Description
Ribbon mixer - Low viscocity dry powders and pasty mixtures
Ribbon or belt mixing technology allows high-quality mixing at low speed. The materials are preserved and the risk of overheating is reduced. The resulting low attrition allows to maintain the initial characteristics of powders or granules blended, such as density, particle size or shape. The mixing principle is based on cross and repeated exchanges in the longitudinal direction established by the helical belt of the rotor. The slow movement of rotation is particularly suitable for heat-sensitive, fragile and abrasive materials.
Discontinuous belt mixers consist of a rotor shaft with opposite coils, located in a mixing tank.
Batch belt and ribbon mixer are available in 2 versions:
- Loading through hopper: MRRA
- Loading through cuff: MRRC
Operating mode |
![]() |
Constitution of the belt and ribbon mixer:
- A central filling opening or alongside the tank
- A central outlet opening
- A vent mouth
- Two closing plates for the ends of the tank to support the end bearings (adjustable and equipped with a shaft sealing unit)
- A gearbox with transmission
Equipment advantages
- Homogeneity of the mixture
- Excellent batch reproducibility
- Gentle treatment of the material without damaging it
- Possibility of complete discharge
- 100% loading rate possible
Features
Technical specification
Technical details:
- Sizes: from 75 to 15,000 liters
- Motorizations: from 1.1 kW to 45 kW
- Capacity: from 2 to 8 batches/h. (depending on the recipe and machine configuration)
- Mixing time: 5 to 15 minutes
- Possibility of manufacturing in high-strength steel, stainless steel or special materials with a heating or cooling casing.
- The discharge door reduces any retention of unmixed materials
- The seal ensures the tightness of the tank
- The discharge door is integrated in a pipe allowing connection to any return system (gravity rotary valve, screw...)
- The operation of the discharge door is carried out by a pneumatic control system including: pneumatic cylinder, distributor, coil, limit switch
- Dispersion 1 kg/ton
Technical characteristics of the mixing tank:
Total volume of the tank | 75 | 150 | 300 | 550 | 800 | 1,100 | 2,000 |
---|---|---|---|---|---|---|---|
Max. net capacity in liters* | 56 | 105 | 210 | 385 | 560 | 770 | 1,400 |
Engine power in kW | 2.2 | 3 | 4 | 5.5 | 7.5 | 11** | 13** |
*according to density of the product
Loading through hopper mixer dimensions: MRRA
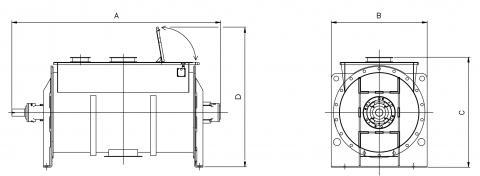
Models | A | B | C | D | Net capacity dm³ | Weight when empty in kg |
---|---|---|---|---|---|---|
MRR-A 75 | 1,300 | 611 | 670 | 1,051 | 56 | 160 |
MRR-A 150 | 1,460 | 670 | 763 | 1,271 | 105 | 270 |
MRR-A 300 | 1,840 | 770 | 930 | 1,393 | 210 | 400 |
MRR-A 550 | 2,150 | 930 | 1,133 | 1,585 | 385 | 690 |
MRR-A 800 | 2,350 | 980 | 1,154 | 1,602 | 560 | 850 |
MRR-A 1100 | 2,690 | 1,100 | 1,260 | 1,754 | 770 | 1,200 |
MRR-A 2000 | 2,920 | 1,340 | 1,465 | 1,975 | 1,400 | 2,400 |
MRR-A 3000 | 3,920 | 1,340 | 1,465 | 2,090 | 2,100 | 2,700 |
MRR-A 4800 | 4,520 | 1,500 | 1,725 | 2,199 | 3,360 | 3,800 |
MRR-A 6000 | 4,820 | 1,600 | 1,876 | 2,325 | 4,200 | 4,400 |
MRR-A 8800 | 5,390 | 1,810 | 2,067 | 2,665 | 6,160 | 5,300 |
MRR-A 10500 | 5,630 | 1,910 | 2,413 | 2,862 | 7,350 | 6,900 |
MRR-A 15000 | 6,124 | 2,110 | 2,706 | 3,190 | 10,500 | 8,000 |
Loading through cuff mixer dimensions: MRRC
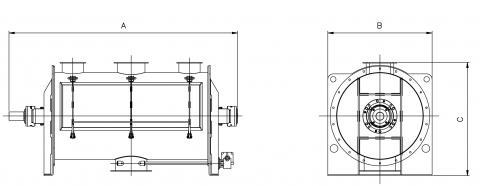
Models
|
A | B | C | Net capacity dm³ | Weight when empty in kg |
---|---|---|---|---|---|
MRR-C 75 | 1,300 | 611 | 649 | 56 | 160 |
MRR-C 150 | 1,460 | 670 | 754 | 105 | 270 |
MRR-C 300 | 1,840 | 770 | 889 | 210 | 400 |
MRR-C 550 | 2,150 | 930 | 1,075 | 385 | 690 |
MRR-C 800 | 2,350 | 980 | 1,151 | 560 | 850 |
MRR-C 1100 | 2,690 | 1,100 | 1,278 | 770 | 1,200 |
MRR-C 2000 | 2,920 | 1,340 | 1,455 | 1,400 | 2,400 |
MRR-C 3000 | 3,920 | 1,340 | 1,455 | 2,100 | 2,700 |
MRR-C 4800 | 4,520 | 1,500 | 1,750 | 3,360 | 3,800 |
MRR-C 6000 | 4,820 | 1,600 | 1,860 | 4,200 | 4,400 |
MRR-C 8800 | 5,390 | 1,810 | 2,130 | 6,160 | 5,300 |
MRR-C 10500 | 5,630 | 1,910 | 2,160 | 7,350 | 6,900 |
MRR-C 15000 | 6,124 | 2,110 | 2,445 | 10,500 | 8,000 |
Case studies
CASE STUDIES WITH THIS EQUIPMENT
Cementation of nuclear waste
Processed powders: Cement + filler, lime and calcium nitrate - Cementation of nuclear waste - This process is intended for the cementation of fines and resinsEnergy
Aromatic herbs conditioning
Processed powder: dried grass seeds - Seeds conditioning - Installation of a double discharge station: big bag emptying and container emptying for mixer feeding as well as a double filling station...Food and Animal Feed