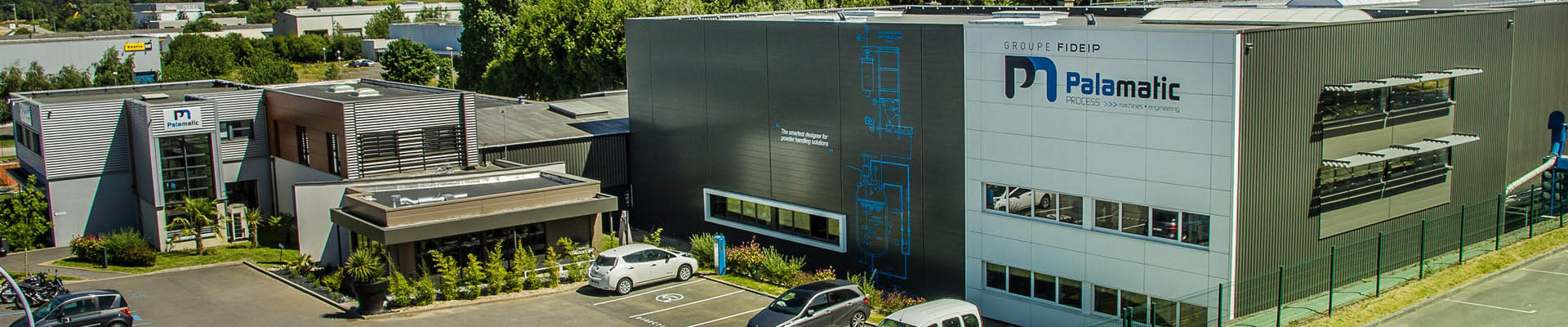
Case studies - Laundry powder
Main process steps:
Storage, pneumatic conveying, mechanical conveying, dosing, mixing, packing.
Laundry detergents contain several "agents" that perform a specific function. Industrial production lines ensure the storage, conveying, dosing and incorporation of the different components into the mixing line.
Case studies with our customers
Optimizing Sensitive Powder Processing with a Custom Solution
Powders handled:lithium, Lithium, NMC compounds (Nickel, Manganese, Cobalt), and anode/cathode materials (graphite, LiFePO4), requiring secure handling due to their toxicity, hygroscopic properties...
Chemical
High-rate automatic bulk bag filling line for the export of natural soda ash
Chemical
Packaging line for washing detergents and detergent products
Chemical
Detergent powder milling
Chemical
Bulk solids supply to a manufacturing tank
Chemical
Discharge of big bags of bleaching agents for tank feeding
Chemical
Laundry powder storage line
Chemical
Agents integrating recipes for laundry and detergent products:
- Alkaline compounds (increase the effectiveness of surfactants, borates, carbonates)
- Sequestrant agents (increase the effectiveness of detergents: citrates, metaphosphates, polyphosphates, zeolites, EDTA, NTA, phosphonates)
- Complexing agents (anti-redeposition agents) preventing dirt trapped by surfactants from redepositing on the laundry
- Enzymes degrading organic molecules
- Bleaching agents (perborates, percarbonates, peroxides, sodium perborate, sodium percarbonate, hydrogen peroxide). Their objective is the oxidation of colored molecules.
Powder & bulk materials handling solutions:
All the necessary ingredients (powder and/or liquid) are stored in storage silos or bulk bags. The formulation and production lines include material transfer (generally pneumatic and/or mechanical conveying) which allows the loading of the mixer. Intermediate hoppers provide weighing by loss in weight or gain in weight functionality. The integrated load cells perform the precise dosing to ensure that the formulation is respected. A line of micro-ingredients completes the detergent production line. After introducing all the bulk materials into the mixer, a spray (incorporation) of perfume in liquid form is performed. For powdered detergents, the industrial mixer is emptied while preventing material attrition and the segregation of the various blended particle sizes (particle segregation).