Automatic ingredient dosing unit with common weighing system
The DosingMatic® Shuttle automatic dosing unit provides successive ingredient weighing by automatically moving the scale under each feeder. The weighing scale is motorized and positioned on a horizontal rail to allow correct positioning under the dosing mechanism called for by the batch recipe and PLC.
Up to 14 of feeders can be utilized by the mobile scale in order to maintain a consistent feed rate.
- Automated batching solution
- High dosing accuracy: 5 grams
- Expandable number of dosing lines
- Optimized weighing cycle time
The preparation of premix batches is a crucial step in ensuring the quality of finished products and blends. The preparation and dosing of premix ingredients is a repetitive, labor-intensive and conscientious process.
The use of the DosingMatic® Shuttle unit enables production plants to equip themselves with an automatic weighing line, which can adapt to the different powders and ingredients being handled, as well as a scalable dosing line.
DosingMatic® Shuttle
DosingMatic® Shuttle 10 |
DosingMatic® Shuttle 14 |
DosingMatic® Shuttle 20 |
DosingMatic® Shuttle 28 |
DosingMatic® Shuttle 40 |
|
---|---|---|---|---|---|
Dosing system | 10 | 15 | 20 | 30 | 40 |
Load cells | 1 | 1 | 2 | 2 | 4 |
Time per batch | 60 s | 80 s | 60 s | 80 s | 60 s |
Power Kw | 18 | 24 | 35 | 47 | 65 |
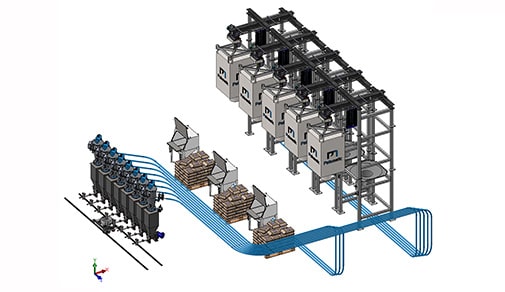
The feeders installed with the DosingMatic® Shuttle skids integrate special technologies to adapt to the powders being handled. Fragile products, or those with large particle sizes, are dosed by vibratory feeders. Fine powders are dosed by single or twin-screw feeders, depending on the precision required, with interchangeable screw profiles. Agitators can be integrated into the screw feeders to ensure even extraction of ingredients with poor flow properties.
Weighing management
The weighing operation is handled by a mobile scale mounted on a rail-mounted cart. A hygienic belt and guide rails ensure the scales back and forth transfer. The belt motor positions the scale under each feeder by the recipe being prepared. The scale is positioned with millimeter precision under the filler, enabling the mobile weighing unit and filler to be connected via clamping.
ontainment is provided via a tulip seal and dust removal in the ingredient preparation area. Weighing accuracy is guaranteed to +/- 5g.
Automation management
The weighing scale integrates a conveyor belt to receive the collection container (tub, bucket, bag, barrel, etc.). It can also evacuate it to a second dosing unit, or to the evacuation conveyors for labeling, sealing or manual dosing.
1 single operator for thousands of batches!
Thanks to the DosingMatic® Shuttle automated dosing unit, only one operator is needed for complete premix production. The operator is present only to replenish the feeders with raw materials and for the placement of the collection containers. The operator is no longer responsible for correct weighing and product selection.
Use of the DosingMatic® Shuttle skid guarantees impeccable premix quality in compliance with the production order standards, and ease of use for your line operators.
Automation
Palamatic Process provides automatic control via the latest PalTouch® PLC technology. All your recipes are integrated and linked directly to your production management IT tool. Recipe traceability (date, precision, weighing, flow rate, etc.) is stored and can be transferred to your supervisory systems.
Our teams of automation engineers are available throughout the project and the life of your installations to optimize and configure the control of Palamatic Process batching units.