Automating coffee dosing and packaging: what solutions for a precise, fast, and compliant process?
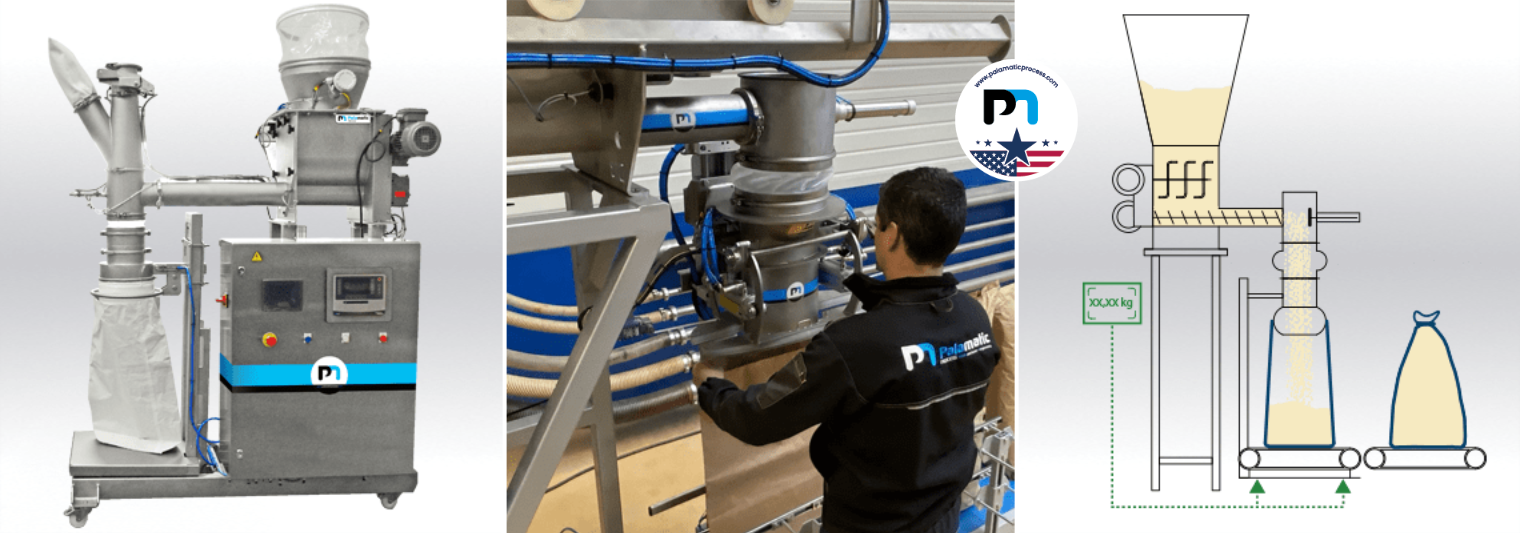
- 1. Mastering the specific challenges of measuring coffee beans or ground coffee
- 2. What dosing technologies are used for coffee ? Weight or volume ?
- 3. How can you automate the filling of bags and big bags of coffee ?
- 4. Integrate traceability, safety, and hygiene into your coffee dosing line
- 5. Optimize your ROI: automation, speed, and operator ergonomics
- 6. Conclusion
The automation of coffee dosing and packaging — whether for beans, ground coffee, or instant powder — has become a necessity for manufacturers wishing to guarantee dose precision, hygiene, traceability, and yield.
From roasting to bagging, each step must be designed to preserve aromas, comply with food standards, and optimize production rates.
Palamatic Process supports coffee manufacturers in this endeavor by designing custom-made dosing and filling lines, combining robustness, flexibility, and regulatory compliance.
In this article, we explore the best solutions for efficiently automating coffee packaging, from integrating a screw feeder to complete control via a Pal'Touch® system.
Whether you produce in small or large series, concrete answers to your challenges in dosing, dust, operator safety, or weight control are here.
1. Mastering the specific challenges of dosing coffee beans or ground coffee
Objective: precise and consistent dosing despite product constraints
In industrial coffee production, the dosing phase is crucial for ensuring the consistency of finished products, avoiding material losses, ensuring end-customer satisfaction, and complying with food trade requirements.
Whether it's coffee beans, ground coffee, or freeze-dried coffee, manufacturers must deal with products exhibiting complex behaviors: variable density, tendency to dust formation, risk of agglomeration, or even electrostatic behavior.
Understanding the particularities of coffee powders: hygroscopicity, particle size, dust
Ground coffee has physical properties that complicate its handling: hygroscopic, fine particle size, electrostatic, volatile dust.
These characteristics require adapted solutions to prevent losses and ensure smooth flow.
How to avoid weight variations and material losses?
Technical solutions include weigh hoppers, servo-controlled dosing screws, anti-bridging systems, upstream sieving, and intelligent control via Pal'Touch®.
These systems guarantee stable dosing compliant with direct sales standards.
What is the difference between weigh-metric dosing and volumetric dosing?
Weigh-metric dosing uses load cells for high precision, suitable for legal requirements.
Volumetric dosing measures a fixed volume, faster but less precise, especially in case of product density variation.
2. What dosing technologies for coffee ? Weigh-metric or volumetric ?
Objective: choosing the right type of feeder according to your formats
The packaging format (sticks, capsules, sachets, bags, big bags) influences the technological choice.
Each use has its requirements in terms of rate, precision, and hygiene.
Focus: Palamatic screw feeders – precision, cleaning, recipe changeover
Palamatic offers a range of screw feeders designed for complex powders like coffee.
Continuous or batch operation, hygienic hoppers, tool-free disassembly, quick cleaning, and control via Pal'Touch®.
What is the difference between weigh-metric dosing and volumetric dosing?
Criterion | Weigh-metric | Volumetric |
---|---|---|
Precision | Very high | Medium |
Legal metrology | Yes | No |
Density sensitivity | Low | High |
Cost | Higher | More economical |
3. How to automate the filling of coffee bags and big bags ?
Objective: fast, clean, and compliant packaging
Filling is a critical step: it must ensure hygiene, speed, traceability, and operator safety.
Automated solutions reduce losses, MSDs (Musculoskeletal Disorders), and ensure better batch control.
PalSack® and FlowMatic® baggers and fillers: what options for coffee?
PalSack®: for bags from 5 to 50 kg, with weigh-metric dosing, clamping ring, integrated sealer.
FlowMatic®: for big bags up to 1500 kg, with suspended weighing, vibrating table, dust removal.
What is the best packaging system for coffee in big bags or 25 kg bags?
The choice depends on the needs: rate, frequency of recipe changeover, volume, ATEX safety.
Palamatic equipment is modular and scalable.
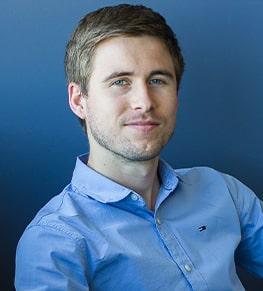
Do you have a project ?
I am available to advise and assist you in your research.
Guillaume, expert in industrial powder safety
4. Integrating traceability, safety, and hygiene into your coffee dosing line
Objective: meeting agri-food and metrological requirements
Hygiene, operator safety, and metrological compliance are fundamental.
A well-designed line limits contamination, guarantees weights, and reduces risks.
Pal'Touch®: intelligent control of your dosing and packaging lines
Pal'Touch® ensures the supervision of the entire line: recipe management, batch traceability, alerts, production history, integration with ERP/MES.
A complete solution for the agri-food industry.
How to ensure hygiene and compliance in food product packaging?
Stainless steel materials, CIP/SIP (Cleaning In Place / Sterilization In Place), tool-free disassembly, FDA/EC 1935/2004 compliant seals, dust removal systems.
Palamatic offers a complete range of hygienic and certified equipment.
5. Optimizing your ROI: automation, rate, and operator ergonomics
Objective: reducing pénibilité and improving overall productivity
Automating reduces MSDs, line stoppages, rejects, and improves production stability.
It also allows operators to be reallocated to value-added tasks.
Modular and scalable equipment: flexibility for production variations
Quick recipe changeover, mobile stations, interchangeable equipment, multi-format compatibility.
An architecture designed for the long term.
What are the measurable gains of an automated dosing line?
Indicator | Before | After |
---|---|---|
Rate | 5 bags/min | 12 bags/min |
Precision | ±5% | ±1% |
Rejects | 3–6% | <1% |
MSDs | High | Reduced by 60% |
Conclusion
The automation of coffee dosing and packaging is no longer just about industrial performance: it is a strategic necessity to guarantee quality, safety, compliance, and competitiveness.
Thanks to its custom-made solutions, Palamatic Process supports producers, roasters, and packagers in the complete optimization of their line, with proven expertise in demanding agri-food environments.
From high-precision feeders to automated baggers, including Pal’Touch® control and FlowMatic® stations, each piece of equipment is designed to integrate perfectly into your process while offering you long-term scalability.
📩 Do you want to automate or modernize your coffee dosing line?
👉 Contact us today to benefit from a personalized technical diagnosis.