Description
Semi-AUTOMATIC BAG DUMP - SAS® - Semi-Automatic opening with respect of fragile materials and small dimensions
Max rate: 2 bags/min.
Steel or stainless steel manufacturing
A semi-automatic bag dump solution ideal for food, pharmaceutical and chemical applications. This machine minimizes the operator's gesture and guarantees a dust-free working environment.
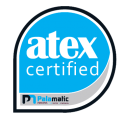
To establish a connection between the manual bag lifter and the automatic bag lifter, Palamatic Process offers the SAS® bag emptying station which has a semi-automatic bag deconditioning system. It is ideal for food, pharmaceutical and chemical applications where mixing processes are frequent. This machine limits the operator's action to a simple bag placement and guarantees a dust-free working environment.
-
Rate2
-
Overall dimensions5
-
Hygiene4
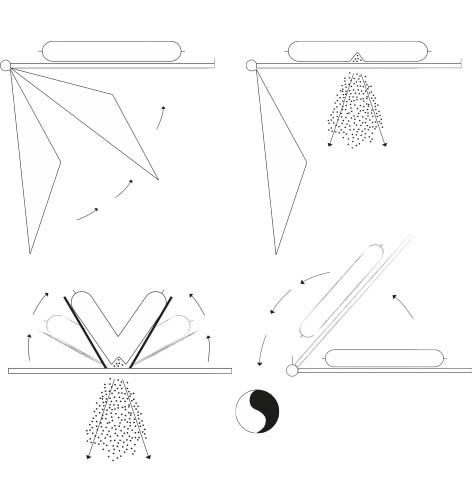
Operation procedure:
1. Open the door mounted on gas cylinders, place the bag on the removable table and close the door
2. Lower of the holding bar and open of the bag with the automatic cutting blade
3. Discharge of the bag using the shaking bars
4. Evacuate of the empty bag through the ejector bar to the bag compactor, which ensures that the waste is contained in a contained sheath
Equipment advantages
- Pneumatically controlled cutting system
- Ideal solution for explosion-proof areas
- Dust free environment
- Available with the "Cleaning In Place" (CIP) option
- Stainless steel finish, mirror-polished interior (optional)
Media
View our equipment in videos
Semi automatic sack discharging station SAS®
This bag opener allows automatic opening with respect of sensitive materials and has small dimensions.
View our equipment in photos
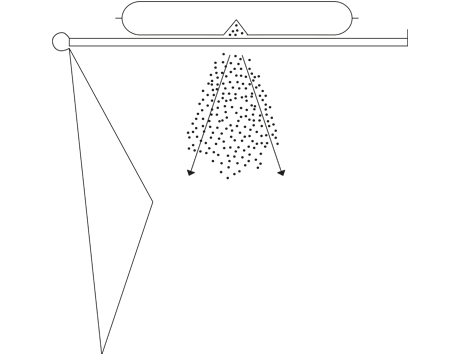
Operating principle
The blade pivots from the back to the channel in the screen and cuts the bottom of the bag.
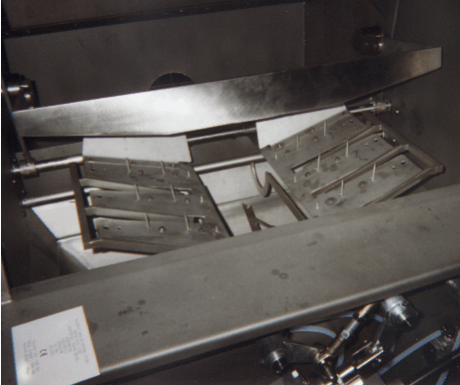
Internal mobile parts
Internal moving parts of the machine for shaking and ejecting bags.
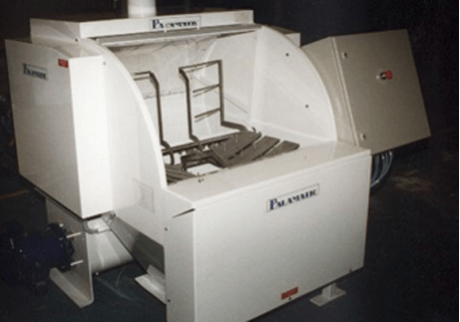
Semi-automatic sack discharging system
Semi-automatic SAS bag dumping unit, small dimensions.
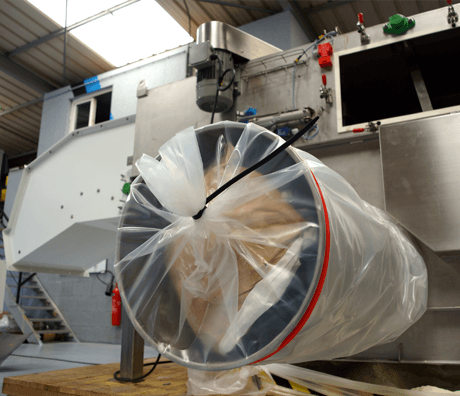
Compactor
Bag dump station with compactor for empty bags.
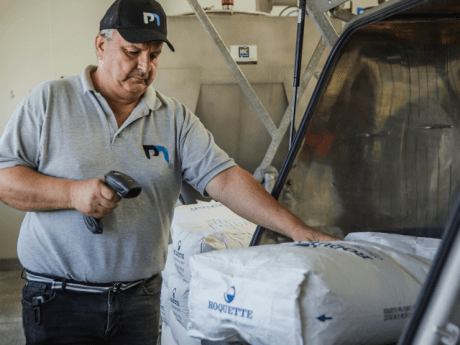
Bag tracking
Traceability of the batches used for the safety of your process.
Features
Technical specification
Rate | 2 to 6 sacks/min. |
---|---|
Capacity | 15 to 50 kg/sack |
Manufacturing materials | Painted steel, 304L stainless steel, 316L stainless steel |
Compressed air consumption | 35 Nm³/h. |
Dust removal rate | 800 m³/h. |
This machine is designed for the semi-automatic opening of all types of bags (except aerosils) by limiting the operator's gesture to a simple placement of the bag. The degree of containment of the machine working with the door closed, the installation of a bag compactor and the connection to the dust collection network limit the emission of fines into the atmosphere as much as possible (a dust collection unit is available as an option). It guarantees working in a dust-free environment and without the need for manual bag cutting.
Electric powers | |
---|---|
Bag infeed conveyor (optional): | 1.5W |
Cutting head drive motor: | 1.5kW |
Compactor and internal conveyor: | 2.2kW |
Fan motor (optional): | 1.5kW |
Vibrating motor (optional): | 0.25kW |
The machine is supplied with a complete control cabinet to ensure the requested output.
Integrated equipment:
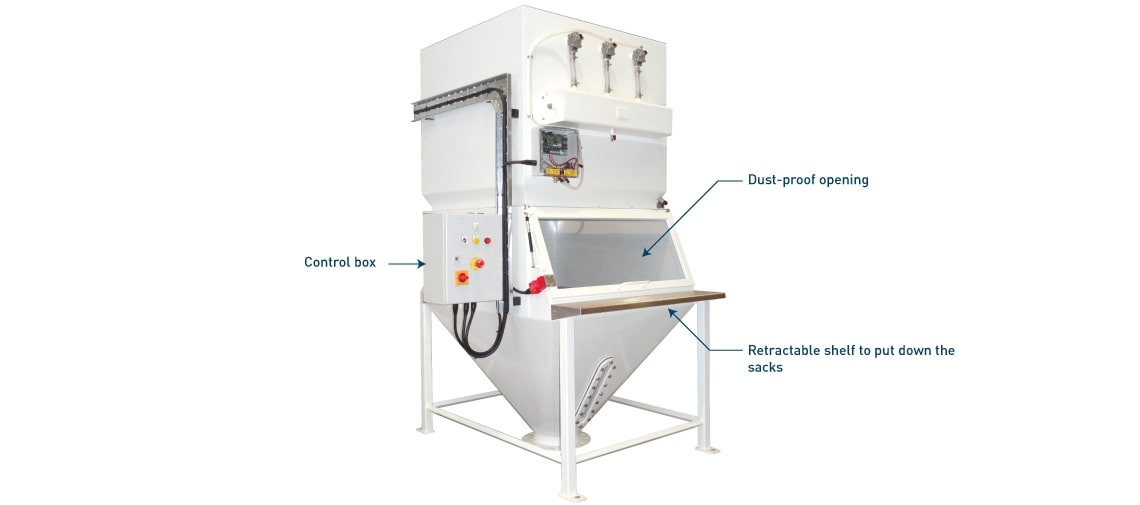
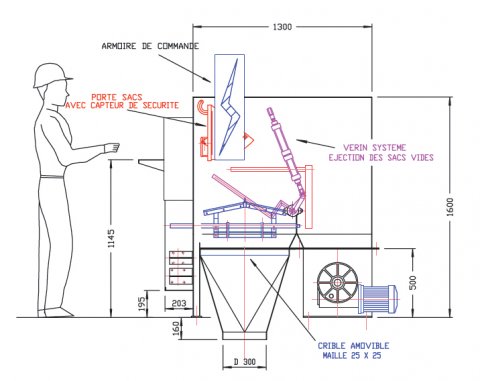
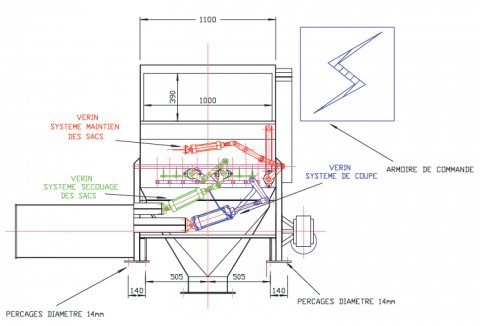