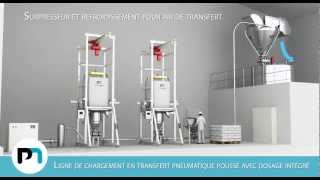
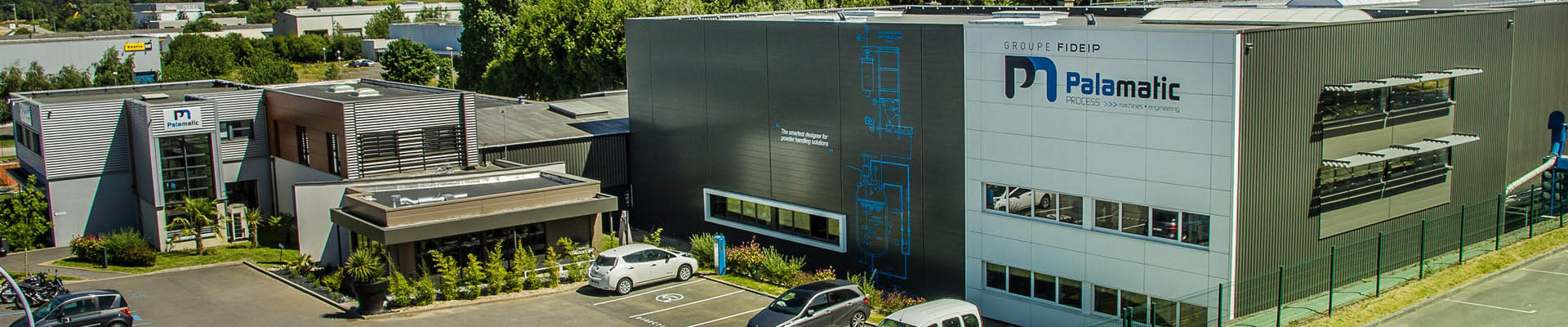
Pneumatic conveying offers an alternative to the mechanical handling of materials. Palamatic Process has developed pneumatic transport systems using techniques such as suction or pressure (dense or dilute phase) for handling powders and bulk materials.
Pneumatic transport of powders under positive pressure is particularly suitable for transferring materials at high flow rates over medium to long distances (approximately 164 to 656 feet, 50 to 200 meters). Pneumatic conveying by suction, on the other hand, is used for short to medium distances (approximately 6.5 to 230 feet, 2 to 70 meters) to transport powders or granules that are heat-sensitive, hygroscopic, or greasy and prone to clogging.
Two types of pneumatic conveying systems for industrial use: dense phase and dilute phase
The suction-based dense phase powder transfer system may be referred to by various names: powder pump, pneumatic conveyor, powder conveyor, vacuum transfer, vacuum conveyor, powder handling system, vacuum pump or transfer cyclone. It is used to transfer of powders, granules, bulk solids, and fine materials without degradation, continuously and in a fully enclosed process.
This dense phase conveying system offers numerous advantages over dilute phase or pressure-driven pneumatic conveying systems. It prevents attrition and demixing of the transferred powders and allows for fully enclosed, energy-efficient operations.
Powders are drawn into the system using a vacuum pump (either electric or pneumatic) towards a receiving cyclone (cyclofilter) with tangential (cylindrical) inlet. The powders are discharged via receiver filters or cyclonic separators, which separate the material from the air directly above hoppers, storage tanks, or other production equipment in the packaging line.
This system is employed to transfer fine materials to one or more production units over long distances while offering greater capacity than suction systems. It is particularly suitable for highly abrasive products, materials of varying flow rates, and all temperature ranges. A rotary valve is not mandatory for operation.
The powders are moved by pushing, with one or more inlets for the material. Bulk products are transferred via rotary valves into conveying lines. The powders and air are propelled through the transfer line and discharged at one or more usage points. The conveyed materials are separated from the air using a receiver filter or cyclonic separator.
Palamatic Process dilute phase pneumatic conveying systems use positive pressure (blowing) within sealed piping to transport materials. These systems handle installations with multiple pickup and discharge points. Powders or fine materials are suspended in air during transport and separated at the usage point via guillotine valves, butterfly valves, and rotary locks. Also known as dispatch locks, these systems operate at high pressure and low speed for transferring abrasive or delicate materials.
Depending on the product characteristics, our engineering team optimizes filtration and transfer speed to prevent:
For ATEX zones, our experts design tailored powder transport solutions adapted to your specific constraints. Various sensors (pressure, temperature, oxygen meters) ensure system control and operational safety.
Palamatic Process also offers specialised pneumatic transfer systems for specific materials, such as the MultiAshFlow® pneumatic ash conveyor and the Cementveyor® pneumatic cement transport system.
Consult our dedicated article, Pneumatic Conveying: Which Technology to Choose?, or contact our experts directly for personalised advice. Palamatic Process can also assist in resolving issues related to pressure loss or efficiency reduction in your pneumatic conveying system. Our business managers can conduct feasibility studies for investments aimed at enhancing industrial efficiency and debottlenecking your site.
Example of a production line with a pressure-based pneumatic conveying system: