The packaging of powders in bags, bulk bags, drums, silos and hoppers may lead to the powder caking. These storage methods can generate compressive forces with certain powders that have a strong tendency to settle and segregate.
The more sensitive the powder is to settling and deaeration, the greater the risk of forming lumps of product.
Several solutions exist to avoid the caking of your ingredients.
1. Agglomeration by compression
Before de-agglomerating your powders, you can integrate solutions in your storage hoppers to avoid settling. The settling of powders is, in the majority of cases, due to the deaeration of the powder particles. The air trapped between the particles can, over time, escape via the compression effect and segregation. The finer particles tend to settle at the bottom of the silos filling in the air gaps. The powder then becomes compacted, and its flowability becomes extremely low. Thus, for powders with a large particle size distribution, storage in suitable hoppers is essential. Some agglomeration can be caused by other factors such as thermal variations or exposure to moisture and humidity.
To avoid powder compression aeration solutions can be implemented. Palamatic offers fluidization solutions by nozzles, plates or double wall designs. The installation of these options in your storage hoppers provide a programmed injection of air in the lower sections. The injected air can have the necessary characteristics: neutral gas, zero humidity, temperature, HEPA filtration, etc. Refer to our pages dedicated to vibrofluidizers to select the model compatible with your silo or contact our teams to obtain personalized advice.
Before vibrating, aerating, heating, fluidizing, impacting or even agitating your hoppers and silos, contact our powder handling experts to define the solution to your compaction problem.
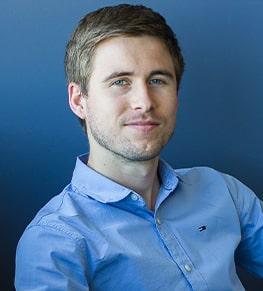
Are you looking for a solution to prevent your
powder from settling? I am available to assist you.
Guillaume, powder expert
2. Agglomeration caused by temperature variations
For this scenario, solutions for insulation and heating of the hoppers are offered by Palamatic. Jacketed tanks heated by coil or by heated fluid transfer can provide the solution. Also, when the packaged powder leaves the manufacturing process at a high temperature, it is important to "accompany" the drop in temperature of the product. The best example are the atomization tower outlets which incorporate fluidized beds.
The alternative to fluidized vibrating beds is the agitation of the hoppers by a threshing paddle. The agitated hopper keeps the product in motion during its "descent" in temperature, thus allowing the calories and humidity to be released freely. This threshing hopper technology is particularly used in sugar grinding processes. Anti-bridging solutions are also developed by Palamatic.
In order to avoid any problem with the flow of your material, upstream tests can be carried out in our powder laboratory to study its particle size. Palamatic Process also has a test station where full-scale tests can be carried out on our equipment.