Processed bulk materials: a hydrazine hydrate derivative used as a polymerization initiator for the synthesis of flocculating agents for water treatment, or as a blowing agent for PVC foam.
Barrel filling with chemical agents
Automatic packing of kraft barrels at the outlet of the mixing tower with automatic feeding and removal of the barrels.
A vibrating dosing unit ATEX 20/22 is used to dose the bulk material without degradation. The dosing unit is fitted with a buffer hopper, a height device for adjustment of the layer of material, a dosing tube (also available in a trough) and the vibration generator. The buffer storage hopper is located above the vibrating corridor to avoid any product flow interruption. The bulk material is then moved to the barrel to be conditioned.
In order to check the quality of the mixture produced upstream by the customer, an ATEX 20/22 pneumatic piston sampler is fitted in the storage hopper. The sampler is provided with a double-acting pneumatic cylinder enabling the translation of an open sampling piston to make it possible to take samples under operating conditions without stopping the process. The sampling is designed in such a way that the bulk material taken remains contained, without contact with the ambient air. The sample is collected in a 200ml screw-on pot.
An ATEX 22 motorized roller conveyor system is used to feed empty barrels and remove full barrels. The length of the conveyors was designed to ensure the storage of 12 empty barrels on one side and 12 full barrels on the other side, which is equivalent to a production batch.
At the heart of the conveyor chain is the packing station. The ATEX 20/22 barrel filling station consists of a motorized roller weighing conveyor on which the barrel rests and an automatic containment platform with automatic up/down movement. This containment platform is controlled by a double-acting pneumatic cylinder in order to achieve the containment by docking on the top of the barrel.
Volume balancing is achieved by connecting a stitch on top of this tray to the customer's centralized dust collection unit.
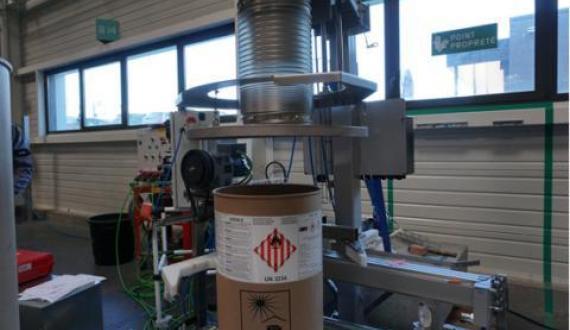
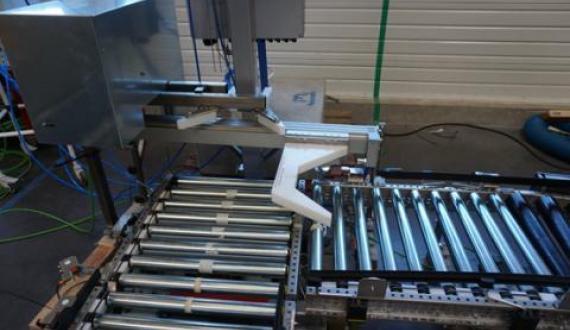
The general operation of the installation only requires the operator to place the empty barrels on the empty barrels storage infeed conveyor and to remove the full barrels on the discharge conveyor at the outlet of the packing station. When setting up, the operator ensures that the inner bag is turned over on the outer edge of the barrel.
When the empty barrel is removed, its presence is detected and the conveyor advances one step. The positioning is carried out by sensors placed on the edges of the conveyors. The operation continues in a similar way until the first one arrived at the packing station.
At this point the containment tray automatically descends to the top of the barrel and the dosing operation can begin. The dosing unit is directly controlled by the weighing loop in order to manage the operation at high speed and then at low speed. The PLC manages metrological data such as setpoint, high and low speed values, drop tail, etc.
Once the dosing is complete, the containment tray automatically rises and the full container can then be transferred to the removal conveyor. The barrel then moves forward one step.
The filling cycles follow one another until the last one is filled.
On the discharge line, a barrel closing station is implemented. A front suction hood is used to collect dust when closing the internal bag containing the material. Once the bag is closed, the operator manually places the cover and its strapping on the barrel.
At the outlet of the evacuation conveyor, a vacuum manipulator mounted on a bracket is used to pick up the barrels by the lid without effort for removal on pallets.
Achieved results:
- Speed and precision: Automatic operation in masked time with the vibrating dosing unit associated with the weighing loop.
- Atex:
- no use of rotating parts in contact with the bulk material to limit heating.
- installation of highly explosive dust collection points.
- use of equipment meeting the explosive characteristics of the bulk material.
- Safety / cleanliness: installation of dust collection points on the containment platform as well as on the barrel closing station.
- Ergonomics: no need to carry heavy loads by installing a tube lifter.