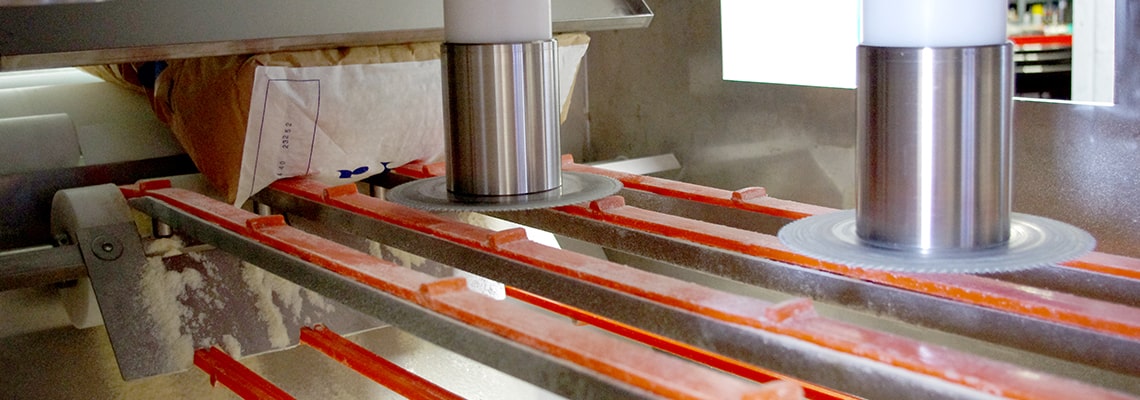
Bag dump stations (also known as sack tip trays) are a very common piece of material handling equipment in production plants for various industries. You may think that if you have seen one bag dump then you have seen them all. One cannot be blamed for this, however, there is actually a fairly wide range of designs and functionalities when it comes to the simple need to unload your minor ingredient sacks into your downstream conveyor system.
Here are a few questions to ask when sourcing this type of bulk material handling equipment.
1. What is the required per minute / hour rate for unloading your ingredients?
There are a few ways to come up with a targeted material unloading rate for bag dump stations. First, you could look at it from just a pure quantity perspective.
How many sacks do you want to unload per minute? Many operations do not require high volumes of these smaller, minor ingredient sacks to be dumped into a downstream process. Often times an operator only needs to unload maybe 1-2 sacks per minute (or even less). In these instances, Palamatic Process can supply a very simple and manual sack tip tray just to contain any potential spills or unwanted dust in the environment. However, another way to measure the required throughput is by the weight of the ingredient sacks and how much overall material needed to feed per minute / hour. For example, a common weight for these ingredient bags is 50 lbs. Perhaps your process requires moving about 15,000 lbs. of material per hour. Now your sack tip tray equipment needs the ability to unload five (5) 50 lbs sacks per minute, not an easy thing to achieve with a basic manual dump station.
Therefore, you need to look at some type of semi-automated or even fully automated station that can cut and unload sacks at higher rates. Palamatic Process offers bag dump stations with built-in cutting blades and conveyor systems that can help increase the rate at which you unload your materials.
2. How much operator intervention is needed (or wanted)?
There is no doubt that the manufacturing industry is moving more towards automation. Of course, nearly every equipment supplier out there has an answer to manually loading and dumping sacks of material. As plants look to upgrade their old material handling systems, or even invest in new manufacturing sites, there is a rising demand for equipment that requires minimal operator intervention. Palamatic Process offers several different versions of fully automated bag cutting and dumping stations. One of these heavy duty solutions is called the Minislit®, which is capable of processing up to 8 sacks per minute.
The Minislit operation sequence:
The sack is loaded onto a motorized inclined belt conveyor or horizontal roller conveyor, the sack is fed through the inlet of the station, sensors inside the equipment detect the presence of the bag, a band saw is lowered and cuts three sides of the bag, inversion discs grab and pull the bag downward releasing the contents to the discharge hopper below, the sensors indicate the evacuation of the bag and the band saw stops and retreats into its rest position, the spent sack is dropped into a compacting auger screw where its pressed into a polyethylene sheath for containment and removal.
Further options can be added to assist with the efficiency and safety of the process, such as: vacuum sack lifter for loading assistance, integrated dust collection for a cleaner environment, vibrating discharge hoppers to promote material flow, and a bag breaker to help assist with compaction of the material while stored.
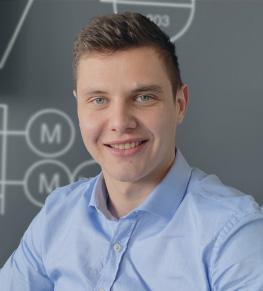
If your require further assistance,
I am at your entire disposal.
Loïc, expert in powders
3. Does your process require hygienic design and sanitary practices?
Perhaps you are in the dairy or food industry and therefore require equipment that is designed to meet the rigorous food-grade standards these types of production plants require.
Palamatic Process can design equipment from any type of steel fabrication: mild, 304 or 316 stainless steel. Design details such as radial welds, polished fine grit or mirror finishes and passivation often lend themselves to how much modification an equipment supplier needs to consider.
Our sack tip trays can even accommodate CIP washdown design to quickly sanitize the station between product batch runs. Perhaps you need to do a quick quality control check by sieving your powder as you dump the sacks into the station. It’s part of our standard design options to integrate a vibratory sieve screener to help catch any foreign contaminants and classify the size of your powders. It’s always good to know the check boxes you need to run down on meeting hygienic design requirements for your specific production process.
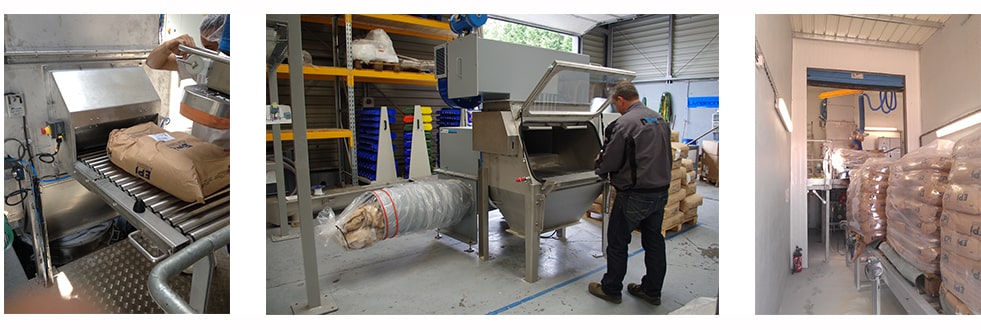
4. Is your material considered toxic and potentially dangerous for exposure to your operators?
Often times production outfits require handling hazardous materials such as active pharmaceutical ingredients, lithium for battery production, etc. In these instances, careful consideration must be taken into account when designing equipment to prevent human exposure. Our bag dump stations can be outfitted with glove boxes to allow manipulation and unloading of the sack while maintaining a physical, dust-tight barrier between the operator and the material. Full dust containment is possible when further integrating a dust filtration unit directly above the hand add station. As for the spent sack material, Palamatic Process can also design a bag compactor directly into the station. The operator only needs to toss the waste sack into a side port and an auger screw will compact the it into a contained polyethylene sheath. With all these features integrated into a sack tip tray, all residues and dust are fully contained and your workers kept safe.
With 29 years of powder processing and bulk material handling experience, Palamatic Process can offer the right solution for your production requirements. We can design full turnkey systems by offering pneumatic conveying systems, belt conveyors, screw-conveyor, roller conveyors, bucket elevators, vibrating feeders, etc.
Contact one of our friendly staff to discuss your project in detail, and together design the perfect solution for your manufacturing goals.