
Lump Breakers (also called powder crushers or granulators) are commonly used in the powder and bulk solids industry for improving the flow characteristics of dry materials. This manufacturing equipment is typically made up of a square or rectangular housing unit with external drive and internal blades / knives attached to shafts. Surrounding the blades is a fixed grid that allows the impact of large lumps of material against the rotating mechanisms.
The operation of the lump breaker offers high torque and low RPM’s to effectively break up larger agglomerates for handling downstream. The fixed grid helps offer a basic means of powder classification, allowing the free-flowing particles to pass right through the machine while holding back larger lumps for further breakdown. Let’s explore common applications for lump breakers and powder crushers.
1. Deagglomeration after prolonged storage or transport of materials
Oftentimes dry bulk materials can become compressed while in storage. Common examples are super sacks, rail cars, silos, IBC’s and Day Bins. As material sits in storage, particle segregation and densification naturally occur as finer materials find their way to the bottom and large particles stay on top. The process causes air pockets between the particles to collapse and over time, compression lumps form.
Furthermore, these containers can be exposed to high levels of humidity or possibly moisture. Exposure to moisture can also form hard lumps that take more energy to tease apart. Therefore, many manufacturers will install lump breakers, or powder crushers, directly underneath their silos and bulk bag unloaders to help condition the material and break down larger lumps. Sugar processes oftentimes rely on this type of conditioning equipment to help break up larger masses of the material back down to its granular state again.
Another common use for lump breakers is directly underneath a bag dump station. When 50 lbs. sacks are palletized and transported to another facility, that allows enough time for certain powders to become compacted. Operators can simply dump the contents of the sack into the bag dump station and the powder crusher will condition the material for the downstream process.
2. Preparation for conveying lines
If material tends to agglomerate during storage, it makes sense that conveying the product from point A to B would be difficult and inefficient. If your plant utilizes pneumatic conveying, whether it be dense phase or dilute phase, pressure or vacuum conveying, you will lose efficiency in your conveying line or have a total block within the pipe work. In order to move material using pressure conveying or vacuum conveying, your material needs the right air to particle ratio (depending on the type of conveyance and the bulk density of the powder). Feeding larger agglomerates interrupts the air to powder ratio mix and therefore can cause a dramatic reduction in your throughput rates. Even mechanical conveyors (screw conveyors, belt conveyors, vibrating conveyors, etc.) need a material with decent flow properties and a somewhat consistent particle size distribution. Rotary airlocks can be used to help meter the feed of powder at a consistent rate into pneumatic conveying lines. Feeding large, hard lumps into a rotary valve may cause equipment failure.
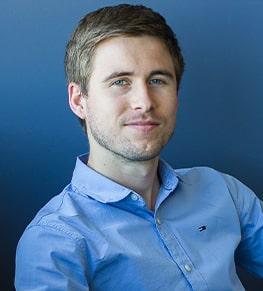
You have a project? I am available to advise
ou and accompany you in your study.
Guillaume, powder expert
Any type of feeding and conveying equipment for bulk materials requires a conditioned dry powder. Screw feeders, vibrating feeders, rotary valves, all benefit from a powder that is free of clumps. Powder feeding equipment is best suited for accurate dosing and metering of powders. This equipment is often used in final commercial packaging for end users. Therefore, accurate dosing by weight or volume is a must. Dosing clumps of material causes inefficiency in the performance of the feeding equipment, if the powder does not have a consistent flow rate. Over or under feeding can occur due to lumps throwing off the accuracy of the weight to be dosed. Again, pre-breaking your material will benefit almost every single step of your production process.
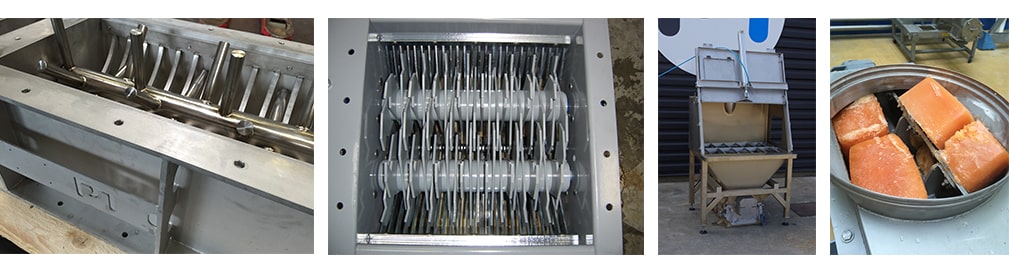
3. Pre-breaking prior to value adding equipment processes
Another stage of controlling your production quality is screening equipment. Take for example salt, which when exposed to moisture can form a brick-like lump. Feeding this into a screener can cause damage to the screen mesh and maybe even the powder sieve itself. The same goes for granulated sugar and some powdered chemicals. Screeners serve several purposes such as: scalping oversize particles off the top end of the distribution curve, policing the production line for foreign objects (quality control) and dedusting finer particles off the bottom end of the curve.
What they cannot handle (typically) is larger agglomerates that cannot be teased apart easily. The same principle applies to milling and mixing equipment. If you feed powder into a mill for particle reduction and value adding, the mill will lose its efficiency in its output if the powder is not of a consistent nature. Also, the mill will use more power over time as it is being overworked to break down larger clumps it may not have been originally designed for (causing unnecessary equipment wear and possibly failure). Trying to mix lumpy powders never gives good results. Another example is spice blends and instant food mixes. Mixing powders that contain lumps will result in batches that have inconsistent flavor profiles. This can be detrimental to sales for products that are direct to consumers (pancake mixes, dry rubs, instant bake recipes, etc.)
Powder conditioning, de-lumping, pre-breaking, etc., is a critical component of every top-level production process. Better equipment performance, consistent results and production efficiencies heavily rely on materials that have both consistent make up and free flowing properties.
Since 1992, Palamatic Process has provided equipment to 2000+ installations in over 30 countries. We offer knowledge and expertise in all manner of powder and bulk automated material handling needs. For more information on our lump breakers, contact one of our experts for assistance with material handling solutions and to request a quote.