1- The physical differences:
Centrifugal sifters, also known as a rotary sieves, are screening machines. These powder sifting machines uses centrifugal forces to control and classify powder particles and granules. The housing of the centrifugal industrial sifter is elongated and typically supports a direct or indirect drive motor on one end, and a bearing for the central shaft on the other end. A discharge hopper below the machine housing helps guide the screened powder into the downstream process.
Likewise, a short, flanged outlet on the bearing end of the screener helps remove unwanted contaminants and over size agglomerates from the process. The centrifugal sifter typically comes equipped with two access doors, a side door for quick inspections of the screen, and a bearing end door to allow removal of the screen for maintenance.
The feed inlet and main outlet are off-center and vary in stack up height between 37” – 40” approx. Various fabrications are possible including mild, 304, and 316 stainless steel and screens are available in nylon cloth, woven wire, perforated plate and stainless steel mesh.
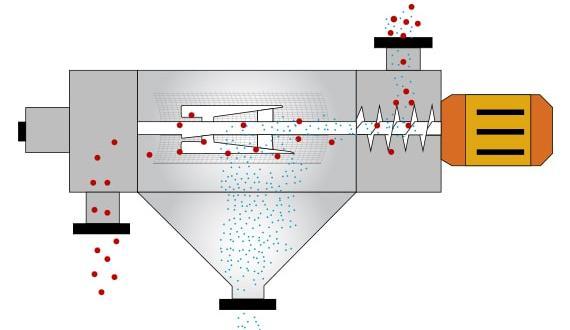
Vibratory screeners, also known as flat deck screener, vibratory sieves or vibrating screens, can come in different shapes and sizes. One of the more common designs are circular decks that support steel or nylon mesh flat screens. It is not uncommon to see 2 decks stacked on top of each other to provide a degree of classification in your screening process.
An offset motor is directly attached to the outside of the screener to provide the vibration that agitates the powders for the screening action. An inlet on the top of the dust cover and an outlet directly below the screener provide the inline throughput of powders and granules.
Vibrating screeners have an inlet and outlet directly in line. Stack up heights vary from 15” to 25.5” and various fabrications are possible including mild, 304, and 316 stainless steel. Vibrating sieve mesh can be made in various micron sizes from wire-cloth, steel-wire, nylon mesh, and perforated plate.
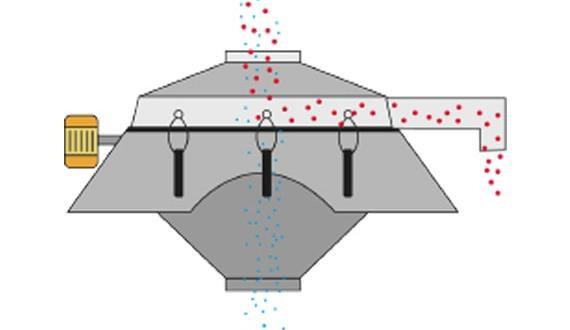
2- The performance differences between sifters and screeners
Centrifugal industrial sifters get their name from the spinning action of the paddles inside the sieving chamber. The screening process starts at the inlet where material is dropped into a mini-feed auger that pushes the material into the cylindrical screening chamber.
A nylon mesh screen is fitted and clamped onto a screen cage for support and sturdiness. As the powder encounters the centrifugal forces of the spinning paddles, the particles hit the surface of the mesh of the industrial sifter. These paddles spin at a rate typically in the range of 600 – 700 RPM. All undersized particles, or “good” material, passes through the screen separator and down into the central discharge hopper. Anything oversize, such as foreign detritus or hard lumps, are carried down to the end of the screen basket and out the oversize “rejection” outlet, removing these undesirable particles from the process. Common applications involve flour sifting, sugar screening, and various applications in food and chemical industries.
Vibrating screeners, or vibratory separators, rely on the off-set motor mounted to the outside for the necessary agitation of the powders to be screened. As product is fed from above, material comes into contact with the woven wire-mesh. The vibration spreads the material across the surface of the screen for separation, sifting undersize particles through and oversize to be swept out the side rejects port. A all deck underneath the screen can be used for rubber anti-blinding balls that will keep the metal sieve mesh free and clear of near size particles.
Common applications of this industrial sifter often involve sieving large amounts of bulk material for large objects like bits of wood and metal scrap.
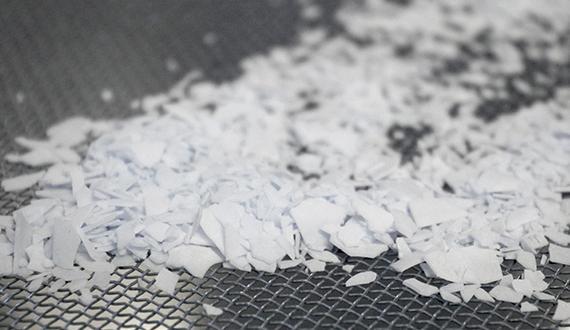
3- The Advantages of sifters and screeners
Centrifugal sifters, by the spinning action of the paddles, offer a mild de-agglomerating action. These machines are often used in food production to help break apart raisins, as well as other types of dried fruits. Any type of small lumps that can be described as friable (e.g., compression lumps in sugar and flour) a centrifugal sifter can most likely handle. The centrifugal forces can also help keep nylon mesh clean from near size particles plugging the screen. Therefore, the machine does not need any other type of mechanical anti-blinding mechanism. Because of this, it is possible to screen materials that contain a low percentage of fat and moisture, for example, screening pet food meal before extrusion.
Also possible with a centrifugal sieve is the ability to scalp small percentages of over-size material for recycling back into the upstream process for a second pass through on milling equipment (refered to as scalping). Finally, these machines are known for quiet operation, adding to worker safety on the processing floor.
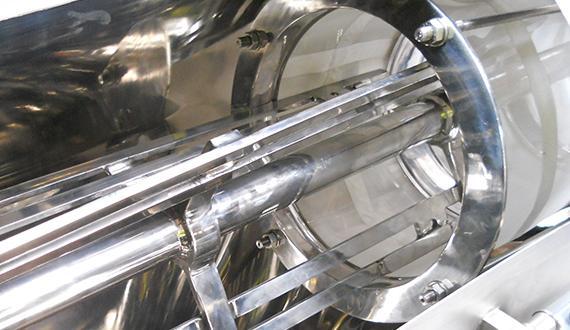
Vibratory screeners are great for high feed rates and quality control of powders, where a simple coarse screen allows 99.9% of the material to pass straight though to the down stream process. They are compact, and the inlet and outlet flanges are inline which makes this screener easy to retrofit into existing processes with restrictive height clearances.
There are also fewer components which reduces downtime for cleaning and maintenance. Also, screens can be more easily swapped out with an on-hand spare replacement.
Finally, these screen separators are less prone to damage when checking for foreign contaminants, like nuts and bolts, since the mechanical action is located on the outside of the housing.
Both types of screen separators can be designed for gravity feed and pneumatic conveying applications. There is a wide selection of micron mesh sizes based on the application.
To help your supplier determine what is the best strainer / screener to choose from, its good to know the following information:
- Feed rate
- Particle Size Distribution
- Material Characteristics
- Fat and Moisture Content
- Purpose of the industrial sifter
In order to determine which type of separation equipment is best for your process, consult with one of our knowledgeable sales staff today!