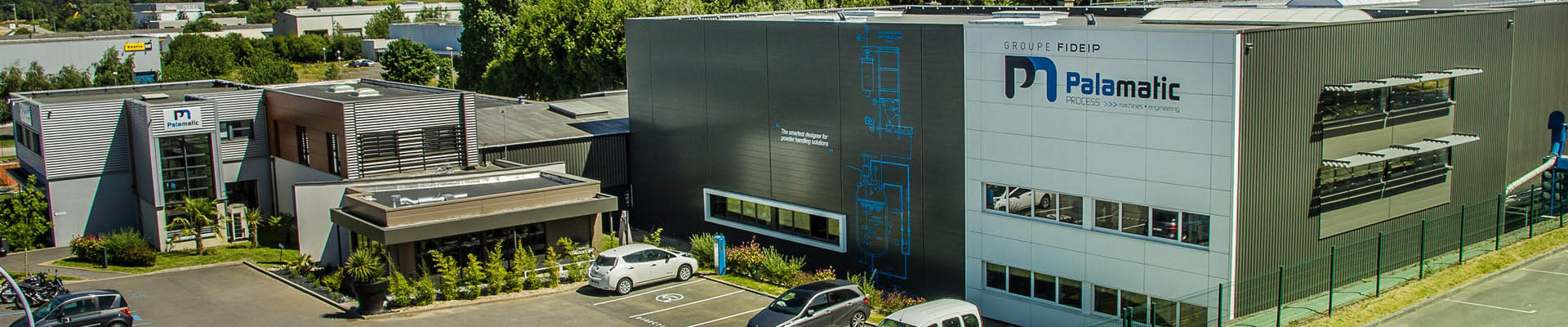
Dry materials automated tipping, conveying and dosing
INTEGRATED EQUIPMENT
Pneumatic conveying - Dense phase vacuum - VFlow® - 5 models
All bulk materials, No material degradation, Line purge
Conveying
Drop-through rotary airlock valve
Rate from 2.2 to 19.5 liters/rev., Extraction and dosing under hopper, silo, cyclone...
Conveying
Flexible fitting, BFM® Fitting Sleeve
Flexible system, Hygiene, Safety, No tools needed for disassembly
Discharge
PalSack®01 Bag filling - Screw feeder
Weighing, Management of dosing speeds, Containment, Packaging for open mouth sacks