Contained drum packaging from 1 ton big bags
This packaging unit ensures the filling of barrels in confined enclosures of powders initially packaged in big bag of 1 ton or more.
Automation of transfers and dosage ensures a minimum of manipulation for operators. This cask reconditioning package is particularly suitable for toxic powders, volatile powders, CRM powders, Atex powders or all industries wishing a hygienic process.
- Integrated dosage
- Sealing of the drum’s inner liner
- Containment of the big bag and the barrel
- Automatic barrel conveyance
- Densification of powder
- 1 single contact for setting up your cask packaging line
The contained drum reconditioning unit integrates a big bag unhooking solution equipped with a glove box. The big bag is placed on the unloading station by an electric hoist, which is controlled by the packaging operator.
The gravity discharge allows for a safe flow of the powder being handled. For installation constraints, our design office can propose the implementation of intermediate transfer solutions for the recovery of the materials to be packaged.
Models
BBDrumMatic® 100 | |
---|---|
Rate | 60 drums/hr |
Capacity | Drums from 5 to 110 KG |
Materials of construction | Mild steel, 304 SS, 316 SS |
Installed power | 10 to 15 Kw |
Compressed air consumption | 2m³/hr @ 6bar |
Dedusting flow | 1,500 m³/hr |
Procedure
The dosing of the powder is provided by a vibrating corridor, allowing a high flow during the bulk fill phase and a small dosage speed to ensure accuracy to the nearest 10 grams. The use of a waterproof vibrating corridor allows a wide range of variation to adapt to the different granulometry and densities of packaged products.
The barrel containment enclosure is the standard of the Palamatic DrumFlow® model which provides a watertight connection and a densification of the products by vibrating the barrel during the filling phase. The weighing is loaded onto the cask connection head, which allows an exact weighing value and offers optional label printing (with the commercial weighing information).
The drums are transferred by a set of motorized roller conveyors, coupled with sensors for autopilot. This allows the packaging operator to remain at his welding station. The supply of barrels by vacuum and the evacuation of the conditioned drums is automatic and managed by our PLC software.
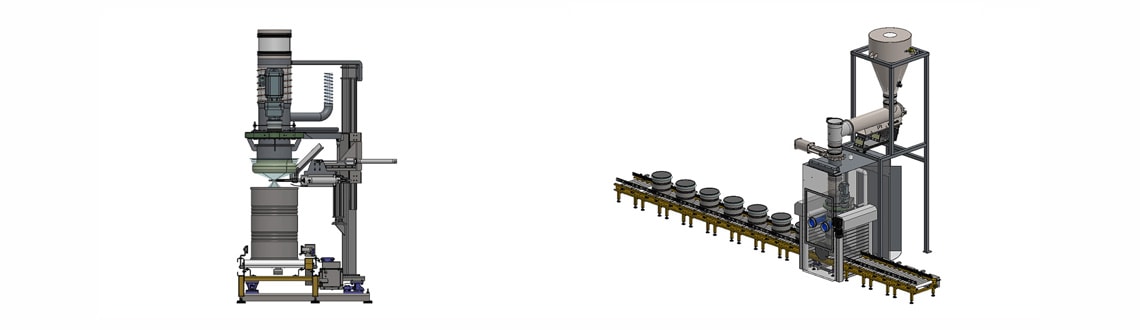
The closure of the casks is carried out by a set of double welding bars with an optional is vacuum sealing or injecting nitrogen gas for material integrity. Partner up with our pre-project design office to define the specific options for your project.
This reconditioning unit is particularly suitable for all manufacturers working in the provision of industrial services. Manufacturers can recondition their products in bulk bags or production units also can pre-dose these powders before incorporation into their manufacturing process.
Barrel-packed powders offer quality packaging with a wide range of capacity and design. The versatility of the BBDrumMaticline® can package 10 to 200 litre drums for the majority of applications.
In addition, the cylindrical shape of the cask allows them to be used directly on barrel mixers to ensure homogenization of the conditioned powder.
Handling the drums in the manufacturing process is easy and ensure handling with great security.
BBDrumMatic® in question
► What type of drum can be used on the BBDrumMatic® unit?
Metal, plastic or kraft drums can be used with a capacity ranging from 10 to 200 liters.
- The metal cask provides an excellent guarantee of safety during transport. It is durable, easily cleaned and reusable.
- The plastic barrel in PEHD is a good alternative for chemical or corrosive powders and is reusable with our without an internal bag.
- The kraft cask, very light to handle and easily recyclable with an internal bag, allows the packaging of all types of products: food, chemicals, pharmaceuticals, etc.
► What type of dosage is integrated?
The type of integrated dosage is a vibrating corridor dosage in gross weighing.
► What space is needed for the line to be set up?
The height of the building must be 8m and the ground surface of 10m x 5m.
► What products can be packaged?
All types of food, chemical or pharmaceutical powders can be treated.
► How many packing operators are needed?
1 packing operator and a driver for the supply of big bags and the evacuation of the packaged drums are sufficient for the smooth operation of the process line.
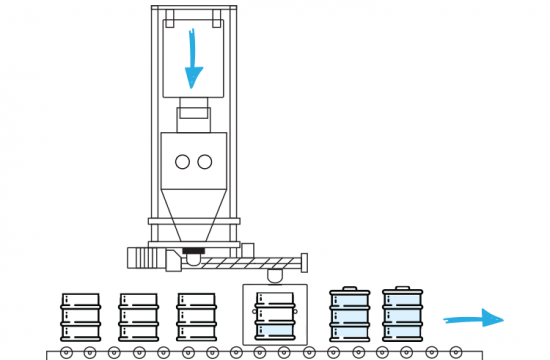
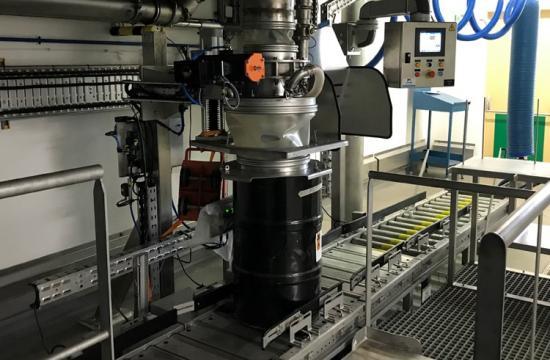
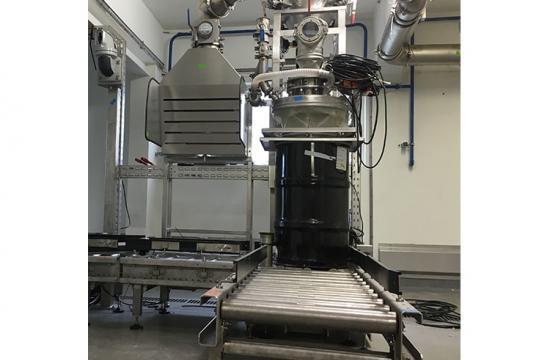
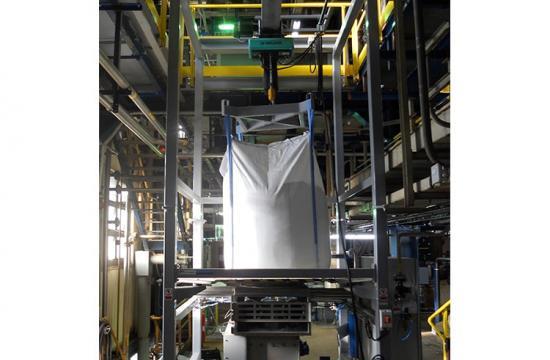
Discover the installations of our customers using the BBDrumMatic® 100 confined drum packaging line.
All the equipment integrated in the process line for conditioning drums in a confined atmosphere are available below.