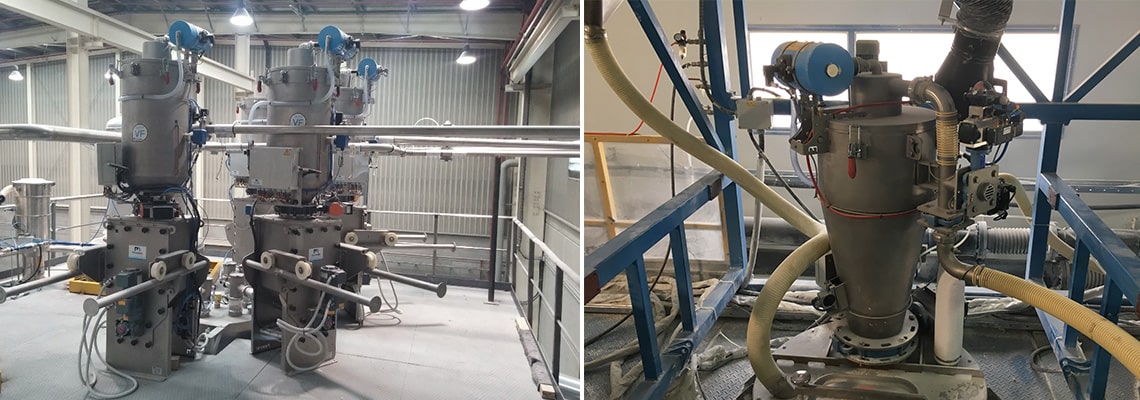
Industrial production plants in any industry, whether it be food, chemical, pharmaceutical or cement, need a means to move dry materials from one point of the process to the next. Manually transferring bulk ingredients is used, but can be very labor intensive and time consuming. This method is ok for small manufacturers with low daily output requirements, but for scaling up production, pneumatic conveying systems are a must. For the purpose of this article, we will learn about one of the most common types of conveying systems, pneumatic conveying by vacuum.
Vacuum conveying is the process of transferring powders and bulk solids, such as granules, flakes and pellets, from a feed point(s) to the next step of the industrial production line. The dry materials are conveyed in a network of pipes from the pick-up point to the downstream process.
1. How does a vacuum conveying system work?
Vacuum conveying uses the principle of negative pressure and air velocity to transfer materials through an enclosed pipe network. These types of industrial pneumatic conveying systems can be used in many production applications in the world of industrial manufacturing.
A typical vacuum conveying system starts with a blower pump, consider this the engine for material transfer systems. The vacuum pump will drive the conveyance of the bulk materials ranging from low throughput rates to high rates in the tons per hour, like powdered chemicals and plastic pellets for example.
To move materials from the feed point to the load point, conveyors utilize pressure differences caused by a vacuum. The bulk solids are pulled to one end by negative pressure and air velocity from the inlets. Dry materials perform better since the airstream from the conveyors entrain the particles in the air flow. One of the big benefits of using vacuum instead of positive pressure is that the chance for continuous accumulation of dust particles is reduced and largely prevented.
Another benefit of using vacuum over pressure conveying is there is less loss of material. For example, if the pipe network has a leak, it will pull the ambient atmosphere inward instead of expelling it outward, which in the later (pressurized line) would cause a dusty mess. Therefore, these types of pneumatic conveying systems are ideal for large applications where the materials are fed from silos, railcars, bulk bags, and other bulk containers (gaylords, drums, etc.). They offer energy efficiency, self-cleaning, easy installation and have a very small footprint compared to mechanical conveying solutions.
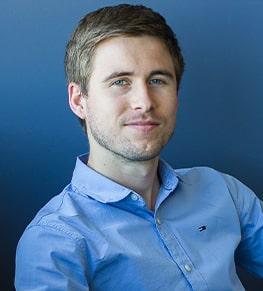
You are interested in implementing a transfer
system? I am available to discuss your project.
Mr. De Clercq, powder expert
2. Typical components of a vacuum material transfer system
The pneumatic suction consists of several elements:
- Vacuum pump: the engine of the pneumatic conveying system responsible for creating the negative pressure and air velocity to pull the material from the feed point to the collection cyclone.
- Cyclone separator: responsible for separating the conveyed air from the solid particulates being conveyed. A high-level probe is used to tell the PCL when the cyclone is full, shutting down the pump and material transfer. A filter cleans the air for safe exhaust to the pump, protecting the device in the process.
- Pipe network: a series of horizontally and vertically assembled pipes with bends to navigate around the production facility and connect feed points to discharge points. Multiple feed points are possible with vacuum conveying.
- Control system: A control system is always necessary for all pneumatic conveying systems and must suit the applications and the environment. In order to meet these requirements, the control systems can be wholly electrical or wholly pneumatic. They may also be a combination of these two systems brought together. These systems can incorporate various units of conveying that require independent control.
3. Batch transfer vs. continuous transfer
Equipment suppliers will need to know if you plan on a continuous conveying operation or a batch conveying operation.
Continuous material conveying applications are often used for uninterrupted transfer of the bulk materials to process equipment, such as continuous mixers or extruders. The cyclone is often fitted with a rotary valve to constantly dose the material as it is delivered.
Batch processes for pneumatic conveying applications involve the use of load cells and level probes on the cyclone and are often used for bulk filling processes, such as: bulk bags, FIBCs, drums, gaylords, etc.
Palamatic Process has several vacuum pneumatic conveying systems to suit your needs and process requirements:
- The VFlow® suction cyclone is a dense phase vacuum pneumatic transfer system. It allows material to be transported without deterioration and is particularly suitable for difficult products.
- The CementVeyor® pneumatic cement conveyor is specially designed for the long-distance transport of cement and other construction products.
- The MultiAshFlo® pneumatic conveyor is dedicated to the transfer of all types of ashes.
- The VF DEP pneumatic transfer with remote filter, which allows continuous recovery of the fine powders sucked in.