Manufacturers in today’s current economy are seeing the need to automate and streamline their production in order to stay competitive and responsive to consumer demand. How you handle, or transfer, your powders and bulk materials is just as important as the milling and mixing (value adding) steps.
If the right conveyor system is not selected for your material-handling process, you can end up undoing all the work you put into achieving the desired outcome. Let’s first look at the different methods and implementations of pneumatic conveyance systems.
1. Dense pneumatic conveying vs. Dilute Phase pneumatic conveying
The two main categories that most pneumatic conveying systems fall under is dense phase or dilute (also called lean) phase.
Dense phase conveying involves conveying material with pockets of high pressure that causes the material to form dunes and valleys, or slugging, along the conveying line. Typically, these systems have a low air-to-material ratio, so conveying air velocities are lower meaning your material is handled more gently when compared to dilute phase.
Often times it is important to a manufacturer to preserve the integrity of the product. Dense phase methods are by far the preferred choice for preventing attrition with otherwise friable powders. Furthermore, it’s also preferred when conveying mixed materials to prevent particle segregation. Dense phase is also used on materials that can be naturally abrasive and would otherwise cause serious erosion to the conveying lines (i.e., worn out pipe bends).
In a typical dense phase setup, material is fed into a pressure capable transfer tank fitted with a dome valve for shut off and sealing. Once the level probes indicate the vessel is full, the dome seals it closed where pressurized air is introduced. Once the vessel is pressurized the outlet valve gradually opens introducing material and the “slug” of pressure into the pneumatic conveying line. Because the Palamatic Process dense-phase conveying system excels at abrasive and friable material transfer, it is not uncommon for our systems to last 1,000,000 operating cycles before general maintenance is required.
The additional advantage of Palamatic Process to the standard functions described above is the non-use of a valve. The Mactenn® airlocks integrate a dome valve avoiding the use of level probes. The Inflatek® dome valve allows the product column to be cut off and the transfer airlock is thus completely filled. In addition, the Mactenn transfer system does not use a valve at the airlock outlet. Pressurization of the airlock is possible thanks to Mactenn's patented and special design.
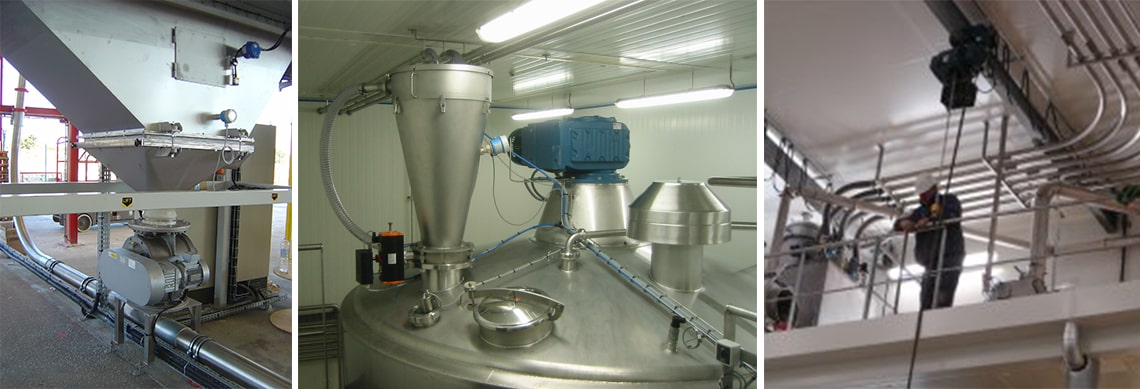
Dilute (lean) phase conveying equipment uses a high air-to-material ratio, so material is transferred at much higher air velocity. This high velocity results in achieving the material’s saltation level, where particles are suspended in the air stream along the conveying lines.
The benefit here is the transfer is uninterrupted as material is conveyed from the feed to the output. The air stream in dilute phase is typically generated by a blower at the front end (pressure system) or at the back end (vacuum system). A typical feed setup in a dilute phase conveying system is a buffer hopper for holding the material and a rotary airlock valve (or rotary valve) to provide a steady feed into the airstream below. This type of material flow transfer system is very common for silo loading and unloading. Another advantage of dilute phase is the ability to use several supply and collection points in one transfer system. Pressure dilute phase systems are also typically better at transferring materials over longer distances and heights.
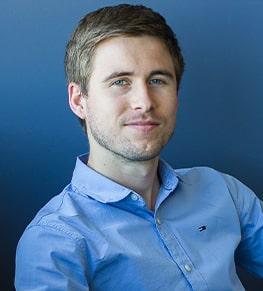
If your require further assistance,
I am at your entire disposal.
Guillaume, expert in powders
2. Pressure vs. Vacuum Systems
Pressure conveying systems are typically made up of a blower or compressed air unit, a hopper/IBC/silo, rotary airlock valve, a conveying line, and the receiver. They also typically require a vent and dust filtration at or past the receiving end. Therefore, pressure systems can result in being higher cost compared to vacuum conveying methods. However, these systems are preferrable when trying to transfer heavier bulk materials over longer distances.
Vacuum conveying systems are typically comprised of pick-up points or a nozzle, conveying line, the receiver and the vacuum generator. Vacuum generators can typically use a number of devices such as a Venturi unit, low-pressure blowers, regenerative blowers, etc.
The vacuum causes the material to move through the conveying lines where it is typically received by a cyclonic air / product separator. In cases of expensive material where product loss to the filter must be kept an absolute minimum, a secondary cyclone separator can be used to retrieve as much of the powder as possible before the air is filtered. One of the main advantages of vacuum conveying is the ability to load the system from open top containers via suction wands (e.g. drums, bins, gaylords, bulk bags, etc.).
Pneumatic transfer systems, due to the pressurization of the whole line, do not produce any product emanation or dust towards the outside.
3. Summary
Ultimately, it is always best to discuss your particular project requirements with one of our Palamatic Process sales people. Our team can help guide you through the decision-making process to select the most appropriate conveying system.
Both pressure/blower and vacuum pump systems are great at providing dry bulk material transfer efficiently while containing any dust emissions. Generally, pressure systems are great at moving heavy materials over long distances but vacuum systems excel at conveying materials that are prone to plugging or where plant floor space is somewhat more restrictive.
Dense phase conveying excels with fragile, blended, and/or abrasive materials where dilute phase is great for a steady, continuous stream over longer distances.
Always be prepared with the following information when seeking a pneumatic conveying system: type of material, bulk density, flow characteristics, required flow rate, conveying distance in length and height, explosivity of material, and how many pickups and drop off points are required. For further information, please visit our website at
Find all our pneumatic conveying solutions and bulk handling equipment or contact our powder experts for personalized support.