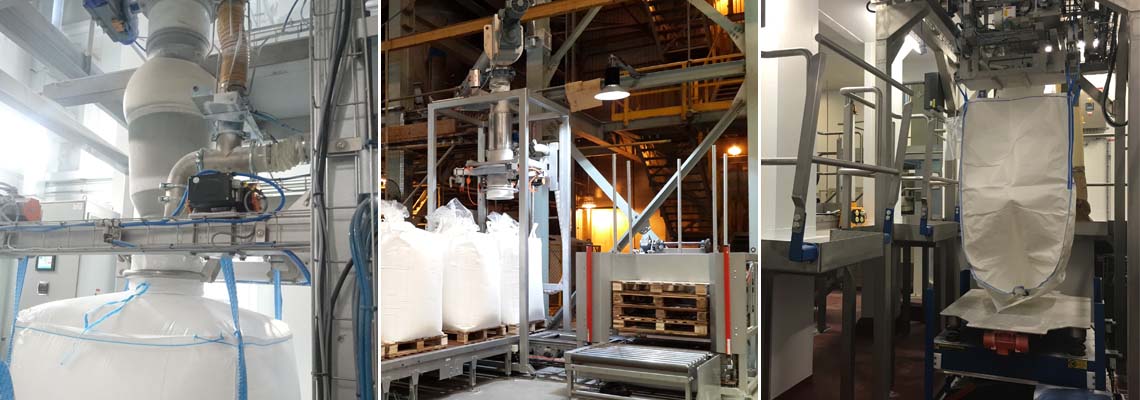
In most industrial applications, there are two main reasons that motivate a manufacturing facility to invest in an automated big bag filling station. Of course, we must leave room for the various production nuances but the two main objectives always boil down to:
- Minimal operator intervention
- Increase in product demand / increased output goals.
Let’s look at the basic building blocks for the implementation of a successful high-rate big bag filling system.
1. Weighed Buffer Hoppers
Arguably the most critical component of a high-rate big bag filling system is the weighted buffer hoppers that feed the station. Buffer hoppers are used to temporarily store powders, flakes and granules in order to achieve an accurate and controlled feed of your powder production system with a greater degree of efficiency.
Most common components used on a weighted buffer hopper are high level probes, low level probes and load cells. Level probes are used to tell the upstream conveying system when the hopper is full of the bulk solids, or when it is empty and calls for the conveying equipment to transfer more powder and fill the hopper.
In order to achieve an accurate and automatic filling weight in the big bags below, load cells are installed under the supports for the hopper. Load cells are typically used in systems that feature gain-in-weight (GIW) or loss-in-weight (LIW) functionality.
Load cells communicate with the main control board that the targeted weight of material has been accumulated in the hopper. In an automated filling system that requires high output rates of packed big bags, dual gain in weight buffer hoppers will work in sequenced time..
When weighted buffer hoppers are installed side by side and feed into the same FIBC filling station, the first hopper with the prepared material can discharge into the big bag while the second hopper is being filled.
By working in this manner, the big bag never needs to wait for the hopper to refill as there is always one ready. Weighed buffer hoppers are typically sized according to the material’s bulk density and the capacity of the big bag to be packed. Butterfly valves or slide valves are typically installed on the powder discharge outlet to control the flow of the dry powder from the hopper.
Other integrated components include flow aid devices such as vibrating motors, air jet nozzles, pneumatic hammers, etc. to help prevent rat-holing or bridging issues with powders that tend to have difficult flow characteristics.
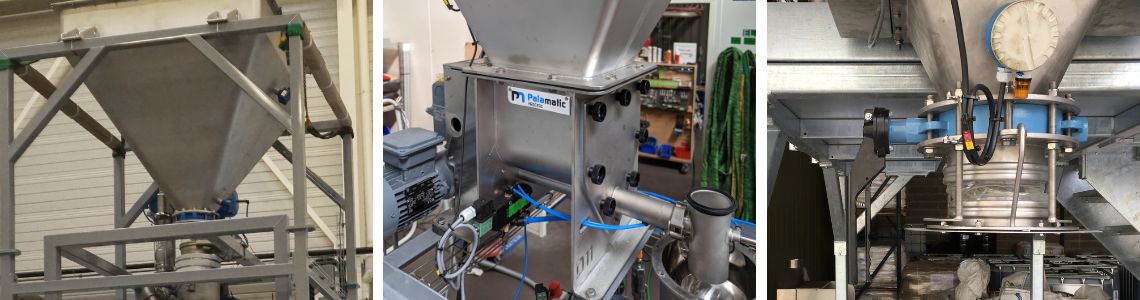
2. Powder Flow Control and Dosing Equipment
Another critical component for achieving high big bag fill rates is how the powder is handled and controlled once it leaves the feed hopper from upstream.
As previously mentioned, typically either a butterfly valve or a slide valve will be used as the main on and off flow control valve for the powder.
From that point, as the powder falls down a gravity connection chute to the filling station below, it can be diverted through one of two channels. The primary channel is the high-rate flow channel, often further fitting with butterfly valves just above and below the channels.
As the target weight of the big bag nears 95% volume, the butterfly valve at the top of the high flow column closes and diverts the powder to a screw feeder. Screw feeders are a type of powder dosing equipment specializing in providing repeatable accuracy of the materials to be dosed. On their own, screw feeders use a built-in hopper with stirring agitator that flood feeds a tubular channel. Within the tube is a small screw that pushes the product through an outlet into the downstream process. There are several designs for the small auger within screw feeders such as: pigtail screws, ribbon screws, and screws with a drive shaft. However, when integrated into a big bag filling station, it is typically just the tubular channel and auger that precisely feed the powder into the package downstream. Screw feeders offer a good deal of precision, in some instances dosing at an accuracy of -/+ 1-2 grams.
They are a common type of feeder as they fit most applications, except in instances of materials that are friable or heat sensitive. Another type of powder dosing system that can be used is a vibrating feeder. Vibrating feeders utilize shaker motors and the structure is supported by spring coils which allow the unit to vibrate. The trough has a minimal angled slope that allows the unit to shuffle the material down the feed bed into the downstream process.
The feed rate can be controlled by increasing or decreasing the vibration amplitude and frequency. This type of powder feeding device is good for preserving the integrity of the product, or avoiding unnecessary wear and tear in the case of abrasive materials. Powder feeders will run for the last 5% of the powder fill target the big bag requires. By utilizing a split feed device like the one described above, automated fill systems can quickly and efficiently fill big bags with precision.
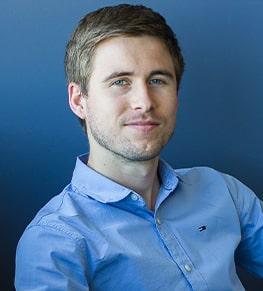
Do you have a bulk bag packaging project? I am available to
advise you and accompany you in your study.
Guillaume, powder expert
3. Dust Containment and Control
One of the most necessary pieces of equipment for any industrial production facility is dust collection and filtration. It is also critical that all material handling equipment be designed for dust-tight operation. It is imperative that no matter what you do, all production equipment is designed to contain the powders being processed. If this is not carefully taken into consideration the results could be catastrophic for any facility. Reasons for this include: material toxicity and human exposure, slip and fall accidents due to powder and dust all over the work station area, mechanical failure of equipment, air to dust mixture ratio resulting in an explosion, etc.
There are several types of dust collectors to consider:
- Centralized dust collection systems for all production equipment. This includes: fabric filter baghouses, inertial separators (like mechanical cyclones), wet scrubbers, cartridge collectors, and electrostatic precipitators.
- Equipment specific integrated dust filter units: an example would be a built-in dust filter on top of a bag dump station
- Hopper venting filters
- Suction booths
- De-dusting rings (also called Pouyes rings): an example would be on top of a storage tank where operators manually feed bags of powder (manway port).
Dust collection units typically have either side mounted or top mounted filter cartridges. These filters are connected to an external compressed air tank that is set to a timer cycle. As dust passes through the filter an intermittent blast of air is sent through them from the opposing side to clean of excessive dust build up. This reverse jet pulse cleaning system does two things:
1. It keeps the filters from clogging without need for maintenance
2. It helps reclaim product lost to the filters.
Other methods of dust containment include seals and connection types. For big bag filling, it is important that the connection between the fill head and the big bag inlet spout be secure and dust tight. A common method used is an inflatable bladder on the fill head. The operator takes the big bag fill inlet and places it around the elastomer gasket. Pressurized air is fed into the bladder causing it to swell and firmly secure the big bag spout.
The fill head can also be double jacketed (an inner tube surrounded by an outer tube). The inner channel allows the material to pass through and into the bag while the outer channel allows air and very light dust to escape through a connection piece that can be fitted with a filter sock or a hose that connects to a central baghouse.
In production outfits that deal with particularly toxic materials, for example lithium powders in the battery manufacturing industry, the entire installation can be surrounded by an enclosure that is designed to pull a constant atmospheric vacuum to an outside dust collection system.
4. Vibrating Densification Tables and Load Cells
One of the most common problems with transporting and storing big bags filled with powders and granular materials is issues with stability. Ask any production operator that handles big bags how frustrating it can be to have a big bag start to tip over on its own and end up falling on the floor, spilling a ton of material everywhere. More often than not, the root cause of this is due to the particles of powder being too loosely packed during the filling operation.
As material settles on its own accord, it can cause particle segregation where all the fine powders fall to the bottom and all the larger particles stay on top. This can cause the bulk bag to begin to sag and tilt to one side, causing instability in moving it around or stacking them on top of each other during storage. Vibrating densification tables are a necessary component of any semi-automated or fully automated big bag filling production line. They utilize shaker weights and spring coals under the table the big bag rests on during filling. As the big bag fills with the bulk material, the densification table will intermittently vibrate. This disturbance allows the small air pockets between the particles to escape, which then provides closer packing of each granule. Now particle segregation is more unlikely to occur naturally and the bulk bag is more stiff and rigid, capable of stacking and transport by truck or rail.
Also as equally important, a small device called a load cell. A load cell is a force transducer. It converts a force such as tension, compression, pressure, or torque into an electrical signal that can be measured and standardized. As the force applied to the load cell increases, the electrical signal changes proportionally. The most common types of load cell used are strain gauges, pneumatic, and hydraulic. Load cells are connected to a PLC that reads how much weight is going into a bulk bag during the filling sequence.
A target weight is programmed into the control panel and as the load cells read the big bag is near the finished amount, it will cause the PLC to send a signal to the powder dosing unit (screw feeder, rotary valve) to slow down and trickle the last 5% of the target weight. When the target weight is complete, the load cells signal the PLC which tells the powder valve to close and stop filling. By using load cells, we can automate the filling sequence with no need for operator intervention, and achieve a very accurate fill weight.
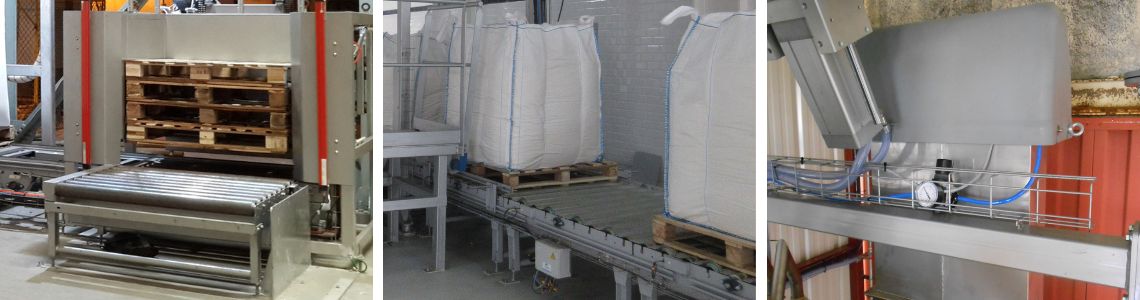
5. Pallet Feeder and Mechanical Roller Conveyor
The last two critical pieces for automating your FIBC filling line are pallet feeders and mechanical roller conveyors. Pallet feeders, or pallet unstackers, utilize robotic indexing arms connected to pneumatic cylinders that can raise, lower and push a pallet onto a fill station. They typically hold up to 15 pallets at a time, but can be customized to hold up to 20. The performance is feeding one pallet every 35 seconds and can be designed to accommodate various pallet dimensions. Every time a big bag is finished filling, the PLC can tell the pallet feeder to push the next pallet in line out onto the mechanical roller conveyor.
Mechanical roller conveyors have a few different functions but are mainly used in this instance, to transfer pallets to the fill station and then the filled big bag on the pallet to a temporary buffer area where a forklift operator can take it to a more permanent storage area. All of the timing and sequences are controlled by the PLC, so all of the guess work or manual labor is taken out of the equation. Roller conveyors are often designed as a tubular framework that supports steel rollers in between them. The rollers are spaced equally a part and are driven by a laterally located gear motor, or by gravity on a minimal sloping angle. With gravity roller conveyors, there are speed regulating rollers that are used to control the speed of the object that is being conveyed. Regardless of the type, roller conveyors and pallet feeders work in sequence to provide a constant high-rate supply of bulk bags to and from the filling station.
With these features, bulk bag filling operations can minimize the requirement for having too many operators tied up on one work station.