Description
PALDRUM® 02 Barrel FILLING STATION - Dosing by vibrating feeder
The PalDrum®02 conditioning station provides weight-based filling of your barrels via a high-precision vibrating dispenser.
The load cells integrated into the packaging station control the vibrating feeder.
-
Rate4
-
Automation3
-
Containment3
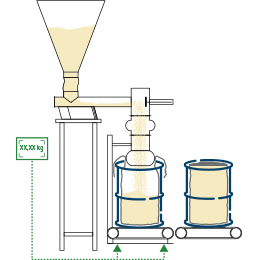
PalDrum®02-J-C-Gross
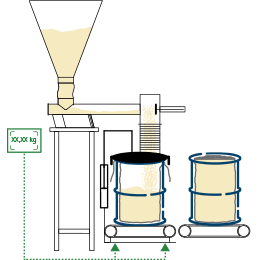
PalDrum®02-P-C-Gross
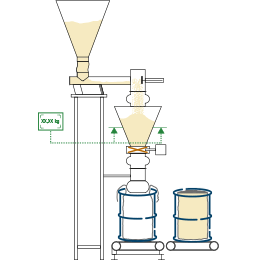
PalDrum®02-J-C-Net
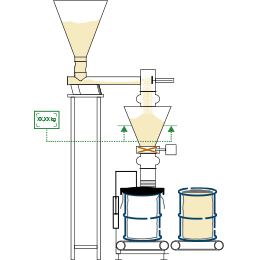
PalDrum®02-P-C-Net
The different possible configurations of the PalDrum®02 model:
Ref. | Possible equipments | Functions | Advantages | |
---|---|---|---|---|
Choice 1 | J | Inflatable seal | Dust-tight connection of the bag / barrel | Maximum confinement |
P | Connection plate | Quick connect of the bag / barrel | Speed ergonomic installation and multi-format barrels | |
Choice 2 | Net | Net weighing | Accurate dosing of the product to be packaged | Accelerated rate (dosing in hidden time) May require double check weighing |
Gain | Gross weighing | Weighing of the entire container and contents | Commercial weighing, traceability | |
Conveyor | C | Evacuation Conveyor |
Holding and evacuation of the barrel during packaging | Ergonomics, increased cadence |
Our PalDrum®02 packaging machine is configurable by modulating the possible basic equipment: choice 1 + choice 2.
Example of possible reference: PalDrum®02-J-C-Gross.
Description of choices:
Choice 1: 2 possible barrel connection systems:
- Inflatable seal connection system: the connection of the bag to the barrel, or directly to the barrel, is ensured by a low-pressure inflatable seal which provides total material containment. The installation of the bag on the inflatable seal must be carried out manually by the operator. The inflatable seal solution is particularly suitable for barrels with an internal liner.
- Connection cover: the cover is connected to the mouth of the barrel via a pneumatic cylinder, which controls the docking cycle. The sealing of the connection is made by pressing the cover on the edge of the barrel. This configuration provides automatic docking without operator intervention.
Advantage: this controlled docking solution allows automatic adaptation to different barrel heights.
A catch tray option is available to ensure collection of fines when disconnecting the bag and lid.
Choice 2: 2 weighing principles:
- Net weighing: the net weighing is carried out via an intermediate hopper installed in the structure of the packaging machine. In this configuration, the product to be packaged is weighed upstream before the barrel filling phase. This net weighing configuration offers a throughput gain of up to 150 doses/hour.
- Gross weighing: this configuration ensures continuous weighing of the barrel during the filling phase. The chain of load cells is installed under the barrel handling roller conveyor. Gross weighing on the filling station offers safe dispensing without the need for double check weighing. The PalDrum®02 barrel filling station can be IPFA approved when using automatic lid connection.
Barrel handling:
The PalDrum®02 dosing station is designed to be installed on your packaging line with conveyors. Barrel handling solutions using suction cups can be placed at the exit of the conveyor to ensure the palletizing of the barrels.
Equipment advantages
- Automatic dosing and filling of all your powders and bulk materials
- Respect for your fragile products by vibrating dispenser
- Containment by sealed connection on the head of the barrel
- Simple and ergonomic adjustment to your different quantities (setpoint weights, barrel format)
Media
View our equipment in photos
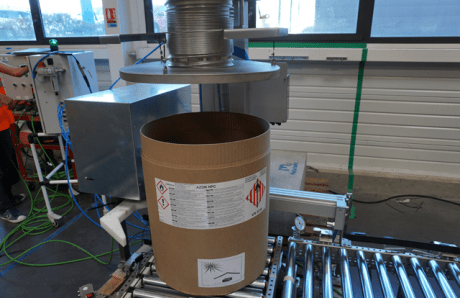
Barrel filling with vibratory table
Conditioning in barrels of animal flour for the animal nutrition sector.
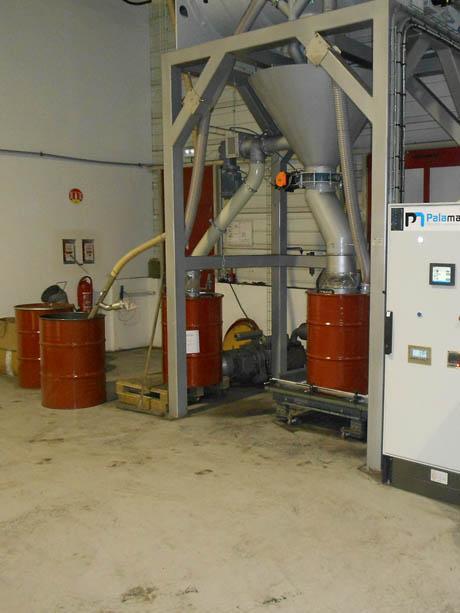
Barrel filling system
Barrel packing line with adipic acid.
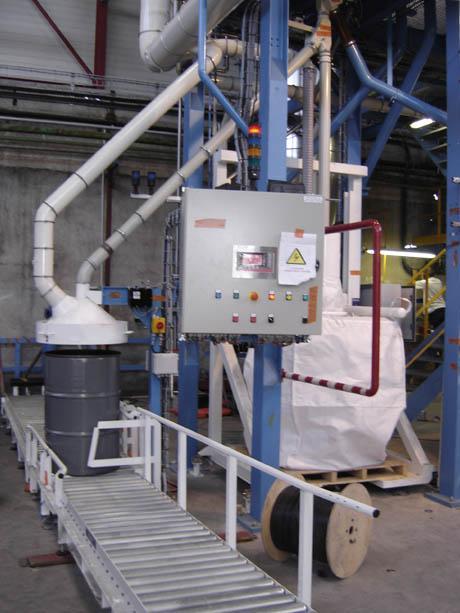
Barrel filling system - Cabinet control
Chromium powder barrel filling line in sealed mode to ensure operator safety.
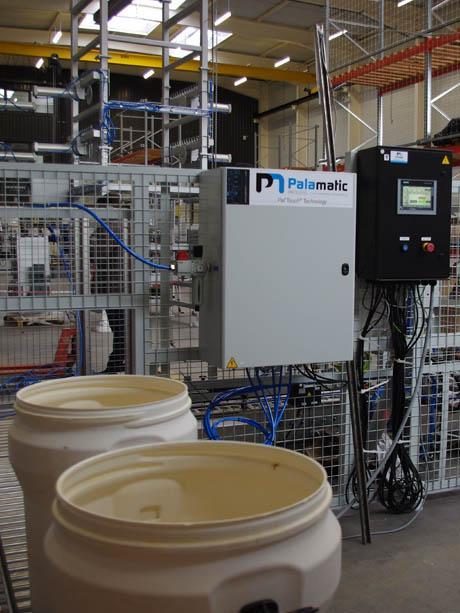
Barrel filling line
Barrel filling machine on a process line treating seeds.
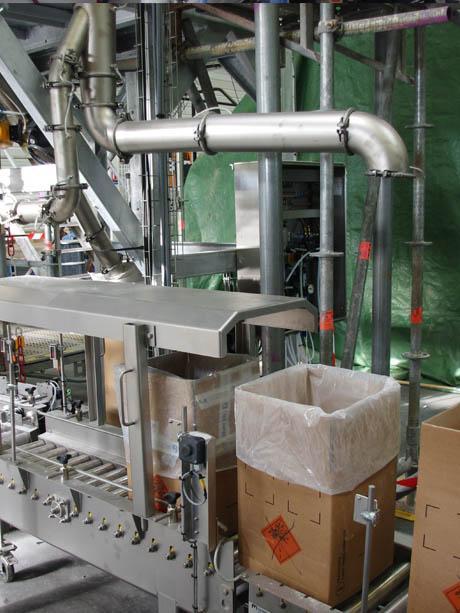
Box and barrel filling system
Packing line for sodium bicarbonate in cardboxes with internal bag and in barrels.
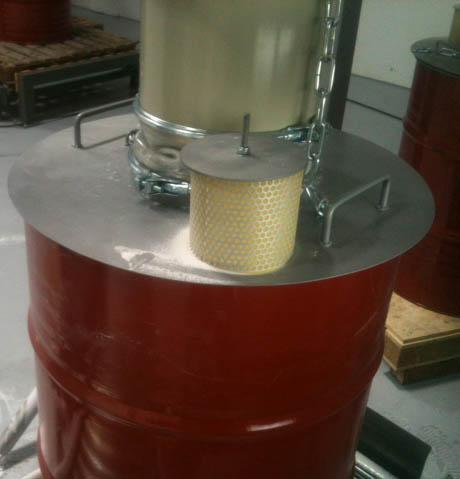
Bulk handling materials - Barrel filling system
Filling head on barrels for contained filling.
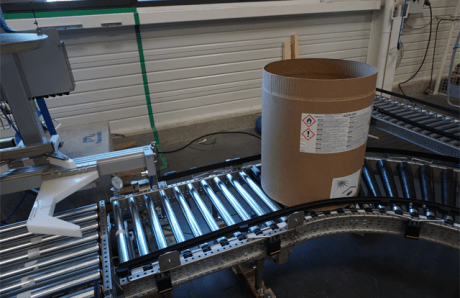
Barrel filling with conveyor
Barrel conditioner on a process line for mixing and packaging phytotherapeutic products.
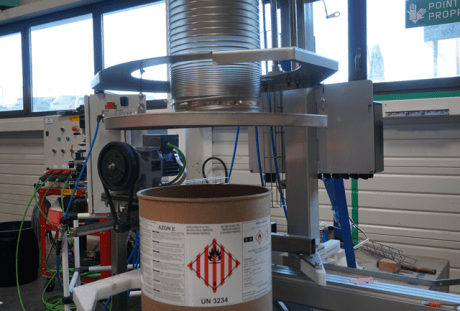
Barrel filling - Plastic application
Industrial process for the contained filling of cardboard barrels with chemicals.
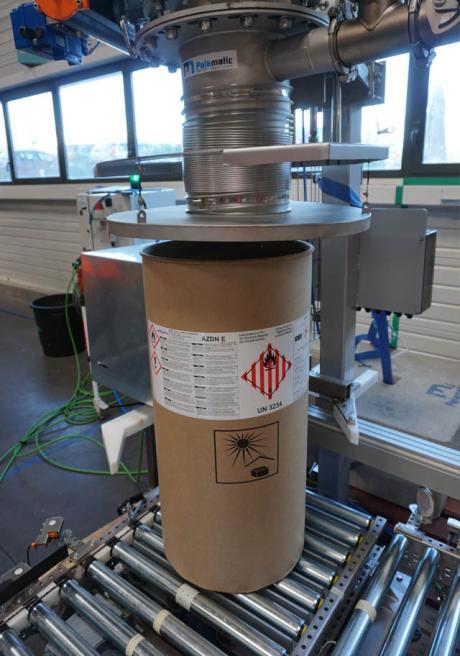
Vibrating table
Roller conveyor on industrial barrel filling station.
Features
Technical specification
Rate | 100 barrels/h |
---|---|
Capacity | 300 kg/barrel |
Manufacturing materials | Painted steel, 316L stainless steel |
Installed power | 3.5 kW |
Compressed air consumption | 0.9 Nm³/h |
Dust removal rate | 300 m³/h |
Specifications :
- Semi-automatic packaging station
- Storage, evacuation and automatic dosing of the product
- Manual docking and positioning of the barrel.