loading methods. Examples include multiple silos, feeding points that require complete clean down and truck unloading operations.
Flowmatic® 08 big bag filling station allows telescopic loading of bulk materials with integrated commercial weighing system. Mainly used for single handle big bags and FIBC storage for the mining, agricultural and chemical fertilizer industries.
Flowmatic®09 big bag filling station offers a very high net weighing rate for big bags with only one handle. This series incorporates automated features and belt conveyor.
FlowMatic® 10 hygienic big bag packaging machine is adapted for clean rooms operations. This filling station is designed in 3 stages: clean room, sealed transitional room, and storage area. Pallet unstacker and belt conveyors further automate the process for minimal operator intervention.
Palamatic Process offers big bag filling solutions ranging from standard, manual equipment to fully automated processing lines. Our solutions are adapted for all sectors of activity: food and beverage, chemical, pharmaceutical, mining, agricultural, water and smoke treatment and nuclear.
Examples of processed powders: maltodextrin, dextrose, sugar, salt, spices, flour, alumina, carbonate, sulphate, titanium dioxide (TiO2), soy, starch, corn starch, wheat starch, calcium carbonate (CaCo3), sulphate, bone meal, iron oxide and hydroxide, dairy powders, caseinate, activated carbon, carbon black, powder pigments, etc.
Big bags, also known as intermediate flexible containers (FIBC), are versatile and robust packaging solutions, suitable for a wide range of products (bulk, food, chemicals, construction materials, etc.).
Big bags are particularly appreciated for their ability to transport large quantities of materials efficiently and securely. They are also easy to handle thanks to their lifting straps, making them an ideal solution for storing and transporting bulk products. In summary, big bags are a versatile and practical option for a multitude of products in various industrial sectors.
To choose a big bag filling station, it is important to consider the type of product to be packaged (powders, granules, liquids or others). The physical properties of the product, such as density, fluidity and sensitivity to humidity or heat are decisive.
The capacity and throughput of the filling station must correspond to the volumes of big bags used and production requirements. Filling accuracy is essential to avoid overloading or underloading. Integrated weighing systems ensure increased precision.
Automation enables increased efficiency by reducing filling time and downtime. Automated stations fill big bags faster than manual systems. Automation also contributes to cost reduction. By reducing the need for labor, businesses can realize cost savings. Increased accuracy and reduced human error minimize non-conforming batches, thereby increasing production yield.