Transitioning to flexible production: adopting IBC containers for efficient powder management
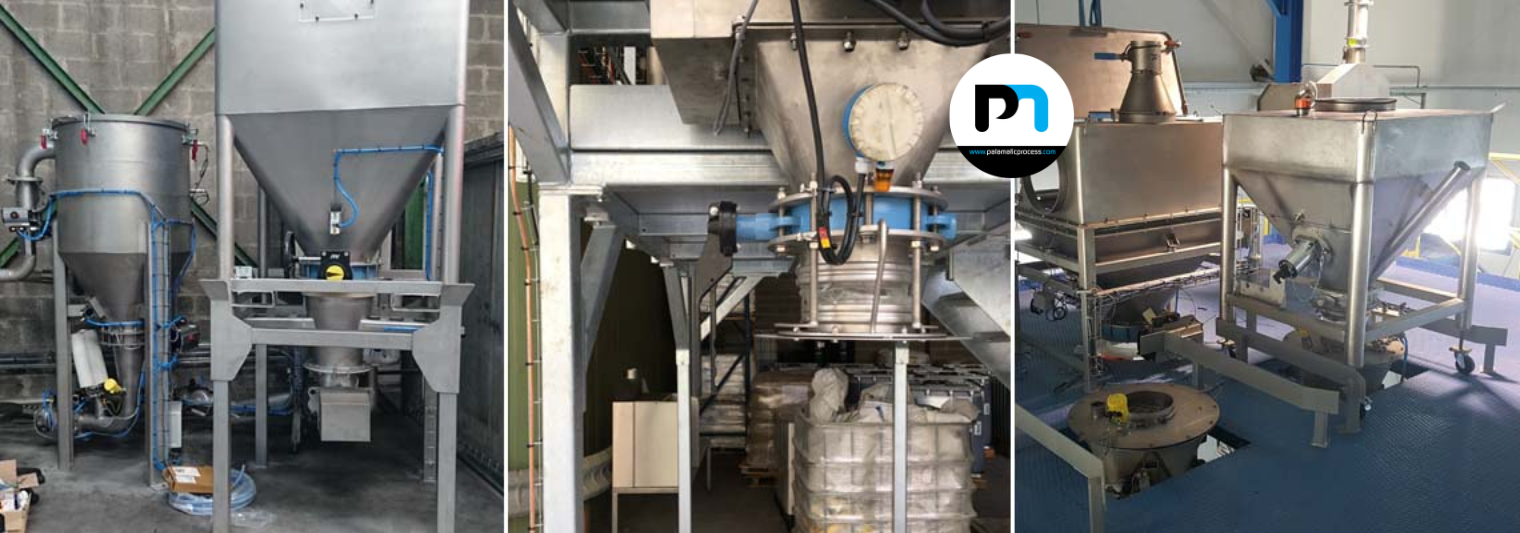
- 1. Why consider switching to IBC containers ?
- 2. Preliminary questions for a successful transition
- 3. Equipment sizing and integration of IBC containers
- 4. Constraints and solutions related to emptying IBC containers
- 5. FAQ: Answers to common questions about transitioning to IBC containers
- 6. Conclusion
The agri-food, pharmaceutical and cosmetics industries are moving towards cleaner and more automated production solutions.
The handling of powders in big bags and sacks poses a number of challenges, including repetitive handling, dust emissions and cross-contamination. Full IBC container solutions offer a reliable and flexible alternative.
They guarantee simplified handling, better traceability and easy integration into automated processes.
But how can this transition be successfully achieved? What criteria need to be considered?
How should equipment be sized and how can IBC container emptying be optimised? This article details the essential steps for adopting a more efficient and hygienic production process.
1. Why consider switching to IBC containers ?
1.1. Limitations of traditional methods
Traditional methods of powder handling, although still widely used, have major drawbacks that affect the productivity and quality of industrial operations.
Heavy handling and ergonomic risks: Handling big bags requires the use of specific equipment such as hoists or forklifts. These operations not only place a significant physical strain on operators, but also pose a significant risk of workplace accidents. Repetitive movements and awkward postures can lead to musculoskeletal disorders (MSDs), the leading cause of occupational illness in industry.
Longer batch changeover times: Switching from one production batch to another with traditional systems involves a lot of handling: removing empty bags or big bags, cleaning equipment, and setting up new containers. These operations can account for up to 20% of total production time, significantly reducing line productivity.
Cross-contamination and hygiene issues: Open systems promote dust emissions and the risk of contamination between different products. In sensitive industries such as pharmaceuticals and food processing, these issues can have serious consequences for the quality of the final product and consumer safety.
Environmental impact: The use of bags and, to a lesser extent, big bags generates a significant amount of waste. Paper and plastic bags are generally single-use, which runs counter to the sustainable development objectives that more and more companies are setting for themselves.
Limited traceability: Traditional systems offer reduced traceability of products throughout the production chain. Manual batch identification and multiple product transfers increase the risk of errors in the tracking of raw materials and finished products.
1.2. Advantages of IBC containers
IBC containers are a modern and efficient alternative that directly addresses the limitations of traditional methods while providing additional benefits.
Airtight and hygienic: The closed design of IBC containers prevents dust emissions and protects the product from external contamination. Stainless steel models offer smooth surfaces that are easy to clean and disinfect, meeting the strictest hygiene standards in the pharmaceutical and food industries.
Easy handling and ergonomics: Designed to be easily moved using pallet trucks or automated systems, IBC containers significantly reduce physical effort for operators. Their standardised shape and optimised dimensions facilitate storage and handling, improving working conditions and safety.
Integration into automated lines: IBC containers are perfectly suited to automation. They can be equipped with identification systems (RFID, barcodes) for real-time tracking. This compatibility with Industry 4.0 technologies offers new opportunities in terms of production management and flow optimisation.
Controlled and safe emptying: Specific emptying systems such as the IBCFlow®02 allow controlled unloading of powders, limiting emissions and ensuring complete product transfer. Advanced technologies such as butterfly valves or double-flap systems ensure perfect sealing during all handling phases.
Reduced downtime: The use of IBC containers optimises batch changes and reduces cleaning times. An empty container can be immediately replaced with a full one, ensuring production continuity. This operational flexibility translates into a significant increase in equipment utilisation rates.
Durability and return on investment: Built to last, stainless steel IBC containers can be used for several decades with minimal maintenance. Although the initial investment is higher than for big bag solutions, the payback is quick thanks to savings on consumables and improved productivity.
Optimised traceability: Each container can be individually identified, enabling accurate batch tracking throughout the manufacturing process. This enhanced traceability facilitates product recall management and compliance with increasingly stringent regulatory requirements.
2. Preliminary questions for a successful transition
2.1. Nature of the products handled
The success of a transition to the use of IBC containers depends largely on a thorough analysis of the characteristics of the powders handled. These properties will determine not only the type of container to be used, but also the auxiliary equipment required for optimal management.
Particle size and distribution: Particle size directly influences the flow behaviour of powders. Products with a fine particle size (less than 100 microns) generally have greater cohesion and may require flow aids. Conversely, powders with a coarser particle size flow more freely but may be prone to segregation during handling. A complete particle size analysis should include not only the average particle size, but also the distribution (range and shape of the particle size curve). A narrow or bimodal distribution can significantly influence the flow properties and compaction of the product.
Apparent and bulk density: The density of powders directly impacts the capacity of IBC containers. A low-density powder will require a larger container for the same mass of product. Knowing the ratio between bulk density and apparent density (Hausner index) makes it possible to assess the compressibility of the powder and anticipate potential settling problems during transport.
Rheological behaviour: The flow properties determine how easily the powder will flow when the container is emptied. Powders can be classified according to their flowability:
- Free-flowing powders: easy to handle, require little assistance
- Cohesive powders: may form agglomerates and require flow aids
- Highly cohesive powders: require specific solutions such as fluidisation, vibration or even mechanical agitation
Specific tests such as measuring the angle of repose, the Carr index or using shear cells allow these characteristics to be accurately assessed.
Moisture sensitivity and hygroscopicity: Hygroscopic powders absorb moisture from the ambient air, which can alter their physical and chemical properties. For these products, perfectly leak-proof IBC containers or containers equipped with dehumidification systems are essential. Sensitivity to moisture can also determine the choice of construction materials and seals.
Electrostatic properties: Some powders, particularly organic and polymer powders, can generate significant electrostatic charges during handling. These charges not only pose an explosion hazard in certain environments, but can also affect product flow. Containers with grounding or made of dissipative materials may be necessary for these applications.
Abrasiveness and corrosiveness: Abrasive powders can gradually damage the internal surfaces of containers, particularly at valves and discharge openings. For these products, abrasion-resistant materials or specific coatings are recommended. Similarly, corrosive products require suitable materials such as 316L stainless steel or protective coatings.
2.2. Production volume and rate
An accurate assessment of production volumes and work rates is essential for correctly sizing your IBC container fleet and associated equipment. This analysis must take into account not only the current situation but also future growth projections.
Production flow analysis: Detailed mapping of your production flows allows you to identify critical points where the use of IBC containers will add the most value. This analysis should consider:
- Daily, weekly and monthly volumes of powder handled
- Seasonal variations and production peaks
- The number of references and frequency of product changes
- The dwell time of products in the manufacturing process
Sizing the container fleet: The number of containers required depends on several interdependent factors:
- The total volume of product in circulation
- The complete cycle time (filling, transport, storage, emptying, cleaning)
- The waiting times between the different stages of the process
- The number of different references handled
A precise calculation of these parameters allows you to optimise the initial investment while ensuring sufficient container availability.
Modularity and scalability: For companies with variable or growing production volumes, modular solutions are particularly suitable. The gradual acquisition of IBC containers allows the investment to be spread out while adapting to changing needs. A modular approach can also be applied to filling and emptying equipment, with scalable stations that can handle an increasing number of containers in parallel.
Physical and information flow management: Optimising the physical flow of containers must be accompanied by efficient computerised management. Real-time tracking systems make it possible to locate each container and know its contents and status (full, empty, being cleaned). These management tools facilitate production planning and minimise the risk of supply disruptions on production lines. They also contribute to full batch traceability, a fundamental requirement in regulated industries.
Optimisation of changeover times: The use of IBC containers significantly reduces changeover times between two production runs. To maximise this benefit, it is recommended to adopt techniques inspired by SMED (Single Minute Exchange of Die) by preparing the containers required for the next production run in advance.
2.3. Regulatory and normative constraints
Industries that handle powders are subject to strict regulatory frameworks that vary according to sector and geographical area. The transition to IBC containers must incorporate these requirements from the project design phase.
Health and food standards: In the food industry, materials that come into contact with food must comply with specific regulations such as European Regulation (EC) No. 1935/2004 or FDA standards in the United States. Containers intended for this industry must be constructed from materials approved for food contact and designed to allow effective cleaning and disinfection. Manufacturers must provide ‘declarations of conformity’ certifying that their containers meet these requirements. The implementation of a Hazard Analysis Critical Control Point (HACCP) system may also require specific adaptations to containers and associated equipment.
Pharmaceutical requirements and GMP/GMP: The pharmaceutical industry is governed by Good Manufacturing Practices (GMP). These standards impose high standards for traceability, cleaning and equipment validation. IBC containers used in this sector must generally have:
- Polished surfaces (finish Ra ≤ 0.8 μm for surfaces in contact with the product)
- Sanitary fittings that comply with standards (Tri-Clamp, BFM, etc.)
- Complete documentation including material certificates, integrity tests and equipment qualification
Validation of container cleaning is particularly critical and may require specific procedures and analytical tests to demonstrate the absence of residues between two production runs.
Safety and environment ATEX: The handling of combustible or explosive powders requires compliance with the ATEX directive (ATmosphères EXplosibles). This European regulation, and its international equivalents, defines the measures to be taken to prevent explosions in hazardous areas. For the applications concerned, IBC containers must be equipped with effective and certified earthing systems. Certain electrical components (sensors, weighing systems) must be designed to operate safely in these environments.
Traceability and data integrity: Regulated industries require full traceability of raw materials and finished products. IBC containers can be equipped with permanent identification systems (engraved plates, RFID tags) to track their history and contents. In the pharmaceutical industry, data integrity is also crucial. Computerised systems associated with IBC container management must comply with the principles of Part 11 of Title 21 of the Code of Federal Regulations (21 CFR Part 11) or Annex 11 of the European GMP.
Transport and logistics standards: IBCs intended for external transport must comply with international standards such as UN/ADR certification for the transport of hazardous materials. Their dimensions must be compatible with logistics standards (pallets, storage racks, trucks) to facilitate handling throughout the supply chain.
3. Equipment sizing and integration of IBC containers
3.1. Choosing the right containers
Selecting the most appropriate type of IBC container is a crucial step in the success of your transition. This choice must take into account a number of technical, operational and economic parameters.
Construction materials: The choice of material depends mainly on the nature of the products handled and the constraints of use:
Stainless steel (304L, 316L)
Advantages: Exceptional durability, high chemical resistance, easy to clean, compatible with sterile environments
Applications: Pharmaceutical industry, fine chemicals, high-end food processing
Considerations: 316L offers better corrosion resistance than 304L and is preferable for corrosive products or saline environments
Food-grade plastic (PE-HD, PP)
Advantages: Low cost, lightweight, resistant to acids and bases
Applications: Standard food processing, non-critical chemicals
Considerations: More limited service life, sensitivity to impact and high temperatures
Composite containers
Advantages: Good compromise between cost and performance, lightweight
Applications: Non-critical products, frequent transport
Considerations: Recyclability can sometimes be complex, moderate durability
Geometry and dimensions: IBC containers are available in a variety of formats, generally adapted to international logistics standards:
Cubic/rectangular containers
Advantages: Optimised storage space, stability
Considerations: May have dead zones in the corners
Conical containers
Advantages: Easy emptying, reduced residues
Considerations: Less optimal space utilisation in storage
The most common standard dimensions are based on pallet footprints (1200x800 mm, 1200x1000 mm) with variable heights depending on capacity.
Volume capacities: The choice of capacity must take into account production volumes, product density and handling constraints:
500 litres: Suitable for small production runs or high value-added products
1000 litres: Standard format offering a good compromise between capacity and manoeuvrability
1500-2000 litres: For high-volume production requiring suitable handling equipment
Specific features: Depending on the application, additional features may be required:
Integrated vibration/fluidisation systems
Advantages: Improved flow for cohesive products
Applications: Fine powders, products sensitive to settling
Double heating/cooling jacket
Advantages: Maintains product temperature, prevents condensation
Applications: Temperature-sensitive products, waxes, greases
Thermal insulation
Advantages: Protection against external temperature variations
Applications: Heat-sensitive products, uncontrolled temperature environments
Closure and sealing systems: The quality of the closure system is crucial to ensure tightness and facilitate operations:
Bolted flange covers
Advantages: Maximum tightness, pressure resistance
Considerations: Longer opening/closing time
Quick-release systems
Advantages: Ease of use, time savings
Considerations: Requires regular maintenance of seals
Bottom valves
Several technologies exist (butterfly, ball, guillotine) with specific characteristics in terms of sealing, cleanability and abrasion resistance. The valve diameter directly influences the discharge flow rate and must be adapted to the process requirements.
3.2. Filling and emptying stations
The effective integration of IBC containers into your production process requires filling and emptying stations specifically designed to optimise material flows while ensuring safe and hygienic operations.
Filling stations: The filling of IBC containers must be designed to preserve product integrity while ensuring fast and accurate operation:
Dosing systems
Volumetric dosers: for applications requiring medium accuracy and high flow rates
Weight dosers: for applications requiring high dosing accuracy
Combined systems: combining speed and accuracy for large capacities
Containment and dust management
Inflatable sealing sleeves to create a tight seal
Localised extraction systems to capture dust emissions
Enclosed cabins with filtration for highly active or toxic products
Compaction and densification
Vibrators to optimise filling and reduce the volume occupied
Compaction tables for products sensitive to settling
Deaeration systems to remove trapped air
Emptying stations: Emptying is often the critical point in powder handling. The IBCFlow®02 is an advanced solution for this step:
Operating principles
Tight connection to the container valve
Integrated flow assistance systems
Precise control of the emptying flow rate
Minimisation of dust emissions
Containment levels
Open containment: for non-hazardous products with suction system
Closed containment: for sensitive or active products with vacuum/pressure transfer
Total containment: for highly active/toxic products with closed circuit and multiple barriers
Integration into the process
Direct emptying into mixers or reactors
Feeding of packaging lines
Interface with pneumatic or mechanical transport systems
Weighing and control: Weighing accuracy is often crucial:
Weighing technologies
Underfloor load cells (standard)
Suspended weighing (increased accuracy)
Dual range systems (capacity and accuracy)
Computerised control
Recipe and batch management
Weighing data recording
Interface with MES, ERP
Cleaning and decontamination: Cleaning the stations is as important as cleaning the containers:
Cleaning in Place (CIP)
Rotating nozzles (filling)
Closed circuits (valves, connections)
Automated sequences (washing, rinsing, drying)
Materials and design
Polished surfaces with no blind spots
Optimised flow slopes
Easy access for maintenance
3.3. Automation and conveying
The automation of the IBC container flow is a key step towards the overall optimisation of your production. It not only reduces manual intervention but also improves the traceability and reliability of operations.
Conveyor systems: The choice depends on the configuration, constraints and level of automation:
Roller conveyors
Advantages: Simplicity, robustness, reduced maintenance
Applications: Horizontal transfers, accumulation
Variants: Free-running (gravity-fed) or motorised rollers
Chain conveyors
Advantages: Versatility, ability to overcome differences in height
Applications: Complex circuits, direction changes
Considerations: More frequent maintenance
Automated shuttles (AGV/AMR)
Advantages: Maximum flexibility, dynamic adaptation
Applications: Changing environments, connection between remote areas
Considerations: Higher investment, IT infrastructure
Positioning systems: Precision is essential for automated operations:
Mechanical stops and guides
Advantages: Reliability, simplicity
Applications: Rough positioning, stopping
Active centring systems
Advantages: High precision, tolerance compensation
Applications: Automatic connection to stations
Sensors and controls
Presence and identity detection
Correct positioning verification
Anti-collision and anti-crushing safety devices
Identification and traceability: Key element for ensuring traceability and avoiding errors:
Identification technologies
Barcodes (economical)
RFID tags (contactless, information storage)
QR codes (dense information, omnidirectional)
Tracked information
Unique container ID
Contents (product, batch, quantity)
History (filling, storage, cleaning)
Status and destination
Supervision and control: A centralised system enables optimal management:
Essential features
Real-time visualisation (status, position)
Transfer order and priority management
Recording of movements and operations
Alarm and fault management
Integration with existing systems
Interface with MES
Communication with process controllers
Connection to quality/traceability systems
Operational safety: Automation must incorporate all aspects of safety:
Protective devices
Physical barriers and secure areas
Presence detectors and laser scanners
Emergency stops and safe restart
Fail-safe modes and emergency procedures
Manual intervention option
Incident recovery procedures
Redundancy of critical systems
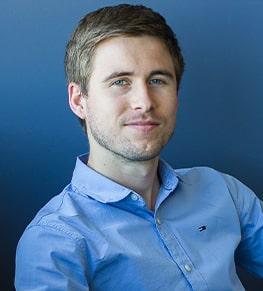
Do you have a project ?
I am available to advise and assist you in your research.
Guillaume, expert in modular powder handling and IBC integration
4. Constraints and solutions related to emptying IBC containers
4.1. Product characteristics influencing emptying
The efficient emptying of IBC containers is directly influenced by the physical properties of powders. A thorough understanding of these characteristics allows potential difficulties to be anticipated and appropriate solutions to be implemented.
Flowability and cohesion: The ability of a powder to flow freely is crucial:
Classification according to flowability
Free-flowing powders (angle of repose < 30°): easy and regular emptying
Medium-flowing powders (angle of repose 30-45°): may require slight assistance
Cohesive powders (angle of repose > 45°): require assistance devices
4.2. Technical solutions for efficient emptying
Various systems are available to optimise the emptying of IBC containers. Flow aids, such as vibrating plates or air fluidisers, prevent the formation of arches and facilitate product flow. For moisture-sensitive powders, emptying under controlled atmosphere is recommended.
4.3. Special case of sensitive products
Reactive or highly hygroscopic powders require special attention. Airtight storage prevents moisture absorption. Emptying must be carried out in a confined environment to avoid contamination. Clean-in-place (CIP) systems ensure impeccable hygiene between production batches.
5. FAQ: Answers to common questions about transitioning to IBC containers
5.1. What are the main advantages of IBC containers over big bags?
- Reduced cross-contamination
- Easier integration into automated lines
- Less handling and human intervention
- Cleaner and more controlled emptying
5.2. How can I ensure that IBC containers are completely emptied?
The use of suitable emptying stations, such as the IBCFlow®02, guarantees total extraction of the product without loss or residue.
5.3. Are IBC containers suitable for all types of powders?
Yes, provided that the right model and accessories are chosen: valves, internal coatings, flow aids.
5.4. What is the service life of an IBC container?
A well-maintained IBC container can last for several decades, thereby reducing operating costs.
5.5. Can IBC containers be integrated into an existing production line?
Yes, they can be integrated gradually to replace big bags and improve process efficiency.
Conclusion
Adopting IBC containers means opting for cleaner, more flexible and more automated production. This transition allows you to optimise traceability, reduce contamination and improve powder management.
📞 Do you work in rare earth processing or recovery?
Contact our experts to design a customised, high-performance and secure production line together.