- 1. What is my dust removal need?
- 2. What are my products to be vacuumed (powders, ATEX)?
- 3. What is my system (local centralised, fine recovery, steel or stainless steel pipes, etc.)?
- 4. How to define the volumes to be aspirated?
- 5. The main design principles
- 6. From "mobile" vacuuming to broom cleaning
- 7. Adjustment during commissioning and after-sales service maintenance
Are you planning to modernise, extend or create an industrial dust collection system? Before you start, it is important to ask yourself all the questions you need to know in order to obtain the desired results.
1. What is my dust removal need?
Before adding up the necessary flow rates for each of your machines, it is important to define the operating times, the hours of use and the flexibility of the machines. The simultaneous use of the production lines is an essential value for the dimensioning of the dust collection network.
Also, the products treated in dust collection require specific designs: granulometry, density... When dedusting carpentry, flour mills or chemical production sites with the possibility of gas, the choice of material is essential.
The fine particles are collected in the filter box, which itself is discharged either into a skip, a big bag, a drum or a bucket. For fly ash installations, Palamatic offers specific FlowMatic® 02 Ashflow big bag stations to maintain the optimal containment level. When discharging into a skip, bottom screws are necessary to distribute the product in the recovery skip. As dust collection fines have several destinations (recycling, incineration, reintroduction), it is important to define your needs.
2. What are my products to be vacuumed (powders, ATEX)?
The product vacuumed has a direct impact on the filtration technology. The air velocities at the collection point, the air velocities in the dust collection ducts, as well as the rising air velocities in the dust collection box must be calculated according to the granulometry and density of the products being sucked up.
The concentration of the fines to be sucked in must be carefully considered as well as the temperature and humidity.
If the speed is too low, this will lead to poor collection, a large deposit in the pipes and a non-optimal use of the filters. On the other hand, too high air velocities lead to loss of product at the collection point, a risk of wear and tear on the pipes and control valves due to abrasion and clogging of the filters in the upper part. The reference velocities at the collection point are between 0.6 and 0.8 m/s and 25 M/s in the pipes.
The explosive nature of your powders is a major point in the definition of the material to be installed. The KST, the EMI, the Pmax of your products must be known for the calculation of the explosion vents and the mechanical resistances of the dust collector box. (Cf ATEX at Palamatic).
The filters installed in the dust collector box can be either cartridges or pockets. The choice between cartridges and pockets depends on the products you are treating and the space available. Pleated cartridges are compact but more complex to unclog. Pockets are simple to declogging by counter-current but take up more space. In the same way, the filtration qualities vary according to the granulometries treated.
Class according to ISO 16890 | ||||
---|---|---|---|---|
Class according to EN779 | ISO ePM1 | ISO ePM2.5 | ISO ePM10 | ISO Grossier |
G2 | - | - | - | >30% |
G3 | - | - | - | >50% |
G4 | - | - | - | >60% |
M5 | - | - | >50% | - |
M6 | - | >50% | >60% | - |
F7 | >50% | >65% | >85% | - |
F8 | >65% | >50% | >60% | - |
F9 | >50% | >60% | >95% | - |
3. What is my system (local centralised, fine recovery, steel or stainless steel pipes, etc.)?
Your dust collection system must be designed to avoid any product deposits in the piping system and to minimise pressure drops as much as possible. Network pressure drops lead to the installation of fans with high suction power (depression) which are energy consuming. The more your network is optimised, the more your energy consumption is preserved.
In order to have a so-called "balanced" network, it is important to provide damper valves to adjust the suction flows at the various collection points and also to close these suction points when the machine is not working. These suction cuts must not lead to "overpowering" of the suction at the other operating points. This overpowered suction would result in loss of product or even a process malfunction. These flow control valves are essential for the correct operation of the line and their automation is often necessary to avoid any manual adjustment due to excessive handling by the line operators.
The choice of materials used must be studied according to your product and your hygienic requirements. Stainless steel piping can be considered in food processing and/or humid environments. Galvanised or painted versions can also be used outdoors thanks to C4 type paints.
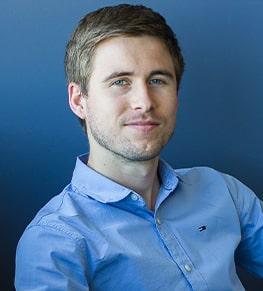
If your require further assistance,
I am at your entire disposal.
Guillaume, expert in powders
4. How to define the volumes to be aspirated?
The quantity of air to be treated depends on machine requirements and the type of collection points.
An extractor hood, a bag pourer, a conditioner or a silo must appear in your need for utility. For example, a flow rate of 150m3 /h may be necessary for a big bag conditioner and 800 to 1200 M3/h for a manual bag pourer. When you wish to dust a trap door or any type of opening, it is important to calculate the section in m² and to make a balance.
A fine calculation must be made in order not to underestimate the flow rate which would lead to an unconvincing result. Or, conversely, too high a flow rate would lead to a loss of product but also a large volume of air regenerated, which could quickly become expensive when your building air is treated, conditioned or even dried out!
5. The main design principles
To summarise the above principles, size your flow rates according to the surface area of the openings to be dusted.
- Surface area to be dusted in m² x 0.6 to 0.8 m/s
- Air velocity in the pipes 25m/s
- Control valve (damper) on each of the inlets
- Required fan depression = pressure drop due to the mains (according to the chart) + pressure drop generated by the filters in operation.
- Necessary filtering surface according to the selected technology (cartridge / pocket) with a respective ratio of 50 and 125 according to the total suction flow.
Pneumatic counter-current cleaning is currently the most effective way of using mechanical vibration solutions. Cleaning pressures are generally around 6 bars. Cleaning ramps are installed in the clean filter housing to come intermittently to clean the filters by "brutal" air injection. The sequence, the cleaning interval, is controlled by a sequencer or by a pressure sensor called Delta P. The Delta P pressure sensor detects the level of clogging of the filters by taking the differential pressure between the clean and the dirty housing. When the threshold is reached, a cleaning sequence is sent.
In case of toxic dust, a second filtration stage must be considered with absolute filtration. In addition to absolute filtration, a so-called tribo probe can be installed to detect particles in the clean air exhaust and thus stop the installation for repair.
For ATEX installations, an explosion vent, a flashback arrestor or quick-closing valves as well as the channelling of the fan outlets must be installed. A point of caution is to be noted for the positioning of the vents and the installation of relief ducts which may be useful in some cases.
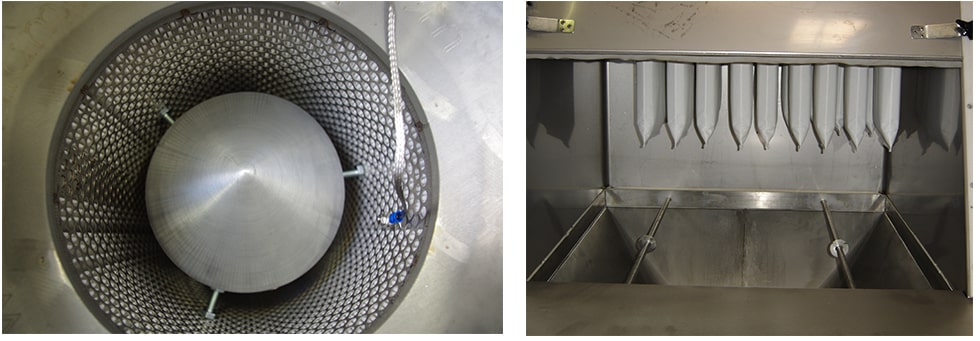
6. From "mobile" vacuuming to broom cleaning
When setting up a centralised network, it is often interesting to consider setting up a "broom" suction network. Specific outlets with manual and flexible valves should be provided at the beginning of the design. Pneumatic booster valves may be necessary if your hoses are particularly long.
7. Adjustment during commissioning and after-sales service maintenance
When installing your dust collection network, it is important to adjust all the flow rates at the various collection points using a flow meter. The adjustment must be carried out by a specialist and all dampers must be locked in position.
For the regular maintenance of your network, the filtering quality of your cartridges must be checked periodically to ensure good performance and also to make sure that no cartridge is pierced. The delta P sensors are precious organs to define the state of your cartridges. Similarly, the vent sensors inform you in case of an explosion in your casings. Any vent rupture is reported to your PLC for shutdown and complete control of the installation.
When air is reintroduced into your building, the controls must be programmed on a periodic and mandatory basis.
Contact our experts in industrial processes dealing with powders to define your dust removal network as well as possible.