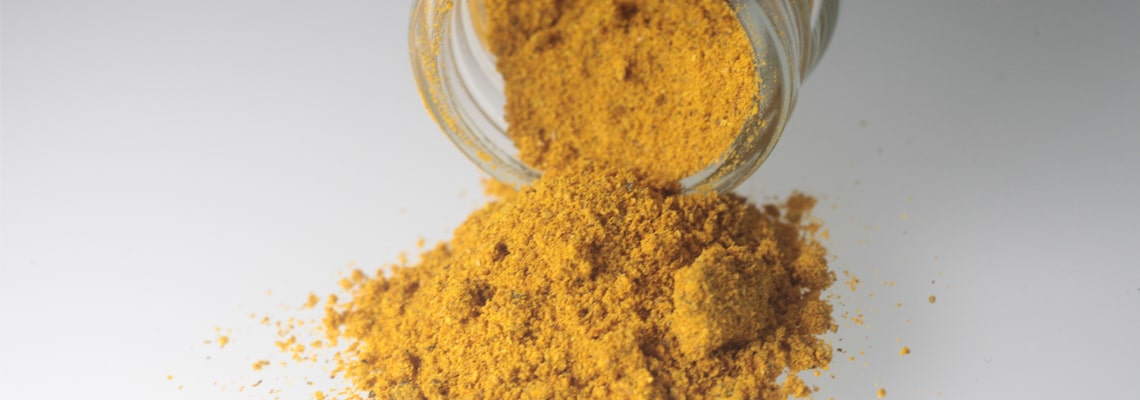
One out of every two factories in the world handles dry powder ingredients. Every powder has unique characteristics which will determine its final quality and can be biological, chemical or inorganic. In addition to the intrinsic properties (composition, particle size, density, morphology, etc.), the behavior of a powder is also determined from the interactions with its environment, in particular with the atmosphere (humidity, temperature, aeration rate). Also, the way the powder is handled will have an impact on its density and flowability (packaging properties, electrostatic charge, surface morphology, etc.).
Whatever your industrial sector (food and feed, chemicals, fine chemicals, construction, water treatment, energy), a careful analysis of your powder is an essential step in obtaining the desired process outcome.
Palamatic Process has determined the 7 main properties of powders to give you the ability to determine their qualification.
1. Particle size of powders
The particle size of a powder includes both its shape and its particle size distribution. This is a major characteristic because it has consequences on the other functional properties of the powder (density, ease of flow, solubility, etc.).
It is important to distinguish two points of mass / density:
- Bulk density is a measure of the mass of several particles in a granule or powder divided by the total volume they occupy
- Density, also called mass density, corresponds to the ratio between the mass of a volume of material and said volume of material.
At Palamatic Process, we take into account the bulk density of powders as a whole with the amount of air that brings them together.
2. Density of powders
The density of a powder, also known as "bulk density," is the density of particles, including the spaces between the solids (particle bed). It is expressed in kilogram per cubic meter (kgm³) or pounds per cubic foot (lbs/ft³).
Density is essential because it will determine the necessary size of equipment and containers (hoppers, silos, bulk bags, sacks) in an industrial process. If it is high, it will reduce the transport cost calculated according to the volume (Pisecky, 1980). It also has an impact on the very functional properties of powders and in particular, that of hydration.
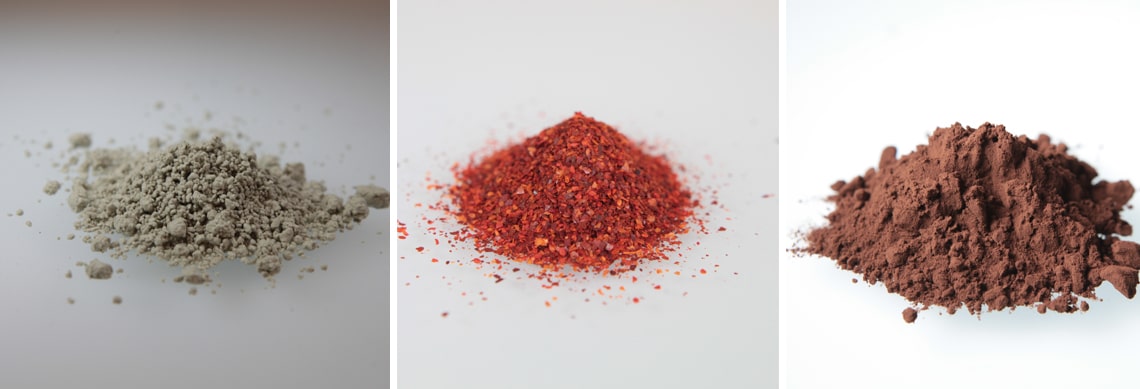
3. Flow of powders
The ability of a powder to flow well is an important parameter to take into account before any conditioning, unloading, transfer, storage, dosing or even mixing operations. If the powder had poor flow properties, it may form lumps which could damage certain equipment.
It is first necessary to study the type of flow of your powder. Several methods for evaluating the flowability of powders exist: measurement of the angle of repose, settlement tests (Hausner index, dynamic tests by settlement or compression), comparison of settlement tests, etc. The Jenike test makes it possible to quantify the flow properties of a powder by determining breaking points, which themselves define a flow location.
The performance of these tests allows us to define the minimum flow diameters, the degree of slope of the hoppers, the necessary surface finish, the installation of a device to aid in flow if necessary, etc. Learn more about the qualification of your powders.
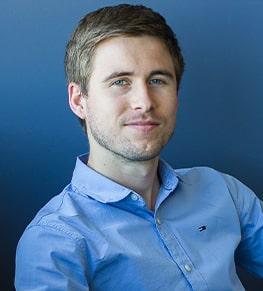
If your require further assistance,
I am at your entire disposal.
Guillaume, expert in powders
4. Hygroscopicity of powders
A hygroscopic powder tends to retain moisture in the air, either by absorption or adsorption. A powder is not considered to be hygroscopic if its percentage of hygroscopicity is less than 10%. Some of the most hygroscopic powders are: powdered milk / lactose, calcium chloride, sorbitol, soda and magnesium oxide.
The excessive moisture content of a powder can make it’s flow problematic due to the formation of agglomerates that can potentially clog transfer equipment. In this example, it will be necessary to set up a dehumidification process upstream in order to avoid exposure to humidity.
5. Solubility of powders
The solubility of a powder, which consists of dissolving a powder in another substance to form a homogeneous mixture, will influence certain industrial processes where the powder is intended to be incorporated into an aqueous phase.
The solubility of a powder is affected by many parameters such as viscosity, air temperature, particle size, etc.
6. Wettability of powders
The wettability of a powder is the time required for all of the powder to pass through the air / water interface without agitation. In other words, the wettability of a powder illustrates its ability to absorb water on its surface. The wetting of a solid, such as a powder, versus a liquid is often characterized by the liquid-solid contact angle.
The wetting will depend on several factors such as pressure, temperature, humidity, for a given liquid-solid combination.
It is possible to adjust the degree of wettability of a powder via the size of its particles, its density, the presence of air, etc.
This is an important property when the powder is used as an ingredient in a process. This is particularly the case in the field of instant drinks.
Palamatic Process has designed a dedicated process line for the rapid mixing of your powder into a liquid by forcing incorporation
7. Dispersibility of powders
Dispersibility is the ease of dissolving a powder in water with stirring. Several elements act on the dispersibility of powders: particle size, temperature of the outlet air, protein content, etc.
Sectors such as instant drinks, or infant nutrition, are looking for high dispersibility powders for the manufacture of their products.
Our experts are at your disposal to qualify and test your powders in our powder laboratory in order to adapt the best process solution corresponding to your manufacturing needs (definition of minimum flow diameters, the degree of slope of the hoppers, the surface condition, grain size, etc.). Contact us for your project.
Source : Agronomic Innovations 13 (2011).