Over the past few decades, big bags (also called bulk bags, jumbo bags, super sacks and FIBC – Flexible Intermediate Bulk Containers) have become the preferred choice of storage and transport for dry bulk materials. They have the benefits of significantly lower costs compared to IBC’s and 50 lb sacks and are easier to store and ship to different locations. Furthermore, big bags are relatively simple to handle, requiring either a forklift or pallet truck to move around a production area. Super sacks are suitable for almost every type of dry bulk solid and powder, and are used in various industries including: food and beverage, chemical, pharmaceutical, cosmetic, minerals and energy.
However, with their increased popularity comes new challenges that manufacturer’s must address. Big bags often are susceptible to suffering from poor flow and unloading properties. There are several reasons for this.
1. Is the material hygroscopic?
Big bags may be dust tight but most of them are not impervious to water and humidity. Steps can be taken to provide better protection for the contained material (i.e., inner liners), but if your material is left for long periods in humid environments, eventually that material will be exposed to those conditions. Over time, some materials will absorb moisture from the environment it is stored in. This can result in operators being unable to get the material to discharge out of the unloading spout once in production. Sugar is a common example when facing this issue. Over time humidity causes the particles in the big bag to agglomerate, forming one large square shaped block.
2. Will the big bag be stored for longer periods before use?
Long storage periods can result in several issues with dry materials stored in big bags.
The first is the powder can naturally segregate over time with finer particles sinking to the bottom and larger particles remaining on top. Also, it is common for big bags to be stacked on top of each other in storage. All that weight over time can compact the particles, resulting in compression lumps. Agglomeration caused by compression tends to be easier to break a part when compared to lumps formed by moisture exposure, however, they can still greatly interfere with the unloading and feeding of the material to a downstream production process.
3. Will the big bag experience temperature fluctuations?
In some areas of the country, the difference between day and night time temperatures can significantly vary. As the air heats around dry particles, water vapor in the air can condense into water droplets. Revisiting the first point, hygroscopic materials can then absorb the condensation in the environment. This is similar to the dew point temperature where the change in temperature occurs faster then evaporation. This results in the same issue, a big bag that has solidified into one solid rock of material.
With these issues present in a manufacturing process, poor or non-existent flow while attempting to discharge a big bag can hamper production and cause costly inefficiencies if the problem is frequently occurring. Operators attempting to manually break up big bags with bats, crow bars, or even the back end of forklifts (pressing against a wall) can present several safety concerns in your factory. The big bag conditioner (also called big bag crushers or big bag massagers) is the industrial solution to this frequently occurring issue.
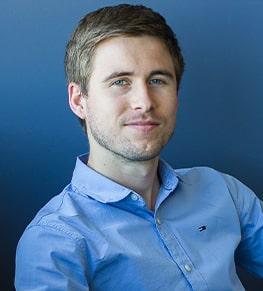
Do you have flow problems with your powder?
I can help you to optimise your process.
Guillaume, powder expert
4. What is a big bag conditioner and how do they work?
There are various designs and configurations for big bag conditioners in the marketplace today. But all operate on the same principal, applying significant amounts of pressure to the walls of the big bag to loosen the material for better flow performance.
The equipment can either be integrated into a big bag unloading station, or designed as a stand-alone solution. Big bag massage paddles can be used on unloading stations to help with bulk solids that contain poor flow properties due to softer lumps contained within.
However, for big bags that are one solid hard block of material the preferred and more useful method is the stand-alone option. Usually, stand-alone big bag crushers rely either on pneumatic or hydraulic pressure that cause rams or blocks of steel to press against a big bag. Pressure performance can vary but often times ranges as low as 7,000 lbs up to 75,000 pounds of force. An operator can load the big bag into the front of the machine and several loading and lifting methods can be used to help manipulate the big bag during its crushing / conditioning stage. Scissor lifts and turn tables can be used to help lift and turn the big bag to apply pressure to all sides. Also, the crushing mechanism itself can be raised and lowered to help apply pressure on the high, mid and low points of the big bag. A PCL can be used to help automate the sequence and store various programs for different types of material that may vary in how the big bag conditioner is best utilized.
The big bag conditioner is fairly simple, yet robust in its construction. A steel support structure surrounds the big bag and provides the necessary strength to give the massaging cylinders enough resistance to be effective. Different options can be selected for loading the big bag but most common is the handling cross support to hold the big bag in place via its handles during operation. Hydraulic arms or pneumatic massage cylinders apply the necessary pressure to break up the hardened agglomerates and promote good flow. Safety enclosures made of either clear acrylic or a metal cage can help protect operators from injury during machine operation. Other safety features include light curtains to shut down the machine if an object breaches the safety parameter. Materials of construction can be offered in painted steel, 304, or 316 stainless steel.
Operation procedure:
Average cycle time: 5 min
- Operator attaches the big bag to the handling cross
- A forklift or hoist loads the handling cross into the conditioning station
- The big bag is secured in the cage and safety switches are activated with the closing of the door
- Conditioning cycle commences with options for lifting and lowering of the big bag (by hoist or lifting table)
- The cycle finishes and the operator opens the access door
- Evacuation of the big bag by forklift or hoist
Since 1992, Palamatic Process has provided materials handling equipment to over 2000+ installations in over 30 countries. We offer knowledge and expertise in all manner of powder and bulk automated material handling needs.
Examples include: big bag unloaders, big bag fillers, pneumatic conveying systems, mechanical conveying systems, mixing and blending, lump breakers, pin mills, centrifugal screeners, bag dump stations, etc.
Contact one of our experts today for assistance with needed material handling solutions and to request a quote.