Production facilities that handle powders and bulk solids can face a lot of challenges during the packaging phase. It is critical for an equipment supplier to understand the production challenges and system requirements of the client when sourcing powder filling equipment.
There are a few basic questions you can ask yourself to help select the right powder filling machine or drum filler that fulfills both production goals and your customer’s expectations. There are a few key criteria that should be understood first regarding drum filling systems, pertaining to their functionality and overall design.
1. What are the production requirements?
Production and design requirements include (but not limited to):
- Production rates (drums per hour)
- Dosing accuracy
- Hazardous area rating
Material handling equipment suppliers should be able to meet a range of needs on drum filling and powder handling requirements. Production rates will largely determine the operational functions and features of the powder filling system. Smaller production facilities may only need to fill a few drums per hour, in this instance a manual filling station with a few integrated features should suffice.
As an example, the PalDrum® 01 drum filling system is a stand-alone station that should be sufficient for manual and low output production rates. But larger production facilities with high production requirements may need a more automated filling system like the PalDrum®03. Integrating features such as cyclone collection filters, motorized roller conveyors, load cells, screw feeders and buffer storage hoppers will provide a client with a turnkey solution.
Some manufacturers may have less concern about precise filling weights if they are selling a less expensive material by bulk. In contrast, the production of high value powders, like active ingredients in pharmaceuticals or precious metals, will need very precise dosing mechanisms. This is to prevent over or under filling the drum containers. By using load cells on the filling hopper and integrating a screw feeder, it is possible to achieve a dosing accuracy within +/- 1 - 2 grams with certain powders and granules.
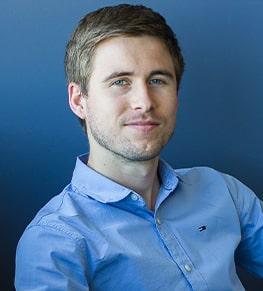
Do you need personal advice on drum filling systems?
I am at your disposal.
Guillaume De Clercq
2. What to consider for ergonomics and safety?
When it comes to improving the ergonomics and safety of a container filling line there are several considerations to take into account. Is the equipment easy to use? What level of containment is required to keep the work environment clean? How toxic is the material and what hazard does it present to an operator’s health? What level of intervention will be required by operators?
For workplace efficiency and ease of use, we recommend discussing the following production sequences:
- How are the drums loaded into the filling system?
- How are they transferred to and from the filling head?
- What level of containment is necessary (i.e. dust filtration, containment field, etc.)?
- How do we remove the drums once filled?
For lower output systems, we can load 1 to 4 drums at a time by a forklift. In this instance, the pallet holding the drums is loaded onto a weigh scale under the filling head. In a system featuring semi-automation or full automation, we will most likely be using a robotic lifting arm or a vacuum lifter. The conveying of the drums to and from the filling station will be handled by motorized roller conveyors. Once the drums are filled, they can be removed by the same equipment, either a robotic clamping arm or a vacuum-based lifter.
To see an example of such equipment, check out the Palamatic Process Drum Manipulator. For materials that present little threat to the health of your workers, we can contain the dust during the filling phase with a tray cover over the drum. This basically consists of a flat lid that lowers over the drum via a pneumatic cylinder, once the filling sequence is finished the tray lifts up to allow the drum to evacuate and the next one in line to takes its place.
However, with materials that are especially hazardous or toxic to the health of your workers, an equipment supplier can design and containment field around the filling station. This can either be a plex-glass cage, or a housing unit made of steel. Dust extraction ports will be attached to the housing to allow a central dust collection system to pull any fine particulates that may be free floating during the filling and conveying phases. To help safely remove the drums, a vacuum lifter for drums can be used by operators to reduce the strain. The vacuum suction does all the heavy lifting for the operator, and they simply need to steer and guide the drum onto a pallet.
3. What amount of automation is required?
Production rates, ROI and system design are the key drivers in what level of automation a production process requires. Powder filling machinery can be grouped into three distinct classes based on the machine’s automation level: manual, semi-automatic, and fully-automatic drum filling machines.
In manual drum fillers, the operators need to be managing the functions of the process and take a very active part in the filling sequence. They need to perform most of the tasks including the following:
- Weighing of the filled containers
- Determining the exact fill quantity
- Starting and stopping the machine
In semi-automated setups, some parts of the process are automated while other parts are still manually done. Depending on the manufacturer, it may be possible to upgrade them to a fully-automatic machine with a few modifications. Semi-automatic drum loaders can have a PLC control system for performing a series of tasks such as quantitative filling and measuring dosing weights. Finally, semi-automatic systems allow the operator to have more control over the filling process. Operators can even use weight-based or volumetric filling limits.
Full automation makes use of the latest technology which results in minimal or no labor input and an efficiently controlled process. The majority of the process’s tasks are done automatically via the PLC system sequences. These tasks include: loading the empty drum onto the line, transferring the drum to the fill head, dosing of the powder product into the drum, product weighing/measuring, densification and transfer to the temporary buffer storage area. Also, automated container fillers can handle both powder and granulated products, which results in an easy to use and flexible packaging process.
Palamatic Process has been supplying the powder and bulk solids industry with drum filling equipment since 1992. In order to determine what solution is best for your project, contact one of our sales engineers. Together, our team of experts can provide the right kind of powder filling equipment that will fulfil your every production goal.
Contact one of our experts today for assistance with needed material handling solutions and to request a quote.