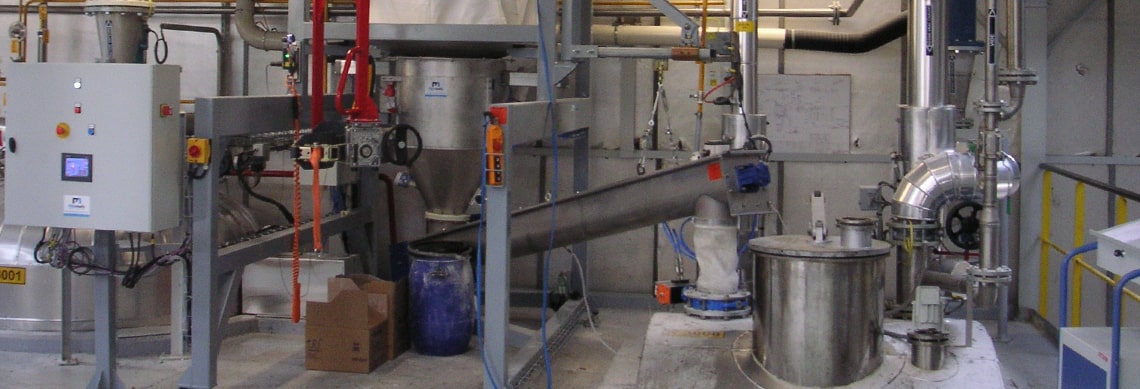
Chemical reactors are widely used in the manufacture of glues, resins, inks, and paints, as well as the pharmaceutical or cosmetic fields for creams, shampoos, reagents, etc.
The operation of loading a reactor can be a delicate process for the chemical industry. The majority of powder feed applications of chemical reactors is typically where NEC zoning is present, and often to a significant degree. The NEC classes are generally defined by Classification 1, 2 or 3 and Division 1 and 2.
The risks associated with loading do not alleviate the need to provide the correct doses of ingredients, the ergonomics of the workstations for the production operators, the traceability of the production batches, etc.
Why stop feeding your reactor through the access manhole?
Loading the reactor with powder or liquid through the reactor manhole is the solution that seems the easiest and most efficient for many chemical manufacturers.
This solution generates many risks with regard to operators and environmental constraints.
1. The risk of electrostatic discharge
The operator feeding powders directly above the reactor can carry electrostatic charges which can spark at any time if he is not properly grounded.
In addition, the friction generated by the powder on the feed hopper or funnel charges the powder with static electricity which can generate micro sparks. These "small" sparks, known as "tassel discharges" cause the explosion of clouds of gas present in the reactor or escaping from the reactor through the manhole.
Using a de-dusting ring is not a sufficient solution to satisfy the NEC zone, and the risk of explosion is increased at the level of the dust collector which collects these clouds of gas with very low ingnition energy.
The required EMI for gases is much lower than the EMI for powders, which is about 3 mJ for powders against NDEs <1 mj for gases!
2. Work ergonomics
Another reason to stop this method of loading your reactors is for production ergonomics.
The operator, in addition to being exposed to the fumes of solvents, must handle large quantities of loads (bags, drums, cans, etc.) without ergonomics and generally in the presence of a dusty atmosphere. De-dusting ring solutions with a bag depositing table exist but remain applicable for low-speed applications.
Relocating your sack dump station or big bag unloading station provides the operator with efficient ergonomic conditions with clean, dust-free unloading operations incorporating suitable handling solutions. Palamatic Process bag manipulators can perform these depalletization operations with ease.
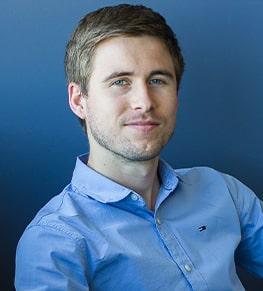
If your require further assistance,
I am at your entire disposal.
Guillaume, expert in powders
3. Maintain your reactor under a nitrogen blanket
The goal of all operators of chemical reactors is to keep their vessel in a controlled atmosphere (generally nitrogen) in order to ensure safety and manufacturing quality. Loading these powders and ingredients in a closed reactor respects manufacturing quality. In some applications, evacuating the reactor to ensure that the mixture is aerated and to promote dispersion or absorption is a necessity.
The solution using an introduction airlock therefore becomes the preferred solution.
See more information about our application: reactor loading case study.
4. Environmental protection
To definitively abandon this charging practice, opening the reactors to release emissions of solvents to the surrounding work environment, VOC gas (volatile organic compound) requires heavy capture and treatment systems to prevent the escape of toxic gases into the atmosphere. Regulatory bodies impose gas scrubbers on installations incorporating reactors.
Make an appointment with our experts to analyze your reactor loading process.