The depollution of fumes from thermal power plants is a major challenge for any thermal process operator. The method used to treat power plant emissions is done depending on the product for the pollution control technology chosen.
1. Depollution objectives and their impact
Globally, committees are setting targets for reducing or limiting emissions from thermal power plants. These targets are ambitious and robust, particularly in Europe where directives set limit values not to be exceeded. They also set maximum concentration targets that need to be achieved within a certain time frame.
Thermal power plants now account for a significant share of greenhouse gas emissions. Usually nitrogen oxides, sulfur dioxide, carbon dioxide, dust or even heavy metals.
Industrial power plants can be sorted into three groups:
- Industrial recovery plants such as incinerators. These factories transform everyday waste into energy, used regularly in urban heating networks.
- Thermal power plants producing electricity or steam such as coal, fuel oil or solid recovered fuel (SRF) power plants. These industrial units transform their oxidizer into steam which can be used in its natural state, or, transformed into electricity.
- Thermal manufacturing plants such as cement plants. These industrial plants are used in processes requiring a direct heat source at one stage of its production.
Thermal power plants must continuously improve their environmental footprint.
2. What methods should be used to reduce emissions from a thermal power station?
To reduce pollutant emissions, it is possible to act on three production stages:
- Fuel: using a less polluting and better quality source (except in the case of incinerators).
- Combustion: using more efficient technologies and emitting fewer emissions.
- Flue gas (or flue gas scrubbing): to get rid of the pollutants contained within it.
Depollution remains the most universal way of reducing emissions into the environment.
3. How to decontaminate thermal power plant discharges?
There are three main groups of flue gas pollution control processes: wet, dry or semi-wet. The semi-wet process is a mix of the first two and has great advantages but requires pre-treatment of the dust.
Dust treatment
Dust can be treated via two methods.
- Filtration of fumes can be done with a filtering media, such as in a dust collector or in a wet filtration system.
- Dust removal can also be carried out by simple cyclone separation. The fumes pass through a suitable cyclone where the dust falls to the bottom of the receptable, and the lighter smoke passes through the top of the cyclone.
Removal of dioxins/furans
Dioxins and furans are toxic chemicals found in very small amounts in the environment. There are 210 different dioxins and furans.
These substances must be removed from the fumes emitting from power plants. They are treated by injecting powdered activated carbon into a saturation chamber causing an adsorbtion effect of the dioxins. Adsorption is a surface phenomenon by which molecules of gas or liquid attach themselves to the solid surfaces of adsorbents.
Activated carbon is delivered in bulk bags or in bulk loads (tankers, rail cars, etc.). The carbon powder is then stored in silos and transferred via a pneumatic conveying system where it is injected directly into the flue gases that need treatment.
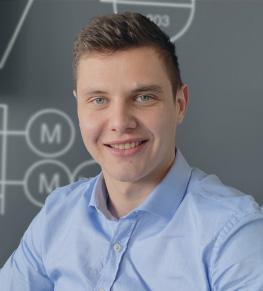
Are you looking for a solution for smoke abatement?
I am available to discuss your project.
Loïc, powder expert
Sulfur remediation
During the treatment of combustion gases, the sulfur is treated with soda or lime. The lime can be in the form of milk of lime or dry lime. Lime milk also has the function of increasing the humidity rate of the fumes and thus reducing their temperature. Flue gas depollution occurs because lime easily absorbs acid gases (fluorine, chlorine and sulphur). As the lime dries, it falls into a pile of dry powder and allows easy elimination of these pollutants. Milk of lime is made by an industrial process of mixing slaked lime and water. Lime can be dosed from a silo or directly from super sacks.
DeNox of industrial fumes
The fumes from thermal power plants also contain nitrogen oxides or NOx. Emissions of this powerful greenhouse gas must be kept to a minimum. The treatment of Nox, or Denox, in fumes is commonly carried out by injecting urea directly into the fumes. Urea is an ammonia derivative that can easily be made from an industrial urea manufacturing process. The process involves urea prills that are dissolved in pure water.
Depollution of halogenated, volatile heavy metals
Industrial fumes may contain halogen particles and heavy metals. These compounds are treated with neutralizing agents:
- Injection of lime into the flue gases (see sulfur depollution above)
- Injection of sodium bicarbonate (formerly called "bicarbonate of soda") for the recycling of fumes. Sodium bicarbonate requires special preparation. Raw product storage silos must be installed as well as a crushing skid comprising an industrial grinder. Grinding sodium bicarbonate allows it to obtain the required reactivity.
- Injection of powdered activated carbon to reduce emissions into the ambient air.
4. Focus on the DeNox of industrial fumes
As indicated above, nitrogen oxides are treated by injecting urea into the flue gases. There are several types of processes.
Types of DeNox
- SNCR (Selective Non-Catalytic Reduction): mainly used in cement factories and incineration plants because it is very simple to implement. In this system, urea is injected directly as a spray into the fumes at 900°C. This system allows 40-60% reduction of Nox.
- SCR (Selective Catalytic Reduction) is used in power plants or electricity production plants. This technology is called low temperature heterogeneous catalysis. The efficiency can, in this case, rise to 95% of DeNox. However, the technology requires the fumes to pass through a more complex honeycomb system to optimize the reaction.
In all these cases, solutions of urea or ammonia are used. Depending on the application, we will use:
- AdBlue® for combustion with diesel
- Marine Urea for Offshore applications
- DEF (Diesel Exhaust Fluid) for automotive applications
- of the 40% Urea Solution for the treatment of industrial fumes
- a 32.5% urea solution which actually corresponds to the AUS32 of the ISO 22241 standard. The ARLA32 or ARLA 40 as it is called in South America.
5. Palamatic and the depollution of smoke from thermal power plants
Palamatic Process is a specialist in the handling of powders and solutions in the field of recycling and treatment of fumes. We intervene throughout the process to advise and support you in your flue gas treatment project.
We can also provide tailor-made process lines in the broad field of environmental management.