Multiple stations for the automatic dosing of additives for liquid eggs
The additives incorporation line is dedicated to the preparation of liquid eggs before drying or packaging. The two big bag discharging stations integrate automatic dosing for major additives (i.e., salt and sugar) and a bag dump station for the introduction of minor additives from floor level, in dry areas.
- Hygienic design
- Flexibility for the introduction of additives (big bag or small sacks)
- Automatic dosing
- High loading rate
In order to meet the requirements of egg products, Palamatic Process has developed the flexible and hygienic automatic dosing line called PowderEgg®02.
This production line facilitates the dosing and introduction of additives into liquid egg tanks. Whether you want to introduce salt, sugar, maltodextrin or xanthan into the egg whites, yolks or whole egg tanks, your additive stations are directly connected to the storage vessels with automatic dosing and material transfer. The use of a powder incorporator such as Polymel, Sylverson, liquidverter or triblender can also be integrated in this egg production line with control of the powder level to avoid risk of foaming.
The force-feeding of the powder additives is conducted by pneumatic transfer with a safety probe.
Hygienic line design
In order to meet the requirements of egg products production, the line is entirely designed in stainless steel and the material retention areas are kept to a minimum.
The transfer of additives into the powder preparation tanks is ensured by a pneumatic vacuum conveying system. Magnets integrated on the transfer line provided a clean product, free of foreign metal contaminants.
If you wish to introduce your additive directly into the disperser, our design office can offer a dedicated big bag discharge station for gravity loading of the powder/liquid disperser. This configuration offers the advantage of minimal equipment on the installation, which can facilitate product changes with faster cleaning.
Ergonomics
In consideration of the hygienic design requirements of the equipment, ergonomics for manufacturing operators has also been taken into account. Our design office has studied accessible equipment heights, reduced the charging ports and made access to maintenance areas easy and secure.
Since your installation is unique, our design office designs the equipment according to your specific constraints and requirements.
Quality of your finished products
The controlled feeding of your powder additives into the dispersion tanks provides a finished product that complies with your recipes and customer requests.
Not aerating your product during mixing and avoiding deposits at the bottom of the tank are important criteria for obtaining a homogeneous and standardized egg product.
Palamatic Process’ experience in the field of eggs (powdering, bagging of egg powder, white powder, yellow powder and treatment of shells) guarantee a high-quality production.
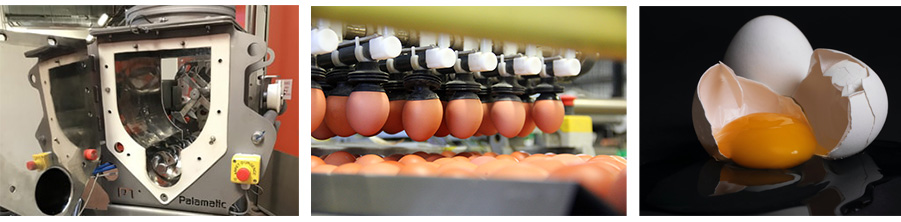
Control and piloting
Our Palamatic Process production lines are supplied with full automation for the correct configuration of your installation. The traceability of the manufacturing batches, the identification of the finished products as well as the history of the recipes are stored in the PLC.
Overview of the production parameters is possible by secure access for your maintenance teams. Our automation design office works with your teams to define your functional needs and your manufacturing history.
Discover the installations of our customers using the PowderEgg®02 line.
All the equipment integrated in the multi-additive process line in automatic dosage are available below.