Processed powder: crystal sugar
Sugar dissolution for beverages
Company dedicated to the design of artisanal lemonade and artisanal syrup.
The customer wishes to manually empty his raw materials, which arrives packed in 50 kg paper bags with dimensions varying from 200 to 800 mm. Crystal sugar must be transported in dedicated mixing tanks.
Palamatic Process set up two manual bag emptying stations Sacktip®, with a bag manipulator to assist the operator in placing the bags on the dispensing table in an ergonomic way. Each bag dump station is independent and is equipped with a manually operated by-pass valve to divert the bulk material to the mixing tank.
The installation is built on two levels. The first includes the two bag dump stations with the bag manipulator, and the second the four mixing tanks (two tanks for lemonade and two tanks for syrup).
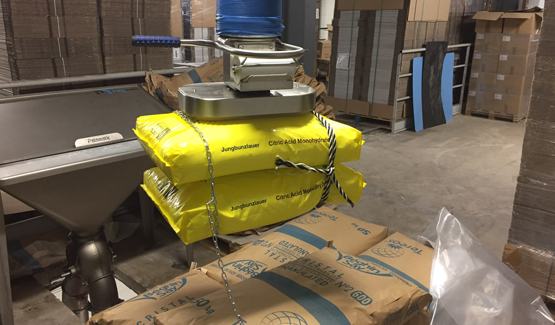
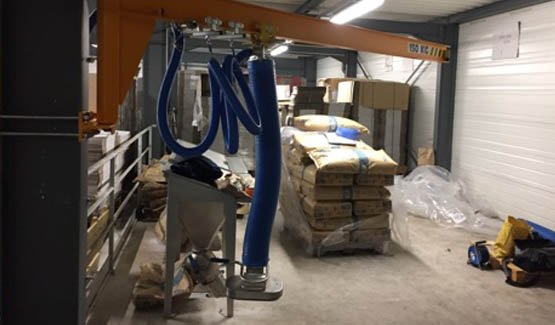
Two bag dump stations on syrup and lemonade processing line
The pallets of bags are positioned on the side of the sack tip trays: one for 50 lbs. bags and the other for 100 lbs. bags. In order to provide workstation ergonomics and easy handling, the operator grabs the bags using a bag manipulator. The vacuum head of the bag manipulator is equipped with a control handle with a barrel allowing the load to be self-stabilized at any height. The lifting tube offers a free rotation of 270°.
The operator positions the bag manipulator above the bag to be lifted and transferred. By lowering the control handle, the vacuum suction is decreased on the vacuum line and allows the bag to be lowered.
By raising the handle, the suction boot grips the bag and allows the bag to be lifted. Once positioned at the designated drop-off area, the operator positions the control handle as far down as possible to cut off the suction grip and release the bag on the Sacktip® bag dump station.
Once the manual cutting operation is completed, the operator shakes the bag and puts the empty bag on a pallet nearby. A dust extraction nozzle, with a flow rate of 470 CFM, is provided on the top of the machine for collection of dust particles. The access doors to the bag emptying stations are equipped with gas springs to keep them securely in the open and closed position, and facilitate opening.
The granulated sugar falls into the hopper of the bag dump station, which can hold 100 liters of water, and passes through a manually operated bypass switch into the two tanks (syrup or lemonade, depending on the bag dump station used).